Structural Steel for Low-Carbon-Emission Lightweight Frames
The Dutch additive-manufacturing startup firm MX3D, a spinoff from the design agency Joris Laarman Lab, surprised observers (and themselves) by creating the world's first functional 3D-printed stainless steel pedestrian bridge, which from 2021 to 2023 was placed across the Oudezijds Achterburgwal canal in Amsterdam's medieval-era red-light district, De Wallen. The proof-of-concept project was the culmination of a lengthy process of experimentation, testing, and approval; those involved were astonished to find how readily the bridge passed loadbearing tests, then withstood heavy foot traffic while open to the public. With important caveats, particularly about energy consumption and emissions, this method could transform certain segments of the steel design and construction fields. Also known as wire-arc additive manufacturing (WAAM), a technology first reported in 1925 when Ralph Baker patented a method of using an electric arc as the heat-energy source for making metallic ornaments, it offers observers the semi-magical sight of robotic arms essentially drawing fully formed structures in open space.
Gijs van der Velden, founder and CEO of MX3D, recalls the firm's early explorations with concrete, resins, and other printable materials after initially purchasing a robot in 2011. “Our goal was basically to see if we could realize these advantages of 3D printing,” he says: “saving materials, more geometric freedom, a new design language.” Chief technical officer Tim Geurtjens had the idea of attaching a welding machine, and after sharing experiments via YouTube from the outset, the firm attracted interest from Autodesk, Arup, ArcelorMittal, and academia. Additional projects with complex geometries in 3D-printed steel have included chairs, benches, bicycles, and maritime propellers.
“We came up with an idea that we could do together with this community, and that was the bridge,” van der Velden continues. “So we said, 'Let's just come up with the wildest idea that we think could be done with a technology like this.' It's maybe a little bit over the top, but it's going to hopefully inspire a lot of people to do the same.” The work, begun in 2015 and carried out over three years in collaboration with engineers from Imperial College in London, the University of Twente in Enschede, and Arup, proceeded from printing test plates to printing segments of the bridge to finite-element (FE) modeling and tests of the segments, and eventually to printing the full 10.5-meter-long structure (see Figures 5-8) for initial public unveiling during Dutch Design Week 2018.
Welding two parts together typically creates a weak point, van der Velden says, but printing layer upon layer amounted to “creating a full homogeneous material that doesn't have that same problem as a typical weld does.” With no building code applicable to the unprecedented material and design, the team developed a testing plan to determine whether test results would correspond to the behavior of the full structure; after destruct tests on pipes, connections, and other segments, they proceeded to print a 2.5-meter length of the bridge, then the complete bridge.
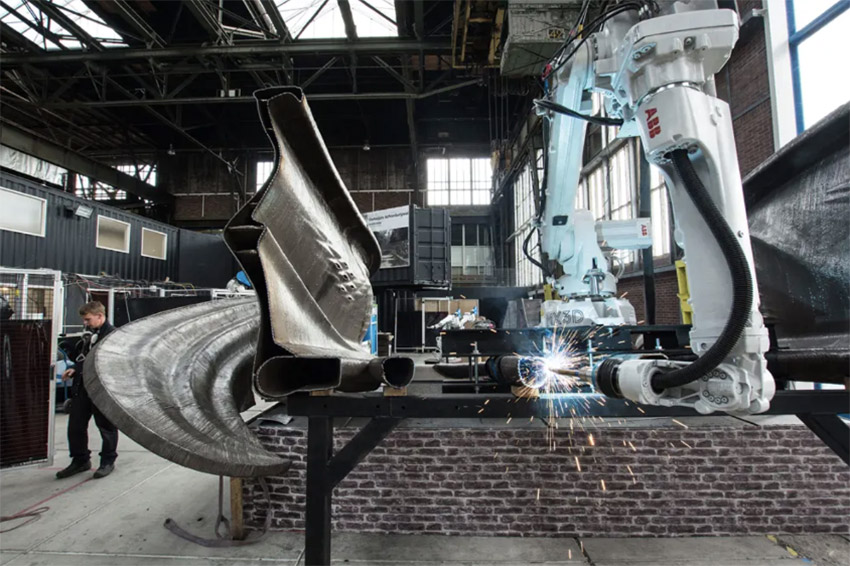
Photo © Olivier de Gruijter; courtesy of MX3D
Figure 6. Printing of MX3D's bridge in progress.
Initial plans to conduct the printing in situ were abandoned as a safety precaution and to minimize security costs; instead, when the permit was approved, it was printed offsite and craned to the canal for installation. Permitting, as one might expect with a radical design in a historic neighborhood, was a slow process, though interest on the part of Dutch Queen Máxima helped expedite the effort. Negotiations with urban preservationists led to a decision to install the bridge as a two-year art project rather than a permanent feature; it remained in place from its opening in July 2021 to October 2023 before removal to another site for further testing.
“We didn't have unlimited time and budget,” van der Velden recalls, “so we said, 'Yeah, we're just going to print the whole thing, and then we're going to test it at the end, well over the design load.” Without claiming to understand the new material thoroughly yet, MX3D built in enough extra mass and structural redundancies to withstand more stress than it would encounter with “human jumping at the maximum capacity.” Even with the material reduced by 20 to 30 percent, he estimates, structural integrity would not have been compromised.
“The first bridge, basically, was over-safe,” van der Velden summarizes; “it's really way too heavy, still, for a 3D-printed bridge, which typically should be lightweight. But we felt that the biggest achievement of the project would be just to show that it would be possible in the first place.” The final design by Laarman included a substructure, handrails, deck plate, end beams, and non-structural decorative curving forms that impart a futuristic and biomorphic aesthetic; all parts except the deck plate and end beams were created through WAAM with six-axis robots. The structure is also a “smart bridge” incorporating a system of structural and environmental sensors developed by Arup and Autodesk. These include load cells, strain gauges, displacement transducers, inclinometers, accelerometers, and thermistors (Wynne et al.), allowing detailed analysis of performance during public use and feeding data into a digital twin of the bridge maintained by the Alan Turing Institute's Data-Centric Engineering Programme in London.
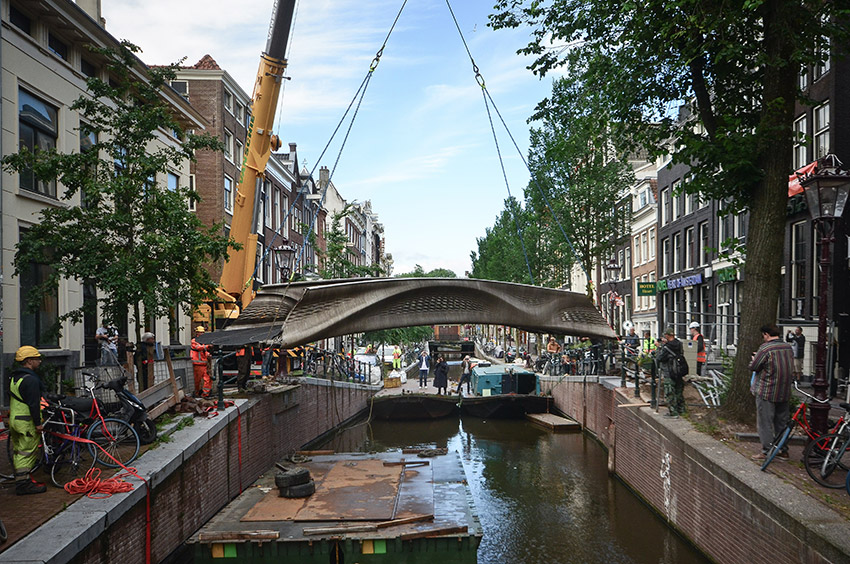
Photo © Adriaan de Groot; courtesy of MX3D
Figure 7. Placement of MX3D's bridge by crane, July 2021.
Leroy Gardner, PhD, FREng, professor of structural engineering at Imperial College in London, headed the academic consulting team on the project. After performing tensile coupon tests to determine mechanical properties, rigorous FE analysis in Abaqus to verify Arup's simpler early models (see Figure 9), tests of parts of the bridge to destruction, then loading tests of the full bridge conducted at the University of Twente in Enschede, withstanding up to 20 tons (beyond the design load), the Imperial group confirmed that it would be fit for purpose (Gardner et al.). Local authorities required the challenging loading tests, he recalls, to ensure public safety with a type of material and infrastructure for which no standards existed. Dynamics under footfall loading, like the harmonic movements that made London's slender Millennium Bridge notoriously unstable at first, were “not a particular issue” here, he reports, because the massing and form of MX3D's bridge were more robust.
The design was driven architecturally rather than by material-conservation considerations, Gardner says. “There's always a little bit of a tradeoff between the exotic shapes that you can produce versus making it as structurally efficient as possible. For me, the most important thing is about the potential of 3D printing to enable optimized shapes, and minimum-material-usage structures, to be realized.... With 3D printing, it is as easy to make optimised shapes as uniform shapes, unlike with traditional manufacturing, so you can put the material where you need it, using less material. And for me, 3D printing or additive manufacturing and optimization go hand in hand. Working together, I think that will be a way of reducing the carbon footprint of structures in the future.” Scaling approaches like MX3D’s up to a replicable status, rather than require extensive bespoke testing in each case, will depend on whether codes will shift to accommodate advances such as computationally assisted design. Gardner is active in code development in Europe and the U.S., though he acknowledges that “in terms of codes for additive manufacturing, and particularly for additively manufactured structures, it's still very early days.”
Mattia del Giacco, PhD, chief operating officer at the Swiss firm Montanstahl AG's Conroe, Texas, subsidiary Stainless Structurals (a downstream manufacturer that was not involved with the Amsterdam bridge but uses related laser-welding methods), comments that “when you use new technology like 3D printing or laser welding, you can go closer and closer to what the architect or the engineer or the designer needs, and this minimizes the waste. If in the past you had to design with standard shapes, so you have to buy a 20-footer even though you need 12- or 14-foot long bars, nowadays it's more and more common to be able to source the 14 feet or whatever length you need.” Limitations of current powder-fed 3D printing, he says, are a matter of productivity and speed: “We're talking about maybe one ton per day of deposition, which is very low in the steel industry.” Bespoke 3D printing extends the material saving over standard members to a precise degree, del Giacco finds, liberating architects from the options found in catalogs. “A key point for architects and designers,” he says, “is try to find a manufacturer who can really start from their ideas and make it become reality without wasting material or energy.”
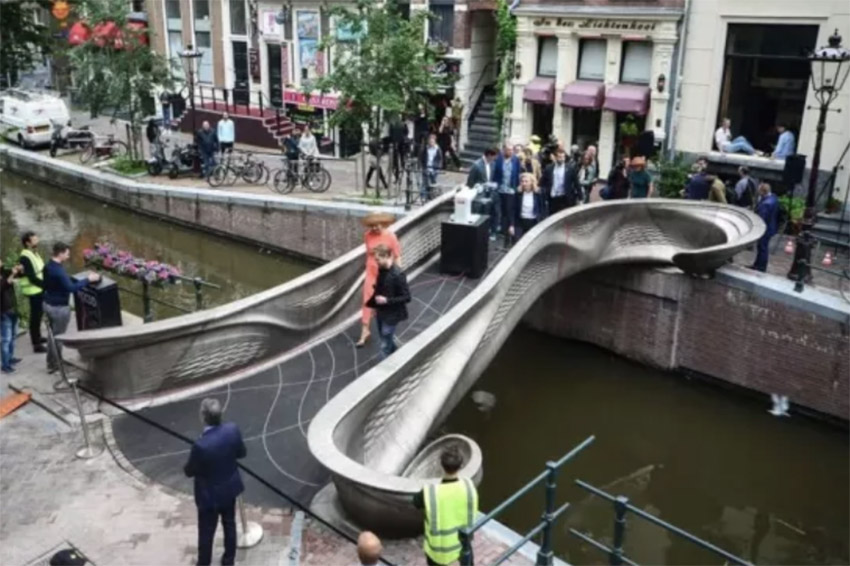
Photo © Adriaan de Groot; courtesy of MX3D
Figure 8. Queen Máxima of The Netherlands opens MX3D's metal 3D-printed bridge in Amsterdam, July 2021.