Subfloor as a Hidden Asset
Removing Standing Water, Ice, and Snow
High-performance panels remain dimensionally stable in standing water; however, removing standing water to hasten the drying process is advisable on all panels, not just high-performance panels. Sweeping and wet vacuuming are the preferred options. Drilling weep holes on a flat surface will only drain water in the immediate vicinity of the weep hole. Before the framing is erected, the use of a tented tarp system is a good preventive measure, but care must be used to provide airflow between the tarp and wood subflooring to avoid trapping water between the tarp and the wood surface, which may lead to mold and mildew.
During winter months, snow and ice may accumulate on subfloor panels. Although this may present a safety hazard, snow and ice will not normally affect the structural integrity of a high-performance panel. Typical PS-2 OSB or plywood may experience some adverse effects due to snow and ice.
Ice and snow can safely be removed with a number of different options. Dark coarse sand, available at any local hardware or big box store, will absorb heat from the sun, assist the melting process and can help minimize the possibility of slipping. Alternatively, a combination of non-sodium based materials including can be used. Most products can be applied with a simple garden sprayer and are widely available commercially in gallon containers. Once the ice and snow have melted and the building closed in, it is important to ensure the panels have completely dried prior to finish floor installation.
Dusty Bitton, owner of Pinetop Custom Homes, builds approximately five to 10 custom homes a year in McCall, Idaho and surrounding areas. Since McCall has the highest average snowfall in Idaho and the building season is only five months out of the year, Bitton must build his homes as quickly and efficiently as possible. To complete his builds under these challenging conditions, Bitton uses high-performance subflooring among other advanced products due to their quick-installation and moisture-resistant properties. “At times we are unable to complete our builds before the heavy snowfall hits and must depend on moisture-resistant products to prevent any issues until we can continue the building process the next spring,” stated Bitton. “I began building a home last November that were exposed through May. Although the homeowner was worried about mold, the strength and moisture barriers of the products prevented any issues, and we were able to resume building without any delay due to rework.”
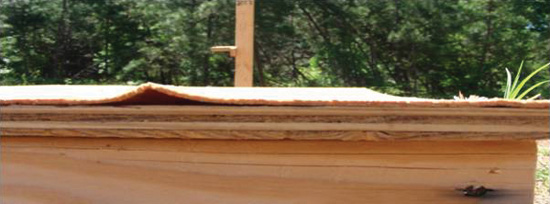
Plywood delamination and damage is the result of wet-dry cycles on a jobsite.
Photo courtesy of Huber Engineered Woods © 2014
Flatness. One key prerequisite for a good installation is achieving flatness. Damaged panels should be repaired or replaced, and swollen seams should be sanded when necessary before underlayments are installed. Note that a cement backer board for tile and a layer of 30 lb. felt for hardwood are often recommended. While felt will raise the coefficient of friction between the hardwood and the subfloor, it will not add moisture resistance. To begin with, the moisture content of the subfloor must be correct. Consistent with the National Wood Flooring Association's (NWFA) definition, a subfloor is flat when the difference in height between two points does not exceed 3/16 inch in 10 feet or 1/8 inch in 6 feet. If the finish flooring type requires substrate flatness tolerances to be more restrictive, some sanding of the subfloor may be necessary. Peaks and valleys in a subfloor can typically be detected by taking a 6-foot or 10-foot level and laying it across the panel surface. If high or low spots in the subfloor exceed the tolerances specified by the finish floor manufacturer, then high spots should be sanded and low spots filled with a leveling compound or other NWFA-approved material. Aside from flatness, the subfloor should be checked for damaged areas and repaired as needed and free of debris such as drywall mud, dust and other debris.
It is the builder's or general contractor's responsibility to provide the wood-flooring contractor with a subfloor that is within the tolerances listed above. The subfloor itself should be inspected carefully. If there is movement or squeaks in the subfloor, it should be resolved accordingly. Refastening may be an option, as is correctly attaching the sill plate to the subfloor. Incorrect attachment of sill plate to subfloor may be a cause of squeaking if the subfloor deflects too much between joists. Protruding fasteners are easily remedied by driving those fasteners deeper into the subfloor. Any roughness or unevenness of the subfloor will result in an unsightly surface on the finish floor and wear on high spots.
With a radiant heating system. As radiant heating systems become increasingly popular it is important to understand their subflooring requirements. Wood subfloor panels are compatible structural members with radiant heating, and the system's temperature, typically ranging from 120 degrees to 135 degrees Fahrenheit, does not affect the performance of the panels. For best results, panels should be installed with the long dimension perpendicular to the supports.
The heating system can be installed either under or over the subfloor, with the tubing laid under the subfloor panels or the electric roll on top of them, according to the radiant heating manufacturer's instructions. Tubing should be attached between the insulation and to the underside of the subfloor using tubing staples between the joist cavities. For the electric roll over the subflooring, a layer of settling material should be applied, per the manufacturer's instructions.