Architectural Millwork: Molded vs. Fabricated
Material Basics
Millwork traditionally is made of wood, plaster, or concrete. These are still used, along with a number of synthetic materials. Each material has its own advantages, disadvantages, and possibilities.
Wood is a familiar, plentiful material used widely all over the world for thousands of years. It can range from very low in cost, as in ordinary, inexpensive trim found in any hardware store, to very high in cost for superior wood types in handcrafted applications. Wood is easily formed into desired shapes. Wood is also considered a renewable resource and can often be recycled or reused for different applications.
Wood as a millwork material does have disadvantages, including the necessity of repeated maintenance to prevent rot, decay, and insect damage. In its ordinary forms, it is combustible, and piece sizes are limited. In the past, long lengths of wood from large, old trees were available, but today most pieces are much shorter. For example, if a piece 20 inches wide were required, it would have to be laminated from smaller pieces.
Fiberglass is another material often used for millwork. It is light, not subject to rot, and can be molded into large, one-piece sections. Fiberglass is relatively difficult to work with, however, and is combustible unless fire rated at a very high cost. Detailed shapes with undercuts cannot be made with fiberglass. Fiberglass products cannot be recycled so there are disposal issues in their life cycle.
Exterior insulation finishing systems (EIFS), on the other hand, are easy to work with and low in cost. But, EIFS will absorb and wick moisture, and they do not typically have a very durable service life, nor can they be recycled at the end. The smooth finishes associated with quality millwork are very difficult to accomplish with EIFS material.
Glass fiber reinforced gypsum (GFRG) is an inorganic mixture that provides a noncombustible product. GFRG millwork can be produced with relatively simple labor and equipment, and is recyclable, although gypsum is a raw material mined from underground, which complicates its environmental impact. It is an extremely heavy material, making it costly to produce and install, and can only be used in areas where it will not be exposed to moisture.
GFRC (Glass Fiber Reinforced Concrete) can be used in wet locations. GFRC is another noncombustible inorganic mixture that can be produced with simple labor and equipment, and is recyclable. But, like GFRG, it is basically composed of a mined raw material, heavy and expensive to produce and install.
Polyvinyl Chloride (PVC) is one of the most widely used materials in current millwork as in many other common products. PVC is a synthetic plastic polymer that also contains many chemical additives and “plasticizers.” PVC does not have many of the disadvantages of other materials since it is inexpensive, available in large sheets, and can be laminated to produce even larger workable sections, and PVC products are often recyclable.
But, for millwork, PVC has its own disadvantages. It is relatively heavy in weight and cannot be made into individual pieces economically, or installed in long, seamless lengths. PVC also contains chlorine and other chemicals whose safety and environmental impact have been questioned. When machined, PVC in general becomes porous and relatively combustible. At the current time, most PVC millwork products are not considered suitable for applications requiring a Flame Spread Rating of 25 or less (Class A FSR).
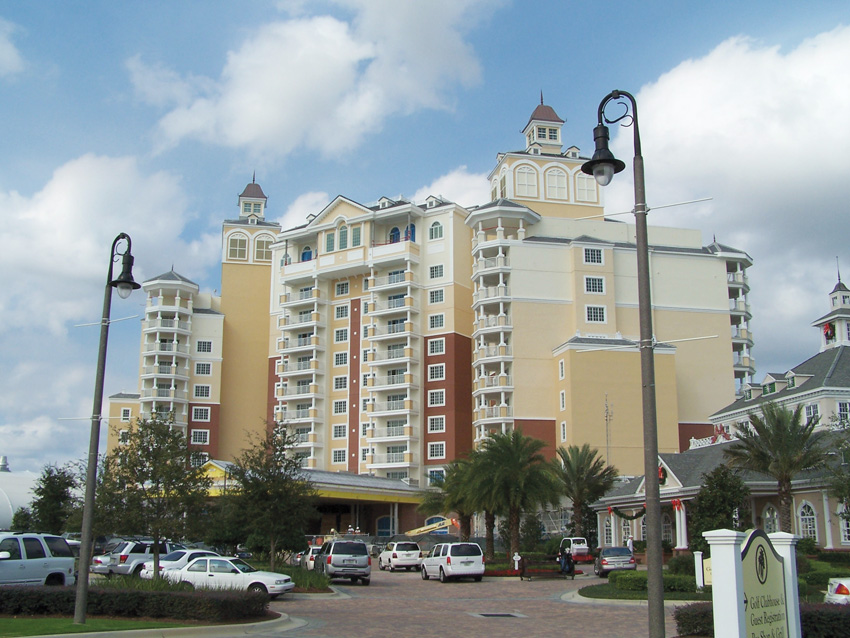
Molded high-density polyurethane is impervious to moisture, insects, and most other types of damage and decay so it is often used in large-scale exterior applications.
High-Density Polyuretheane for Millwork
High-density polyurethane solves a number of the problems with other common materials outlined above. There are many varieties of polyurethane, used in a host of common products, but high-density, chemically reacted, two-component polymer systems were invented by American chemists in the 1940s. Rigid polyurethane began to be used in commercial millwork in the 1960s. The material has a virtually limitless useful life due to its thermosetting chemical makeup.
Today, most building components are made with a higher surface density than previous polyurethanes, an average in the range of 14 to 18 pounds per cubic foot, an overall density similar to white pine. The process used to create superior-grade products provides a greater skin density than core density, which increases durability.
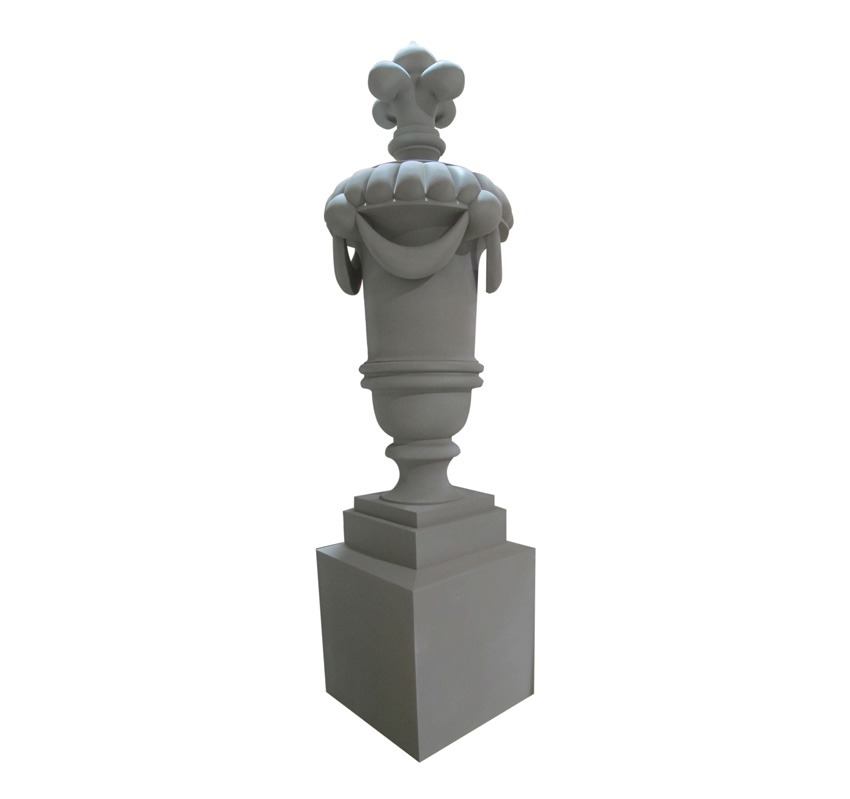
This molded polyurethane urn with a simulated terracotta finish was produced for the Jade Hotel, Greenwich Village, New York City, New York. The urn is more than 7 feet high and 2 feet wide and looks identical to natural terracotta, but weighs only about 125 pounds.
Rigid high-density polyurethane is composed almost entirely (98 to 100 percent) of closed foam. This composition not only makes the foam rigid but also hydrophobic. Millwork molded from high-density polyurethane is completely water resistant. This eliminates the possibility of rot, warping, and discoloration caused by moisture. Since it has no nutritional value for any organism, polyurethane is impervious to mold, mildew, fungus, insects, or rodents.
High-density polyurethane is light in weight and easy to transport and handle. It can be molded in a single section and installed in long, seamless lengths or made in flexible form for radius applications. Molded pieces can also be joined together to form larger components.
The material can be machined with traditional woodworking tools. Molding can reproduce minute details and any surface texture, and can be easily painted, stained, or finished. Complex shapes with extremely fine detail can be produced at low cost and in a reasonable time frame, requiring very low maintenance and much less skilled labor at most points in the process than what is needed for traditional materials like plaster, gypsum, concrete, metal, and stone.
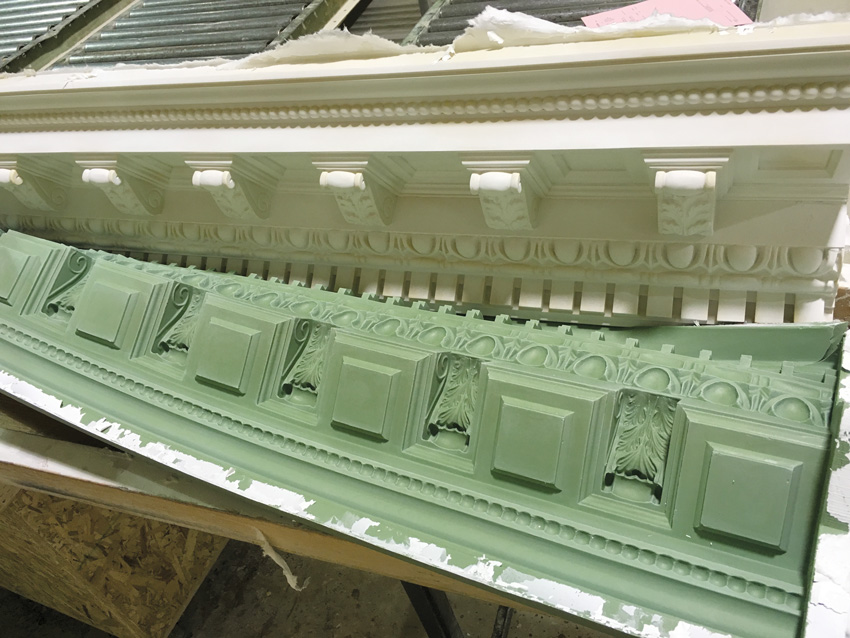
In the final steps of manufacturing, millwork can be painted, or virtually any finish or surface texture—e.g., sawn wood, stone, plaster, stucco, etc.—can be meticulously reproduced.