Subfloor as a Hidden Asset
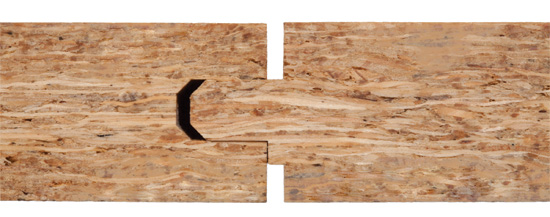
Photo courtesy of Huber Engineered Woods © 2014
Finished Floor Installation Scenarios
Each type of finish floor has its own discrete requirements for a subfloor.
Under ceramic tile. Ceramic tile floors will crack if there is any significant movement within the subfloor. Consequently, high-performance panels are a better option than plywood or OSB, as there is less deflection. However, ceramic tiles should never be installed directly over wood subfloor panels; an approved underlayment must be installed prior to tile installation. The type of underlayment should be based on the type of construction and installed according to the tile manufacturer's recommendations. Generally speaking, a layer of thin-set mortar should be applied to underlayment in straight beads; there are several choices of thin-set mortar on the market, but the one selected should be consistent with what is specified in the Tile Council of America Handbook for Ceramic Tile Installation, which is the “bible” for acceptable methods of tile installation on structural panel substrates. According to the handbook, there are several types of underlayment available, including cementitious backer board and rubber membranes. The backer board is applied directly to the wood subfloor, and ceramic tile can be bonded to it with dry-set, laytex/polymer modified Portland cement mortar, or epoxy depending on the backer board manufacturer's instructions.
The handbook notes that the owner should communicate in writing to the project design professional or the general contractor the intended use of the tile installation in order to plan to accommodate expected live load, concentrated loads, impact load, and dead loads, including the expected weight of the tile and setting bed. Proper attention should be paid to spacing of underlayment and subsurface tolerances for thin-set tile installations.
Under hardwood flooring. Quality subflooring is particularly important under hardwood floors, with fastener holding power and panel strength providing an exceptionally solid base for keeping hardwood flooring flat and quiet. Everett Custom Homes in Charlotte, North Carolina, builds approximately three to five high end custom homes each year with each between 4,000 to 6,000 square feet, with the typical house having at least $50,000 worth of hardwood floors installed. Everett's Eric Brown says they use a lot of high end hardwood floors, such as 10 inch wide walnut, and finds that high-performance subfloor panels perform better than other subflooring materials. “You don't have to sand seams, it doesn't rot, it doesn't get soft, and it doesn't delaminate. We don't have problems with floor squeaks, and we've never had a problem with moisture content in the subfloor whenever we are ready to install the hardwood finish.” Says Brown, “Other types of subfloors lose nail-holding power.”
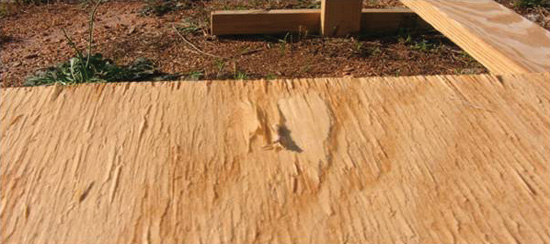
Photo courtesy of Huber Engineered Woods © 2014
For proper installation of a subfloor under hardwood, joists should be spaced a maximum of 19.2 inches o.c. Subfloor panels having a minimum 23/32 inch thickness and subfloor panels should be installed with long dimensions perpendicular to supports. It is important to note that truss and joists systems spaced greater than 19.2 inches o.c. will require additional subfloor thickness. Either a one-inch-thick OSB subfloor, or one that is installed in two layers, with the first layer requiring an engineered wood panel and the second a minimum ½ inch plywood panel, are the two approaches that can be successfully used according to the NWFA.
A big issue in hardwood floors is moisture. With narrow strip hardwood flooring the moisture difference between the subfloor and hardwoods should be no more than 4 percent; with wide plank hardwood flooring, the difference should be no more than 2 percent. In most U.S. states, the recommended moisture content should be no more than 12 percent, according to the NWFA.
For best results in measuring moisture, a pin model moisture gauge calibrated for the species being tested should be used. At least one reading should be taken per 100 square feet of subfloor, and more along walls and near windows and doors. Many installers keep written and often photo documentation as proof that the correct procedures were followed in the event of future problems. Ideally, the building's HVAC system will be operational prior to installation to help acclimatize the wood. When subflooring is installed over a crawl space, polyethylene sheeting should be placed over the ground, and adequate ventilation should be used to help control moisture.
If the levels are found to be excessive, moisture in the subfloor as well as in the rest of the framing can be decreased by drying the structure's interior with heat. Kerosene-fired torpedo heaters are used by many builders to dry interiors, but because one of the byproducts of combustion is moisture, the heated air needs to be vented to the outside. A better alternative is to have the HVAC unit up and running before the finish floor is installed. Forced air systems are also an acceptable method of drying the structure and venting the moisture, with the National Wood Flooring Association recommending a five-day forced air drying period before flooring installation. It goes without saying that a subfloor with a lower moisture absorption rate will obviate the need for many of these approaches.