Flooring: Affecting the Environment from the Ground Up
Learning Objectives:
- Identify and recognize the aesthetic significance of floor surfaces as part of the overall interior design and project documentation of a space.
- Assess the health and safety performance aspects of floor surfaces as they relate to durability, slip resistance, and sustainability.
- Explain the importance of proper subfloor preparation and installation techniques to enhance overall flooring and assembly performance.
- Determine ways to incorporate the principles and topics presented into building design and documentation as evidenced in project case studies.
Credits:
This course is approved as a Structured Course
This course can be self-reported to the AANB, as per their CE Guidelines
Approved for structured learning
Approved for Core Learning
This course can be self-reported to the NLAA
Course may qualify for Learning Hours with NWTAA
Course eligible for OAA Learning Hours
This course is approved as a core course
This course can be self-reported for Learning Units to the Architectural Institute of British Columbia
Flooring of one type or another is used in virtually every building project. Indeed, it may even be a renovation project unto itself. How many square feet of flooring is needed? Likely the same number of square feet as in your building, plus any outdoor deck or activity areas. With such a ubiquitous nature and far-reaching implications for design and construction, it has also been the focus of intense scrutiny in terms of its impact on both indoor and outdoor environments. The flooring industry has responded in recent times by changing the way it sources materials, updating its manufacturing processes, and seeking out and achieving independent, third-party certifications to meet green building standards. In that regard, many now conduct life-cycle assessments (LCAs) on their products to look at the specifics and impacts from the “cradle” or material-sourcing phase through the manufacturing process and then to the “gate” phase, where it is ready to be shipped to a jobsite. Others may look at it all the way to the “grave,” where it is used to the end of its useful service life and then either recycled or disposed of. Based on this process, some also have environmental product declarations (EPDs) available that report the objective findings of the LCAs.
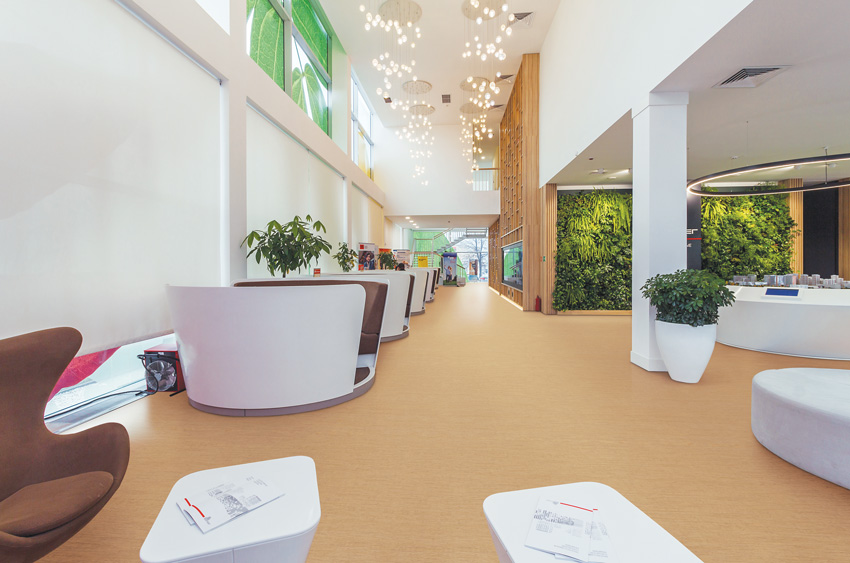
Photo courtesy of Lonseal Flooring
Manufacturing advances now make commercial flooring more appealing, sustainable, and durable over the life of the building in which it is installed.
In this course, we will review some of the different types of indoor and outdoor flooring products and materials that are available for high-performing commercial floor assemblies. In the process, we will look at the ways they each address sustainability and green building principles that allow design and construction professionals to create better performing, better designed, and more sustainable projects.
Sustainable Self-Leveling Underlayments
Any flooring contractor will readily point out that all flooring requires a good subfloor to perform well. Sometimes that is straightforward to achieve in new construction, sometimes not. In renovation projects, the quality of the subfloor may be difficult to determine at best and problematic at worst. Hence, it is common to use an underlayment that can provide an appropriate surface for the flooring and cover over or correct many deficiencies in the subfloor in the process. A common choice for an underlayment over wood and concrete subfloors is a cementitious self-leveling underlayment (SLU) product. While cementitious products tend to carry a very high carbon footprint, some new SLU products have been developed that achieve much more favorable sustainability attributes.
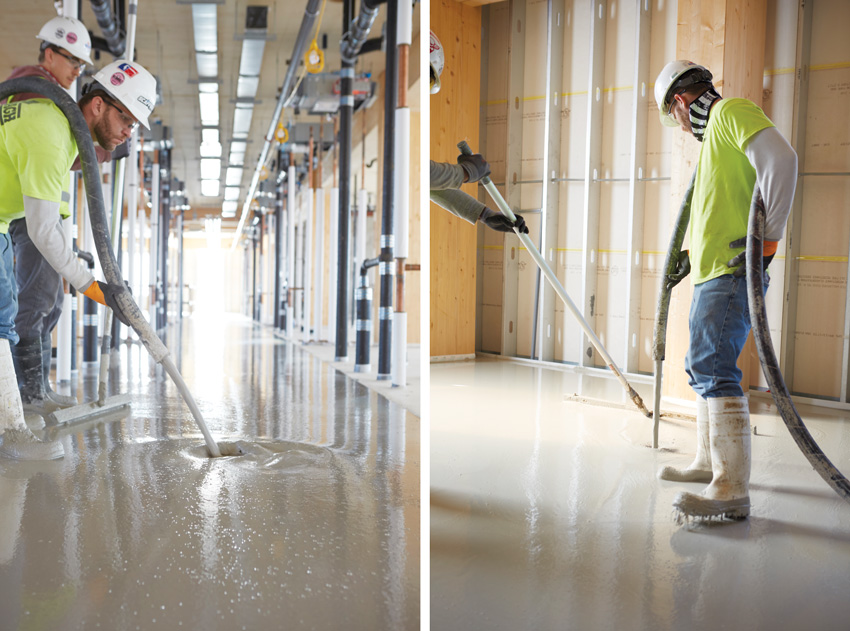
Photos courtesy of USG
Installing a self-leveling underlayment (SLU) helps assure the long-term durability and performance of the finish flooring. Selecting an SLU that has sustainable qualities helps with overall quality of the building.
SLU Overview
SLU products are generally an aqueous mixture of hydraulic cements (i.e., cured with water), fillers, polymeric binders, and additives. The type and amount of cements, chemical additives, as well as the amount of water in the binder are used to control the key properties, such as flow, setting behavior, and compressive strength. The dry product is mixed with water and applied to a subfloor to achieve a smooth surface that is either suitable for use as is or as a substrate for other flooring materials. SLU products are used in both interior and exterior applications and are available both in un-sanded (i.e., sand is added as a filler at the jobsite) and sanded (i.e., no additional sand is required at the jobsite) formulations. There are a range of SLU products that come with a wide variety of performance attributes to suit different jobsite requirements, such as compressive strength, self-healing behavior, working time, setting time, crack resistance, the need for a wear surface, the presence of feathered edges, tolerance for high humidity and moisture, freeze-thaw and salt resistance, etc.
Achieving Sustainability
Traditional SLU products consist of a combination of portland cement and calcium aluminate cement (CAC) as binders, sand and limestone as fillers, and various additives. The sustainability issue with portland cement and calcium aluminate cement is that they are produced using energy-intensive processes. As such, they have a relatively high global warming potential (GWP) value, which is basically a function of two factors: formulation (i.e., inherently high GWP values for cement binders) and transportation (i.e., heavy weight). An understanding of the contributions of each of these factors allows for selecting a self-leveling underlayment that has a reduced GWP.
The following table illustrates the GWP impacts of these two cements compared to other options. Note that the values used in the graph represent approximate cradle-to-gate GWP impacts. They are for illustrative purposes only and will vary depending on the LCA process followed. Flue-gas desulfurization (FGD) stucco refers to FGD gypsum that has been calcined so that it has setting properties.
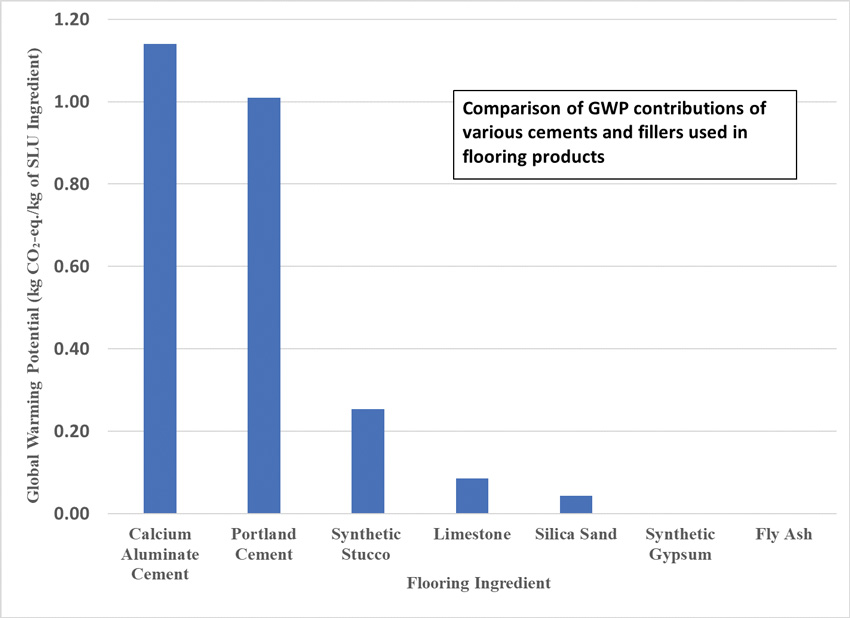
Image courtesy of USG
The GWP value for each of the materials shown above represents the amount of greenhouse gas (i.e., kilogram CO2-eq.) emitted during the cradle-to-gate production of 1 kilogram of that SLU ingredient. Using an FGD gypsum-based SLU instead of a traditional SLU that utilizes CAC saves the equivalent of approximately 52 gallons of gas per ton (907 kilograms) of SLU. A value of 10 kilogram CO2-eq. is roughly equivalent to using 1 gallon of gasoline or driving 25 miles by passenger car.4
The key to minimizing the GWP impact of any self-leveling underlayment product is to first inspect the EPD, which should be readily available from the manufacturers. When scrutinizing EPD documents for comparisons, be sure that the results are based on the same functional unit. Also recognize that one way of lessening impact on GWP is to use an un-sanded SLU product versus a pre-sanded one since this removes the impact of transporting sand across the country by truck and instead uses locally derived sand. This relatively simple difference can result in a potential GWP savings of approximately 20 percent with no change in the final properties of the installed product.1
A second means of lowering the GWP impact is to utilize products produced with FGD gypsum rather than with natural mined gypsum. FGD gypsum is derived from flue gas desulfurization during electricity generation from coal. Since it is a waste product, it is treated as having no GWP contribution other than that required to transport it from the power plant to the manufacturer and processing it for manufacturing. Using FGD gypsum as a raw material in the self-leveling underlayment product eliminates the need to mine an equivalent weight of gypsum from the ground.
Finally, at least one manufacturer uses an innovative, alternate cement formulation instead of traditional portland cement. This alternative is geopolymer cements, which are based on the reaction between fly ash, a waste product of burning coal for electricity generation, and chemical activators. As a waste product, fly ash does not contribute to the GWP of the flooring product. While this basic chemistry has been around since the 1970s, it is now being used in place of portland cement in self-leveling underlayment products. Using a geopolymer cement-based product compared to a portland cement-based product can reduce the overall GWP for a self-leveling underlayment by as much as 70 percent.2
The demand for SLUs with lower GWP and product-specific EPDs is being increasingly fueled by voluntary programs such as LEED v4.1 and others. Mandatory programs such as California’s law AB 262 known as the Buy Clean California Act requires state agencies to consider the embedded carbon emissions of industrial products.3 Preferential treatment is given to products that demonstrate reduced GWP values compared to a standard industry GWP value. Similar legislation is being pursued elsewhere and it is expected that this trend toward lower GWP products will continue, with additional building products added to the list of those targeted for a reduction in GWP.
More Sustainable Resilient Flooring
A very popular commercial flooring type is resilient floor coverings, which include sheet vinyl, vinyl tile, rubber, polymeric, and linoleum products. Architects and interior designers recognize resilient vinyl flooring in particular as a durable material for high-traffic areas or areas that need to be kept meticulously clean, such as health-care settings. Resilient vinyl flooring has become more favorable over the years in commercial spaces and is being specified in more settings due to updated design and material modifications for quality, high-performance, and more sustainable products. Some of the features that lead architects and interior designers to vinyl flooring are its ability to “bounce back” from the weight of objects compressing its surface; it is also better acoustically and more comfortable underfoot than some options. In addition, the durability, ease of maintenance, and moisture resistance contributes to its increased demand, particularly by building owners and managers.
Sustainability Standards
The Resilient Flooring Covering Institute (RFCI) is the not-for-profit trade association that has been at the forefront of helping manufacturers identify and advance the sustainability of resilient flooring products. In 2007, RFCI introduced a draft standard for trial use that addresses sustainable resilient flooring products in conjunction with NSF International, a not-for-profit, nongovernmental organization focused on public health and safety. The draft standard, known as American National Standard for Trial Use – NSF 332 – Sustainability Assessment Standard for Resilient Floor Coverings, is designed to help manufacturers of sustainable resilient flooring products demonstrate their commitment to the principles of sustainability.
RFCI, in conjunction with resilient flooring manufacturers, has also facilitated third-party-certified EPDs for resilient flooring. The EPDs report the industry average data for five product types based on LCAs following the flooring industry’s product category rules (PCR). Using all of this as a basis, RFCI has also developed its own FloorScore IAQ Certification program related to indoor air quality, particularly the emission level of specific volatile organic compounds (VOCs). For a resilient flooring product to receive FloorScore IAQ Certification, it must be independently certified by SCS, an internationally recognized third-party evaluation, testing, and certification organization. Certified products comply with the VOC emissions testing criteria of the California Specification 01350: California Standard Method for the Testing and Evaluation of Volatile Organic Chemical Emissions from Indoor Sources Using Environmental Chambers, Version 1.2. Under this method, SCS 1) reviews all VOC emissions test reports for particular products generated by independent testing laboratories; 2) determines whether those test results meet the California Specification 01350 requirements for listed VOCs; and 3) conducts periodic manufacturing plant inspections to review product formulas, processing, and quality control to ensure the continuing integrity of the FloorScore seal.
Notice
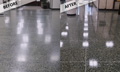
www.adsil.com
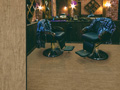
www.lonseal.com
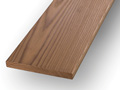
www.thermoryusa.com
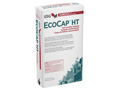