Revolutionizing Ceiling and Wall Surfaces with Parametrics and Digital Fabrication
Environmental Controls: Acoustics
In addition to lighting evaluations, the architects were concerned with the complex acoustics in the airport terminal. They were particularly interested in assuring that airport announcements over speakers were clearly heard by the waiting or walking traveler. In the past, perforated aluminum ceiling panels were mass produced with one or more types of hole openings in a rectangular grid pattern. Any other solution or hole size variation or location in one tile would be cost prohibitive. For the airport concourses, the designers used standard perforation pattern for parts of the ceiling, but they also reviewed custom perforations based on hole sizes the percent of openings while developing a pattern “field” across many ceiling tiles. Each tile is unique with its own unique pattern and location on a ceiling grid.
Since the Airside Modernization project was tasked with using best green practices and sustainability initiatives, the architects chose a fleece sound insulation made from recycled cotton blue jeans, a bonded, ultra-absorbent cotton as part of the ceiling tile sandwich. The engineers investigated the variations in the size of the holes, clusters of holes patterns, and different locations. The acoustic engineer applied appropriate noise-rating criteria, and the ceiling was modeled to meet or achieve those parameters.
The American Society of Heating, Refrigerating and Air-Conditioning Engineers (ASHRAE) develops and provides standards for acoustics in buildings. The primary criteria for noise design criteria are dBA and NC ratings. A dBA rating is a weighted sound level rating noise volumes; for example, ASHRAE recommends that a finished large auditorium has a weighted dBA between 30 and 35. An NC rating defines background noise in a space both existing and achievable in new construction. The airport design team required that the ceilings perform to NC 90 ratings, a high-performance standard for a successful acoustic ceiling tile.
In addition to high-performance acoustic values, the design team wanted the sound equipment to be invisible. It added an AV consultant to the team to evaluate a custom speaker perforation into the ceiling panels. The airport speakers sit on the backside of the ceiling tile, and from the room side, only a small 4.5-inch speaker blends into the ceiling. It was able to measure frequency intelligence across spectrums of audio to make it easier for passengers to hear announcements throughout the concourses.
Environmental Controls: Air Flow and Fire Safety
All drop ceilings are placed to allow for the HVAC, plumbing, communications, and lighting infrastructure to be placed above the habitable space. Ceilings can be designed to be part of the air-circulation system and used as a plenum for air circulation. Parametric design alternatives can include the calculations of the size of perforations in ceiling tiles as related to airflow standards. Additional algorithms will include infrastructure clearances and flame-spread limitations. Using a parametric design and fabrication process removes many of the limitations of manufacturing that used to be out of the control of the conceptual designer.
Construction Controls
Part of the digital design fabrication process is that it can provide a new means of testing design and constructability. The design team for the airport met for a week with the fabricator. The team included all participants for the design of the project: engineers, contractors, and owner’s representatives. The contractor was skeptical of this process and assured the manufacturer that it didn’t need to be there since it could “hang any ceiling” that was designed for the project. By mid-week, the contractor became a willing participant, as it began to see the benefits of real-time modeling of these unique one of a kind, mass-customized ceilings.
Large 36-foot-by-36-foot ceiling models were fabricated for construction on the factory floor to review any difficulties in the ceiling grid for the large, barrel-vaulted Great Hall. The contractors assembled the components, and then the team reviewed any installation problems. Everyday, the contractor would stop after completing a ceiling section and meet with all involved, from tinsmiths to the design team. The team questioned what worked, what didn’t work, and what might help the contractor make the installation easier. Suggestions included adjustments to the ceiling grid, support changes, and different trim pieces. The manufacturer called the fabricator, and new mockups were produced or additional pieces were created over lunch. By working with the fabricator, the contractor was able to adjust the system to allow for easier and faster installation for the completed project. In addition, the owner and the design team were able to view the difference in perforation patterns that could also be remodeled as necessary.
For the University of Oregon facility, Orona commented that using a team process requires that “contractors are working closer with the design team as owners are concerned with efficiency. Contractors need to be abreast of costing and work with manufacturers early to understand how to build and execute our ideas in the fastest most efficient way possible. The close collaboration between the contractor, design team, and digital fabricator is key. There have been various projects that we have partnered with digital fabricators. It seems that as technology advances, the customization of solutions is more prevalent. This need of customization drives the need for digital fabrication.”
Performance Benefits: Warranties
There are many performance benefits to this method of design and construction. According to Orona, “We used products we knew met our specifications in terms of acoustics, lighting, flame spread, etc. Manufacturers typically provide warranties, given the fact that they engineer their products in house. Experience and trial and error in modeling have given them a comfort level to warrant their products. All the products we used for the ceilings were under a warranty of some kind.”
Completed ceilings, walls, glazing, etc. arrive at the site as custom-made pieces labeled with their precise locations. Material use is optimized and waste is minimized, as this form of lean manufacturing produces only what is needed for the job specification.
The benefits of parametric modeling and digital fabrication include:
- More design control and ability to achieve conceptual integrity on all surfaces
- More accurate results for all design parameters
- Lower costs, less material waste, less transportation of unnecessary products, and efficient use of labor
- Ease of client approvals
- Early reviews of constructability
- No long lead times for the production of a customized product
- The ability to exceed codes in every location of the building, as all areas are modeled to achieve performance criteria
- Higher acoustic privacy goals through geometric modeling and sound-reduction panels and ceilings with unique shapes and curves
- High fire ratings along with larger or unique ceiling perforation patterns
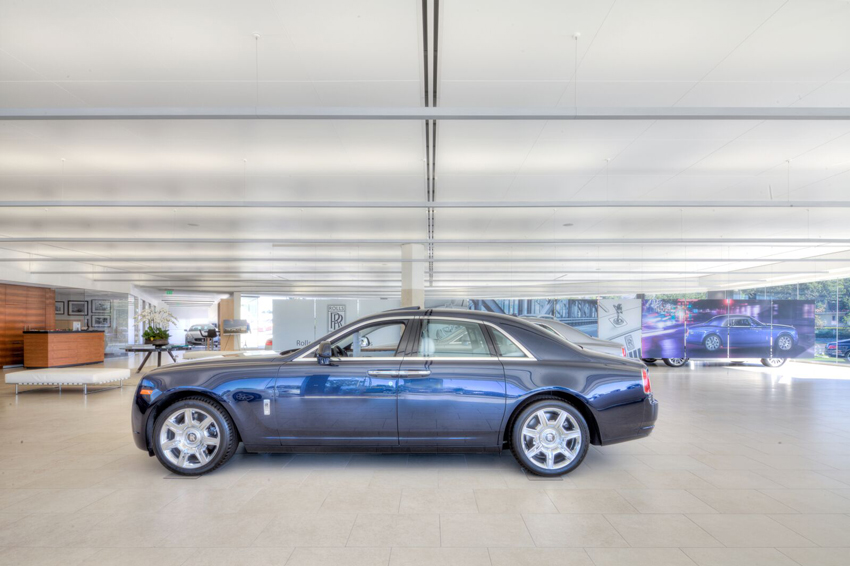
A digital model can provide information on the effect of glare by calculating the desired plane of maximum illumination.
Summing up performance values, Erik Luhtala of Ceilings Plus elaborates on other uses of digital manufacturing. He describes the evaluation of an exterior panel used to screen a glass facade. “The required daylight levels and absorbed energy from sunlight can be balanced inversely by utilizing known data regarding building location, orientation and weather data to iteratively explore perforation locations, size, and depth. Parametric modeling and digital fabrication can achieve a best-case design, where the final product is based on intelligent analysis and delivers the highest-performing results.”