Code Compliant Exterior Systems for Wood-Framed Building Envelopes
Structural Framing and Sheathing
The first and most common purpose of wood framing is to provide the structural support for the building. Several chapters in the IRC have very specific tables and charts indicating the required sizes of framing members for floors, walls, and roof-ceiling construction. These tables break down the allowable spans for different types of wood species at different spacings (16 inches, 24 inches on center, etc.). While this information is important and valuable for both the engineering of a wood-framed structure and identifying code compliance, there is more to the structural requirements than the framing.
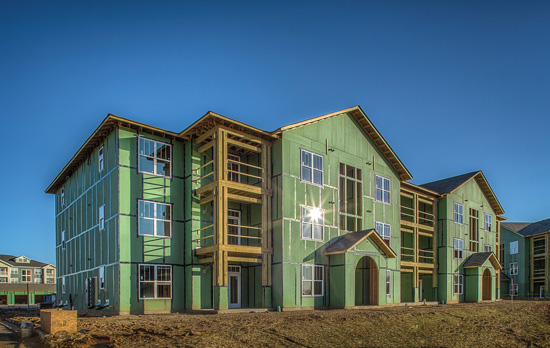
Photo used with permission of Huber Engineered Woods LLC ©2013
The applicability of a code or its specific requirements starts first with a determination of the building type based on the way the building is used, its occupancy, size, or construction type.
Structural engineering principles and the IRC recognize that if a wood-framed wall is not properly braced, it will move, warp, and potentially fail. This is true not only of a particular wall, but of the entire building as well. Dramatic failures of this type can be found in news coverage of storms or floods, where a wood-framed residence is seen slanted to one side or even collapsed with a pitched roof still intact above. The wall bracing in these cases was subjected to wind or other forces that exceeded the capacity of the bracing. As such, the IRC and the IBC require that exterior walls be designed not only to provide for the direct vertical loads imposed on them, but also for the other horizontal or shear loads that can be imposed by outside forces.
There are multiple methods for providing the needed wall bracing as recognized and allowed for by the building codes. The historical approach was to use “let-in” corner bracing, which was rather labor intensive and required a series of studs to be notched at an angle to receive a one-by-four member recessed to be flush with the face of the studs. Although the IRC still recognizes that approach, the availability of structural wall panels made from plywood, structural particle board, oriented strand board (OSB), or other acceptable engineered products are much more popular and common. The reasons are obvious, in that a continuous layer of structural sheathing provides a more consistent, rigid, wall bracing system that is quicker and more economical to install. It also provides a continuous, fairly smooth surface for other layers of material to be applied. Hence, the codes recognize a series of different materials that can be used for continuous or intermittent bracing of exterior wood-framed walls.
Because there are variables between buildings and their locations, the codes call for a bit more detail in the selection of wall bracing material. Specifically, the code identifies zones or locations where bracing is required as a minimum structural requirement. It goes on to identify nailing or fastening patterns and spacings, taking into account the spacing of wood framing members. It further indicates the minimum thickness of selected materials since more thickness essentially equates to more strength. There are also tables and criteria for addressing seismic and wind loads of different degrees, which directly impact the structural requirements of structural sheathing that acts as bracing.
Roof construction follows a similar set of requirements. The IRC identifies allowable spans for rafters based on varying structural criteria and also recognizes the use of pre-engineered roof trusses. But, it also goes on to identify the minimum requirements for wood structural panel sheathing used over the rafters or roof trusses. Attachment, span, thickness, and other traits of the structural sheathing are all identified based on reference to the appropriate tables. The additional variable is the presence or absence of snow loads to various degrees, which must be taken into account for the sheathing, just as it is for the framing members. Hence, the sheathing thickness comes into play based on the anticipated loading and the spacing of the framing beneath it.
Whether used for wall or roof construction, it is important to recognize that there is a wide variety in available sheathing products, and not all of them carry sufficient structural strength to be used everywhere. Inadequate strength may not lead to dramatic and sudden failure, but it could likely lead to sagging and deterioration not only of the structure, but of other building components and systems as well. The American Plywood Association (APA) has published a voluntary product standard known as PS 2-10: Performance Standard for Wood-Based Structural-Use Panels. This is the document that forms the basis for the definition, testing criteria and certification of different types of wood panels, including sheathing, structural sheathing, and combination subfloor underlayment applications. For sheathing, it defines the general minimum requirements for use in construction applications, such as a covering material for exterior walls and roofs when fastened to supports spaced in accordance with the span rating of the wood panel. It also defines a Structural 1 Sheathing, which must meet all of the requirements for common sheathing plus additional requirements identified in the Performance Standard for “cross-panel strength and stiffness and for racking load performance.” This higher performance has a greater capacity for use in braced shear wall designs, making it appropriate to resist high winds and other forces. Prudent designers will tend to routinely specify Structural 1 panels to eliminate any guesswork for safety and structural integrity. Fortunately, some manufacturers seek that certification as a matter of routine for their products, recognizing that it is a designation that makes for a better product and a better building in the end.
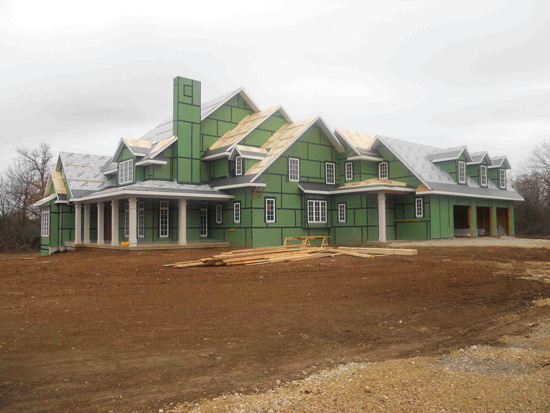
Photo used with permission of Huber Engineered Woods LLC ©2011
Inadequate strength may not lead to dramatic failure, but it could lead to a compromised structure. There is more to structural requirements than framing.