Designing for Durability
Termite Control
Insects, mainly termites, carpenter ants, and powder post beetles, can cause significant property damage, including (though not limited to) wood-frame structures or wood- or cellulose-based components. Of the offending insects, subterranean termites cause the most damage, particularly the non-native species known as the Formosan subterranean termite. Though found only in the southern United States, it is responsible for most of the value loss due to insect damage in that area. With proper design and detailing, good construction practices, and ongoing maintenance, wood-frame buildings can be as termite-resistant and durable as buildings made from other materials, according to the WoodWorks Wood Products Council technical guide, “Effective Termite Protection for Multi-Family & Commercial Wood Buildings.” Regardless of building material selected, approaches to subterranean termite prevention must be planned. With proper planning and design from a pest control specialist, effective pest management does not have to be onerous or cost prohibitive. The current thinking is that total eradication of termites from certain areas is unfeasible, and a more realistic approach involves containing existing insect populations and limiting risk to buildings. As with the moisture control strategies described above, the strategy for combating termites is based on the assumption that none of the following measures are 100percent effective on their own, but, in combination, create conditions where the risk is negligible. Where termites pose a risk, it is good practice for the general contractor to engage a pest control specialist during pre-construction to map out an appropriate plan.
The "Six-S" strategy includes the following lines of defense:
Suppression: This involves reducing termite populations in a particular area and preventing their spread to new areas. An “area” can range from an entire state (though usually only if the termite is a recent introduction and still has limited distribution) to a single home. Methods of suppression include locating and destroying termite colonies, burning infested wood, and heat-treating reclaimed lumber.
Site management: Proper site management begins before clearing and continues through construction. Management steps include (insert citation here):
- Removal of stumps, roots and any untreated wood. Stumps provide food and shelter for colonies and roots offer pathways underground that could lead termites to the structure.
- Covering and wrapping construction materials that are stored on site, making sure to keep non-treated wood a minimum of 6-8 inches away from soil.
- Removal of concrete form boards and disposal off site.
- Removal of offcuts and other wood construction debris on a regular basis, including debris in CMU block cells if being used.
- Draining water away from the building at a slope of 5% per 10 feet.
- Prohibiting use of excavation spoil under wood-frame elements.
- Prohibiting storage of cellulose-based materials such as wood or cardboard in the crawlspaces.
- Closing the building in as soon as possible.
Post-construction, once landscaping is complete, another check should be done to make sure the required clearances have been maintained.
Soil barriers: Treating the soil is a popular and cost-effective option for protecting against conditions that lead to termite damage, especially in states like Louisiana and Florida where termites are a major issue. Initial treatment is applied before work begins on the slab, or on footings, in the case of a crawlspace.
Per guidance from WoodWorks (insert citation here), the site is treated with termiticides according to the product label—e.g., 1 gallon per 10 square feet—focusing on the soil in and around the excavated area where the slab will be poured, and pipe beddings. Labels often refer to “treated zones,” which may be continuous, creating a barrier between the soil and structure.
As with all termite-prevention tactics, there are limitations to soil termiticide treatment and it is vital to follow label instructions and requirements for maintenance. For example, the efficiency of a soil barrier depends on soil type and other factors, foundation drains could make it difficult to apply the treatment, and treatments should not be used near a well or cistern unless the soil is excavated, treated and replaced.
After the slab is poured and the form boards have been removed, termiticides can be applied vertically to the soil against the foundation walls. However, concrete overpour or mortar that’s accumulated along the exterior foundation perimeter should be removed before treatment.
Another treatment may be applied around the outside foundation wall once landscaping is complete. In most jurisdictions, a pest management professional is required to issue a certificate of compliance to the building department following treatment.
Although pest companies are well-versed in termite control, the GC is also expected to be aware of the requirements, particularly in relation to avoiding displacement of the chemical termiticide. For example, the Florida Building Code includes several requirements for avoiding displacement of the chemical termiticide after soil treatments.
Physical Barriers: Installed during construction, physical barriers are intended to prevent termites from accessing a structure unseen. To breach the barriers, termites are forced to build their shelter tubes above ground, making it easy to detect and remove threats.
Physical barriers are less common and more costly than chemical barriers, and add a degree of difficulty to the construction process. However, they offer an effective, environmentally-friendly option. The use of physical barriers and other non-toxic approaches may make the project eligible for credit under a government green building program or rating system such as LEED. (insert citation here) Information on barriers courtesy of WoodWorks. For further reading and resources, visit https://www.woodworks.orgMarine grade stainless steel mesh screens - With apertures smaller than 0.02 inches can be installed under the foundation, at the base of wall systems, under sill plates, around expansion joints and pipes, at perimeter wall junctions, on crawl space vents, or at any juncture where there may be openings that allow termites to pass from soil to structure. For example, mesh can be fixed to service pipes that will extend through the concrete slab before the slab is poured, preventing even the tiniest gap. Mesh can be embedded into concrete, fixed to the concrete slab, or fixed to pipes. Particle barriers - Usually made from sand or rock, are effective when the particles are too close together for termites to pass through, and too large for them to move out of the way. Since native subterranean and Formosan termites are different sizes, the particles must be tailored to the species found where the barrier is being used. A single size won’t be effective where both species are present. Although not common, particle barriers can be used on the exposed perimeter of buildings where the soil meets vertical concrete, in openings for bathtub plumbing (a favorite entry point for Formosans), and around other plumbing penetrations.
Geotextile membranes - Come in a variety of configurations to protect various parts of a structure. Under-slab sheets include 8.5 mils of high-strength cross-laminated polyethylene backing topped with a 69-mil-thick layer of barrier sealant integrated into a high strength non-woven geotextile fabric. Peel-and-stick barriers, which come in large sheets or a variety of roll widths, consist of a 4-mil-high density polyethylene film bonded to 36 mils of sealant. (insert citation here) When termite-resistant materials are used, an air barrier can also serve as a termite barrier. However, continuity is essential. Small deficiencies that don’t pose much risk in terms of air tightness may still pose a risk for termites. Execution is key to effectiveness. A barrier that is poorly installed, damaged, buried by improper grading, or otherwise changed may not be effective.
Slab and foundation details: Slabs and foundation walls should be designed to inhibit the entry of termites into the building and to facilitate inspection for termite shelter tubes. If hollow concrete masonry units (CMUs) or double walls are used in foundations, they must be capped with concrete or masonry to eliminate holes. All exterior slab edges or foundation walls must be kept free of cladding for a height of 6 inches from the finished soil level to allow inspection for shelter tubes. This separation of cladding from the ground must allow for any landscaping to be done immediately after construction or likely in the future.
It’s important to note that there should be no contact between the building woodwork and the soil or fill material. For best results, exterior woodwork should be at least 6 inches above ground and any wood in contact with or adjacent to the soil should be preservative treated.11 (For more details, see the section on code requirements below.)
Structural protection: For many decades, preservative-treated framing has been successfully used to deter termites. These days, wood products can be treated with borate (disodium octoborate, sometimes expressed by its oxide B2O3), a water-soluble chemical that is benign to humans, but kills insects that feed on it. Borates are used in many common household products, from eye drops to washing powder. Borate-treated products—from dimension lumber to plywood, OSB, and cellulose insulation—are enabling termite-resistant structures. While suitable for framing and sheathing, borate-treated wood should not be used for outdoor applications, such as decks and porches, since the chemicals are water-soluble. A good quality coating, such as a three-coat film-forming finish, prevents the borate from moving out of the wood. Architects should consult the American Wood Protection Association (AWPA) standards for borate and other preservative treatments under specific conditions and types of termites.12
Preservative treatments can either be pressurized or non-pressurized. With pressure treatments, combinations of pressure and vacuum achieve a deep, thorough chemical penetration by infusing the wood cells with preservatives. Pressure-treatment preservatives consist of chemicals in either a water or an oil solvent: odorless water-borne options are more popular, as they achieve a paintable or stainable clean wood surface. Depending on local codes, several types of wood preservatives may be used. With non-pressure treatments, the preservative can be applied via brushing, spraying, or dipping of the wood member. Spray application of borates at the framing stage is recognized as an effective termite protection measure by some codes. For information on preservative-treated and naturally durable species, see the section on code requirements.
Surveillance and remediation: To ensure effectiveness of the management strategies discussed above, regular inspections are necessary. Baiting may be used to detect the presence of termites. Tubes or traps holding pieces of untreated lumber, or “bait”, are placed around the building. Termites feed on the bait, which can then be replaced with treated lumber that contains a slow-acting chemical that the insects bring back to the colony. Over a period of time, the colony is destroyed. The original untreated bait can then be restored to the traps to determine whether there are any remaining termites. Alternatively, the infested building can undergo either chemical fumigation or heat treatment, the former having the obvious disadvantage of toxicity and the necessity of evacuation for several days.
Both types of remediation must be done by licensed contractors and, while they will eradicate the termites, they do not protect against re-infestation. Vigilant monitoring is key to identifying sources of food and moisture, including leaks in downspouts or gutters, air conditioners, pipes, window or door seals, and poorly ventilated bathrooms. The type of action taken against termite colonies will vary widely depending on the type of termite, location, and condition of the building.
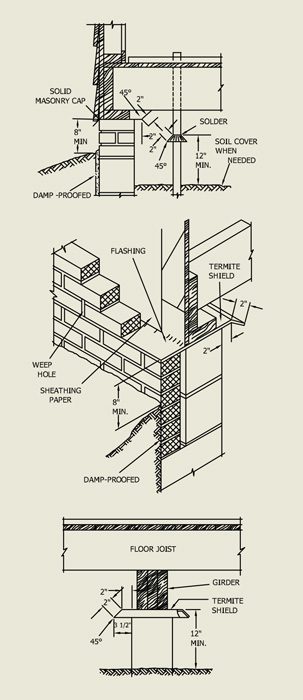
Image courtesy of the American Wood Council
Installing termite shields has proven to be an effective means of control.
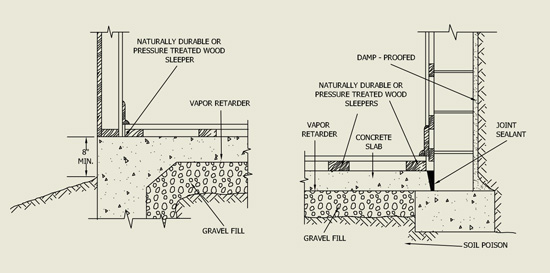
Image courtesy of the American Wood Council
An example of termite control for slab-on-ground construction.