Subfloor as a Hidden Asset
Subfloors—Parameters of Performance
While every flooring installation is unique and has its own specific requirements for subfloor preparation, performance is primarily a function of three main criteria: moisture resistance, stiffness, and fastener holding strength. Choosing the right material for a subfloor could mean the difference between a successful job or one that is plagued by problems. The most common subfloor materials are plywood, conventional oriented strand board (OSB), and high-performance subfloor panels. High-performance panels are engineered and certified to exceed OSB and plywood PS-2 standards for strength, stiffness, and fastener holding power. In addition, high-performance panels generally have the lowest moisture absorption rate in the industry, leading to better on-site performance especially when weather is an issue. This goal is reflected in building code standards and borne out in tests.
Approved testing and inspection agencies for wood structural panels, specifically OSB, all test and inspect to the same Department of Commerce PS-2 standard; this standard has become a minimum in today's construction practices. High-performance panels are designed to exceed the PS 2 minimums. Such panels will be stamped with an Evaluation Service Report (ESR) number or some other identifying mark. ESRs are reports issued by evaluation services, like the International Code Council (ICC) Evaluation Service. For example, one high-performance panel adheres to ESR 1785, which indicates a commitment to higher standards than those qualified under PS-2 for bending strength, bending stiffness, planar shear strength, axial compression strength, and stiffness. This high-performance panel provides designers with as much as 62 percent better design bending strength than PS-2-level plywood and OSB, 28 percent better design bending stiffness than PS-2-level OSB, and 16 percent better than PS-2-level plywood.
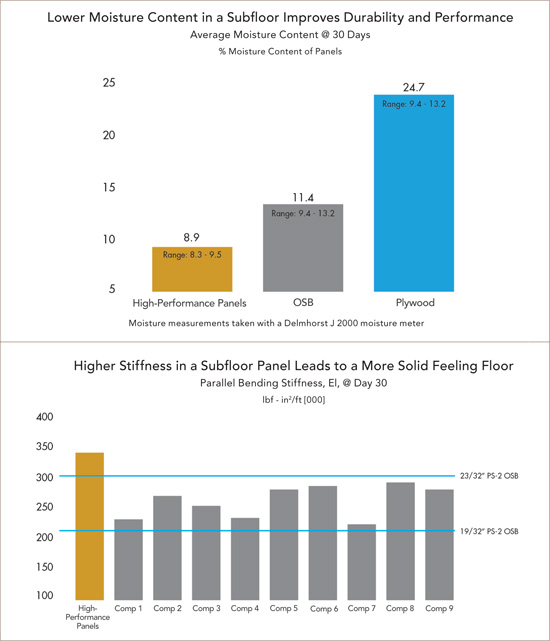
Charts courtesy of Huber Engineered Woods © 2014
One subfloor manufacturer constructed a panel exposure deck that compared thirteen ¾-inch subfloor products, exposing them to the elements for 30 days to gauge their performance under harsh conditions comparable to an actual jobsite. Product samples were analyzed for three key indicators of performance and after 30 days and 6 inches of rain, the high-performance panels ranked highest on average in all three categories. As can be seen in the accompanying charts, high-performance panels achieved the best average results, maintaining a much lower average moisture content which is critical for the integrity of the panel and the ability to deliver strength and fastener holding for hardwood floors. The much higher moisture content shown in the OSB and plywood panels can and does often lead to panel degradation. In fact, after 30 days some of the OSB panels showed stiffness levels below PS-2 code minimums, and others approached code minimums for a 19/32-inch panel.
The difference between high-performance panels, plywood, and OSB is due to several factors. More wood is packed into high-performance panels, which produces a more dense, much stronger panel that securely grips fasteners. Resins also play a very vital role in the engineering of OSB and plywood. Typical manufacturers use powder or liquid based phenol formaldehyde resins that glue strands or veneers together with a secondary, weaker bond. These bonds are more susceptible to moisture due to the sodium content in the resins. Some high-performance panels utilize a premium, advanced resin as their primary binder that reacts chemically with the natural moisture in the wood, creating a much stronger covalent bond with the strands. This bond provides deep and long-lasting moisture protection throughout the panel. In high-performance products, wood strand orientation and size are carefully monitored to achieve maximum strength, stiffness, and fastener holding power. And, unlike other panels that may be sanded on only one side, high-performance panels are sanded on both sides to ensure consistent thickness so every panel lays flat and installs easily.
The result is a stronger, higher-density panel that performs well in the field. High-performance subfloor panels are a little heavier than standard OSB, but they cut and accept fasteners the same as other panel products. Doug Steimle, a project manager for Steven Schaefer Associates, a structural engineering firm based in Cincinnati, says “I don't go into a project without specifying subfloor panels that exceed the minimum PS-2 requirements. If the client chooses to remove them from our specs, he's well aware of the risks that causes to the building's performance.”
A closer look at the performance parameters will give a more complete understanding of the problems that may arise.