Right Roof = Right Requirements + Right Materials + Right Place
- Consider additional insulation to maintain interior temperatures as well as appropriate air sealing to prevent condensation within the roof assembly.
- Consider the use of a vapor retarder at the roof deck level to prevent condensation and uncontrolled air movement.
- Consider the transition between steep slope and low slope materials including compatibility and warranty.
- Consider a dedicated vapor retarder or air barrier at the roof deck level with appropriate air sealing detailing to ensure no air loss occurs into the roof system.
- Consider a coverboard and insulation with a high compressive strength. A thicker and more robust membrane will also provide resistance to added foot traffic and weight of the overburden system.
Building Location and Climate
The climate zone where the building is sited also impacts assembly design and specification—whether the structure is in warm and humid Florida, in the dry and cold mountains of Colorado, in temperate and windy Indiana, or within a major metropolitan heat island, like New York City or Los Angeles. The geographic location of a building will affect the weather that the building needs to endure including the amount of rain, snow or sun. More robust membranes and roofing assemblies should be considered where there are extremes of temperature or weather conditions, including high winds and hail. Weather and temperature constraints can also vary greatly depending on exposure and the structure’s position within an urban or rural environment. A more robust system will allow for the roof assembly to be resilient to weather events.
Consideration to wind resistance also varies widely, as coastal locations are impacted by higher wind speeds. Additionally, the wind speed that a particular building will need to resist can vary widely even from one part of the state to the next, depending on its immediate surroundings, whether the building is on a hill or isolated location, or more sheltered from wind impacts by taller surrounding buildings or trees.
Local city and county regulations may have specific requirements for reflectivity and volatile organic compounds (VOCs). Reflectivity requirements impact the membrane color selection, which require lighter colored membranes. The limitation of the VOCs will impact the roof attachment method as certain adhesives may not meet the regulations.
Choosing the Right Materials: Roof Components
The main purpose of a roofing system is to shield buildings and their occupants from the exterior climate or weather conditions. This purpose includes providing immediate protection from wind, rain, hail, snow, heat, cold, and sun, as well as sheltering from the long-term impacts of these weather elements. The roofing system must also be able to shed moisture and provide insulation. A roofing "system" is composed of several components that must work together to provide the best overall protection.
Basic roof components for a low-slope commercial roof include:
- Roof deck
- Substrate board/roof board & vapor retarder/air barrier
- Insulation
- Coverboard
- Roof membrane
- Overburden
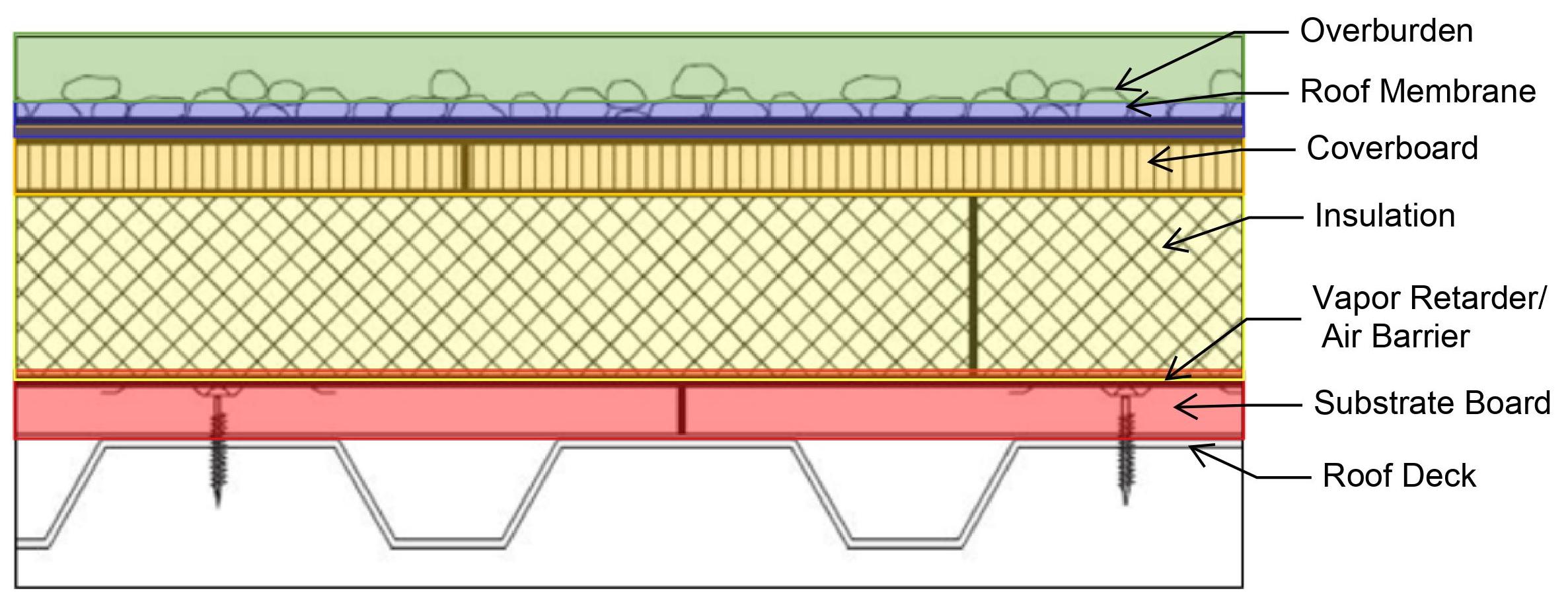
Basic roof components.
Roof Deck
Just as the foundation is the load-bearing portion of a building, roof decking forms the load-bearing portion of the roof system. Decking is designed to bear the weight of the entire roofing system, as well as snow, overburden, or equipment. The maximum load that the roof deck can withstand is most often limited by the overburden, particularly during reroofing of existing buildings.
There are three main roof deck types, classified by material: metal, wood, and concrete. Roof deck selection is influenced by the building construction type, building use, and regional trends. Each has their own implications to roof system selection including roof attachment methods and reaction to moisture.
Metal Decks
Metal decking accounts for approximately 45 percent of low-slope commercial roof decks due to its strength and speed of installation. Metal decks may be installed only as a metal deck or may also include a concrete slab. Additionally, metal decks may be vented or unvented. Vented decks are typically used for lightweight structural concrete systems to allow for drying of the concrete placed on top of the metal decking. For metal decks without concrete, the deck profile and gauge can impact the performance of the roofing system, including structural ratings, wind uplift resistance, and fire resistance.
For metal decks without concrete, which are most commonly unvented metal decks, roof systems are typically mechanically attached to the metal deck. Roof systems can be mechanically attached through all of the layers of insulation, or only the first layer of insulation with additional layers adhered. Ballasting roof materials is also an option, however, wind uplift and weight of specific ballasted assemblies should be verified. Another consideration for metal decks is the flute span capability of the materials placed directly on the metal deck. The concept of flute span capability is directly associated with the strength of the material being installed and its ability to handle the anticipated loads where the material is not supported by the top flange of the roof deck (that is, over the flute). This is directly related to thickness of materials, such as rigid insulation, perlite boards, or gypsum roof boards that may be placed directly on the deck.
While steel takes longer to degrade from moisture than other construction materials, steel is still susceptible to moisture intrusion. Moisture on the steel deck can cause corrosion, including rust, that if left untreated, can weaken the deck structure and require section replacement.
Wood Decks
Wood decks may be composed of plywood, oriented strand board (OSB), plank, panelized, or mass timber. Roughly 25 percent of roof decks are wood, a factor related to both regional construction preferences and the age of the building. Wood is a combustible and organic material, which are primary characteristics that need to be considered when designing low-slope roofing assemblies. Being an organic material, wood is susceptible to moisture so insulation placement and condensation potential are critical in the design. While it is common to have below-deck insulation in wood deck assemblies, the addition of insulation above deck may substantially reduce the condensation potential in assemblies where there is risk. Condensation, or trapped moisture on wood decks can rot the wood deck, which can lead to substantial wood deck replacement during reroofing.
Additional considerations are required to accommodate combustibility requirements. A material such as a fire resistant slip sheet may be required on the deck prior to installation of insulation, or the use of a fire rated insulation board with coated glass fiber facers that will meet a specific fire rating may be installed directly on the wood deck.
Roof systems are typically mechanically attached to wood decks. Where rigid insulation is used above deck, the first layer of insulation can be mechanically attached and subsequent layers can be adhered.