Weight Watching: Adaptive Reuse with Structural Steel
Adventures in Steel
Transforming an old mechanical courtyard into an exciting double-loaded steel-framed gymnasium, John Ciardullo Associates took a historic structure—made primarily from steel over the course of 1885, 1899, and 1921—and changed it into a happening academic complex for secondary students at 26 Broadway in Lower Manhattan.
For this particular project, the team was very pleased with steel’s flexibility, which enabled the center core of the building to create a skylight and a large space for a gym.
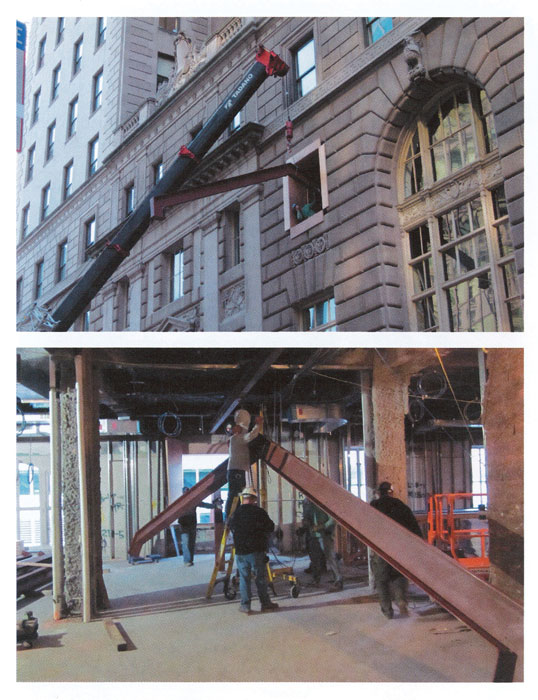

Photo courtesy of John Ciardullo Associates
Structural steel was the material of choice for John Ciardullo Associates’ adaptive use project for Lower Manhattan’s 26 Broadway, where an old mechanical courtyard was transformed into a double-loaded steel-framed gymnasium for a secondary school.
“You can literally put the beams anywhere within the steel structure,” John Ciardullo, RA, NCARB, president, says in a Metals in Construction article (the magazine is published by the Steel Institute of New York).
A concrete construct can be very difficult to analyze structurally because it’s impossible to know exactly what reinforcing steel is in the concrete frame without having to drill into the concrete.
In order to execute this, W18x86 wide-flange beams were brought two stories above street level right into the building’s window openings. Next, the beams were welded at one end of the existing 1921 steel columns while 1-by-1-foot, 10-inch-deep pockets were cut in the 1890s masonry bearing wall resting atop a bearing plate attached, according to Ciardullo. In addition, the roof structure was cross-braced by W12x22 and W14x22 members, which are bolted to the W18s.
The skylight structure itself is created with W14x43 members, set up into five roof sections, which were lifted through the historic building’s windows and into the courtyard.
“The contractor, along with the steel fabricator and erector, came up with the solution of how to bring the steel into the building and put it in place,” says Ciardullo. As each piece was moved into position, the erection crew hung cables from the steel beams above in order not to damage the existing floor below. Whereas a design that utilized heavier material would have been impossible, steel’s light weight avoided the need for the formwork and the wheel mixer required for concrete.
Yet another program requirement was designing a convenience stair in order to connect the school’s four floor levels to limit elevator use.
It was achieved by removing a structural steel column to make room for the opening, something rarely undertaken in concrete construction. The remaining column adjacent to the stair opening was supported laterally by steel beams at each level, so the team had to calculate how many beams could be removed to create the opening.
“I knew the size of the steel column and I had the weight of the steel structure, so we did an analysis to determine the acceptable unsupported height of the column,” he says. “Since I had the size of the columns to calculate the buckling effect and column width by taking out the lateral support at one floor, we were able to then determine that the existing column could take the elimination of the lateral support beam and handle the buckling effect, and the non-lateral support, at each floor.”
Ciardullo also came up with an innovative way to eliminate some bulk from the area where the top of the stair was attached to a lateral steel beam. In most cases, plates are fastened to the top of a wide-flange beam to support the stair risers and treads, but this would have created a very bulky structure. As an alternative, the team cut away the top flange of the lateral beam, welding the top-most stair riser and tread to the beam and thus allowing it to function as the beam’s top chord. The stairs were fabricated in flights from Grade A36 plate and hoisted into the building through a window.
Highlighting another noteworthy Metals in Construction project, TEN Arquitectos tapped into a number of benefits for the Tribeca condo project One York in New York.
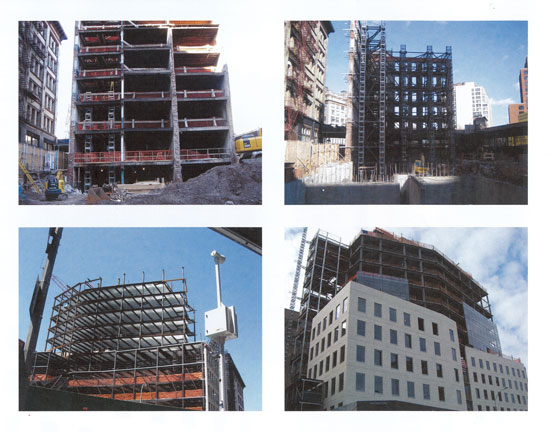
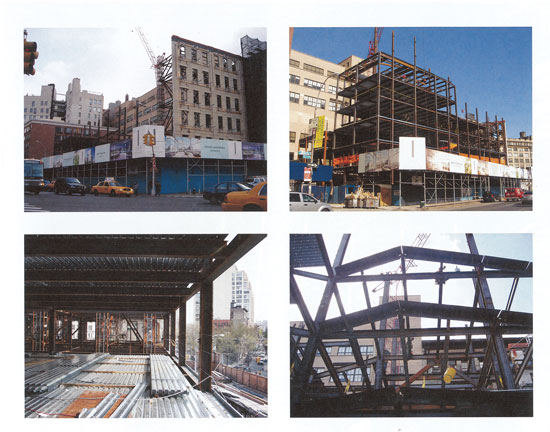
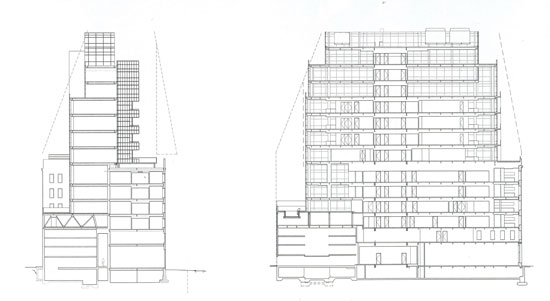
Photo courtesy of TEN Arquitectos
Thanks to its weight, flexibility, speed of erection, ease of reinforcement, and economics, structural steel was selected for New York’s Tribeca condo project, One York, enabling an additional seven new stories worth of high-end amenities and wraparound views, whereas concrete would not have afforded this option.
For starters, weight, flexibility, speed of erection, ease of reinforcement, and economics fared very well for structural steel. Perhaps equally as compelling, steel allowed several choices that a heavier concrete frame could not, including seven new stories’ worth of high-end amenities and wraparound views.
Bringing out an interesting point, DeSimone Consulting Senior Project Engineer Peyrouz Modarres relates that projects such as this, where planning and approvals create a long lead time and fabrication time isn’t as important as rapid construction, there is an opportunity to create a strong case for overcoming what Modarres calls “this false attitude that for residential construction, steel is not suitable.”
For the project, a number of large, relatively light members were used; namely, 12-inch-wide flange beams of ASTM A992 Grade 50, ranging from W12x14 through W12x30, amounting to a total of 876 tons of steel.
In order to contrast the difference between the glass and masonry volumes in the condos, TEN project architect Florian Oberhuber explains that in the apartments, the team wanted the curtain wall to have many horizontals and a wide span between the vertical members and lose the sense of slabs. Since the concrete flooring is a slim, 4¾-inches thick, the curtain wall is connected directly to cantilevered steel plates with welded inserts. Columns were set back from the perimeter about 4 feet along the west wall and 1½ feet along the east, and column sizes include W12x58, W12x72, W12x96, and W12x120, plus W14x257 columns in the elevator core.