Life-Cycle Assessments for Appliances
Impact Categories
In an ISO-compliant LCA, environmental impacts are broken out and organized into different specific impact categories to describe the effects during a product's life cycle (or individual phases) on specific areas of concern. These impact categories include things like fossil fuel depletion (embodied energy), global warming (carbon footprint), water depletion, metal depletion, and various air pollution impacts. The ISO standard requires that specific environmental impact categories must be measured and included in the LCA and subsequently reported on. Other categories can be added beyond these basic minimums. (See sidebar “Common Impact Categories for Appliances” on the previous page.)
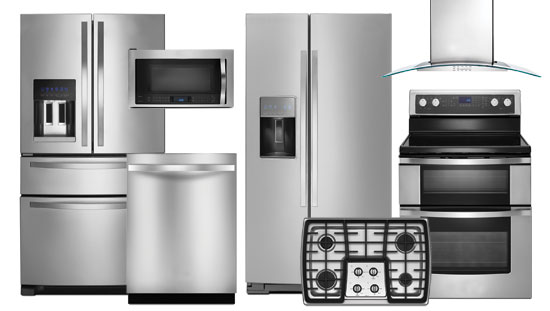
Images courtesy of Whirlpool Corporation
The use of LCA allows appliance manufacturers to assess their existing line of appliances and determine where to make improvements that reduce environmental impacts.
Product Category Rules (PCR)
A product category rule (PCR) is relevant only to a specific type of product or material meaning it is written for all products/materials within its category (i.e. roofing or flooring or appliances, etc.). With a PCR in place, the method for conducting and reporting the results of an LCA in an EPD is standardized for products within the category. This ensures that all products in a certain product category, regardless of manufacturer, are measured the same way in each life-cycle phase. The PCR defines the specific impact categories that must be addressed and determines the common functional units of measurement (e.g. square feet, BTUs, tons, etc.) so direct comparisons can be made between individual products. To be in compliance with the ISO standards, all impacted stakeholders must have an opportunity to participate in the development of the PCRs. At present, there is not a large number of PCRs since they can be expensive and time consuming to develop. However, this is starting to change, and more PCRs are being developed each year for different categories of building materials and products including some for specific appliances.
Environmental Product Declaration (EPD)
The ISO acknowledges an Environmental Label as a “claim which indicates the environmental aspects of a product or service.” It goes on to clarify that an environmental label or declaration may take the form of a statement, symbol, or graphic on a product or package label, in product literature, in technical bulletins, in advertising, or in publicity, among other things. In practice, EPDs are published by the product manufacturers, usually as a summary document for each product or class of products they are making a declaration about.
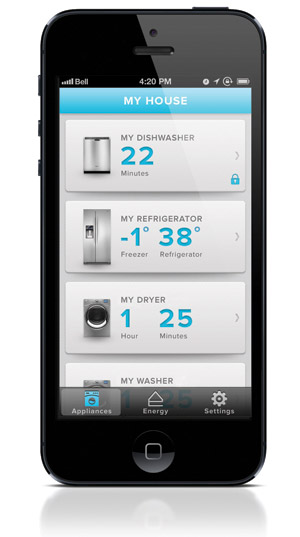
Image courtesy of Whirlpool Corporation
To help consumers optimize the energy their appliances use, some appliances have smart phone apps that control the duration and the time that appliances run.
Once the LCA for a product or class of products is completed following ISO 14044, other ISO documents take over for the EPD preparation. There are standards for three types of EPDs: Type I prepared by independent third parties; Type II, which are self-proclaimed; and Type III prepared by a program operator. A program operator can be a company or a group of companies, industrial sector or trade association, public authorities or agencies, or an independent scientific body or other organization. In most cases it is a Type III EPD that is prepared, hence ISO 14025 is the primary standard used since it establishes the principles and specifies the procedures for developing both the specific programs and the actual declaration documents for Type III environmental declarations. Type III environmental declarations are primarily intended for use in business-to-business communication, but their use in business-to-consumer communication under certain conditions is not precluded. The document specifically establishes the use of the ISO 14040 series of standards related to LCA as the basis for Type III environmental declarations. The series also references other ISO standards including ISO 14020, which defines general principles of all EPDs of all types.
When completed, a standardized EPD is the ultimate outcome of an ISO 14044-compliant life-cycle assessment for a particular product following the appropriate PCRs. In essence, it summarizes all of the basic materials and processes required over the life cycle of that product, from raw material extraction, through manufacturing, transport, use, and end of service life recycling or disposal.
An EPD presents the summary of the quantified environmental data for products or systems. EPDs are voluntarily developed by manufacturers or trade associations, but since they are typically verified, at least in part, by independent third parties, their purpose is to provide reliable and comparable information regarding the environmental performance of similar products in a product category. EPDs enable architects, building owners, and other members of the design team to make direct comparisons of the environmental attributes—such as carbon footprint and embodied energy—of similar products. Hence, products can be assessed when they may have the same traditional attributes (e.g. performance, cost) but need to be selected and specified based on minimizing negative environmental impacts. EPDs are used often for comparison of two (or more) products to determine where the differences lie in the product or the process of its life cycle.
When it comes to reporting impact categories in the EPDs, ISO 14025 requires eight categories at a minimum with the PCRs defining additional impact categories, if any, that must be included. Of course, EPDs can always report more impact categories than required by the PCR. Architects should consider which impact categories are of greatest interest for their projects. For instance, while carbon footprint is likely always a concern, in the arid Southwest, impact on water resources might be of particular concern.
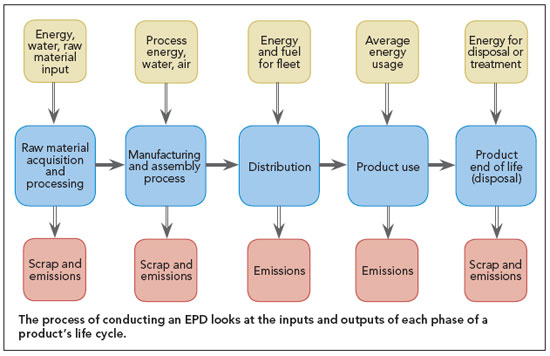
Image courtesy of Whirlpool Corporation
All across the United States, there has been increased interest in EPDs with some of the attention being driven by federal agencies, such as the General Services Administration (GSA), to potentially use EPDs as a vehicle to comply with Executive Order 13514 requiring government agencies to purchase environmentally preferable products. The U.S. Green Building Council (USGBC) has also incorporated EPDs as a part of the LEED version 4 green building rating system in the Materials and Resources (MR) section, which has been substantially revised. Points that were previously available for regional materials and recycled content are being rolled into the points available for LCAs and EPDs. Happily, the USGBC is not asking project design teams to conduct LCAs or to become product and material experts. Instead, the project team will be able to request an EPD (or perhaps another approved form of reporting) that discloses the required LCA-based information. In essence, LEED version 4 will ask product manufacturers to gather the life-cycle information on their products and to disclose relevant portions of that information in the standard EPD format. The new relevant credits are anticipated to affect four out of the five MR credits beyond the prerequisites and earn up to 11 points in the process.
Clearly, EPDs are seen as an important validation tool that allows manufacturers to objectively assess the environmental sustainability of their products, while providing buyers with clear and credible information necessary to make product comparisons. In addition, buyers and product specifiers are increasingly demanding transparent data that supports claims of the environmental sustainability of the products they select, ensuring a growing demand for EPD-backed products. In the increasingly competitive marketplace for environmentally sustainable solutions, EPD-backed products better enable specifiers and buyers to make objective and informed purchasing decisions. Finally, manufacturers who use EPDs help to create a greater public awareness of the environmental impact aspects of products, thereby contributing to global sustainability efforts.
When it comes to appliances, the LCAs and EPDs are currently most widely done to assess existing products. While using LCAs for comparison purposes are useful, the real reason manufacturers complete them is to make improvements in their products. Typically, the results are used internally to quantify the environmental impacts of the products and help to guide product development or materials decisions. LCA results can also be used to assess the environmental footprint of a product over time and to support marketing claims for products. It is important to remember that LCA is a complex modeling tool that has to rely on the best possible data available to provide a good estimate of impacts. Nonetheless, becoming aware of where the biggest environmental impacts in a product's life cycle exist gives manufacturers clear direction for making important changes to reduce those impacts.