Mitigating Water Leaks around Windows in Wood Framed Walls
Advances in Flashing Solutions
In the spirit of the WBDG and in the interest of mitigating the potential for construction defects, the best flashing solutions need to be looked at holistically in terms of the particular wall construction and the specific windows being used in a project. For purposes of our discussion here, let’s focus on common wood-framed construction as used in single-family and multifamily low-rise residential construction. In this construction type, wood studs are spaced evenly and strengthened with exterior sheathing on the outside and gypsum board applied to the inside. Window openings are framed based on the rough opening dimensions for premanufactured windows and the corresponding openings in the exterior sheathing are cut, thus defining the basic location and conditions for window installations. The actual window units should be specified to prevent leaks through any part of their frame or sash by using sound, proven technologies. These might include mitered corners stiffened by spline inserts, molded corner gaskets, vulcanized perimeter gaskets, and shop-applied perimeter collars as opposed to field-applied sealants. Assuming the window units are good quality and can be expected to perform within an appropriate standard of care, then attention can now turn to the details of continuity of barriers.
Weather and Air Barriers
Before the windows are installed, the requisite barriers need to be accounted for. In northern climates, vapor retarders may be required per the IBC and are typically part of the interior work, which comes later. But since the IBC also requires the weather-resistant barrier on the exterior, such a barrier needs to be installed and coordinated with the window openings. The code identifies two options for a weather-resistant barrier, first indicating: “A minimum of one layer of No. 15 asphalt felt, complying with ASTM D 226 for Type 1 felt” (IBC 1404.2). Asphalt felt has certainly been a traditional material for many wall assemblies; however, it is seen as a rather obsolete material compared to other modern alternatives. Fortunately, the second IBC option is to allow “other approved materials,” which refers to “materials that are acceptable to the building official or authority having jurisdiction” rather than a long list of specific alternatives. Such other approved materials currently include a variety of forms. Some are self-adhered sheet membranes (sometimes called “peel-and-stick” materials) that have commonly been used in roofing applications and were also popular on below-grade walls. There are also spray-on systems that are formulated to be applied in thin or thick applications depending on the product and its makeup. Additionally, there are other types of rolls or sheet goods that have their own requirements for installation. Note that there are a variety of manufacturers and products such that performance can vary considerably based not only on the product but also on the quality control of installing them in the field. Seams and joints are particularly important in this regard and can be a significant source of problems later on if not treated correctly.
An air-infiltration barrier is also required as part of most energy codes along the plane of the exterior sheathing. It is important to realize that not all weather- or water-resistant barriers also qualify as an air barrier and vice versa. It is also notable that in a wood-framed wall with a multitude of individual materials and components, air infiltration can be difficult to control. The key to success lies first in the ability of a particular material to be considered a true air barrier. The codes rely on ASTM E2178: Standard Test Method for Air Permeance of Building Materials as the basis for determination. Hence, any individual material or combination of materials that can demonstrate compliance with this test showing a very limited air permeance can qualify as an air-barrier material. The second key to effectiveness of an air barrier is to look beyond the specific material and to its ability to be truly continuous. That means any joints, seams, penetrations, or other breaches of the barrier need to be addressed in some manner as part of a total system. The codes then look to other specific tests; in this case, namely ASTM E2357: Standard Test Method for Determining Air Leakage of Air Barrier Assemblies and ASTM E1677: Standard Specification for Air Barrier (AB) Material or System for Low-Rise Framed Building Walls.
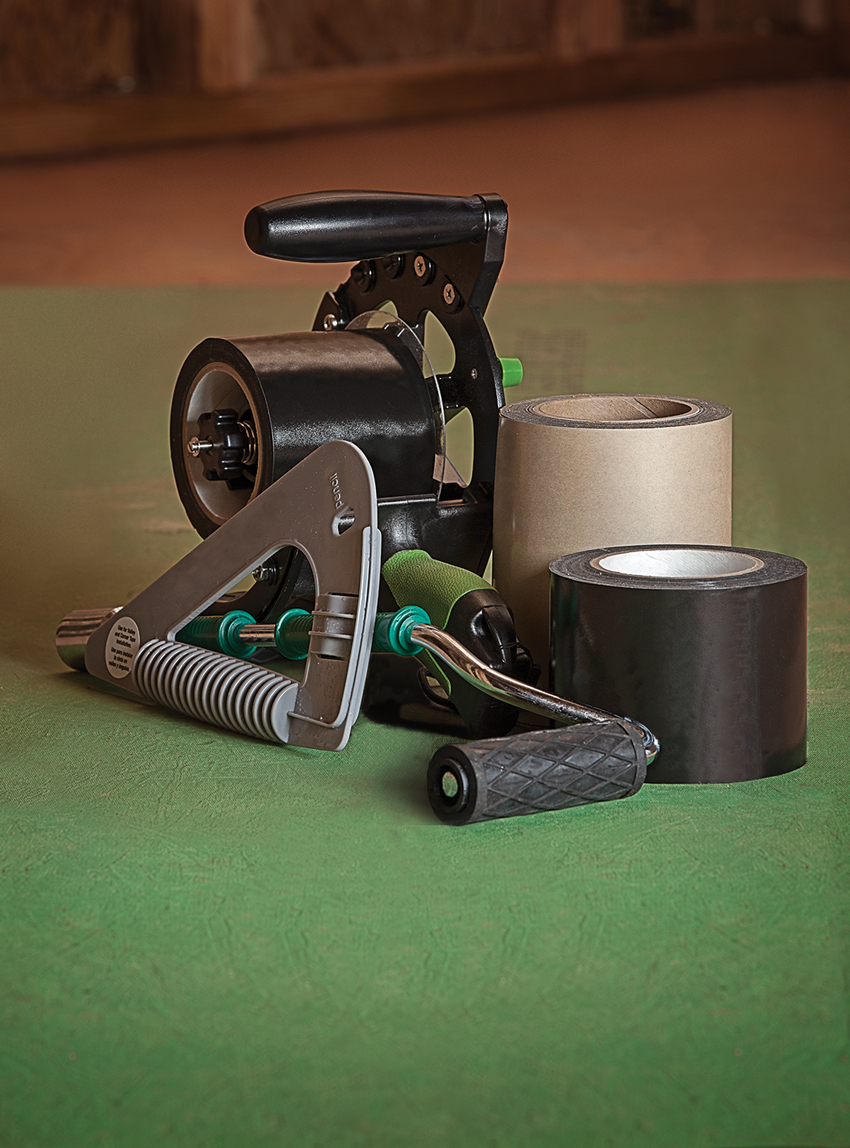
A complete roll-tape system includes everything needed to seal any gaps or seams both in water and air barriers and for flashing installations.
The difference between the testing just for a product (compliance at 4 thousandths of a cubic feet per minute) and the testing for a complete assembly (compliance at 4 hundredths of a cubic foot per minute) might seem to be a big difference, but the net number is still very small. This current code-required level of air infiltration is dramatically less than found in typical wood-framed construction in the past. Its significance lies in the fact that all of the joints, seams, connections, etc. need to be included in the test to be sure that the total assembly does indeed perform as a complete, unbreached air barrier. Commonly, house wrap materials have been popularly used because as a material, they rate very well as an air barrier. Their weakness has been in securing them around penetrations, window openings, and to the sheathing, as well as the sometimes inefficient ability to seal the joints and seams, which can often be seen flapping in the wind prior to the installation of cladding. That has given rise to other systems, such as peel-and-stick or spray-on membranes, which address air infiltration in the full wall assembly and may also carry weather/water-resistant qualities.
Integrated Systems
In designing a wood-framed wall assembly, it is important to be aware of the availability of high-performance, engineered wood sheathings that offer an integrated product approach. Such products provide structural sheathing, a weather-resistant surface, and a qualified air barrier all manufactured into one finished product. This multifunctional approach eliminates the need to identify and install separate products, thus saving steps during installation and lowering labor costs. It also reduces the burden on skilled labor in the field by performing the critical system work under controlled conditions at the factory. Such products address joints and seams by providing advanced adhesive tape systems that have been independently tested and proven to meet the requirements of both a full weather-resistant covering and an air-barrier assembly.2 Part of the beauty of the tape is that it avoids the need for penetrating fasteners, offering a truly continuous seal without fear of compromise from mechanical fasteners.
When it comes to providing flashing that integrates with the air and weather barriers on the sheathing plus addresses all of the needed conditions around windows, there are also some advanced, high-performance products that should be considered.
- Self-adhering, roll-tape flashing products: Traditionally, butyl or asphalt tape has been used successfully in building enclosures, not only for seam covering but for flashing. These have most commonly been used in roofing applications and roof/wall junctures, particularly where other asphalt-based products have been employed. Currently, there are also advanced tapes that are made from an advanced composite acrylic that provides superior adhesion, resistance to ultraviolet (UV) light exposure, and aggressive bonding. Some of these tapes are especially formulated for use with high-performance, multifunction sheathing to assure that they work continuously with the integrated weather and air barriers. One acrylic tape is manufactured to stretch in all directions so that only a single piece is need to flash complex corners and curves that are particularly vulnerable to water leak paths. In this way, the tape flashing can be used to cover the exposed framing and face of the sheathing on heads, jambs, and sills to create a continuous protective layer that seals out water and air around window openings. Such flashing roll tape is available in wider widths than other building tapes to provide the appropriate coverage in a single installation over the full depth and perimeter of window openings, particularly deep window assemblies common in multifamily construction. The fully flashed opening is then ready to receive a window unit, which may then be further counter flashed over or around integral flanges using similar acrylic straight flashing tape. In either case, the tape is pressure rolled into place using hand-held rollers to assure a complete and uniform bonding. This avoids the need for fasteners and does not require any unusual or specialized construction skills to execute.
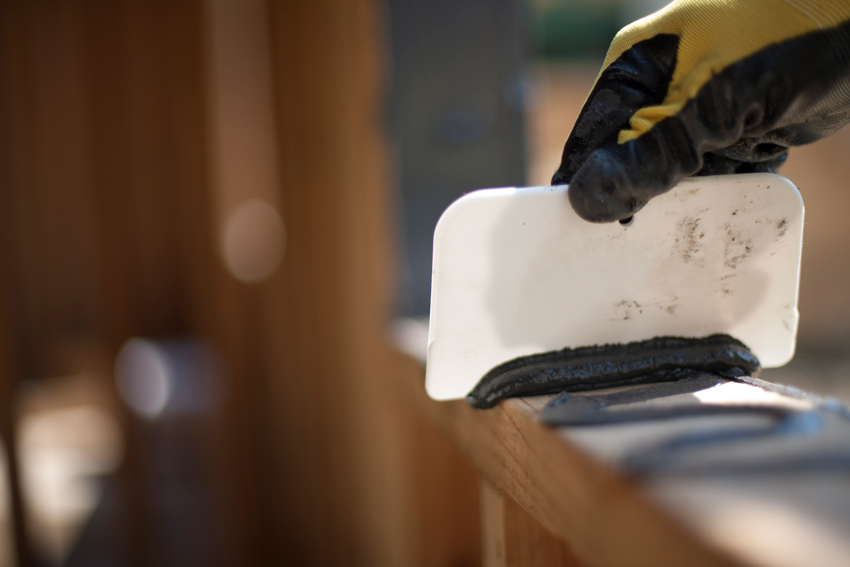
Liquid-applied flashing can be used to seal surfaces completely even in wet or cold conditions.
- Liquid flashing products: Much like other liquid waterproofing products, liquid flashing can be applied for a continuous, seamless condition around windows and other openings. It is common for products like these to be hand applied onto a surface, such as sheathing, framing, metals, etc. Once applied, it is intended to dry to a complete water- and air-proof seal around all portions of a window opening. Since it is usually the thickness of the application that is important to quality control, applicators likely need to be trained in the installation of these flashing products, and on-site quality control becomes very important. Nonetheless, such liquid products are particularly suitable for upper stories in multifamily buildings subject to higher wind ratings.
Part of the effectiveness of liquid flashing is that it can be applied with optimal viscosity to flow easily into irregular shapes and surfaces, such as recessed windows, corners, roof valleys around chimneys, and pipe penetrations. Typically, such flashing can be weather resistant and tack free in as little as 20–40 minutes. Even better, a liquid flashing membrane like this can bond and cure in otherwise unfriendly site conditions, including wet weather and damp substrates. At least one is backed by a 180-day exposure guarantee, meaning that if it remains uncovered for up to six months, it will still perform. In the end, it is usually the architect’s preference whether to use liquid-applied flashings or other systems, but the versatility and durability of these products cannot be ignored, particularly for long-term solutions on larger and taller buildings.
There are a few final considerations when looking at flashing system choices. Ideally, having the ability to use the same flashing system for window openings as for other parts of a wood-framed building, such as wall-to-roof junctions, keeps construction processes simpler by using the same trades and products across a project. This simplicity can make it easier to have effective warranties, too. Choosing to specify an integrated system that provides water and air barriers as well as coordinated flashings can mean that all of these products come from a single manufacturer with a single warranty. That can eliminate any potential arguments over who is responsible if multiple products are used from multiple manufacturers when a problem or defect emerges.