Cover Boards for Low-Slope Roofing Systems
Factors Impacting the Long-term Performance of a Commercial Roof System
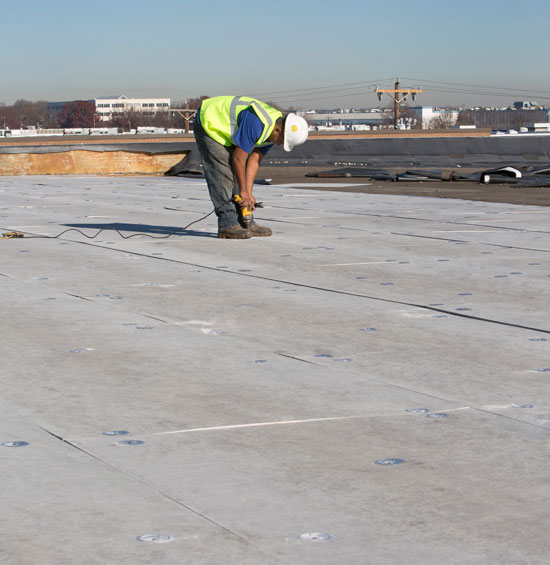
Photo courtesy of National Gypsum®
A worker is screwing the fasteners through the cover board and the insulation into the deck below the assembly.
Many outside influences affect the performance of the roofing system, and thus the durability of the building. Simulated outside forces are tested on various roofing assemblies, which are then awarded ratings to assure the specifier that the project will live up to expectations.
Here are the factors that can affect the roofing assembly and the tests and ratings that determine an assembly’s efficacy:
Fire — The fire rating for any particular low-slope roofing system is determined by the testing of the total roof assembly. There are no individual “parts” of the assembly that determine the fire rating. That means that the use of certain materials (gypsum-based cover board, cementitous-based cover board and/or thermal barrier, for instance) can positively affect the outcome of the test results.iii
The two widely accepted fire-testing agencies in the United States are Factory Mutual (FM), and Underwriters Laboratories (UL).
FM rates for combustibility from above the roof deck in these classifications: Class A, Class B and Class C. And it tests combustibility from below the roof deck with the Class 1 classification.
It’s important to understand that a Class A roof is not the same as a Class 1 roof. The achievement of a Class A roof rating is the result of one test — the external spread of flame test.
However, a Class 1 roof has been tested for a series of events, including the external spread of flame, the flame spread on the underside of the roof deck, plus wind, hail, corrosion and leakage. The test standard to achieve a Class 1 rating is much more comprehensive than the standard used to gain a Class A rating. Another way to put it is that all Class 1 roof assemblies are Class A roofs, but not all Class A roof systems meet Class 1 standards.
UL tests fire resistance according to UL 790, and rates roofs according to these standards:
- Class A roof coverings are effective against severe fire test exposures.
- Class B roof coverings are effective against moderate fire test exposures.
- Class C roof coverings are effective against light fire test exposures.
The three types of tests that UL performs to determine the fire ratings are:
- Burning Brand Test — for combustible decks only.
- Spread of Flame Test — for all combustible and noncombustible decks.
- Intermittent Flame Test — for combustible decks only
Some roof cover boards improve the fire rating of the system, while others contribute no improvement at all. We’ll discuss more fully which boards offer this added measure of protection later in the course.
Moisture/mold — The primary reason for a low-slope roof system to be installed on a building is to keep moisture out of the building. This is an on-going battle that will be waged for the 10- to 20-year life of most roofing systems.
There are any number of ways for water to get into the roof system, and then most likely into the building. The three most common ways are:
- During the installation of the roof system
- Through leaks in the roof system after it’s been installed
- By the condensation of moisture already in the building because of its use (including paper mills, buildings with indoor pools in them, food processing plants, etc.)
Mold requires a number of factors to occur in order for it to grow: heat, moisture, food, and mold spores.
Inorganic materials that are not paper-faced reduce the availability of “food” that mold spores require to grow. Fiberglass-faced or cementitious non-paper faced products reduce the availability of food that mold spores require to grow.
Note that no material can be considered “mold proof,” nor is it certain that any material will resist mold or mildew indefinitely. When used in conjunction with good design, handling and construction practices, products designed to be mold-resistant can provide increased mold resistance versus standard wallboard products. As with any building material, avoiding water exposure during handling, storage and installation, and after installation is complete, is the best way to avoid the formation of mold or mildew.
Below is a list of the roof cover boards that are manufactured to resist mold:
Glass-Mat Gypsum Board
Asphaltic Board
Extruded Polystyrene (Fanfold)
Cementitous Board
Hail and impact resistance — Including a high compressive strength cover board in the roof system design as a separation layer between the insulation and the membrane will disperse an impact load over a wider area and help protect both the membrane and underlying insulation from premature failure.
The high amount of repetitive traffic that occurs across the surface of the roof system during its installation can negatively affect the insulation below the membrane.
Wheelbarrows, power carts, and a continual stream of roofers walking and dragging materials across the rooftop can damage the roof system before the installation is even complete (crushing, facer delamination, etc.). This potential damage may or may not be noticeable during the roof system manufacturer’s warranty inspection.
Cover boards can also help prevent punctures of the roof membrane from occurring after the roof system has been installed. This can occur due to service technicians dropping tools while working on the rooftop equipment, or wind blown objects such as tree limbs falling on the roof.
Sound intrusion — While its true that excessive sound levels do not affect the long-term performance of the roof, they can definitely have a negative impact the quality of life that occurs inside of the building. This is particularly true for buildings in the immediate vicinity of airports, or located within their regular flight paths.
The inclusion of a cover board between the top layer of insulation and the roof membrane can mitigate this noise problem. And by using a layer of gypsum board on the roof deck as well, designers can create a sandwich effect that will noticeably decrease the amount of sound transmitted to the interior of the building through the roof.
Wind uplift and fastening patterns — Resistance to wind uplift is increased by the addition of certain cover boards, while other cover boards offer little or no improvement.
The main factors taken into account for wind uplift ratings are:
- Building Location
- Height of Building
- Wind Velocity
- Ground Surface/Topography
FM Global checks the roof edge requirements on all of their buildings. FM 1-90 is a standard wind rating used in the roofing industry. FM 4470 is the approval standard for single-ply, polymer-modified bitumen sheet, built-up roof (BUR) and liquid applied roof assemblies for use in Class 1 and noncombustible roof deck construction. FM 4450 is the approval standard for Class 1 insulated steel deck roofs.
UL 580 is the test standard for uplift resistance of roof assemblies. According to UL, “This test method subjects a 10 ft. x 10 ft. test sample to various static and oscillating air pressure to index performance under uplift loads imposed on roof decks.”