Active Chilled Beams Come of Age
Active Chilled Beams—A Proven Alternative
One alternative technology to an all-air system that is gaining traction is the active chilled beam, which incorporates the distribution of the ventilation air and uses room air induced across a water coil to transfer sensible thermal energy for both heating and cooling to the occupied space. When active chilled beams were first introduced in the North American market, they were limited by their capacity and their inability to meet aesthetic and architectural integration goals. Today's high-efficiency versions, however, can be seamlessly integrated in the buildings of the most demanding customers. In fact, active chilled beams have been used in Europe for over 20 years and were initially used primarily in high-performance office and educational buildings in the United States. As energy-efficient HVAC designs have become more common, many designers are using chilled beams in all types of buildings and finding that along with energy savings, occupant thermal comfort is also enhanced by better air distribution and thermal control of the occupied zone. The potential exists for chilled beams to have a significant role in both new construction and renovation of existing structures. Reed construction data indicates an increasing use of chilled beams in the U.S. market, with educational facilities and the commercial market representing the top two user groups. Healthcare facilities have just started using chilled beams as standards such as ASHRAE 170 Ventilation of Healthcare Facilities now allow chilled beams in patient rooms.
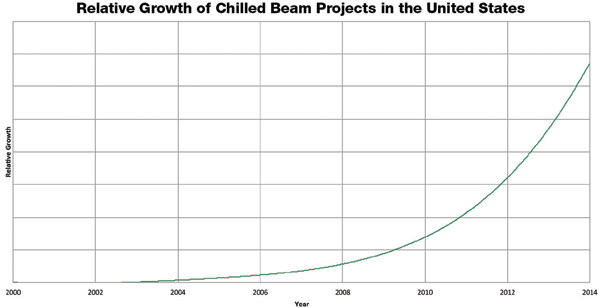
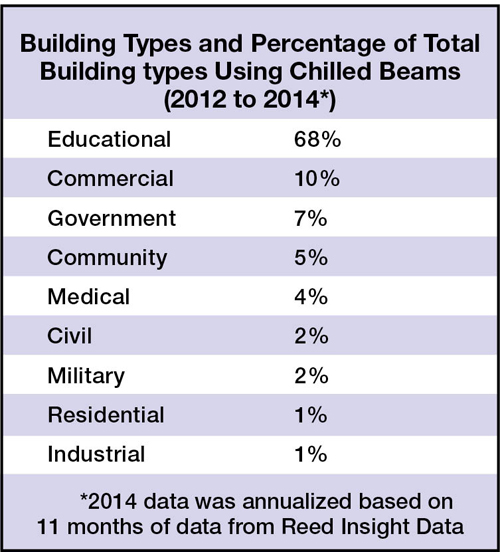
Source: Reed Construction Data and Price Industries
Benefits and Drawbacks
Active chilled beams may not be appropriate for all building/occupancy types, and their benefits and drawbacks should be evaluated in light of a particular application. Among their benefits, chilled beams have no internal moving parts and consequently little to no maintenance requirement compared to the traditional all-air VAV (variable air volume) system. They are also more efficient than their traditional VAV counterparts. A chilled beam system using a dedicated outdoor air system (DOAS) may see a reduction of 50 to 80 percent less primary air transport than that required in the traditional all-air VAV system. This lowered volume of primary air can lead to reduced floor-to-floor height as chilled beams do not need as much interstitial space for ductwork and have smaller mechanical room footprint requirements.
Due to the energy density of water compared to air, it takes about 1/10 the energy to move the same amount of thermal energy with water than air. Further, it is easier to achieve superior mixed air distribution with chilled beams—a scenario that leads to higher levels of occupant thermal comfort. In addition, when primary air is kept to a minimum, chilled beams offer quiet operation.
Despite their advantages, there is a lack of familiarity with chilled beams among MEP engineers, contractors, occupants, and building owners. The most common perceived issue is risk of condensation. However, this is not a concern if the mechanical system is designed to manage the dehumidification load and the building envelope has good control of moisture infiltration. Space is an important consideration. Chilled beams may occupy a higher percentage of ceiling area than traditional VAV, and space humidity sensors and condensate sensors are required for the best occupied space humidity control and least risk of condensation. In some instances, chilled beams are not appropriate, notably high-humidity (high latent load) spaces such as kitchens, and spaces that experience high air volume change such as laboratories with fume hoods.
What are Chilled Beams and How Do They Work?
Chilled beams are of two basic constructions: passive and active. Passive beams are cooling-only devices that use gravity-driven natural convective cooling to condition the occupied spaces. Passive beams are typically installed along perimeters of buildings to try to intercept and condition most of the cooling load from the building shell before it reaches the occupied areas of the building.
Active beams are an induction device, where supply air is used to draw room air through a water coil. The air and water both provide cooling or heating depending upon the season. The water coils provide sensible cooling and the supply air handles the fresh air requirements and controls the occupied space humidity levels. The more optimally configured active chilled beam systems use only the ventilation minimum air volume, that is, fresh air, as the supply air; the rest of the sensible heating/cooling is provided by the water coil.
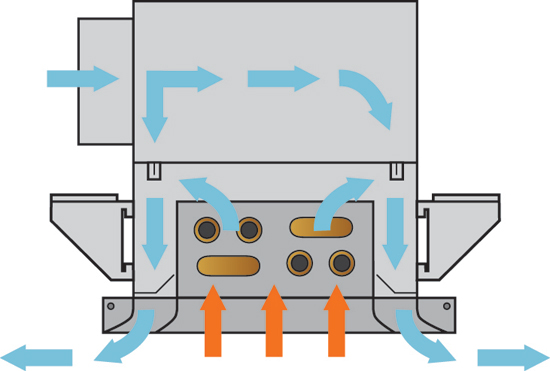
Image courtesy of Price Industries
Air Flow Pattern in an Active Beam
Condensation and Control
As most designers and end users have concerns about the potential for condensation, it is common for the designer to explore using a condensate pan as a safety feature even if the active chilled beam system is designed to not condense. Condensation is the heat transfer process by which water vapor is converted into liquid water, while condensate is the water that collects on the cold surface. The potential for condensate to form on a surface is determined by the difference of the surface temperature relative to the dew point of the air, which is the temperature at which water vapor in the air will become liquid water.
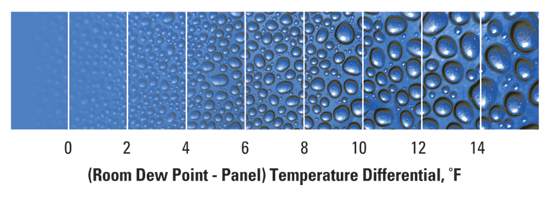
Source: Mumma, 20021
Condensate on panel with temperature differential
Surfaces with temperatures below the air dew point will form condensate. The rate at which the condensate forms is a function of how cool the surface is in relation to the dew point of the surrounding air, as well as the length of time the air is in contact with the cool surface. Since the space relative humidity is typically 50 percent or less, the risk of condensation can be mitigated by keeping the supply water temperature above the design room dew point. This dew point temperature of room air at 75°F and 50 percent relative humidity is ~55°F; therefore chilled surfaces above this temperature should not cause condensation. Engineers typically use a safety factor on this value to account for humidity and supply water temperature fluctuations; therefore supply water temperatures of 58°F are common. Interestingly, when room air is blown across a cold surface, the formation of condensate occurs at lower temperatures than the dew point because the air is moving and the air needs a longer duration of contact that the length of water coil fins used in active chilled beams. Since the cooling coils on a chilled beam are only two rows deep, the coil temperature may be significantly below dew point before water droplets form and fall from the coil fins.
When condensate forms, it is too late to prevent the surface from becoming wet. The question, however, is how to prevent condensate from becoming a design flaw in the building.
The HVAC designer needs to verify that the ventilation system is capable of handling the latent load. Humidity loads that must be addressed include:
• Ventilation load. Generally the largest moisture load, particularly in a humid climate.
• Infiltration load. Moisture that crosses the building shell through windows, cracks, and other penetrations. Non-operable windows and pressurization of the building can minimize this moisture source.
• Occupant load. As people breathe and perspire, moisture is released into the space.
• Other loads. Fountains, doors, and windows left open, wet clothing, etc.
It is important to note that around the world, many active chilled beams installed in humid areas do not have drain pans, nor do they need them. That said, most building codes have historically required drain/condensate pans for cooling coils. Recently, the chilled beam section at the Air-Conditioning, Heating and Refrigeration Institute (AHRI) filed an interpretation request with the International Code Council (ICC) concerning the requirement in the International Mechanical Code (IMC) that cooling coils must have a drain pan. In response, the ICC added an exception to the 2015 International Mechanical Code removing the condensate drain system requirement for cooling coils designed to operate in sensible cooling mode only and when a design strategy is used to prevent condensate formation on the sensible cooling coils.