Next Generation Machine-Roomless Elevators
The Greenest Options
True MRL elevators are designed to minimize carbon footprint by optimizing the size, materials, and weight of components. Some models incorporate further energy-saving technologies. Because they are not always standard MRL features, early in the specification process architects should note whether the following five energy-saving elements are included in the model they have selected.
Gearless Machine
Permanent magnets boost the power of the motor, which enables a reduction in motor size. Some gearless machines are 70 percent smaller than machines used in conventional traction systems, and are compact enough to tuck away at the top of the hoistway. The system's efficient use of energy lowers elevator operating costs. With a permanent-magnet synchronous motor and digital VF closed-loop drive that combine to form an efficient system, the gearless machine can reduce power consumption by as much as 50 percent compared to conventional geared machines.
Coated Steel Belts
In the most environmentally sound elevators, flat polyurethane-coated steel belts replace the heavy woven steel cables that have been the industry standard since the 1800s. The belts make the smaller sheave possible. They are only 0.1 inch thick, yet they are as strong as woven steel cables and far more durable, flexible, and space-saving. There are several advantages to using these belts. Lying beneath the polyurethane coating of the belt are 588 high-tensile strength steel wires with zinc-plating to minimize corrosion. The polyurethane coating avoids metal-to-metal contact (of rope to sheave), reducing noise and vibration. It helps provide a smoother ride and higher level of passenger comfort not found in steel rope applications. In addition, coated steel belts have been found to have a life two to three times longer than conventional steel ropes.
Lastly, because of its design, the coated-steel belt eliminates the lubrication requirement of conventional ropes and its associated smells and messes as well as the need for storage, cleanup, and disposal of hazardous waste. Some manufacturers offer maintenance systems that electronically monitor the status of the belts' steel cords, and automatically detect and report belt faults to maintenance personnel.
Compared to hydraulic systems, the gearless MRL reduces car noise by 30 percent and vertical and horizontal vibration by as much as 75 percent. Compared to geared systems, this option reduces in-car noise and vibration by 25 percent. Coated steel belts help to improve ride quality. In terms of the machine, the sealed bearings reduce noise and vibration. Rubber pads are located at the bearing point at each end of the integrated machine and bedplate, and the sound-isolated structure keeps vibration to a minimum.
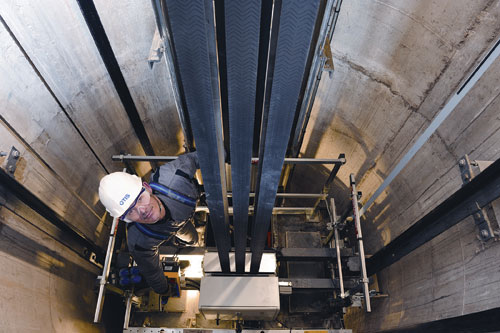
Photo courtesy of Otis Elevator Company
Coated steel belts are only 0.1 inch thick, yet they are as strong as woven steel cables and far more durable, flexible, and space-saving
Regenerative Drive Technology
All traction geared or gearless elevators will generate electricity. In simple terms this means that in certain modes of operation, the elevator motor will behave as a generator and generate electricity instead of consuming electricity. Specifically there are two primary modes of operation where the elevator motor will generate electricity:
- When a heavily loaded car travels in the down direction, it outweighs the counterweight and works with gravity. This motion generates electrical power.
- When a lightly loaded car travels in the up direction, the counterweight outweighs the car and works with gravity. This motion generates electrical power.
In non-regenerative systems, the electricity generated during these modes of operation is dissipated as heat into the machine room. This energy is wasted and in many cases the customer also has to add air conditioning to the machine room which is an additional expense.
In regenerative systems, the electricity generated during these modes of operation is converted by the regenerative drive to useful energy that can be used to power other loads within the building such as lights, air conditioning, office equipment etc.
![]() |
Some regenerative drives also offer the additional advantage of creating clean electricity, which eliminates concerns that the elevator's regenerative energy will have a negative effect on other electrical equipment in the building.
In addition to energy savings and clean power, the regenerative controller also offers more space and flexibility. It is 50 percent smaller than the conventional geared controller, and uses up to half the space of a traditional non-regenerative traction controller. It is also quieter and produces less heat.