Structural Steel for Low-Carbon-Emission Lightweight Frames
A particularly promising area for WAAM is “complex-geometry diagrid structures,” says Mathew Vola, an Arup Fellow and director specializing in computational design, who leads Arup's structural-engineering practice in the Netherlands and worked with MX3D on the bridge. “If you create the node with printing, you can have standard steel members, circular sections, or maybe even timber members, and then if you make the connection in steel and solve all the complexity within that joint, I see a future for this technique.” With 3D printing, “we can deposit our material where we want,” Vola explains; it becomes possible to “look at structural optimization algorithms to see where the material needs to be... That's something [that] with traditional steel beams you cannot do.” As a different set of Arup engineers did on a large scale with the irregular diagrid of OMA's CCTV tower in Beijing two decades ago, the bridge engineers were able to add and subtract material proportionate to local stresses, here with the nuanced curves of computationally aided design. The process contributed to the bridge's aesthetics: “We found that if you start putting some curvature in plan in the bridge,” Vola says, “even though it's typically a U profile, the stress patterns become pretty beautiful.”
Some aspects of the design, Vola recalls, evolved to meet Dutch code requirements: gaps in guardrails must be small enough that children's heads can't fit through them, limiting the size of the holes. Others were simply practical: “It was also installed in the red-light district, so people with high heels had to walk over this bridge.” While celebrating the success of the experiment, he cautions against overenthusiastic inferences from a two-year project, too short to assess long-term fatigue and crack propagation, and still involving uncertainties: “The problem with printing a bridge is, obviously, you don't know the material properties; you don't know the steel quality that you get, because you don't know the printing conditions, like for example humidity; you don't know the tolerance of the printing of each little drop; you don't know the exact temperature of the drop when it comes down. So there's the geometrical inaccuracies and imperfections. There's microstructure behavior, which creates your stresses because, for example, if the printer's process pauses for a while, the steel cools down, and then it heats up again.” MX3D's bridge withstood extensive scrutiny: a promising precedent for a new method, yet an n=1 sample size all the same.
One other reason for caution is that the bridge's weight (about 4,500 kg of stainless steel) entails a formidable embodied-carbon metric. Philip Oldfield of the University of New South Wales in Australia tweeted a quick calculation after it opened in 2021: “Stainless steel has an embodied carbon of 6.15 kg CO2/kg. This bridge, then, has an #embodiedcarbon of at least 27.7 tonnes of CO2 to span a few metres” (Oldfield). Though a prototype project would not realistically be expected to satisfy standard energy-performance criteria for building or infrastructure typologies, the critical question is whether the discoveries it makes possible will create environmental benefits in the long run.
Vola acknowledges that “the cost of material per unit is not offsetting the saving in the material at the moment,” that the printing process is energy-intensive, and that downtime in any form of robotic fabrication can be costly, so that, for now, scaling up to produce large structures may prove less likely than niche production of smaller ones. Such applications will enjoy advantages in customized design, speed to market, and reduction of material waste, perhaps translating into improved metrics for embodied and operational carbon. Discussions are reportedly under way about a second-generation bridge. Gardner, meanwhile, notes that “whilst other bridges like this could be made, the way I see it is that for the wider use of this technology, we need to be looking at more mundane connections between beams and columns: the kinds of things that are on every structure, not just on special ones.”
The bridge, says van der Velden, “was never intended to prove a lower carbon emission compared to the currently most effective way to cross a few meters. We intended to show it was possible to use 3D printing for a structural application in the first place. This first step was necessary in order to make the next one: i.e., fabricate a bridge with significantly less material that current building methods would require.” He looks to material efficiencies for environmental and economic advantages: “There's a lot of weight in a steel beam that doesn't necessarily have a lot of function in some of the places. If you use an I-beam or an H-beam and then the biggest load is on a certain point, and then other points are stronger than they necessarily have to be, that's what with 3D printing you can tackle. You can basically make a much more efficient beam or shape that has the same safety and capacity as you need, but nothing more, and therefore reducing the footprint and the weight of a bridge or structure.” Life-cycle assessment was performed from the beginning of the bridge project, despite the inherent difficulties of comparisons between a unique structure and conventional predecessors; though emissions measurements with WAAM involve the additional step of producing wire feedstock, van der Velden says, “if you then start saving material, then the numbers look really good for the 3D printing.” Comparisons with milling processes, he adds, where material is wasted, favor 3D printing more decisively.
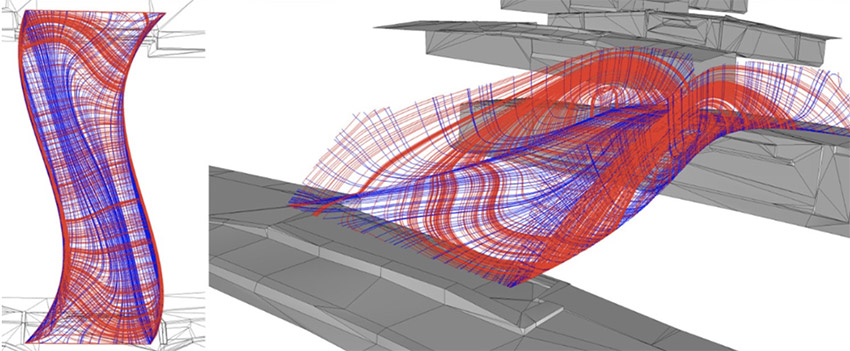
Image courtesy of MX3D
Figure 9. Images from structural analysis of MX3D's bridge.
CONCLUSION
Criteria for selecting structural metals, Houska summarizes, include longevity, suitability for an application environment (e.g., stainless steel where corrosion resistance is a priority), energy absorption (with steel obviously preferred to aluminum if temperatures are high or blast impact is a risk), and now environmental resilience: once a value-added option, now a central driver of ideas. The sustainable-steel field is maturing, though the various parties involved in design, procurement, regulation, and construction decisions often operate from different information bases.
Pilarczyk reports that clients are often aware of LEED, the best-publicized among green standards in the U.S., but less informed about the specific goals the program sets for structural steel or any other element. “When we're talking to folks about sustainability in general, and we ask them, 'What are your sustainability goals for this project?', a lot of times what we get back is, 'Well, we're looking for LEED certification of some sort.' I think that's a definition that's ingrained... that's synonymous with sustainability. But really, we're talking more in depth about the embodied carbon of the steel and of the building itself, and not necessarily the LEED ratings.” More specific metrics for sustainably sourced materials logically lead to better-informed decisions. Pilarczyk describes before the Buy Clean Initiative, meeting designers and owners who had good intentions and would say “'We want to take the industry average and cut it in half,' and set those limits as the threshold for all the steel on their projects. And then we start to realize there's no steel that's made in the world that can meet these.”
Well-intentioned but haphazard alternatives to BAU are now giving way to clearer standards and, equally important, attention to suppliers' capability of meeting them. “The challenge that we're seeing now is, how do we actually have the procurement and supply chains in place to make sure that we're meeting the thresholds that are being set?” When one facility out of several has the lowest number on an Environmental Product Declaration (EPD), Pilarczyk says, “if everybody said that they wanted all their steel to come from that one facility, it just would totally disrupt the supply chain that's out there.” Locations of mills and logistical planning can span the gap between intentions and performance; “certain materials travel [or] are more regional than others. A beam mill like we have in Arkansas is completely capable of supplying steel across the country, just based on the rail systems, the rivers and barge systems, or just on the back of trucks.... It's when you start looking at materials coming from overseas and some of the disruptions that we saw in the last couple of years, with canals getting stopped up, changes on a project, or material that's incorrect, having to reship those from overseas can really cause major disruptions to the projects.” Fortunately for U.S. architects and steelmakers, and arguably for the planet, the facilities using the most progressive technologies are proliferating, and the operators of the others are presumably paying attention.
WORKS CITED
1American Institute of Steel Construction. Buy Clean Guidance for Structural Steel Products. Nov. 2, 2022. https://www.aisc.org/contentassets/937a380ddd404a2da0c48669d438bf3b/buy-clean-guidance-for-structural-steel-products.pdf.
2Architecture 2030. Why the Built Environment? https://www.architecture2030.org/why-the-built-environment.
3Baqershahi MH, Ayas C, Ghafoori E. Design optimisation for hybrid metal additive manufacturing for sustainable construction. Engineering Structures, February 2024. DOI: 10.1016/j.engstruct.2023.117355.
4Brady T, Eggert R. Ferrous scrap’s role in decarbonizing steel: assessing steel product lifespans. Steel Manufacturers Association, May 3, 2023. https://acrobat.adobe.com/link/track?uri=urn%3Aaaid%3Ascds%3AUS%3A7ebd5f57-ae76-3810-93aa-1b3b586345d2&viewer%21megaVerb=group-discover.
5Carbon Leadership Forum. The Carbon Challenge. March 31, 2020. https://carbonleadershipforum.org/the-carbon-challenge.
6Gardner L. Metal additive manufacturing in structural engineering – review, advances, opportunities and outlook. Structures 2023; 47: 2178-2193. https://doi.org/10.1016/j.istruc.2022.12.039.
7Gardner L, Kyvelou P, Herbert G, Buchanan C. Testing and initial verification of the world’s first metal 3D printed bridge. Journal of Constructional Steel Research 2020; 172, 106233. https://www.researchgate.net/profile/Leroy-Gardner-2/publication/342822366_Testing_and_initial_verification_of_the_world%27s_first_metal_3D_printed_bridge/links/5f0cc4f8299bf1074456ce40/Testing-and-initial-verification-of-the-worlds-first-metal-3D-printed-bridge.pdf.
8Giusti AC, Leggate J. US Steel, Nucor build major mills amid steelmakers' modernization. Engineering News-Record, Jan. 14, 2022. https://www.enr.com/articles/53439-us-steel-nucor-build-major-mills-amid-steelmakers-modernization.
9Global Steel Climate Council. The Steel Climate Standard: Framework for Steel Product Certification and Corporate Science-Based Emissions Targets. August 2023. https://globalsteelclimatecouncil.org/wp-content/uploads/2023/12/GSCC-Standard-August2023.pdf.
10Greenhouse Gas Protocol. Corporate Value Chain (Scope 3) Accounting and Reporting Standard: Supplement to the GHG Protocol Corporate Accounting and Reporting Standard. https://ghgprotocol.org/sites/default/files/standards/Corporate-Value-Chain-Accounting-Reporing-Standard_041613_2.pdf.
11Hasanbeigi A. Steel Climate Impact: An International Benchmarking of Energy and CO2 Intensities. Global Efficiency Intelligence, St. Petersburg, Fla., 2022. https://static1.squarespace.com/static/5877e86f9de4bb8bce72105c/t/624ebc5e1f5e2f3078c53a07/1649327229553/Steel+climate+impact-benchmarking+report+7April2022.pdf.
12Kyvelou P, Spinasa A, Gardner L. Testing and analysis of optimized wire arc additively manufactured steel trusses. Journal of Structural Engineering 2024: 150 (3). https://doi.org/10.1061/JSENDH.STENG-12832.
13Meng X, Weber B, Nitawaki M, Gardner L. Optimisation and testing of wire arc additively manufactured steel stub columns. Thin-Walled Structures 2023; 189: 110857. https://doi.org/10.1016/j.tws.2023.110857.
14Muslemani H, Liang X, Kaesehage K, et al. Opportunities and challenges for decarbonizing steel production by creating markets for ‘green steel’ products. Journal of Cleaner Production 2021; 315:128127. https://static1.squarespace.com/static/596a539de4fcb5edd0dad77f/t/60f97aa84d80571ef0fa72ce/1626962606599/Muslemani+et+al.+2021+JCP.pdf.
15Nippon Steel Corporation. Start of studies to shift from blast furnace steelmaking process to electric arc furnace steelmaking process. News release, May 10, 2023. https://www.nipponsteel.com/common/secure/en/news/20230510_400.pdf.
16Oldfield P. Post to Twitter (now X), July 18, 2021. https://twitter.com/SustainableTall/status/1416729492748345349.
17Reed S. How to clean up steel? Bacteria, hydrogen and a lot of cash. New York Times, March 17, 2021; updated May 14, 2021. https://www.nytimes.com/2021/03/17/business/steel-emissions-arcelor-mittal.html
18Shah IH, Hadjipantelis N, Walter L, et al. Environmental life cycle assessment of wire arc additively manufactured steel structural components. Journal of Cleaner Production 2023; 389: 136071. https://doi.org/10.1016/j.jclepro.2023.136071
19Shen X, Myllyvirta L. China’s steel sector invests USD 100 billion in coal-based steel plants, despite low profitability, overcapacity and carbon commitments. Centre for Research on Energy and Clean Air, Aug. 1, 2023. https://energyandcleanair.org/publication/chinas-steel-sector-invests-usd-100-bn-in-coal-based-steel-plants-despite-low-profitability-overcapacity-and-carbon-commitments/.
20State of California. Buy Clean California Act: Public Contract Code Sections 3500-3505. Passed Oct. 2017; effective Jan. 1, 2018. https://www.dgs.ca.gov/PD/Resources/Page-Content/Procurement-Division-Resources-List-Folder/Buy-Clean-California-Act.
21United States Code, 2014 Edition. Title 23 – Highways, Chapter 3 – General Provisions. Sec. 313 - Buy America. U.S. Government Publishing Office, www.gpo.gov. https://www.govinfo.gov/content/pkg/USCODE-2014-title23/html/USCODE-2014-title23-chap3-sec313.htm.
22United States, Executive Office of the President [Joseph Biden]. Executive Order No. 14057. Catalyzing clean energy industries and jobs through Federal sustainability. Federal Register Vol. 86, No. 236, December 8, 2021. https://www.govinfo.gov/content/pkg/FR-2021-12-13/pdf/2021-27114.pdf.
23U.S. Department of Energy. Industrial Decarbonization Roadmap. Publication DOE/EE-2635. Washington, DC: September 2022. https://www.energy.gov/sites/default/files/2022-09/Industrial%20Decarbonization%20Roadmap.pdf.
24U.S. Energy Information Administration. Manufacturing Energy Consumption Survey (MECS): 2018 MECS survey data. Feb. 23-Aug. 27, 2021. https://www.eia.gov/consumption/manufacturing/data/2018/. See Table 3.2: Energy Consumption as a Fuel by Manufacturing Industry and Region.
25U.S. Energy Information Administration. Natural gas explained: natural gas and the environment. Nov. 7, 2022. https://www.eia.gov/energyexplained/natural-gas/natural-gas-and-the-environment.php.
26U.S. Environmental Protection Agency. Reducing embodied carbon of construction materials through the Inflation Reduction Act. Sept. 28, 2023. https://www.epa.gov/greenerproducts/reducing-embodied-carbon-construction-materials-through-inflation-reduction-act.
27World Steel Association. Worldsteel announces the 2022 Steel Sustainability Champions. News release, April 12, 2022. https://worldsteel.org/media-centre/press-releases/2022/worldsteel-announces-the-2022-steel-sustainability-champions/.
28World Steel Association. Sustainability Indicators: Sustainability Performance of the Steel Industry 2004-2022. Brussels, 2023. https://worldsteel.org/wp-content/uploads/Sustainability-indicators-report-2023.pdf.
29Wynne Z, Buchanan C, Kyvelou P, et al. Dynamic testing and analysis of the world's first metal 3D printed bridge. Case Studies in Construction Materials 2022; vol. 17: e01541. https://doi.org/10.1016/j.cscm.2022.e01541 (https://www.sciencedirect.com/science/article/pii/S2214509522006738).
30Zhang M, Chow E. China plans to increase iron ore output, boost use of steel scrap. Reuters, Feb. 7, 2022, https://www.reuters.com/article/idUSL1N2UI0FL/.
Bill Millard is a New York-based journalist who has contributed to Architectural Record, The Architect’s Newspaper, Oculus, Architect, Metals in Construction, OMA’s Content, and other publications.