Blending Aesthetics and Sustainable Design Through Facades
The building envelope is the first line of defense when it comes to keeping outside air out and inside air in. Whether designing and constructing a new building or renovating/retrofitting an old building, it’s important to understand the entire building envelope system as having a direct impact on energy use and indoor air quality (IAQ). According to a 2015 report from the U.S. Department of Energy, “about 50% of the heating load in residential buildings and 60% in commercial buildings results from flows through walls, foundations, and the roof.” Energy created within the home that flows to the exterior is just one of the problems caused by a poorly sealed building envelope. Unwanted intrusions from outside the building also can penetrate the envelope, flowing inside and harming the building’s structure and its occupants.
Over the past several decades, huge technological advancements have been made to materials, products, and construction best practices. The adoption of new technology and high quality products is becoming increasingly important as the effects of climate change are leading to increased instances of extreme weather that can directly impact the building envelope. Dramatic temperature swings as well as increased flooding in some areas – while others experience extreme drought – can leave an area susceptible to wildfires, and unprepared buildings are more vulnerable to costly damage. Areas that typically have precipitation are suffering from larger and more intense storms such as hurricanes that can produce dozens of inches of rain in a single storm, or blizzards that drop large amounts of snow.
All of these conditions strain buildings and threaten to damage the building envelope, allowing unwanted air and water to penetrate building materials. As flood waters recede or blizzard snows melt, the buildup of water can flow into spaces around exterior flashings or expansion joints. If not prevented or quickly remedied, unwanted moisture intrusion can cause catastrophic physical damage that is not only expensive to fix but also can be harmful to building occupants. Mold and mildew can easily grow in water-damaged spaces, leading to poor air quality and causing physical harm to occupants.
By keeping outside air and moisture outside, the building envelope assists other systems. For example, the HVAC system works more efficiently to keep occupants comfortable with consistent temperatures and safe with improved air quality.
Many natural and man-made materials can help seal the exterior facade by providing natural water and moisture resistance.
Sintered stone has a porosity of less than 0.09 percent, so it doesn’t easily absorb water. By keeping water out of the surface material, the building is less likely to be affected by water penetrations and subsequent staining, mold, or mildew on the exterior facade. Sintered stone is also resistant to thermal shock, making it suitable for any climate.
Ultracompact surface materials are shown to be impervious with an average water absorption rate of 0.03 percent. They also have an average moisture expansion of 0.02 percent and an average abrasive wear index of 182.2.
Natural stone can be manufactured in large panels that contain faux joints to achieve the look of brick or terrracotta; a single panel may appear to have more than a dozen bricks. Fewer seams and fewer spaces between panels leaves fewer ways for water to penetrate the building envelope.
Thin brick fastened using the “keyback” method is less likely to separate or pull out from the main structure, reducing the risk of wall damage that can lead to air and/or moisture intrusion. Thin brick also is lighter and creates fewer seismic concerns as it requires less structural support while providing a genuine brick appearance. Thin brick is significantly less expensive than classic full brick because it is much thinner and therefore uses less material.
Low-e glass coatings help prevent the amount of heat transfer on either side of the glass. They help keep hot air outdoors in summer but warm air from the HVAC system indoors in winter. With low-e coatings preventing heat transfer, an HVAC system doesn’t have to work as hard to maintain temperatures for occupants, and energy costs are reduced. Occupants also experience the added benefit of comfortable temperatures without needing to use curtains, blinds, or other means to block light from the outside to keep unwanted heat or glare from entering a space.
Expansion joint systems help seal gaps between panels and spaces in the building envelope. These joint systems are vital in preventing air and moisture intrusion from entering the building.
Allowing the building envelope and the HVAC system to work together rather than in opposition of one another not only saves the occupant energy costs, it also promotes the health, safety, and welfare of occupants by preventing them from exposure to toxic mold, mildew, or other harmful materials in the wall structure.
DESIGN AND AESTHETICS
When specifying materials and products for facades, it is also important to consider how the material will be manufactured, shipped, and installed. For large scale commercial projects, large panels can provide options for unique, visually stunning facades. Panels can be cut into custom shapes and offer infinite options as to how they are displayed. Large panels can even include designs that give the illusion that the panel is made up of many smaller pieces of different shapes and sizes. However, the major benefit to having large sheets and panels is that there are fewer seams or areas where water and moisture can seep into the building.
Sintered stone is a lightweight product that can be cut to almost any requirement, making it cost-effective to ship and easy to fabricate and install. The material can be affixed to a building’s structure by using one of the following systems:
Hidden Fixing with Longitudinal Adhesion (HC): Comprised of a hidden support system that uses a longitudinal elastic chemical adhesive with a vertical support featuring T- or L-profiles.
Visible Mechanical Fastening Fixation (VM): Comprised of a self-supporting metal structure for ventilated facades designed to support ceramic tiling in different formats and thicknesses.
Strongfix: A longitudinal mixed (chemical and mechanical) hidden profile system.
Notice
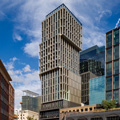
www.alucobondusa.com/
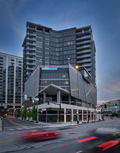
www.pro.cosentino.com
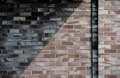
www.endicott.com
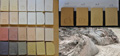
www.hofmann-facades.com
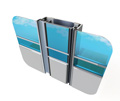
www.inpro.com
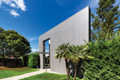
www.neolith.com
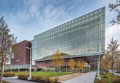
www.vitroglazings.com