Building and Energy Code Updates
ASHRAE 90.1
The American Society of Heating, Refrigeration, and Air-Conditioning Engineers (ASHRAE) has long been involved in optimizing the engineering of energy-using equipment in buildings. It has also recognized the significance that the building envelope has on the amount of energy needed to operate that equipment, both in terms of capacity and in the amount of time it needs to run. As such, ASHRAE has committees and work groups made up of members and associates to generate some recognized standards for building design. ASHRAE 90.1: Energy Standard for Buildings Except Low-Rise Residential Buildings is meant to apply to most commercial, industrial, and institutional buildings. The ICC has recognized this standard as “equivalent” to, albeit not identical to, the requirements of the IECC. Hence, it is a recognized alternative to use when showing code compliance for nonresidential buildings. While there are indeed differences between ASHRAE 90.1 and the IECC, a building designed to meet the minimum standard of either one should yield approximately the same overall energy performance.
California Title 24
In the state of California, the codes are referred to as the California Building Standards Code, which is embodied in the California Code of Regulations, Title 24. It is commonly referred to simply as Title 24 and includes 1) some adopted I-Codes as written; 2) some I-Codes with adaptations to suit California; and 3) some California-generated standards to suit particular state concerns. As such, the Title 24 codes are generally more stringent, particularly in regards to energy performance and seismic issues, than the model I-Codes alone. This means that the “code minimum” threshold for energy performance can be expected to be higher in California than elsewhere in comparable climate zones. It has also been observed that other states, particularly those in the Pacific Northwest, have begun to follow California’s lead and are starting to incorporate their own state adaptations to the model codes.
International Green Construction Code
The ICC has collaborated with a number of non-profit organizations to create a model green building code. Referred to as the International Green Construction Code (IgCC), it addresses more than just energy, including other common aspects of a green building such as site design, water usage, material selections, and indoor environmental quality. This code has primarily been adopted by localities, as opposed to statewide adoptions, and provides multiple options for achieving minimum performance levels. It works in a very similar manner to the voluntary programs (such as LEED) but codifies it so that code enforcement officials have a tool to work with similar to other codes.
Based on all of these developments, it is clear that the future direction of energy code updates and the purview of authorities having jurisdiction is to continue to seek better energy performance in buildings and reduce the emissions caused by the use of fossil fuels in the heating, cooling, and operation of buildings or generation of electricity.
Building Envelope Update
The latest published version of the IBC and IRC is 2018, which was finalized at the end of 2017. The code development process for the 2021 versions is now complete, with publication expected by January of 2021. By way of example, we can look at one significant exterior wall update to demonstrate how the codes have been revised to suit current needs and conditions.
Water-Resistive Barriers
Both the IBC and the IRC have required that exterior building walls are protected from the elements to prevent potentially damaging water penetration into the rest of the wall assembly. Commonly, particularly on stud-framed walls, this includes a cladding material (i.e., siding, metal, masonry, stucco, etc.) as the outermost first layer of defense. This is the visible material on the outside of wall assemblies and is usually chosen for a combination of design, performance, and cost reasons. Underneath, however, and usually not visible, is where the second code-required layer resides. In prior versions of the code, it was referred to as simply a “weather-resistant barrier” (WRB) with limited expectations. More recent versions of the code (i.e., 2012 and later) require a “water-resistive barrier” (WRB) defined as “a material behind an exterior wall covering that is intended to resist liquid water that has penetrated behind the exterior covering from further intruding into the exterior wall assembly.” This clearly identifies a higher expectation that it will keep water from passing into the full wall assembly.
This requirement for a WRB has been in the code for quite some time. In fact, the only stated material for a WRB is “not fewer than one layer of No. 15 asphalt felt, complying with ASTM D226 for Type 1 felt or other approved materials,” (IBC 1403.2). In this case, “approved” is a defined term in the code meaning “acceptable to the building official.” In response, most modern material manufacturers of WRBs will have their products independently tested and rated to demonstrate that they perform at least as well as, if not better than, Type 1 asphalt felt to allow them to be approved by the building official, not to mention the architect of record. Note that the minimum requirements for acceptance are specific and outlined in Acceptance Criteria for a WRB published by the ICC Evaluation Service (ICC-ES), a subsidiary of the ICC.
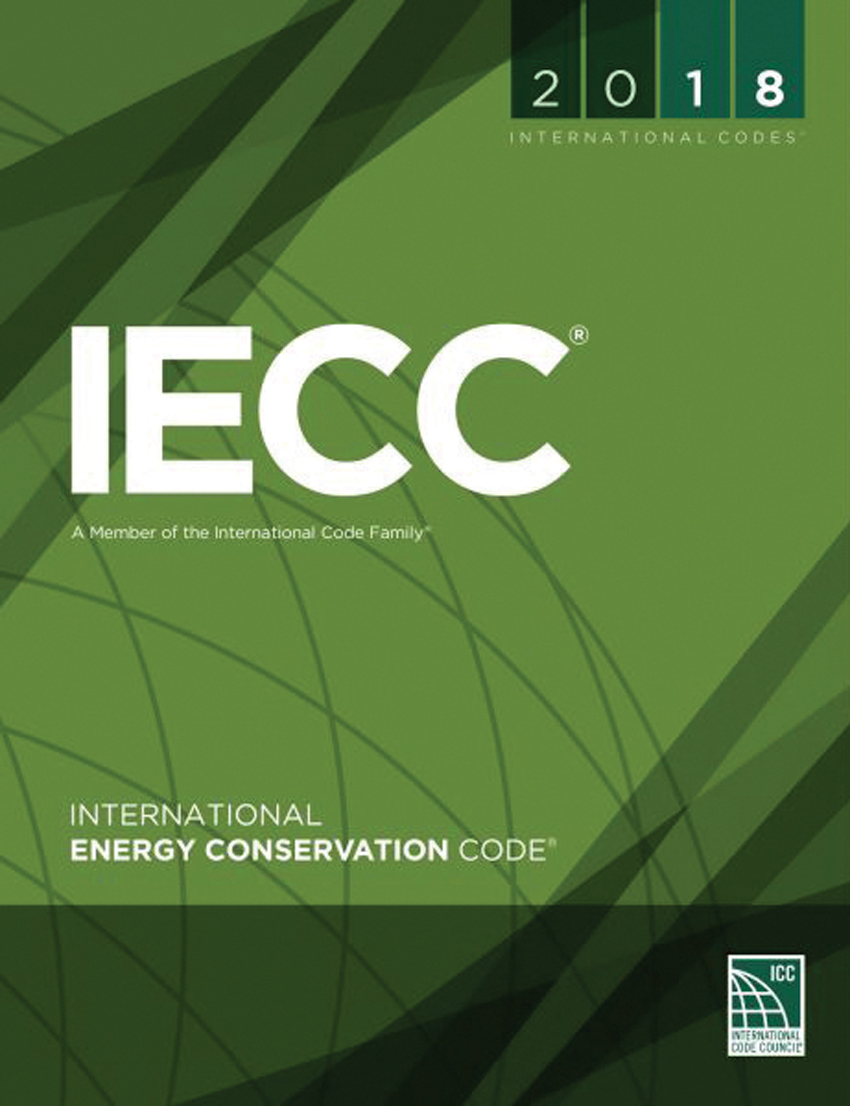
Source: International Code Council
The 2018 International Energy Conservation Code (IECC) reflects the latest "code minimum" standards for energy performance in buildings.
Water Drainage
In addition to the requirement for a WRB, the IBC and IRC require “…a means for draining water that enters the assembly to the exterior,” (IBC1402.2). This is most commonly achieved through the use of a WRB designed for enhanced drainage or by detailing a full rainscreen system behind the cladding. In the fullest form of this requirement, wall systems with enhanced drainage have become common. In this assembly, the cladding is expected to allow some air and water to penetrate into a space between it and the WRB where it can then safely and harmlessly drain away. This type of approach has been common in brick veneer wall construction, which relies on such a gap and weep holes at the base to create the drainable surface and water discharge. However, on other wall systems, particularly lighter-weight framed walls with siding or stucco, creating that drainage gap has also become a more common practice for enhanced water management and drying capacity of wall systems. In fact, some siding manufacturers are starting to require it.
Air Barriers
Beyond a WRB, the energy code (IECC) requires an air barrier (AB) in exterior walls. That barrier can be located in the assembly either on the exterior or the interior but needs to be continuous across all junctions, penetrations, and openings. In some cases, manufacturers may provide detailing for a product that performs as an AB or WRB alone or a combined WRB and AB system. This means that whatever product is used, sealing the edges and any seams properly and fully without undue penetrations is critical for good performance and code compliance. Some manufacturers offer full sealing systems that use a compatible adhesive, sealant, or tape. This allows the edges to be held permanently in place, usually by using a hard roller or hand applicator to press the barrier and the tape together. With enhanced detailing, this combined approach can be a cost-effective way to achieve both the moisture- and air-infiltration performance requirements for a project.
2021 Code Update
Not all wall conditions are the same when it comes to assemblies using cladding, WRBs, and ABs. In particular, reservoir cladding systems like gypsum or cement-based stucco have suffered from entrapped moisture and reduced drying capability. Notable field issues and problems have come about as a result, which have prompted a number of proposed changes to code requirements to overcome them. Specifically, the 2021 version of the ICC codes will incorporate changes for residential, multifamily, and commercial buildings that address these concerns. These changes are specifically found in the new IRC and IBC sections of the code. In particular, Section 2510 of the IBC addresses Lathing and Furring for Cement Plaster (Stucco). For residential applications, the same language may be found in the corresponding section of the IRC.
There is a major change in the language in Section 2510 to reflect differing climate conditions across the United States. Specifically, paragraph 2510.6 has been rewritten and broken into subparagraphs to address different conditions related to dry climates and moist or marine climates. The significance of this change is the recognition that some of the problems that have been caused by moisture and condensation in stucco-covered walls are directly influenced by a local climate. Similarly, it recognizes that there is the need to allow for any trapped moisture in the wall to properly escape and drain, which was not adequately addressed before. Some of the affected sections and language are highlighted as follows:
“2510.6 Water-resistive barriers. Water-resistive barriers shall be installed as required in Section 1403.2 and, where applied over wood-based sheathing, shall comply with Section 2510.6.1 or Section 2510.6.2.”
This paragraph is a shortened version of the prior 2510.6 but still refers to the requirement for the WRB (1403.2), which we discussed earlier. It then recognizes two different climate conditions that will determine code compliance when wood-based wall sheathing is used: “2510.6.1 Dry climates. One of the following shall apply for dry (B) climate zones:
- The water-resistive barrier shall be two layers of 10-minute Grade D paper or have a water resistance equal to or greater than two layers of water-resistive barrier complying with ASTM E2556, Type I. The individual layers shall be installed independently such that each layer provides a separate continuous plane and any flashing, installed in accordance with Section 1404.4 and intended to drain to the water-resistive barrier, is directed between the layers.
- The water-resistive barrier shall be 60-minute Grade D paper or have a water resistance equal to or greater than one layer of water-resistive barrier complying with ASTM E2556, Type II. The water-resistive barrier shall be separated from the stucco by a layer of foam plastic insulating sheathing or other non-water absorbing layer.”
Notice
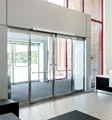
www.crlaurence.com
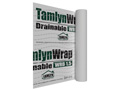
www.tamlyn.com