Revolutionizing Ceiling and Wall Surfaces with Parametrics and Digital Fabrication
Parametric Design Defined
Parametric design is a process based on algorithmic thinking that enables the expression of parameters and rules that, together, define, encode, and clarify the relationship between design intent and design response. Parametric design in architecture is not a new concept. Design is a series of relationships and/or principles that alter the end result of aesthetic choices. Any designer understands that by varying parameters, either mathematical or figuratively, a concept can be explored based on a set of design controls. For the Airside Modification project in Atlanta as well as the design of the Great Hall Ceiling at the University of Houston Classroom and Business Building, these design controls included the layering of technical requirements for lighting and acoustics determined by consulting engineers to the design requirements by the architect.
Digital parametric tools allow the designer to create customized form based on projected environmental goals—for example, the acoustic performance values for a concert hall or the foot-candles on a desk plane—while manipulating the aesthetic design of an interior or exterior facade. These tools allow architects to emulate the design of the natural world. They are able to design complex shapes that respond to data-driven parameters.
Many architectural graduates and innovative firms began using automated computer design software programs with building information modeling (BIM). For example, HKS Inc., one of the prime architectural firms leading the Hartsfield-Jackson Design Collaborative joint venture for the design of the Airside Modernization project for the Hartsfield-Jackson Atlanta International Airport, ordered a laser scan of the project that was quickly used to develop a BIM model. One-thousand-million dots were turned into a model the designers were able to manipulate and view with the client. According to Griffin, they collaborated with their MEP consultant, Thompson Consulting Inc., to apply environmental data in the digital model to vary daylighting and LED lighting as they adjusted the aesthetics of the design.
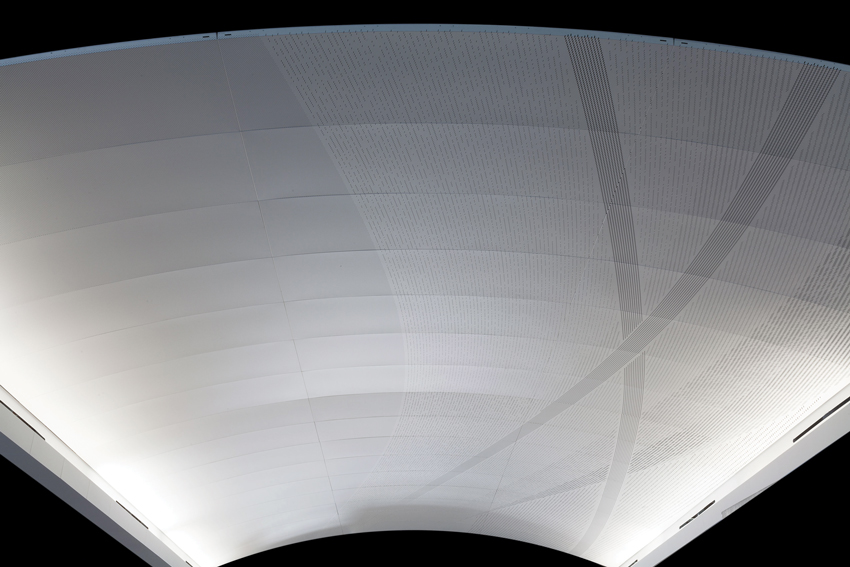
One-thousand-million dots were turned into a digital model of the Hartsfield-Jackson Atlanta International Airport to allow the designers to develop the ceilings for the concourses, holdrooms, centerpoints, train stations, and the train level transportation mall. More than 675,000 square feet of the acoustic ceilings were evaluated for lighting and acoustic parameters through digital and physical models to maintain the conceptual integrity while developing a ceiling that met the highest safety and environmental standards.
Manufacturing Process
The industrial revolution offered the promise of affordably manufactured goods and services that would be mass produced. By the mid-20th century, modernists like Eero Saarinen enlisted manufacturers to develop mass-produced materials built to standard modules to simplify construction processes and manufacturing costs. These revolutionary initiatives led to the deadly conformity of many contemporary commercial buildings. Designers, restricted to selections from the catalogue, found rising budgets limited their ability to conceptualize and they paid dearly for choosing unique shapes and forms.
Manufacturers found that they too could control fabrication processes to create precise materials designed for specific locations. These manufacturers have found that the benefits include meeting demands for faster turnaround times, the creation of more precise forms, and a reduction in material waste. Now manufacturers are partnering with architectural firms as early as the initial design stage. The same data used in the design process can also run an automated production line. After fabrication, each custom-made piece arrives at the project labeled with its precise location for installation. This assures the architect’s aesthetic intentions as well as the performance goals for each building component in a variety of microclimates in a building. See the case study online, Both Sides Now: Mass-Customized Acoustic Cloud Ceilings, for an example of how Gensler achieved both aesthetic and acoustic project goals in the design of the Reading Room at the Quiet Hall for the University of Houston’s Classroom and Business Building.
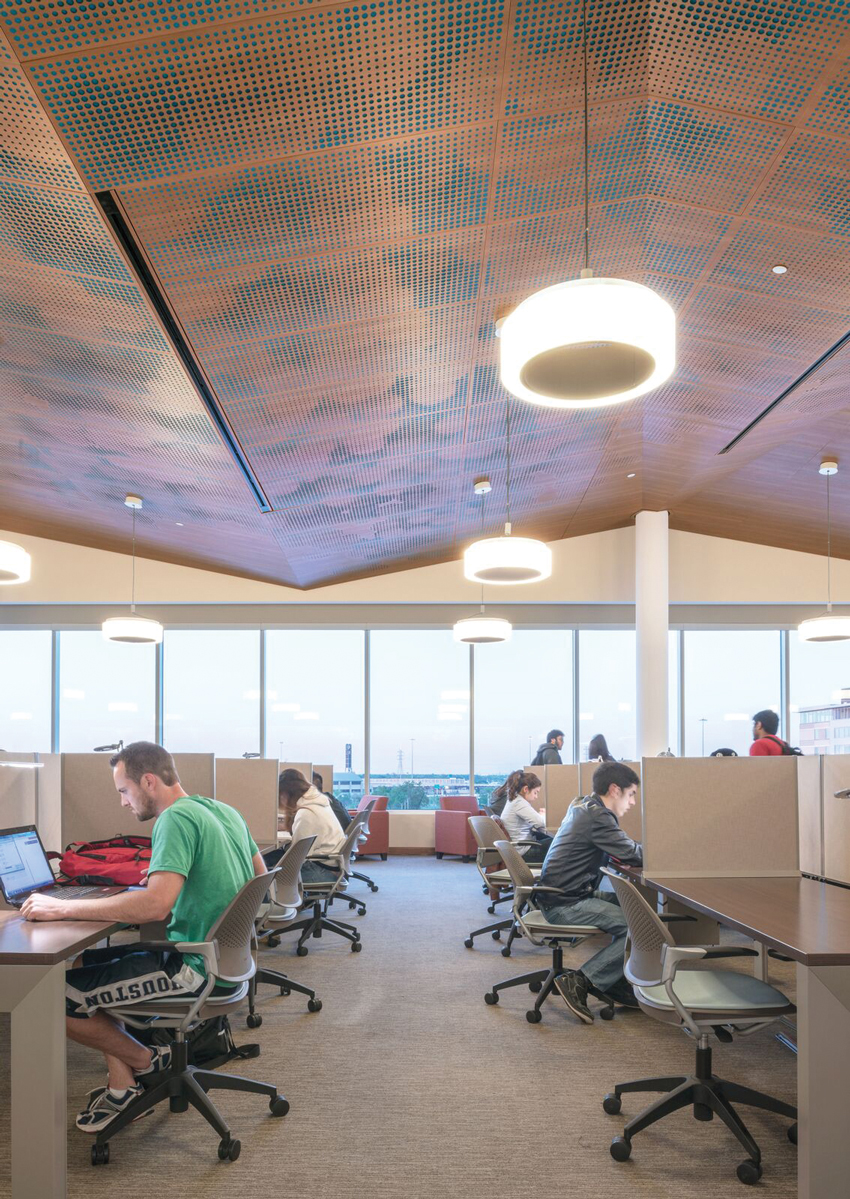
A new collaborative design process used parametric design software combined with digital fabrication to translate the spirit of the New York Public Library’s Rose Reading Room into a new Reading Room at the University of Houston Classroom and Business Building.