Weight Watching: Adaptive Reuse with Structural Steel
Historic Restoration
When it comes to historic restoration projects, structural steel can greatly benefit these unique and challenging endeavors.
Case in point, thanks to a lightweight steel frame, nine floors were added to the existing eight stories of a 1920s steel and masonry warehouse in Manhattan’s Hudson Street without having to reinforce the building foundations. By opening the column grid to as much as 40 feet, as compared to the existing 13-foot-by-26-foot grid, using W36 rolled steel transfer girders the new layout could be conducive to a modern office, while the lower floors maintained a historic loft feel.
“The modern building has been upgraded to meet modern wind and seismic loads by the addition of a new braced steel core around the central elevators and stairs,” relates Gottlieb, who headed up the project for Thornton Tomasetti. “The steel bracing allowed the framing to offset at different floors to address entrances and layout changes required in the building while fitting the core with the existing floor plates. Four columns were inserted into existing masonry flues so as to be invisible within the floor plates while providing support for the new braced frames.”
For another historic reuse project on the Lower East side, Thornton Tomasetti brought in a new floor and roof to a group of five historic brick and timber buildings. The additional stories, “needed to be completed while the ground floor was being occupied,” explains Gottlieb. “A system of lightweight steel columns and girders was added on the existing masonry-bearing walls while the floors were constructed of 8-inch hollow core planks spanning each of three 25-foot spans for the 100-foot length of the building. This kept the weight low while maximizing ceiling heights on the new floor.”
The second phase was the removal and replacement of the ground and second floors with noncombustible floors, the removal of all of the bearing walls, and the installation of the new wind and seismic resisting system. This was achieved by installing new steel columns into chases in the existing bearing walls and then selectively removing the walls and flooring, followed by installing new steel-framed floors with concrete slabs on metal deck.
“The use of steel framing allowed for the very sequenced installation of member transfer of loads from the existing load-bearing members to the new columns and framing while keeping the upper floors fully occupied,” sums up Gottlieb. “This ability to prefabricate and install the framing sequentially was key to making the project possible. This would not have been possible without the use of steel framing.”
For another historic structural steel project, The Architectural Team refurbished a Boston Bay masonry building from the 1900s. As was typical of many early steel buildings of this era, its columns were vertical box trusses made of channels and plates bolted together with first-generation rolled C channels bolted back to back.
This horizontal expansion with structural steel provided the solution to resolve the lateral force deficiency of the existing structure. In this case, the new steel addition was designed entirely with moment connections of sufficient capacity to not only address the lateral stability of the addition, but also for the original building.
Dealing with a more complex undertaking, the Architectural Team had its hands full with the 1923 historic Boston Police Headquarters involving an additional three stories to its existing seven levels.
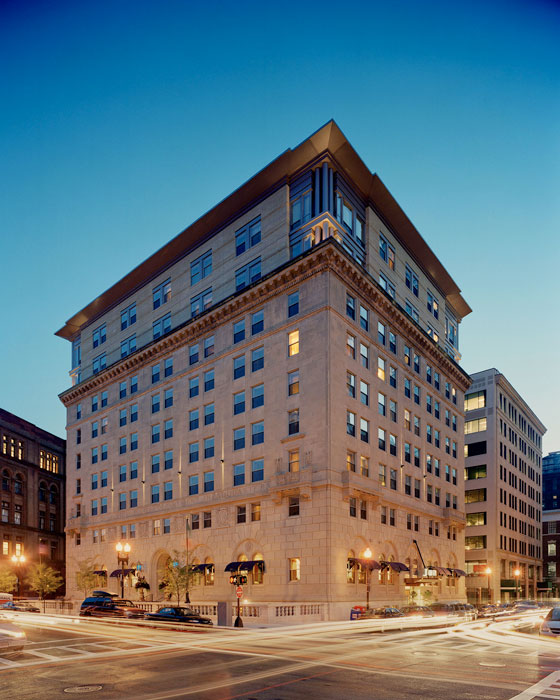
Photo courtesy of The Architectural Team
Adding three new stories to the former seven-story historic Boston Police Headquarters, structural steel was a great choice for The Architectural Team, leveraging speed of erection and dealing with an acute lack of lay-down space.
“While the original construction drawings suggested a concrete strength capacity of 3,500 psi at the columns, Swiss Hammer testing suggested compressive strengths as low as 1,800 psi,” explains Liu. “To make matters worse, the designers discovered that a 3-inch topping slab had been poured over the existing floors, presumably to correct and level poor structural concrete work, adding additional weight to the already overloaded columns. Finally, the original concrete bell caisson foundations were under-designed.”
Given the inadequacy of the existing structure and foundations, concrete was not an option. Rather, structural steel was the logical solution for both of the additional floors, as well as the horizontal addition. Steel also offered the advantage of speed in erection, and its use simplified a critical component of the construction schedule, which involved an acute lack of laydown space in this zero lot line urban project where street closures had to be kept to a minimum.
Yet another Architectural Team Boston North End project, this one at historic waterfront warehouse structure, involved the removal of two floors and the addition of three new floors with structural steel. “The implementation of new structural steel permitted the designers to eliminate alternating rows of columns, doubling the span of the structural bays and, in combination with a dramatically increased ceiling height, create dramatic, open, light-filled interiors in these new upper floors,” reports Liu.
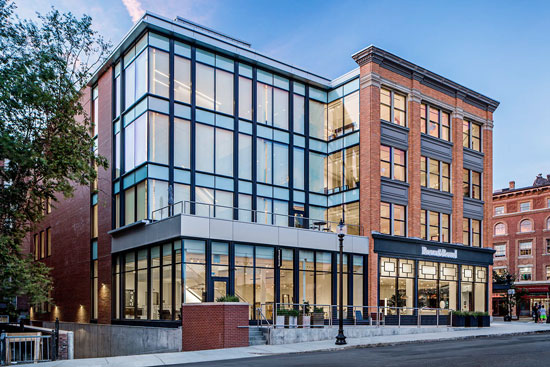
Photo courtesy of The Architectural Team
Horizontally expanding this historic Boston Bay project at 375 Newbury, structural steel enabled The Architectural Team to resolve the lateral force deficiency of the existing structure.
Lateral forces were addressed at lower floors with reinforced shotcrete stiffening of existing exterior walls, while moment connections were used at the new three upper floors to maintain the open spaces free of cross-bracing.
“Like many steel buildings of its era, the archaic steel superstructure of the original 1903 building was fireproofed by encasing the built-plate members in concrete. Selective demolition of the concrete encasement of a representative sampling provided sufficient information to determine performance characteristics for reinforcement, which was accomplished by removal of the existing non-structural concrete jackets and their replacement with formed and reinforced concrete surrounds.”