Architectural Millwork: Molded vs. Fabricated
Using Molded Millwork
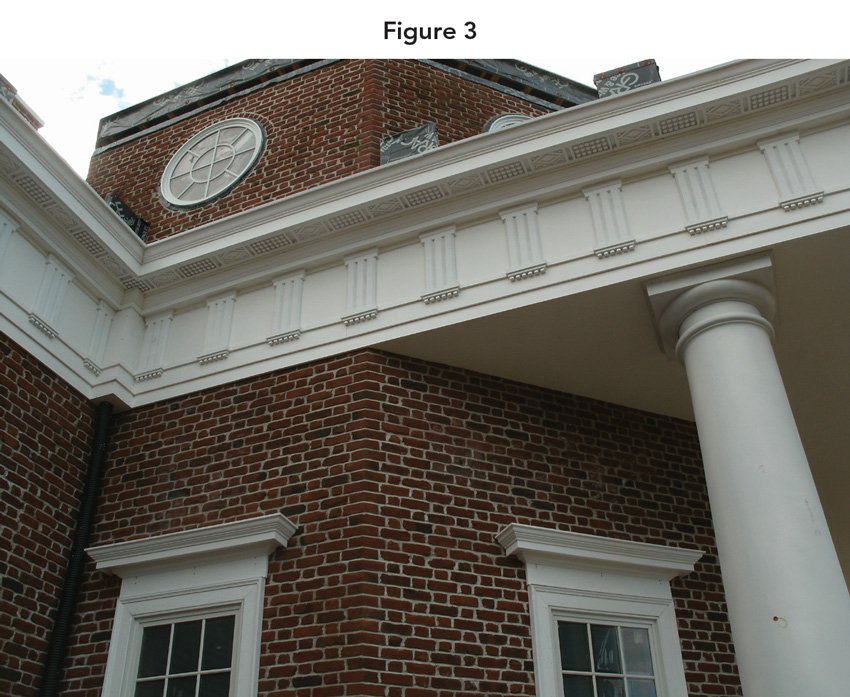
This may look exactly like a detail of Thomas Jefferson’s famous mansion in Virginia, but it is actually part of a complete, minutely accurate, full-size historic reproduction of the entire mansion, recently completed in Somers, Connecticut. Many of the materials used are identical to the originals at Monticello, such as the handmade red brick on the exterior and the copper downspouts. But, the precisely reproduced exterior and interior trim and other millwork details are cast from molded polyurethane.
As mentioned above, the catalogues of some molded millwork manufacturers will include thousands of components that can be ordered off the shelf so for many projects the specification process is streamlined. But, some manufacturers specializing in custom designs can take the concepts of an architect from idea to sketch to finished product. For example, Figure 4 is the shop drawing developed for the custom peaked trellis in Figure 5.
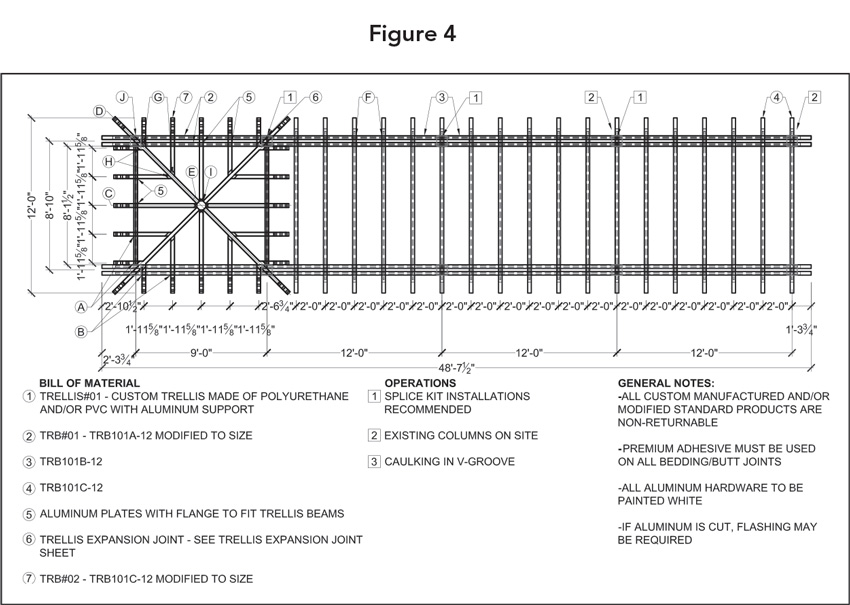
Shop drawing for trellis
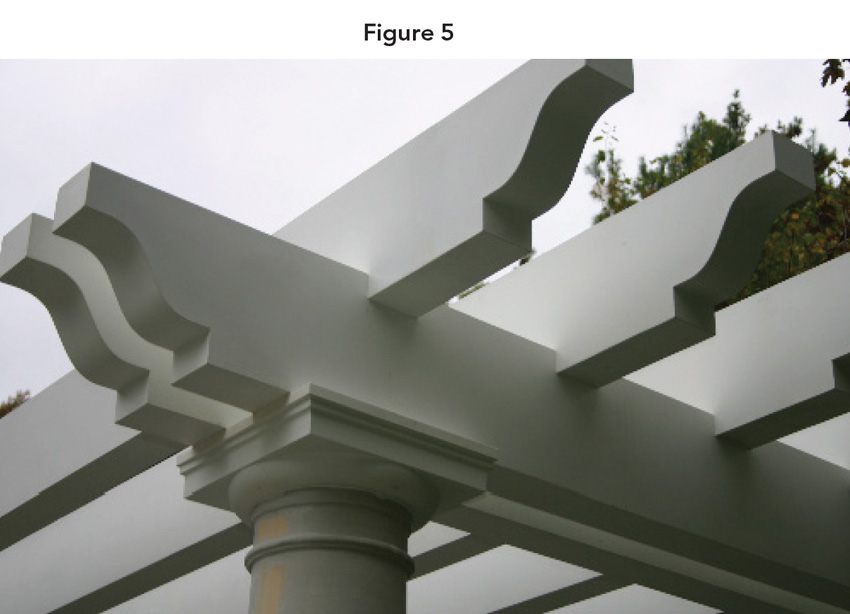
Finished trellis
The process is often used for creating original, brand-new designs. But, it can just as easily be used to make meticulous reproductions of existing pieces of millwork for historic renovations or for using past forms as inspirations for new projects. In Figure 6, deteriorated building components were reproduced in high-density polyurethane. In the reproduction of Thomas Jefferson’s Monticello shown in Figure 3, the challenge for the architects was to recreate an accurate, authentic appearance for a sophisticated new home with a modern floor plan, features, and amenities. (One other advantage of modern materials: the reproduction “Monticello” was completed in 15 months as opposed to the decades lavished on the original.)
See sidebar “Old Is New Again” for other examples.
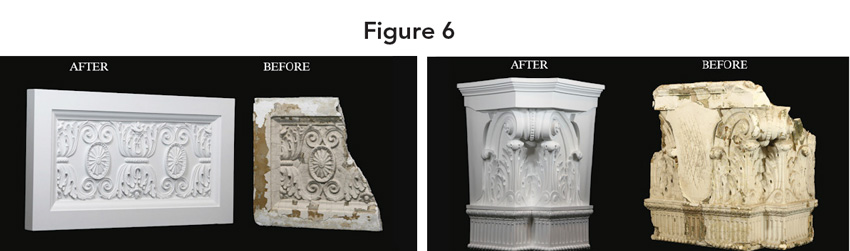
Before and after
The technology, process, and materials in these projects can be applied to virtually any millwork application. A sample specification section for a molding is shown at the end of this course.
Some of the key basic choices to be considered include:
Surfaces
Very detailed, custom surface textures and finishes can be specified. For other types of products, millwork can be shipped with a paint/primer, ideally guaranteed for at least five years. This standard paint is ready to accept field-applied finish coats of paint as required. During the installation process, discussed further below, screws are typically installed through the face of the product so most will require a final coat of paint after the product is installed, and any screw holes or seams can be repaired. Dark colors are desired in high solar gain areas, and premium, long-lasting paints are recommended.
But, the options for custom surfaces go far beyond paint. One of the major advantages of molded polyurethane is the ability to create surfaces that closely simulate almost any other material, including (but not limited to) different varieties of stone, concrete, plaster, and wood. An exact silicone rubber mold is created from one relatively small piece of the natural material, which can then be reproduced in any size or quantity. For example, pecky cypress is a highly desirable material particularly in the American South. In the wild, the distinctive appearance of the wood is created by a fungus, mainly in Florida swamp areas, and using the wood in a sizeable project might require cutting down several hundred trees. But, the appearance of pecky wood can be created in a mold from a relatively small amount of actual wood, probably about half of one tree, simulated with minute accuracy, and then produced in large quantities for a much smaller cost and even smaller impact on the existing forest. The same is true of sawn wood, another distinctive wood look that can require cutting down trees and then manually scraping and distressing each piece of wood—or it can be recreated in molded polyurethane in whatever size and quantity is required.
Adhesives
High-quality adhesive is essential to the long-term durability of the component. Failure to use the right adhesive with the right procedure can be the source of completely avoidable future problems. Ideally, the millwork manufacturer will have developed proprietary formulas to work with its specific product material and installation methods, and to provide fast curing and exceptional strength in all climates (with some products, bonds can be made in temperatures ranging from -18 degrees Celsius [0 degrees Fahrenheit] to 204 degrees Celsius [400 degrees Fahrenheit]). The most advanced adhesives are environmentally safer than conventional adhesives, with low toxicity and very low odor, and are waterproof and nonflammable/noncombustible.
As with almost every building component, material, and product, installation will ultimately determine the success of even the most brilliant and carefully engineered design. The correct type and proper use of adhesives and fasteners is perhaps the single most important consideration during installation of millwork. Manufacturers should give detailed instructions and support for correct installation of their products.