Right Roof = Right Requirements + Right Materials + Right Place
Liquid Applied
Liquid membrane roofing was developed in Europe in the 1980’s. These roofing systems are manufactured in various chemical compositions, including silicone, acrylic, and urethane. Liquid systems are modern built-up roofs where layers of liquid membrane and reinforcement are installed on the roof. Typically a base coat is installed, then a layer of reinforcing fabric is installed, and then a top coat. Depending on the formulation, liquid roofs can be installed by brush, airless sprayer, or roller. Completed thicknesses will vary by product, but can be more than 60 mils depending on the system.
Liquid applied systems offer superior results for complicated flashing and transition details and places that are difficult to access as they are self-terminating and seamless. Liquid membranes are available in reflective white as well as custom colors. Liquid applied membranes are sensitive to extreme temperatures, which can influence both installation and cure times. Roof coatings, which are generally liquid applied membranes without the reinforcement, are ideal for installing on top of an existing roof in overall fair condition without trapped moisture. This will extend the service life of the roof.
Performance Highlights:
- Liquid systems cure very quickly.
- Great solution for difficult penetration details.
- Various formulations have good resistance to oil and grease.
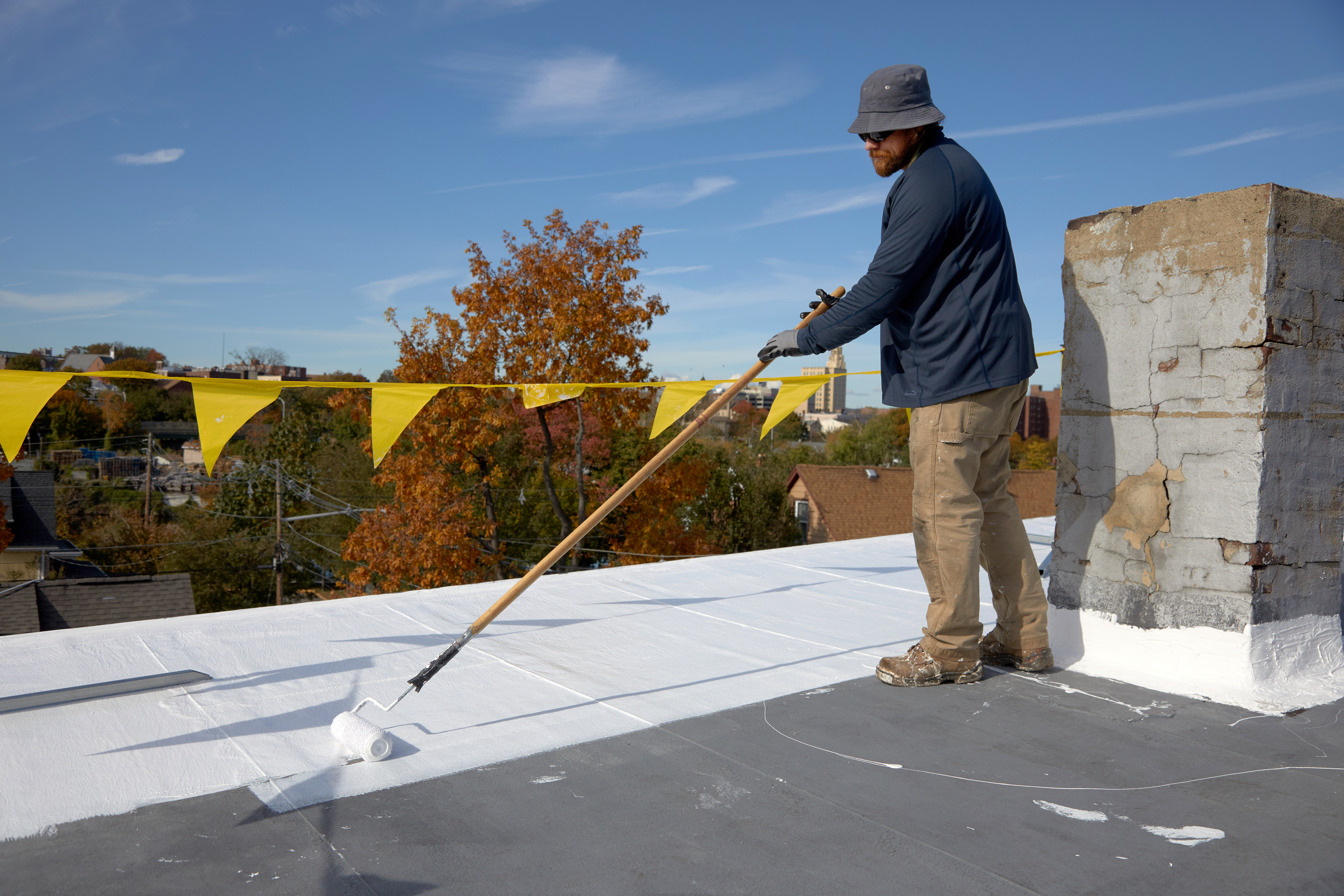
Liquid membrane roof installation in progress.
Membrane Color
Roof color can have a significant impact on the performance of the system and also on the roof surface temperatures; reflective roof membranes can lower the ambient roof temperature. EPDM membranes are traditionally dark in color and TPO, PVC, and liquid roof membranes are typically white or light in color. BUR and modified bitumen roofs can have light colored granules on the cap sheet which can increase reflectivity of a roof’s surface. Two roof surface temperatures, differing only by color, can vary by as much as 60F in the summer heat. Dark colored roofs can reach up to 150F, whereas white or reflective roofing colors can have significantly lower surface temperatures. Using a lighter colored roof can decrease the urban heat island effect in cities, and also may decrease the amount of heat that is able to radiate into a building’s interior. The more heat gain that a roof assembly absorbs, the warmer the interior temperature will be. In the summer, while the heat gain is offset by HVAC systems, the warmer the interior temperature causes the systems to have to run longer, which can increase energy use, and potentially raise energy bills.
For roofs where there is overburden, such as solar panel installations, light colored or reflective roof membranes can lower the ambient roof temperature which allows the panels to function more efficiently. The temperature of a PV panel can significantly impact how much electricity the panel produces; as panels get hotter, they produce less power. According to an article published by GAF, “It is estimated that the efficiency of a PV panel can be up to 13 percent higher when installed over a highly reflective membrane compared to a dark membrane with low reflectance. Also, the use of bifacial PV panels over reflective roof membranes can increase the efficiency by 20-35 percent, as they take advantage of the reflected light.”
Reflective roofs, or cool roofs, are also being installed in many locations to meet local green building standards. Many municipalities have adopted Codes that require new or replacement roofs to meet a minimum Solar Reflective Index (SRI), an indicator of the ability of a roof surface to return solar energy to the atmosphere. The Cool Roof Rating Council has a directory of roof products with SRI values listed for reference.
Membrane Attachment Methods
There are two broad categories of roof attachment; mechanically attached via use of fasteners, and adhered. The attachment method will vary depending on the deck type, membrane type, and project specific requirements such as energy efficiency, fume tolerance, and fire hazards.
Selection of attachment methods should be reviewed for ease of installation in the short-term and energy efficiency over the long-term. Energy efficiency from the roof assembly can be directly related to thermal bridging, which occurs when components allow for heat transfer through the roof assembly. Loss of internal temperatures means that the mechanical equipment will have to work harder to maintain the desired set points. Thermal bridging has the potential to occur at gaps or discontinuities between materials, such as at fasteners in a mechanically attached single-ply system. Particularly where the fasteners penetrate the entire assembly from the membrane through the insulation and into the deck, the fasteners provide a direct thermal path from the exterior to the interior.
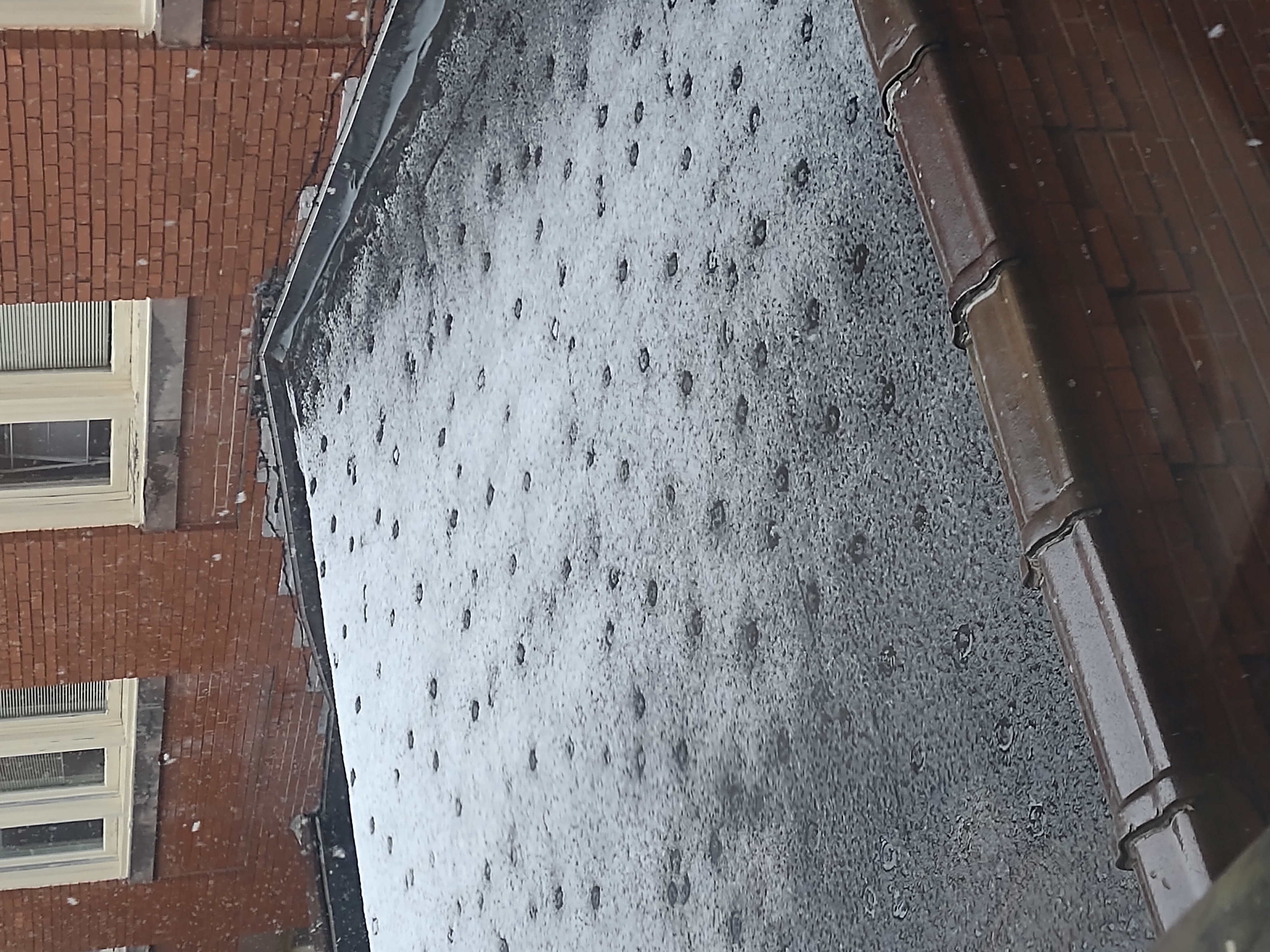
A mechanically attached single-ply system. Thermal bridging from the fasteners is melting the snow on the roof.
Mechanically Attached Systems
Mechanically attached systems are generally referring to single-ply systems as these membrane types often use fasteners to install both the insulation layers and the membrane. The fasteners must be continuous through each layer and into the structural roof deck for securement. The number of fasteners will depend on project specific requirements, but typically for a mechanically attached system, there is a minimum of six fasteners per 4’x8’ insulation board, and additional fasteners for membrane attachment. This can lead to a substantial number of fasteners penetrating and creating thermal bridges within the roof assembly. It is important to note that most systems require the first layer of insulation to be attached with fasteners, even if the specified system is to be adhered. However, by burying the fasteners in the system, and adding adhered layers of insulation and membrane on top of the mechanically attached insulation layer, the interior air loss and thermal bridging is significantly reduced.
Mechanically attached single-ply systems are also subject to billowing in high wind events. Billowing, or fluttering, of a membrane is when wind causes a negative pressure by pulling interior air into the roof assembly creating uplift force on the roof assembly. Although this is an acceptable behavior of single-ply membranes, over time, it can cause stress and fatigue on the mechanical attachments and membrane. Interior air that is pulled into the roof assembly equates to energy loss since often the temperature controlled air may warm or cool based on the temperature of the membrane.
It should be noted that mechanically attached single-ply systems are commonplace in the market and have had many years of successful installations. These systems are also able to achieve high wind uplift ratings due to the direct attachment to the roof deck and have no fumes associated with the installation.
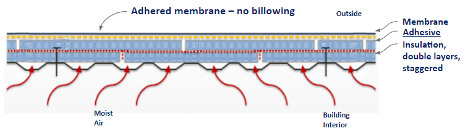
Adhered system where only the first layer of insulation is mechanically attached, significantly reduces interior air loss and thermal bridging.
Asphaltic systems can be installed utilizing fasteners, however, these fasteners are only installed to secure the insulation to the deck. While there are significantly less fasteners used in asphaltic systems than in mechanically attached single-ply systems, there is still potential to reduce thermal bridging of the fasteners. Fasteners can be installed only in the first layer of insulation and then each subsequent layer of insulation can be installed with adhesives. Similarly, since asphaltic membranes are not installed with fasteners, they are not subject to billowing like single-ply membranes are, and generally have reduced air movement through the roof assembly.
Adhered Systems
Systems that use adhesives to secure the roof assembly and do not use fasteners, greatly reduce thermal bridging by eliminating the path from the interior of the roofing assembly to the exterior. Adhering also prevents billowing of the membrane, by mitigating the interior air that can be brought into the roof assembly.
Asphaltic based membranes use asphalt to adhere the roof assembly. BUR roofs use several layers of plies and asphalt to form the roof surface. Modified bitumen roofs can be installed several different ways, including using a torch to melt the asphalt plies or by using a cold applied adhesive. The multiple asphalt plies in either system form a robust roofing system that is not penetrable to air or the effects of billowing. Asphalt, and particularly hot (torched-applied or hot mopped) asphalt, can have strong fumes. On an occupied building during a reroof, or a building in close proximity to other buildings, the use of asphalt may not be preferable since HVAC intakes may transport asphalt fumes into the building. Many insurance companies and jurisdictions do not allow the use of torches or hot kettles on the roof due to the fire hazard of open flames. Cold applied modified bitumen applications are an alternative that use an asphaltic based adhesive that is rolled onto the substrate prior to installation of the membrane. Cold applied applications offer the same modified bitumen wearing surface, but with fewer fumes than a traditional torch applied or hot mopped application. Modified bitumen roofs are excellent for mitigating air movement as the multiple layers are impermeable to air, and therefore are not subject to billowing like mechanically fastened single-ply systems.
Single-ply membranes tolerate a wide variety of attachment methods and are able to be both adhered and mechanically attached. The types of adhesives can vary from melted asphalt (with fleece-backed membranes) to various types of commercial adhesives manufactured for specific single-ply membrane types. Although product specific, single-ply adhesives release fewer hazardous fumes during installation, in contrast to those by asphalt based products. These adhesives do not require heating or torching for application and generally come in pails or canisters and can be installed with a roller or a spray attachment. Single-ply adhesives are generally less messy and can be quicker to install than traditional asphaltic based products.
Another adhered option for both single-ply and asphaltic cap sheets is a self-adhered option. For these membranes, an adhesive is factory-applied onto the back of the membrane and a release liner is removed on-site to expose the adhesive once ready for installation. Self-adhered membranes function similarly to a membrane installed with an adhesive, which results in the membrane not billowing on the roof. Self-adhered membranes also have little to no fumes associated with the installation. There is a waste factor to consider, as the release liner will require disposal.
Induction Welded Systems
Induction welded fasteners are another type of roof attachment that is installed frequently in the single-ply roofing market. By definition this is a mechanical attachment method, but it has many of the features of adhered systems. The technique fastens TPO and PVC membranes to the substrate below using a microprocessor-controlled induction welding machine. The thermoplastic roof membrane is welded directly to specially coated fastening plates used to attach the insulation. The combined insulation and membrane fasteners resist wind uplift forces, so that wind loads are more uniformly distributed versus a conventionally attached system. Thermal bridging is also reduced, compared to traditional mechanically attached membrane systems as there are less fasteners required for this installation. There are no application temperature restrictions and there are no fumes or fire hazards associated with the installation.
Ballasted Roof Systems
Ballasted roof systems are where the membrane is not attached to the roof, it is held down by overburden placed on the membrane. Many EPDM roof systems were historically ballasted with gravel such as a smooth river rock stone. Modern day ballasted roofs consist of pavers or amenity spaces and can be installed over most single-ply and asphaltic membranes. The challenge with ballasted systems are the weight of the ballast and the difficulty to find leaks as the ballast must be removed for investigation and repair.
Many insurance companies and municipalities limit the size or prohibit gravel ballast since it can become projectiles during a wind event. Ballasted systems can also present challenges on existing buildings in re-roofing scenarios as more recent provisions increase requirements that older buildings may not be able to accommodate due to weight restrictions or lack or parapet walls.
Overburden Assemblies
Often unused space on the buildings, roof space is more commonly being utilized. Roofs can be a space to integrate solar for renewable energy, rainwater management strategies, rooftop agriculture, and amenity space. While design of the overburden system is important, selection of the roof membrane, the waterproofing layer that protects the building, is critical for the success of the overburden installation. Two main considerations are membrane performance (including color, thickness, and attachment) and roof assembly configuration, including location of the membrane in the assembly. The improper selection of membrane can result in water infiltration into the building, costly repairs, or even replacement. Incorporation of a leak detection system into the roof assembly may also be beneficial. Special considerations to the type of insulation and the presence of a cover board should be explored. Most importantly, the roof system should be designed to have an equivalent or longer lifespan than that of the overburden systems. When there are leaks, the overburden will require removal which can be costly and damaging to the overburden systems.
Special considerations are needed for the roof assembly when overburden is present. Read this article on Overburden for further information.
Conclusion
Each Roof is Unique
Each roof is unique. A building’s interior use, its climate, and planned rooftop use all will impact roof design. The roof assembly itself can have a profound impact on the energy efficiency and operation of a facility. While its main objective is to mitigate water entry into the building, appropriate quantities of insulation, and air and vapor control can affect how the roof functions over time. A well-designed roof assembly includes consideration of all components: from roof deck, insulation, and coverboard to attachment method and membrane. In addition, proper detailing and integration of the roof membrane, as well as the roof installation are paramount to the overall success and longevity of the roof system.
Kristin Westover PE, is part of the Building and Roofing Science Team where she works with designers on all types of low-slope roofing projects to review project design considerations so designers can make informed roof assembly decisions.