Structural Steel Cast Connections
A common misconception regarding steel castings is that they are brittle because they are sometimes confused with cast iron. This is not the case in cast steel products which are just as ductile as rolled structural steel products, if not more so. The main difference between standard rolled structural steel shapes and steel castings is the production process which results in their final yield strength. Hot-rolled or cold-formed products attain their yield strength through the rolling or forming processes, whereas steel castings are heat treated after they are cast to attain the desired mechanical properties. In a normalized condition, low alloy steel castings can be readily produced with yield strengths in the range of 30 to 40 kips per square inch (ksi). By introducing quenching and tempering processes, yield strengths of 50 ksi and greater can be attained. In Europe, a process called secondary heat-treatment is now being used to attain yield strengths as high as 150 ksi in castings to be used in special structural applications.
The typical process for the creation of all cast steel products occurs at a metal foundry and is essentially the same regardless of the size or complexity of the casting. The process starts once a particular shape is designed and analyzed for structural integrity. Then a full-size, three-dimensional rigid replica or pattern is made of the component out of cut wood, plastic, or similar material using a computer numerical control (CNC) process. Next, chemically treated sand is placed around the finished pattern in two halves. When the sand has cured and stiffened, the pattern is removed by opening and then re-closing the halves, thus leaving a hollow, stiff sand mold that replicates the pattern exactly. In preparation for casting, the surfaces of the sand mold are treated with a ceramic-based coating. The sand and ceramic coatings are selected by the foundry for their ability to withstand the high temperatures of molten metal.
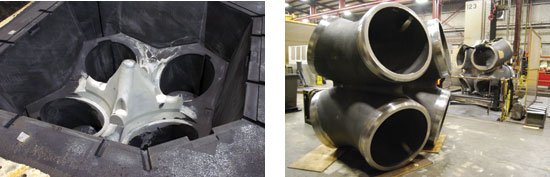
Photos courtesy of CAST CONNEX
Cast steel is formed in a hollow sand mold which receives the molten steel and then is removed to reveal the finished steel product.
With the mold readied and secured in place, the specified metal is heated in a blast furnace until it reaches its molten state. It is then carefully poured into the sand mold and allowed to cool until it solidifies into shape. After the cooling is complete, the casting is removed from the sand mold by breaking away the sand. This means that the mold is destroyed in the process but the original pattern remains which can be reused to make multiple identical molds. Hence the process can be repeated as often as needed to make as many identical products as desired.
Using this common and time proven process, cast metal products are readily produced in virtually any size from very small to very large. Further, the shape and complexity is limited only by the imagination of the designer and the limits of the materials being used. There are of course certain design parameters that make for a better casting than others, but those are fairly well known and understood within the industry. Small, simple cast steel products include things like small cable connectors or cast hardware or decorative elements. Large, complex ones include multi-angle, multi-force custom structural elements for buildings.
Cast Steel Structural Connections
Cast steel has been in use for quite some time in a variety of applications. Railroads use cast steel couplers for connecting freight cars to locomotives. Industrial equipment such as mining trucks use steel castings to make different parts including the entire load bearing frame for improved durability and resistance to impact loads. When it comes to buildings, steel castings have been commonly used for valves and fittings.
The use of cast steel as part of a structural system first occurred in the late 1970s in the construction of offshore oil platforms. These platforms consist of a complex framework of tubular steel members that commonly used welded connections. Problems arise, however, since the structures and their welded member connections are subjected to strong wind and wave action at sea. Given the constant loading and the complexity of the welded joints between the members (anywhere from two to eight members intersect and must be connected to transfer forces) these connections are susceptible to fatigue failure. In response, the concept of a rigid “cast steel node” was developed. This alternative employed casting manufacturing to handle the complex geometry of the junction point thereby smoothing out the stress concentrations in the connection and moving the welded joint away from the region of geometric complexity. Further, the geometric freedom afforded through casting enables thickening the metal where necessary, as opposed to welded fabrication whereby connections are built up from plates. The use of cast steel nodes in this way improves the high-cycle fatigue performance of these connections by more than an order of magnitude. Although these nodes are purely functional, the smooth, more organic, and sweeping appearance of these junctions made them a prime candidate to eventually be applied in architectural construction on land.
One of the first architects to make substantial use of steel castings in the design and construction of an onshore building structure was the firm of Renzo Piano and Richard Rogers. In the mid 1970s they designed the Centre Pompidou in the Beaubourg area of Paris, France. The intentionally exposed structure created a post-modern, high-tech design style with structural steel cast elements used to tie different structural elements and portions together. These castings were used as much for the structural integrity of the building as they were for the desired aesthetic. Since then, cast steel structural connections have become common in architecturally exposed structural steel (AESS) designs throughout Europe. In North America, however, their use has lagged behind primarily due to the historical focus of U.S.-based steel foundries on mass production rather than “jobbing” customized production. However, the recent advent of various standardized cast steel components meant for use in building construction has led to an interest by the U.S. foundry industry to support the architectural community in providing both standardized and custom designed steel castings.
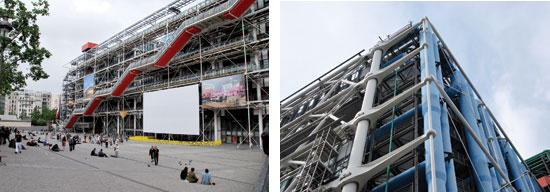
Photos courtesy of Terri Meyer Boake
The Pompideau Centre in Paris, France, was one of the first buildings in Europe to use architecturally exposed structural steel incorporating cast steel components.
Some of the beneficial characteristics of cast steel connections that have been realized in buildings include a dramatic increase in geometric and aesthetic freedom compared to conventionally fabricated connections. Structurally, they provide improved connection stiffness, strength, and fatigue resistance. During construction, they provide simplified fit up, fabrication, and erection. Given all of this, when does it make sense to consider cast steel connections in a building design? Their characteristics make them a preferred choice whenever architecturally exposed structural steel (AESS) is part of the design, particularly if round Hollow Structural Section (HSS) members are the primary structural members being used. They also work quite well for connections in exposed timber frame construction. There are several other building design conditions that also make cast steel connections a preferred choice to solve and simplify loading and connection issues, such as:
• When the building design requires complex connections due to complex geometry (i.e. many members framing together at a single location and/or at sharp angles where weld access would be an issue)
• For heavily loaded connections or when increased connection stiffness is needed
• When material fatigue is a critical connection criterion
• When the connection has to satisfy a special performance requirement, like blast or seismic resistance
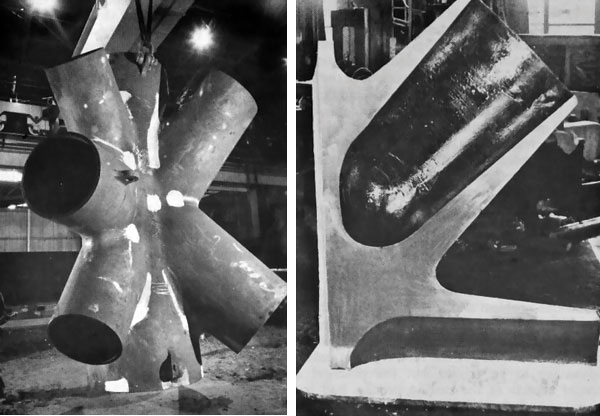
Photos courtesy of CAST CONNEX
The proper design of cast components allows for metal to be thicker or thinner within the piece as structural loading may require.
The analysis and decision on whether or not to use steel castings are best incorporated early on in the design process. Standardized cast connections can be reviewed in consultations between the architect, structural engineer, and a manufacturer's representative. Sizing and selection can often be made from available online or printed literature much the same way as other steel products. However, the building design may give rise to the need for a custom casting if standard ones are not appropriate. Given the specialty nature of such a custom casting design, they are often procured as a design-build item with all parties involved in the process. In this case, specialty casting engineers work directly with the building design team to fully integrate the building design needs with the best practices of casting fabrication. In this way all casting requirements and building design parameters can be properly assessed and accounted for. Such well integrated casting designs not only enable highly unique architecture and connection detailing, but they can also simplify fabrication, improve construction tolerances, ease erection, and thereby lower the overall cost of the installed steel structure.
In the process of reviewing how the cast connections join with the main structural elements, it is important to avoid the misconception that steel castings are not weldable. Again, this comes from incorrectly drawn parallels to cast iron. The reality is that cast steel grades can be selected for any number of mechanical properties, including weldability. In fact, welding is the primary and most common means for joining a cast connection piece to an AESS element since the joint can be ground smooth and finished to appear as a continuous member. In particular, The American Institute of Steel Construction (AISC) publishes standards and guidelines such as AISC 360-10 which lists ASTM A216 Grade WCB as a cast steel grade useful for steel structures. However, there are currently no cast steel grades listed as prequalified base metals in standard welding guidelines so welding procedure specifications must be qualified accordingly. In particular, preheating is required for welding very thick castings and common good welding practices should be exercised.