Structural Steel Cast Connections
The first step in the process is to properly identify and understand the structural loading and flow of forces through the structural members in order to create structurally appropriate cast connections. This is where the three-dimensional computer modeling and structural analysis becomes important. By assessing the forces and capabilities of the steel, the shape and thicknesses of the castings can be optimized by reviewing alternatives that meet all of the design requirements of the project. This process also allows for elegant and sweeping forms that follow the natural flow of forces. As an alternative, the connection can be sculpted in different ways purely for aesthetic reasons while still being assessed for proper structural performance. Either way, the end result will be a designed connection that cleanly and smoothly carries the imposed loads while allowing full control of the final appearance.
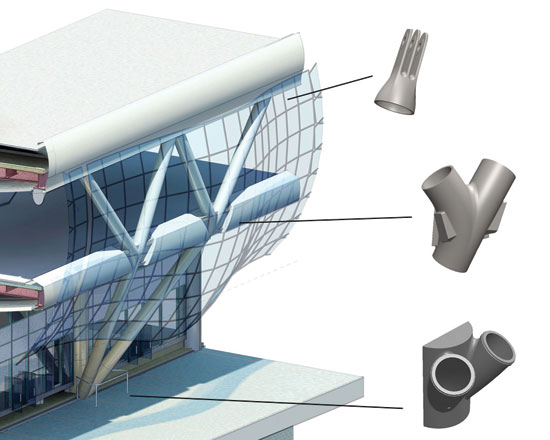
Photo courtesy of CAST CONNEX
Any given project may have a variety of custom cast connectors that need to be modeled and designed by a qualified casting engineer.
Once the preferred connection shape and size are finalized, the full industrial design and detailed engineering of the custom casting will need to be undertaken. The actual casting may include features that are needed for the casting or installation process such as fins or lifting lugs that are ultimately removed after the full structure is in place. This will tie directly into the engineering that goes on in the foundry to create the patterns and molds that will be used for the custom casting. Once all of those details are worked out, a cast of the “first article” needs to be undertaken to determine its full suitability and quality. First article castings are subjected to rigorous non-destructive (and sometimes even destructive) examination to prove out the production process. If anything is not up to par, then changes can be made to the pattern or the feeding and gating system for the casting to produce a casting that passes muster. If the first article is found to adequately meet specifications, then the original pattern becomes the basis for all subsequent castings.
By now it should be clear that there is some necessary lead time that needs to be built in to a design and construction schedule to allow for the full engineering, molding, and first article testing of custom cast products. Further, there will be some time needed to produce the quantity of custom castings that are ultimately needed for a particular design project. That means any given project needs to work within the overall production schedule of the selected foundry that will be providing the cast products. The overall actual production time will vary of course based on things like the size and complexity of the castings, the quantity needed, and the other schedule commitments of the foundry. Hence, all the more reason to engage with casting professionals earlier rather than later to assure that the connections can be made and shipped to the construction site when needed. In the end, the results will likely be very worthwhile, but proper planning and time scheduling will keep expectations in line and help maintain positive relationships between all parties.
Specifying Cast Steel Connections
Based on everything that we have covered thus far, you may have decided to use cast steel connections on a project because of an appreciation that standard steel fabrication may not or cannot achieve what casting can. You also understand that custom castings generally require a longer lead time than conventional fabrication and have allowed for that in the project schedule. While you may know all of this, you also need everyone working on the project to know it too. As a designer, the principal tool for communicating with the contractors and fabricators are the contract documents prepared by your firm. Drawings which show the castings with some general, overall dimensions and maybe some 3D images are appropriate to convey intent and make it clear to bidders that castings are required. But beyond that, the specifications will generally dictate the details of casting requirements.
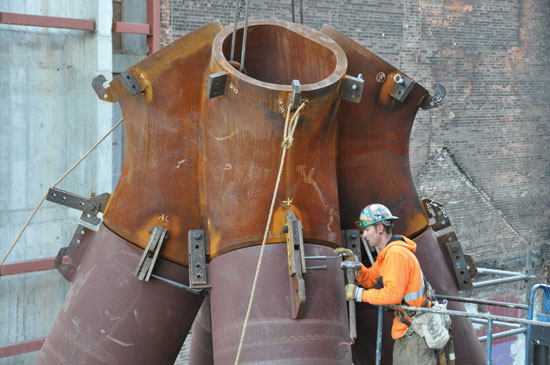
Photo courtesy of CAST CONNEX
Performance specifications are the primary means to communicate the design, fabrication, and installation requirements of cast connections to the construction team.
Since most architectural and general structural engineering offices don't have direct experience in casting design and production, either a specialized casting designer is added to the design team as discussed above, or performance specifications are used that delegate appropriate responsibilities to a suitably experienced party. Such specifications spell out the key architectural features and governing load-cases (i.e. the performance criteria) which must be met such that the casting designer can satisfy architectural, structural, and castability requirements, simultaneously. Including these items within the performance specification can help ensure that the design team and ultimately the client gets what is intended. It will allow the casting designer the flexibility (even creativity) in satisfying the architectural and structural requirements, but promote productive communication between all parties. Requirements for deliverables including a casting design report, shop drawing submittals, and production documentation (chemical and physical test reports for each cast heat and non-destructive examination reports for each casting produced) are also typically included in the performance specification. The goal of having these deliverables is to allow the casting designer the freedom to develop an economical casting design but to still allow the project architect and engineer to retain control over design intent.
The casting designer will thus be required to engineer the castings to meet these performance requirements and will prepare the required detailed casting specifications and shop drawings for review by the architect and structural engineer. An experienced casting designer typically assumes full engineering responsibility for the castings and may even procure the castings. Remember that foundries obviously have casting expertise but most will not assume design responsibility or assess whether a component they produce is fit for any specific purpose or use. Most foundries won't assist in the production of three-dimensional models or shop drawings, either.
A detailed casting specification prepared by an experienced casting design firm typically covers a number of key items including:
• Foundry qualifications in terms of capability and capacity to produce the type and size of castings being specified
• Quality control and assurance standards for production
• Metal material grade based on industry standards
• Non-destructive examination (NDE) requirements for both the first article and all subsequent production components
• Surface finish quality requirements
• Dimensional tolerances
• Machining requirements (if any) for the finished cast pieces
• Notes on handling and integration of the cast steel elements into the structural steel framing