This CE Center article is no longer eligible for receiving credits.
Nearly a century ago, aluminum revolutionized the world of metals. Since then, coil anodizing technology has allowed remarkable architectural possibilities of designs, textures, and finishes that are functional, versatile, and environmentally responsible. Anodized aluminum can be roll-formed, stamped, laser engraved, laminated, perforated, welded, embossed, and silk-screened. Moreover, recent breakthroughs in coloring techniques provide a range of colors rivaling those of paint. Among the many applications of anodized aluminum are architectural exteriors, interiors, paneling, roofing, windows, doors, ceilings, and lighting.
What is Anodizing?
Anodizing is an electrochemical conversion process, not an applied coating. The procedure of anodizing aluminum is a very technical and artistic process involving an electrically charged solution that works with the natural components of the aluminum substrate. The surface of the aluminum metal is converted to aluminum oxide as a result of reactions occurring at the anode in an acid solution. The process is called “anodizing” because the sheet or part to be treated forms the anode electrode of an electrical circuit. The thickness and properties of the anodic layer will vary with the aluminum alloy, specific anodizing process employed, and electrical current cycle time (ampere-hours).
Anodizing increases corrosion resistance, protects the surface of the aluminum from further oxidization, creates a very hard and durable protective layer, and provides better adhesion for paint primers and glues than bare aluminum. Anodized aluminum can also be used for a number of cosmetic effects because the thick porous oxide layer can absorb dyes, creating an infinite number of colors.
While aluminum anodizing remains the same for all applications, there are two processing methods: batch anodizing of fabricated parts and continuous anodizing of aluminum coils.
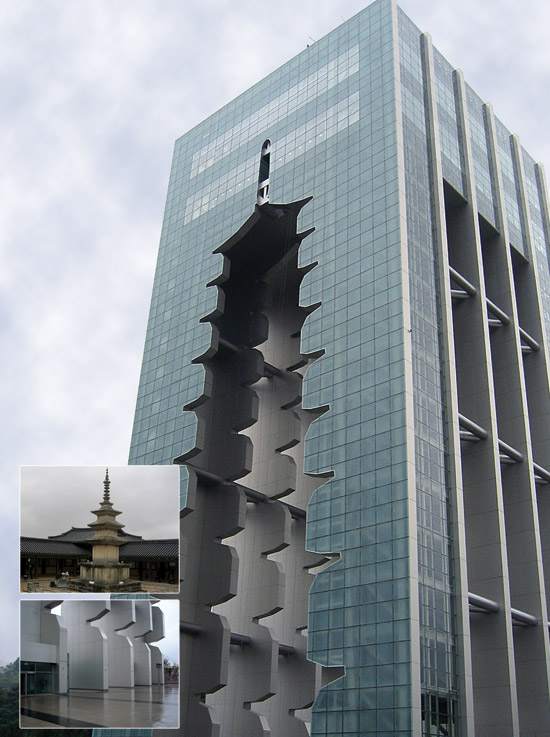 |
Anodized aluminum cut-out honeycomb panels in the Gyeongju Tower in Gyeongju, South Korea, echo the legendary Hwangnyongsa Temple’s wooden pagoda.
Photo courtesy of Lorin Industries |
Batch Anodizing
Batch anodizing, sometimes known as piece part anodizing, is very labor intensive, requiring racking and un-racking of thousands of parts. Parts are immersed in a series of treatment tanks in the anodizing process. Because not all parts are positioned equally in the process—their distance from the electrical current and from each other in the tank varies—their color will vary. Batch anodizing is primarily used for small run jobs not requiring tight finish and color control.
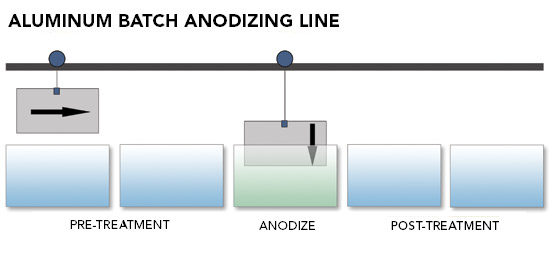 |
Batch anodizing is sometimes known as piece part anodizing.
Diagram courtesy of Lorin Industries |
Continuous Coil Anodizing
The continuous coil anodizing procedure is when coils of wrought aluminum are unwound through a series of tanks where the processing itself takes place. The coils are rewound upon completion ready for shipment and immediate fabrication.
Developed as an alternative to piece part or batch anodizing, continuous coil anodized aluminum is the most useful product for the design and construction industry due to its efficiencies and versatility. Moreover, since the aluminum travels through a series of tanks in a continuous operation, aluminum coil anodizing has significantly greater color control than a batch process. The result is a very uniform color from start-to-finish and from edge-to-edge of the aluminum coil. The continuous coil anodizing process also maintains a consistent anodic layer, minimizes handling damage since the coil is a single part, reduces manufacturing scrap, and does not come with rack marks like batch anodizing. A typical aluminum coil anodizing line includes three primary treatment processes: pre-treatment, anodizing, and post-treatment processes.
 |
Coil anodizing is a continuous unwinding of aluminum coils through a series of tanks.
Diagram courtesy of Lorin Industries |
Pre-treatment. Wrought aluminum is received from the aluminum suppliers with contaminants on the rolling surface. In the first step of the pre-treatment stage, mill oils, grease, aluminum oxides, and dirt are “chemically” removed from the wrought aluminum. If these contaminants are left on the surface, the anodic film may become pitted, create a non-uniform anodize thickness, or cause visual imperfections in the surface quality of the finish.
Another step in the pre-treatment process is to prepare the surface for finishing requirements as specified by the design professional. The surface can be etched for a soft, matte appearance or brightened for a mirror-like appearance.
• Etching in a chemical solution prepares the aluminum surface for anodizing by removing a thin layer of aluminum. Removing this thin layer will clean up any minor imperfections in the aluminum alloy and at the same time produce a matte surface finish. The tight control in the etching process is also used to maintain and manage the gloss of the aluminum surface, allowing for more consistent panel-to-panel matching. Panel-to-panel matching quality is critical if the architect and designer require uniform color appearance between panels on a flat wall structure. Batch anodizing will not satisfy this type of finish control.
• Chemical brightening is a process that smooths the surface roughness of the high-purity wrought aluminum to achieve a non-directional and reflective surface. The brightened surface creates a different dimension in finish quality, allowing design professionals to explore unique reflective and colored finishes. The brightened translucent oxide layer accentuates the rich metallic appearance of the aluminum and does not cover it up like paint or a rolled coating.
• Electropolishing is an electrochemical process that also brightens high-purity wrought aluminum alloys that have been specially prepared and polished. Specular reflectivity tests have shown that electropolished aluminum will be 10 percent to 12 percent brighter after anodizing than conventional chemical brightening. Electropolishing will produce a sharper, mirror-like reflective image.
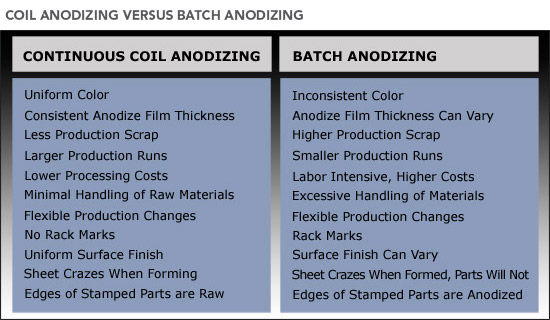 |
Table courtesy of Lorin Industries |
Electropolishing has been around for a long time but the only chemical solution that originally worked was one requiring several pounds of toxic and costly-to-treat chromic acid or hexavalent chrome which is a known carcinogen. Leading aluminum coil anodizing manufacturers have now developed electropolishing solutions that do not require chromic acid.
Electropolished aluminum finishes are used where applications such as solar concentrators require a reflective surface to capture and distribute light efficiently. Electropolished brightened aluminum is significantly lower in cost as compared to silver-plated glass mirrors that are commonly used as solar concentrators. Coil anodized aluminum that has been electropolished can also be used for decorative metal panels in architectural design.
Case Study
Roll-Formed Coil Anodized Aluminum Panels: Mercedes-Benz Superdome, New Orleans, LA |
The Mercedes-Benz Superdome in Louisiana required restoration and resurfacing after Hurricane Katrina caused significant damage to New Orleans. The state-owned building, which was part of the New Orleans skyline for over 40 years, gained negative international attention in the aftermath of the hurricane. This meant that its restoration would be monitored very carefully worldwide.
One of the performance-based criteria for the work to be performed was specifying a 365,000-square-foot cladding system. There were several requirements for the system: It should replicate the New Orleans Saints’ gold; it should allow the beauty of the embossed aluminum to show through; its panels be strong enough to pass upgraded wind testing; and it should retain its color for many years to come.
“We were tasked by our client, the state of Louisiana, to match the original specified custom anodized aluminum color of the Mercedes-Benz Superdome, returning it to its original aesthetic appearance of 1975,” says Brad McWhirter, AIA, lead project manager, Trahan Architects. “It was imperative that it be rebuilt to its original design aesthetic, but meet all of the stringent finish and performance standards of modern day exterior building systems.”
Requirements for ease of installation, ease of panel replacement, color consistency, panel strength, and rain screen qualities were solved by selecting roll-formed coil anodized aluminum. “Initially, we had reservations about roll forming an anodized finished product due to the surface hardness, but this proved to be a non-issue in terms of cracking or crazing of the formed profile,” says Dan Vinet, president, Kalzip, cladding system fabricator. |
Anodizing. Once the surface is prepared for the design professional's finish requirements, an aluminum oxide layer is built from the base aluminum substrate itself. The aluminum is immersed in a tank containing a sulfuric electrolyte (sulfuric acid electrolyte is most commonly used). Electrical current is then passed through the electrolyte. The aluminum is the anode in this electrolytic cell; the tank is the cathode. Voltage applied across the anode and cathode causes negatively charged anions to migrate to the anode where the oxygen in the anions combines with the aluminum to form aluminum oxide (Al2O3).
Raw (not-anodized) aluminum exposed to the outside harsh environment will build its own natural oxide layer and protect itself from further corrosion. However, this oxide layer will be soft, thin, white in color, and non-uniform. The aluminum anodizing process improves upon nature, creating a natural product that accentuates and celebrates the metallic look of aluminum through a uniform translucent protective layer which is very thick and hard with qualities equal to that of a sapphire.
AAMA 611-12, Voluntary Specification for Anodized Architectural Aluminum, published by the American Architectural Manufacturers Association (AAMA), describes the test procedures and requirements for high performance (Architectural Class I Anodic Film Thickness) used primarily for exterior building products and other products that must withstand continuous outdoor exposure, and commercial (Architectural Class II Anodic Film Thickness) architectural quality aluminum oxide layers applied to aluminum extrusions and panels for architectural products. The specification also covers anodized finishes produced in batch or continuous coil.
Post-treatment. The aluminum oxide layer is porous and well suited for coloring using two common methods: absorptive dye coloring and electrolytic two-step coloring.
• Absorptive dye coloring employs both organic and inorganic dye materials. Since the aluminum oxide layer is a very porous structure, it will absorb staining materials. Any colored fabric dyes can be absorbed into the aluminum oxide layer and will deliver vibrant colors that cannot be matched by any painted metal system currently on the market. Inorganic dye materials can also be absorbed into the oxide pores and offer fade-resistant colors.
• Electrolytic two-step coloring is a process that offers color versatility and is the most technically advanced coloring system available today. This coloring technology is used for architectural applications requiring UV stability and exposure in harsh environments. After an oxide layer is built, the metal is immersed in a bath containing an inorganic metal salt. Electrical current is applied which deposits the metal salt into the base of the anodic pores. The resulting color is dependent on the type of metal salt used and specific anodize processing conditions applied. This coloring process offers exceptional fade resistance and is very suitable for exterior applications. Design professionals should be aware that color-matching capabilities can vary among manufacturers and it is recommended that a continuous coil anodizing process be requested for tight color control and panel-to-panel matching capabilities.
Sealing is the final step in the anodizing process. Proper sealing of the porous oxide layer is absolutely essential to the satisfactory performance of the anodic layer. The pores must be rendered nonabsorbent to provide maximum resistance to corrosion and stains. The sealing process also locks in colors and helps minimize any color degradation. Sealing is accomplished through a hydrothermal treatment in proprietary chemical baths. Hydrothermal treatments hydrate the anodized pores, stopping the anodization process.
However, in some cases, unsealed products can be effective and offer a viable alternative for an adhesive-friendly surface. For example, an unsealed oxide layer can absorb some printing inks and is used quite readily in identification nameplate applications.
 |
Standards AAMA 6111-12 govern required thicknesses of anodized layers for different applications.
Chart provided by Lorin Industries |
Anodizing may be built on chemistry, but through the skill and artistry of the anodizer, buildings and products can become more alive—celebrating the beauty of the metal instead of covering it up with paints or coatings.
Properties of Anodized Aluminum
Anodized aluminum is well suited for architectural applications for several reasons:
Durability and abrasion resistance.Having an oxide layer that is very durable and resistant to abrasion, anodized aluminum is tough enough to withstand both the rigors of spaceflight and adverse climatic conditions.
The thickness of the anodized layer for architectural use should be specified as either an Architectural Class I (minimum of a 0.700 mil or 18 micron thickness) or Architectural Class II (minimum of a 0.400 mil or 10 micron thickness) according to AAMA specifications (see the chart in the online version of this course). Features of the oxide layer include:
• Three times harder than the aluminum itself and provides a natural abrasion resistance not found in copper, zinc, brass, bronze, or stainless steel.
• Integral with the aluminum substrate and therefore very durable—it cannot chip, flake, or peel.
• Protects the underlying metal and self-heals by building its own oxide layer if cut or scratched.
Strength and flexibility. Aluminum's high strength-to-weight ratio has many advantages for architectural applications. It allows design professionals to build lighter structures with more stability and greater design flexibility. This can minimize expenditures on foundations and structural support elements, thereby reducing overall costs. Anodized aluminum will flex or deflect more than steel which lessens the force of impact loads.
 |
After 28 years, a dark bronze anodized aluminum roof has less corrosion than a 15-year-old polyester painted roof.
Photo courtesy of Lorin Industries (top)
Photo courtesy of Kalzip (bottom) |
Corrosion resistance. The oxide layer is resistant to corrosion and is one of anodized aluminum's greatest strengths.
• The aluminum oxide layer is tenacious, hard, and instantly self-renewing because aluminum spontaneously forms a thin, but effective protective oxide layer that prevents further oxidization or corrosion if scratched.
• Anodized aluminum will not patina like copper and zinc, nor rust like steel, nor weather like brass. It is an excellent material to use in marine environments and coastal waters. Salt-water exposure will not corrode an anodized aluminum surface because of its neutral pH.
• Anodized aluminum is highly resistant to weathering, even in many industrial atmospheres that often corrode other metals. The major pollutants in an urban environment are carbon monoxide and carbon dioxide, which have no effect on an anodized aluminum surface.
Color control and selection. Anodized aluminum may be processed to any color in the visible light spectrum and is able to closely match any custom color requirements specified by architects and designers.
• As noted previously, an aluminum oxide layer has a very porous structure and will absorb staining materials such as fabric dyes or inorganic metal salts, depending upon the coloring method applied.
• Since the aluminum oxide layer is part of the aluminum itself, the dye is absorbed into the anodic layer and will not chip, flake, or peel.
• Anodized aluminum can be colored as a low-cost alternative to match other metals such as stainless steel, brass, muntz (a form of brass), bronze, zinc, gold, and copper.
• Continuous coil anodized aluminum has superior color control compared with batch processing.
 |
Left: Anodized aluminum in a clear matte finish was specified for sunshade louvers at the Winspear Opera House, Dallas, Texas.
Right: High-pressure laminate anodized aluminum may be used for interior walls with multiple colors.
Photo courtesy of Lorin Industries (left)
Photo courtesy of Wilsonart International (right) |
Finishing options. In addition to multiple color and metallic finishing options, manufacturers can offer other anodized aluminum finishes such as specialty embossed textures.
Production efficiencies. Anodized aluminum arrives clean and ready for immediate fabrication. Coil anodized aluminum can be processed in large coils with a significant amount of lineal feet of material. This results in less machine set-up time and less processing scrap.
Lightweight. Anodized aluminum (0.339 lb/ sq ft) weighs 60 percent less than stainless steel (1.044 lb/sq ft), brass (1.180 lb/sq ft), and copper (1.180 lb/sq ft). Anodized aluminum is also safer to handle during fabrication because of its lighter weight than other metals. It can also lower overall weight of products, reducing fuel usage, harmful emissions, and overall energy consumption.
 |
Anodized aluminum is significantly lighter than other metals.
Chart courtesy of Lorin Industries |
Reflectance properties. Clear anodized aluminum can play a significant role in cool roof design because of its higher solar reflective index (SRI), solar reflectance, and thermal emittance than, for example, white polyvinylidene fluoride (PVDF) painted aluminum.
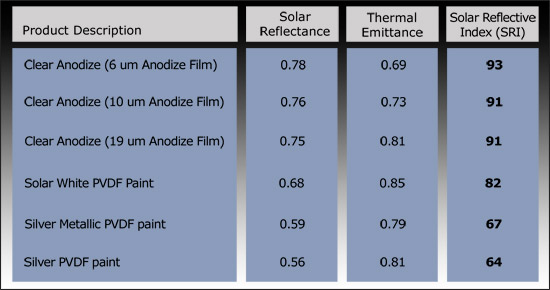 |
Comparison of reflectance and thermal emittance properties of anodized aluminum and polyvinylidene fluoride (PVDF) paints.
Table courtesy of Lorin Industries |
Testing standards comply with ASTM C1549 for total solar reflectance; ASTM C1371 for Thermal Emittance and ASTM E1980 for solar reflectance index (SRI) calculations.
Adhesive quality. While some applications require roughening of the aluminum surface for good adhesion, anodized aluminum is clean and ready for taking on adhesives without the health risks of breathing in aluminum dust particles. The aluminum oxide layer will accept adhesives without the use of a chemical treatment using hexavalent chrome. Anodized aluminum also outperforms other adhesion processes such as grit blasting and vapor degreasing.
Comparisons with Other Materials
 |
Anodized aluminum can be matched to simulate several other metals like antique copper and stainless steel.
Photo courtesy of Lorin Industries |
Compared with PVDF paints and 316 grade stainless steel, anodized aluminum is somewhat less expensive, yet considerably less expensive than brass, natural zinc, and copper. Another advantage is that anodized aluminum weighs approximately 60 percent less than most other metals and is therefore much safer to handle during fabrication. The reduced weight also results in lower transportation costs.
Anodized aluminum has the advantage of a metallic appearance but not the disadvantage of detrimental oxidization that occurs with other natural metals. Following is a summary of the advantages and characteristics of various anodized aluminum finishes as compared to other metals:
Copper anodized aluminum. Copper is a unique metal with a distinctive look that makes it appealing for many building applications. But like other metals today, its cost is increasing and its weight and workability can complicate and add expense to the construction or manufacturing process. Copper anodized aluminum can offer the visual appeal of copper without many of its disadvantages:
• Provides a consistent, stable, and uniform color that will not stain like natural copper.
• Natural copper used in architectural structures today will eventually corrode and oxidize over time to create a green color called patina.
• Comes with a substantially lower price tag and is one-third of the weight of natural copper.
Typical architectural uses include: exterior composite or honeycomb panels, ceiling system designs, elevator panels, store fronts, retail store decoration, gutters and rain screens, and roofing systems.
Stainless anodized aluminum. Stainless steel has a clean, classic appearance, but its weight and workability can complicate and add expense to the construction or manufacturing process. Stainless anodized aluminum provides the appealing look of stainless steel plus several important advantages:
• Provides approximately 60 percent more square feet per pound than stainless steel.
• Will not show finger prints as much as stainless steel. The surface finish will not stain as easily and cleans up with only mild soap and water. No harsh chemicals are required.
• Durable, low-maintenance surface resists scratches and dents and can't chip, flake, or peel.
• Stainless anodized aluminum does not contain levels of chromium to prevent rusting, as does stainless steel. This contributes to a lower cost and avoids any potential health risk arising from the disposal of a carcinogenic substance.
• Increased production efficiency. Larger coil sizes, faster fabrication, and material that arrives clean and ready to use.
Typical architectural opportunities for stainless anodized aluminum include exterior composite and honeycomb panels, ceiling panels, column covers, elevator cab interiors, directional signs, and commercial kitchen back-splashes.
Brass anodized aluminum. One of the attractions of brass is its deep color and soft textures. Brass anodized aluminum has the same appeal plus many advantages over the natural metal:
• Provides approximately 60 percent more square feet per pound than natural brass.
• Will not tarnish or stain, unlike natural brass, which must be protected from the environment with an applied coating to prevent further oxidization.
• Since copper, a very expensive metal, is the base element found in brass (it is alloyed with a high percentage of zinc), the cost of brass is considerably higher than that of anodized aluminum.
Typical architectural uses of brass anodized aluminum include shopping mall store fronts, perforated parking garage screen panels, elevator cabs, ceiling panels, and decorative panels for interior decoration.
Zinc anodized aluminum. Long used in parts of Asia and Europe as a building envelope material, zinc has sustainability attributes and is growing in popularity in the U.S. When zinc anodized aluminum is compared with natural zinc, the former has several advantages for some applications:
• Provides 60 percent more square feet per pound than natural zinc.
• Does not scratch and burnish as easily as natural zinc and therefore has less handling and processing damage.
• Unlike natural zinc, zinc anodized aluminum will not “crack” during fabrication and bending in temperatures less than 40 degrees F.
• Natural zinc is difficult to clean, fingerprints easily, and over time will change color through environmental exposure. Zinc anodized aluminum is significantly easier to clean and will not change color in harsh environments.
Typical architectural uses include standing seam roofs, wall cladding, exterior composite and honeycomb panels, accent decorative trim, and interior decorative panels.
Paint. The anodized aluminum translucent oxide layer accentuates the rich metallic appearance of the aluminum and does not cover it up like paint. The oxide layer will not chip, flake, or peel like paint. While comparable in cost, PVDF paint does not have the benefits of anodized aluminum.
• If painted carbon steel is exposed to air and moisture, the steel will oxidize and red rust may “creep” under the coating causing the paint to peel and flake off. This is quite different from oxidization (corrosion) in steel, where red rust puffs up and flakes off, constantly exposing new metal to corrosion. Aluminum will create its own oxide layer and protect from any metal loss.
• Organic paints will chalk over time. Chalking is caused by a degradation of the resin systems at the surface of the painted finish, due predominantly to UV exposure. As the paint resin system breaks down, resin particles, along with imbedded pigment particles, lose adhesion and take on a white appearance. Anodized aluminum will not chalk.
• The aluminum oxide layer does not emit ozone depleting volatile organic compounds (VOCs) like PVDF paints.
• The anodic layer is harder than any PVDF paints on the market. In accordance with ASTM D3363, Test Method for Pencil Hardness, the aluminum oxide layer passes the maximum rating of 9H.
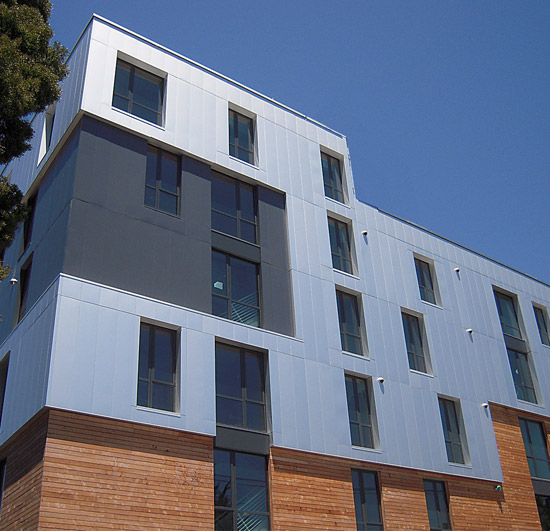 |
Composite anodized aluminum panels were used as exterior cladding for a UC Berkeley residence, Berkeley, Calif.
Photo courtesy of Westmet International |
Types of Fabrication of Coil Anodized Aluminum
Roll forming is a continuous bending operation in which sheet or strip metal is plastically deformed along a linear axis. Tandem sets of rolls (known as roll stations) shape the metal in a series of progressive stages until the desired cross-sectional configuration is obtained. As a continuous process, roll forming is ideal for producing parts with long lengths or in large quantities. Coil anodized aluminum can be easily roll-formed like many other metals into many different configurations of width, height, and pattern. One example of an application is the Mercedes-Benz Superdome in New Orleans, Louisiana (see case study one).
Honeycomb panel construction typically consists of an aluminum honeycomb core sandwiched and bonded between two anodized aluminum sheets. This provides high rigidity and an extremely low weight. It is particularly applicable as wall cladding for high wind load locations and large self-supporting structures.
Composite panel construction. These panels are typically comprised of a polyethylene or thermoplastic core sandwiched between two anodized aluminum sheets.
Solid panels can be formed using a press brake machine that bends metal. The lower part of the press contains a V-shaped groove. The upper part of the press contains a punch that will press the sheet metal down into the V-shaped die, forcing it to bend.
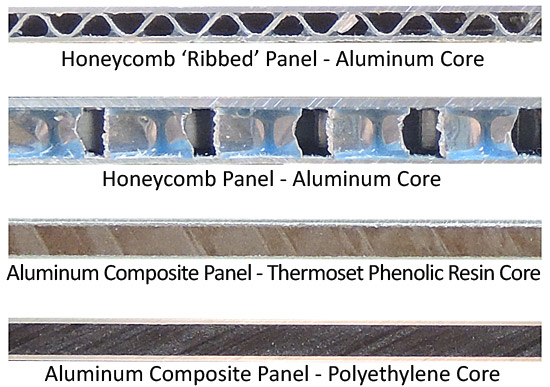 |
Examples of how anodized aluminum can be fabricated into formable panels
Image courtesy of Lorin Industries |
Stamped. Anodized aluminum can be formed into many components just like other metals such as steel, copper, brass, and zinc. A metal sheet is stamped or pressed on a machine using dies and hydraulics to create the designs. It is performed in rapid succession and involves various techniques for the types of shapes and designs that are being created. Pre-anodized aluminum may not be able to sustain a deep drawn stamped part.
Other fabrication processes include laser engraving, silk screening, chemical and mechanical etching, and high-pressure laminating.
Case Study
Coil Anodized Aluminum Honeycomb Panels, Gyeongju Tower, South Korea |
 |
Photo courtesy of Lorin Industries |
The Gyeongju Tower, part of the Gyeongju World Cultural Expo Park located in Gyeongju City, North Gyeongsang Province, South Korea, is an architectural landmark achievement. The 17-story (82-meter) building was built with a cut-out in the center resembling the legendary nine-story, sixth century Hwangnyongsa Temple’s wooden pagoda in South Korea.
The principal architect, building owners, and city officials were interested in a reflective, metallic finish that would illuminate the structure and show off their ancestral heritage. They were also insistent that the honeycomb fabricated panel have a durable finish, be corrosion resistant, and have a consistent panel-to-panel match.
Anodized aluminum honeycomb panels with a clear matte finish maintained, rather than covered, the aluminum’s reflective properties unlike so many buildings in Korea that are obviously painted. Since the anodized aluminum was processed in a continuous coil operation, the panel match quality far exceeded expectations as compared to batch anodizing producers. Since the aluminum oxide layer is three times harder than the aluminum itself, durability of the finish was not a concern. |
Sustainability and the Environment
Aluminum is the most abundant element in the earth's crust and its environmental advantages are widely acknowledged.
Recyclability
As one of the most durable and versatile of metals, it is 100 percent recyclable. According to the Aluminum Association, about one-third of all aluminum produced in the U.S. today is from recycled sources saving some 95 percent of the energy required to produce aluminum from raw materials. Once produced, it can be recycled repeatedly without any loss in quality and reused in the manufacturing of consumer goods. The recycled content of aluminum flat-rolled products in the U.S. building market is estimated at 85 percent; 60 percent is from post-consumer scrap sources according to the Aluminum Association.
Compliance
Resource Conservation and Recovery Act. One leading manufacturer of anodized aluminum reports that aluminum anodizers have little difficulty complying with federal and state environmental regulations such as the 1976 Resource Conservation and Recovery Act (RCRA) governing the disposal of solid waste and hazardous waste.
U.S. Environmental Protection Agency. Anodized aluminum, a water-based process, does not contain any volatile organic compounds and will not burn and emit toxic fumes. There are no vehicle solvents, no carrier resins, and any pigmentation used in anodizing is created by extremely small amounts of metals or dye securely locked within the hard surface. Under U.S. Environmental Protection Agency (EPA) rules, conventional anodizing generates no hazardous waste; nor does it use EPA listed toxic organics. The involvement of heavy metals is dramatically lower than exterior-use paint pigments or plating.
Cleaning and maintaining anodized aluminum requires no harsh or toxic chemicals. The anodized layer should be cleaned with a neutral pH solution. Highly alkaline (with a high pH) or highly acid solutions (with a low pH) will damage the oxide layer.
NSF/ANSI. Clear anodized aluminum products are compliant with NSF/ANSI Standard 51 for direct food contact applications. Color anodized aluminum meets requirements for NSF/ANSI splash zone standards for non-food contact surfaces.
Restriction of Hazardous Substances Directive. The majority of aluminum anodizers are compliant with the Restriction of Hazardous Substances directive (RoHS) (a European Standard), which aims to restrict certain dangerous substances. Any RoHS compliant component is tested for the presence of lead, cadmium, mercury, hexavalent chromium, polybrominated biphenyls (PBB), and polybrominated diphenyl ethers (PBDE).
Fire Safety
In solid form aluminum does not produce flames or emit any toxic fumes. At over 660 degrees Celsius (1,220 degrees F) it will melt and not burn. When ground into fine powder, aluminum will burn and is a common component of sparklers and the sparks produced in fireworks.
Energy Saving
Aluminum is a good conductor of electricity while the anodic layer is an insulator. Combinations of these two properties can be incorporated into systems that save energy and materials. With their higher solar reflectance index values than white painted aluminum, anodized aluminum roofing products deliver energy savings for cool roofs.
Leadership in Energy and Environmental Design (LEED®)
Following are categories where anodized aluminum could contribute LEED points under 2009 New Construction and Major Renovations (updated April 2013):
Sustainable Sites. SS Credit 7.2: Heat Island Effect–Roof (1 Point).
Intent: To reduce heat islands (thermal gradient differences between developed and undeveloped areas) to minimize impact on microclimates and human and wildlife habitats. Clear anodized aluminum produces a value for SRI of 0.73 for low-sloped roofs, exceeding the value required by LEED/ENERGY STAR for low or steep-sloped roofs.
Materials and Resources. MR Credit 4: Recycled Content: 10%-20% (post-consumer + ½ post-industrial) (1-2 Points)
Intent: Increase demand for building products that incorporate recycled content materials, thereby reducing impacts resulting from extraction and processing of virgin materials.
Requirements: Use materials with recycled content such that the sum of post-consumer recycled content plus ½ of the pre-consumer content constitutes at least 10% (1 Point) or 20% (2 Points), based on cost, of the total value of the materials in the project.
Newly developed recycled aluminum alloys can qualify for LEED points in the MR category. One alloy that qualifies has 70% post-consumer scrap content with an anodized quality surface.
Indoor Environmental Quality. EQ Credit 4.2: Low-Emitting Materials: Paints and Coatings (1 Point)
Intent: Reduce the quantity of indoor air contaminants that are odorous, irritating, and/or harmful to the comfort and well-being of installers and occupants.
Requirements: VOC emissions from paints and coatings must not exceed the VOC and chemical component limits of Green Seal Standard GS-11 requirements. Anodized aluminum contribution: 1 Point–anodized aluminum emits no VOCs.
Conclusion
Anodized aluminum has many properties that make it a functional, versatile, and environmentally responsible choice for design professionals. Strong and corrosion resistant it has built-in durability, ease of maintenance, and will not chip, flake, or peel. Compared with batch anodizing, continuous coil anodized aluminum processing delivers many more advantages such as uniform colors, surface and edge consistency, plus metallic finishes that echo those of natural materials but do not degrade. Coil anodized aluminum is fabricated for a range of applications from roll-formed and composite panels for exterior cladding to stamped and perforated designs for interior uses. Design professionals should also note that anodized aluminum is eligible for LEED points.
|
Lorin Industries Lorin Industries offers architects and designers a full range of anodized aluminum finishing solutions for a multitude of architectural applications. Our world leadership in metal finishing continues through innovation and creativity, keeps us at the leading edge of technology.
http://www.lorin.com/
|