Next Generation Machine-Roomless Elevators
True MRL for the Holeless Hydraulic System
Machine-roomless systems have been available with traction systems for years, but they were not available as a major construction hydraulic product offering until very recently. The critical components of the true MRL holeless hydraulic system — oil tank, controller, and main disconnects — have been redesigned to fit into a standard hoistway, that is, a hoistway with the same depth and width, pit depth, and overhead allowance as a conventional holeless hydraulic elevator. Access to these components is obtained through a standard door that can be located on a hoistway wall on the first or second elevator landing.
The hydraulic elevator system, in which the elevator car is pushed from below by a plunger, is the oldest operating system and the least expensive. Though highly dependable, hydraulic elevators run at lower speeds, and are thus designed for low- and medium-rise applications. Holeless systems are environmentally preferable to holed options, where the cylinder is buried underground in a hole equal in depth to the rise the elevator travels. A PVC liner protects the walls of the cylinder from underground contaminants. For the holeless option, there is no inground cylinder. Its side-mounted plungers are surface mounted at the base of the hoistway, which eliminates the need for drilling a hole into the ground to accommodate the plunger — a scenario that precludes any possibility of oil seepage into the ground, thereby lowering the risk of soil and groundwater contamination.
Manufacturers estimate that the true MRL holeless hydraulic system saves up to $10,000 in time and material costs on the construction site, while enabling more revenue-generating space for the owner. Savings is due to elimination of the need to build a large hydraulic machine room with walls, lights, fire protection and HVAC system.
True MRL For the Traction Elevator
The true machine-roomless option, meaning that all components fit in the hoistway, has also come to traction elevators, which dominate the medium- and high-rise market. A traction elevator system works like a pulley — on one end is the car and on the other end is a counterweight. The car and counterweight are attached via coated steel belts or wire ropes that are looped over the machine, which is located at the top of the hoistway. The counterweight provides a counterbalance to the weight of the car, therefore significantly reducing the energy required to raise and lower the elevator. Traction elevators offer the ability to travel at higher speeds and rise with a smoother and quieter ride than a hydraulic system.
Historically, there have been two types of traction elevators: geared and gearless. The main difference between the two is the way in which the motor rotates the drive sheave. Today's traction market is primarily gearless. Gearless elevators incorporate a motor that connects directly to the drive sheave and rotates it at variable speeds similar to the operation of an electric hand drill. The variable-speed AC motor is cost effective, quiet at high speeds, and precisely controls maximum speed, acceleration, deceleration and leveling. The high power factors of the variable frequency (VF) drive allow for smaller mainline feeder sizes, and its reduced starting current allows for the use of a smaller emergency generator.
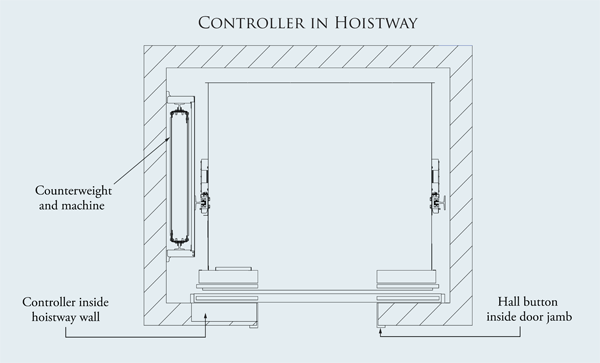
In true MRL models, compact controllers fit inside the hoistway, a key advantage over other elevators.
Drawing courtesy of Otis Elevator Company
The true MRL gearless traction model has been made possible by two main factors: the compact controller innovation and the inspection/test panel. In these true MRL models, compact controllers fit inside the wall of the top elevator landing, and most necessary test and maintenance features can be concealed behind a panel in the elevator entrance to give building personnel, elevator mechanics, and city or state inspectors access to the critical items they need. This inspection and test panel typically includes a mainline disconnect accessible to building personnel who may need to cut power to the elevator. There is also a separate lockable panel which houses the service port for elevator mechanics and access to the safety circuits in case of emergency or troubleshooting. In most jurisdictions, safety tests can also be performed from this panel.
The true MRL gearless traction model also features flexible coated steel belts, which have a significantly smaller bending radius than conventional wire rope, allow a smaller sheave, some 4 inches in diameter vs. a conventional geared sheave of 30 inches in diameter. This enables a more compact machine that is 70 percent smaller and up to 50 percent more efficient than conventional geared machines. Pits can be shallower and overhead lower, creating the smallest hoistways to date.
Some elevators of this type feature minimal vibration and in-car noise, which creates a smooth ride and quiet building environment. Cost savings are also realized. Based on estimates of general contractors in various parts of the U.S., a machine room for a traction elevator costs approximately $35,000 on average, and a control room, $5,000.