Next Generation Machine-Roomless Elevators
Considered groundbreaking when it was first introduced, gearless MRL technology has virtually replaced the traditional geared machine type traction elevator that has dominated the mid-rise market for more than half a century, and has made inroads into the hydraulic market. Advances continue, with major manufacturers offering their own MRL solutions and innovations. In 2011, gearless models were introduced that eliminate the need for any sort of separate elevator control space, enabling all elevator support equipment to be placed within the hoistway and creating a true machine-roomless model. Also in 2011, true MRL technology was extended into hydraulic elevators, enabling those models to dispense with their full-size machine rooms. In short, with the latest advances, the elevator has become a self-contained system.
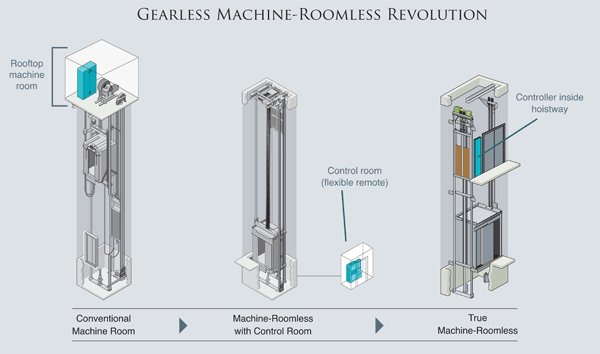
Chart courtesy of Otis Elevator Company
The advantages of this are several fold. Architects are free to use the extra space, which can be as large as 100 square feet per elevator, to support their design vision. Higher use of that extra space, such as additional apartments or offices, enables developers and owners to manage the building more economically as well as benefit from lower building costs. Because an elevator machine room is not just four walls, but a space that requires a complex system of lights, fire protection, and HVAC equipment, eliminating the room altogether results in reduced construction costs and time, materials, and coordination issues on the jobsite. With fewer moving parts, installation can be simpler than for conventional elevator systems, with decreased requirements for interfaces and roof penetrations. In some instances, elevators can be installed via the hoistway, without having to be positioned by expensive overhead cranes. On certain products, hall call buttons can be integrated into the elevator doorjambs, rather than on building walls, which further reduces time and interface among trades on the jobsite. Newer models can have lead times as short as six weeks — half the industry average — due to their modular design, automation, and proximity of the factory. Shorter lead times enable the architect to “push the order button” on an elevator already specified when the project is further along and the owner has selected the elevator's final aesthetics. At this point, the installation date can be more realistically targeted. This avoids having to pay costly storage fees for elevators that arrive on site when the construction project is facing delays. Some true gearless MRLs are also good options from an environmental perspective. Their smaller footprints, more efficient motors and regenerative drives can reduce HVAC demand and require up to 75 percent less energy than their traditional counterparts.
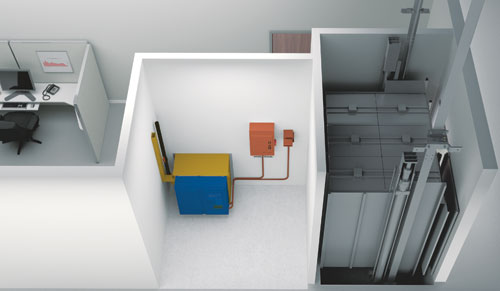
Image courtesy of Otis Elevator Company
A. Conventional System: Requires dedicated machine room space
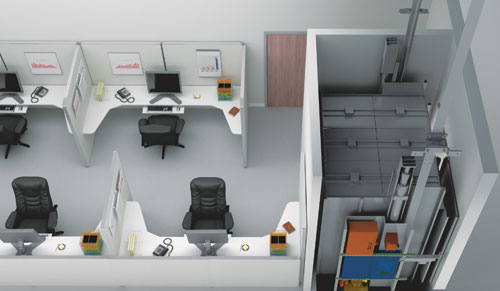
Image courtesy of Otis Elevator Company
B. MRL Holeless Hydraulic System: More usable space in your building