Connection Solutions for Modern Wood Buildings
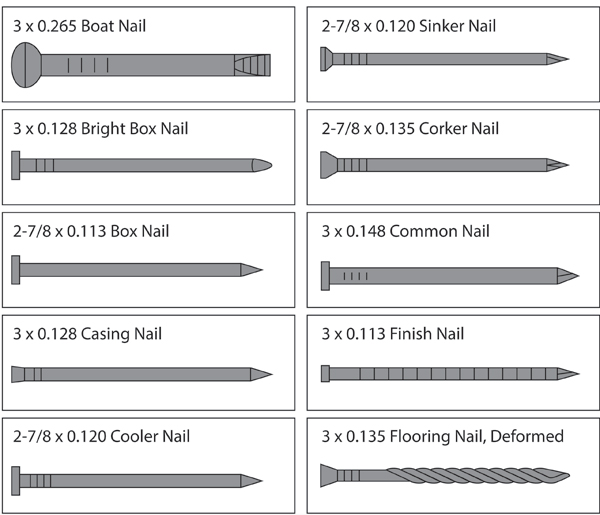
This chart shows 10 nails, all referred to as 10d, and each with potentially different performance characteristics. Thus, specifying a 10d nail is not clear.
▶ Nails come in many types (e.g., box nail, common nail, rink shank, sinker, cooler), as well as multiple pennyweights (the NDS tabulates 6d to 60d). There are also proprietary nails unique to specific manufacturers.
For flooring, APA – The Engineered Wood Association recommends using a glued-nailed system, as described in the Engineered Wood Construction Guide. In this system, glue is used to attach sheathing to the substrate member, whether lumber or an I-joist, to minimize squeaks and increase stiffness due to T-beam action. All nailing must be completed before glue sets. Gluing is not recommended for bonding wall or roof sheathing to framing because it leads to reduced ductility. This approach is actually prohibited in high seismic zones.
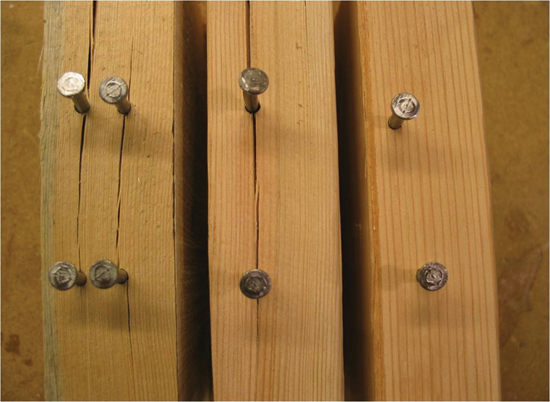
Photo: American Wood Council
Nail spacing is important. If splitting occurs, it will always occur parallel to the grain and not perpendicular to grain, no matter how close the nails are spaced along this axis. Staggering a line of nails when closely spaced, minimizes potential splitting along the length of the member. In a tightly nailed shear wall, staggered nailing helps prevent splitting of framing members and allows higher loads to be transferred.
▶ Bolt design values are tabulated in the NDS for five diameters (1/2 in., 5/8 in., 3/4 in., 7/8 in. and 1 in.). Diameters greater than 1 in. are not permitted as they can initiate localized stresses in the wood member, which can cause splitting or other brittle wood failures. Bolts are inserted in pre-drilled holes 1/32 in. to 1/16 in. larger than the bolt diameter. A common mistake is not leaving enough room for installation of nuts or tightening with a wrench or other torque device.
▶ Lag screws are typically used when it isn't possible to use a nut as required for bolts or when withdrawal capacity is required. They are inserted into pre-drilled holes. The clearance hole for the shank (unthreaded portion of the lag screw) should be the same diameter as the shank, while the lead hole for the threaded portion is a variable percentage of the shank diameter based on the wood's specific gravity. Because lag screws can be fully threaded, the NDS assumes fairly conservative design values which are based on the smaller “root” diameter of the fastener. Higher lateral capacities for lag screws can be calculated if the designer can ensure the threads are far enough from the shear plane. For more information, see the American Wood Council (AWC) publication, Application of Technical Report 12 for Lag Screw Connections, Design Aid No. 1.
▶ Timber rivets are high-strength steel nails typically hot-dipped galvanized, with a flattened oval shank section and a wedge-shaped head. When driven through the pre-drilled steel plate and into the timber, the tapered heads wedge tightly in the holes. Rivets must be driven with the long axis parallel to the wood grain. An excellent way to spread the load with multiple fasteners, they can be used as an alternate to a large number of bolts, resulting in a connection with greater ductility and resilience.
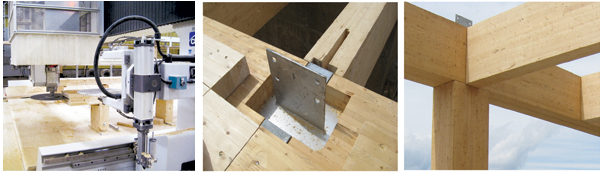
Modern Computer Numerically Controlled (CNC) connections provide the ability to fabricate joints with precision. This is especially useful when fabricating joints on large members with complex shapes.
Metal connector plates with integral teeth partially penetrate the wood members and are used primarily with fabricated lightweight wood trusses. With these connections, loads are transferred near the surface of the wood member.
Shear connectors, sometimes referred to as bearing connectors, are typically used to accommodate heavier loads. They include split rings, shear plates and toothed shear plates. They are usually made from cast iron or light metals, and are capable of transmitting the load relying solely on bearing and shear resistance of the wood in the direction parallel or perpendicular to the grain. They can be used to connect wood to wood members or wood to steel, and may be concealed or visible.
Profiled using special machining tools, split rings are usually fitted in a circular groove on the meeting side of the timber members. The split in the steel rings allows the gap in the ring to close or open if the wood members shrink or swell to ensure that the wood members and split ring remain in contact. A bolt is installed through the center to hold the joint assembly together. In connections with shear plates, grooves must be precision machined with special tools, which recess the wood so the shear plates sit flush with the surface. Typically, shear plates and split ring connections have brittle wood failure modes and should be avoided in structures located in high seismic regions unless the designer employs elastic seismic design.
Proprietary connections. Some of the most innovative connection systems are proprietary—that is, produced exclusively by one manufacturer or designed specifically for one building. This area has seen considerable growth in recent years, with connection systems and products developed for use in larger and more complex buildings being designed to take advantage of wood's economic, aesthetic and environmental benefits.
Custom-fabricated structural framing connections, for instance, provide a single-piece connection between two framing members. They generally consist of bent or welded steel, carrying load from the supported member (through direct bearing) into the supporting member (by hanger flange bearing, fastener shear or a combination of the two).
Pre-engineered metal connectors are commonly used in all types of wood construction. Traditional fasteners like nails, bolts and rivets, as well as generic types of pre-engineered metal connectors such as metal hangers, are reliable and widely used, but have some limitations in large, multi-story buildings that newer proprietary systems are designed to overcome. Newer systems, for example, are often concealed, which makes them fire-resistant if they are sufficiently below the wood surface. They can be designed for use in multiples without reducing the strength of the wood, and they can be designed to be either stiffer or more flexible, depending on the application.
One example of a proprietary product that's becoming widely used—especially in cross laminated timber (CLT) and glulam structures (see sidebar on page 5)—is the self-tapping or self-drilling screw. A number of manufacturers in North America, Europe and Japan produce them with different features and in many shapes and sizes. They have enhanced hardness for higher lateral load capacity, and come in various capacities for different applications. The main advantage is that they can be driven into wood without pilot holes, using a regular handheld power drill. This lessens the risk of mistakes in the field and improves efficiency and reliability.
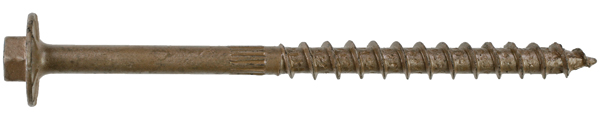
Photo: Simpson Strong-Tie
Self-drilling screws have a drill-shaped point to cut through substrate and eliminate the need to drill a pilot hole.
Pre-engineered connectors are manufactured by component manufacturers, which have exhaustive catalogues of products that suit various applications. Categories, in addition to the ones previously mentioned, include framing anchors, hold-down devices, straps and ties. Many components are fabricated using formed sheet metal, increasing in thickness as loads increase. Specific nailing and fastening requirements are provided by the manufacturers and must be rigorously followed to develop full connection capacity.
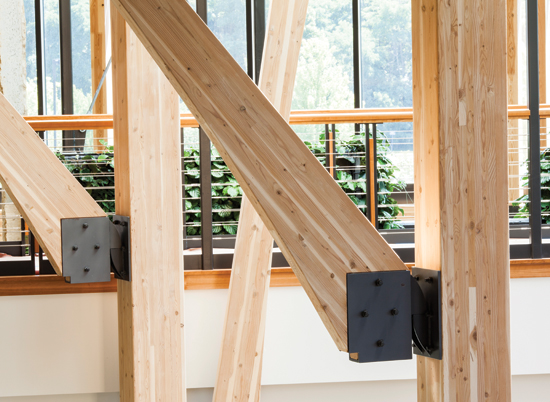
Photo: C&N Photography, courtesy of Uihlein/Wilson Architects
The 52,000-sq-ft client and staff center at the Promega Feynman Center has virtually no square angles, which made beam-to-column connections a challenge. To avoid the need for more than 100 different configurations, a steel pin connector was designed that allows up to 10 degrees rotation in either direction.
Reference design values for mechanical connections are provided in various sources. The NDS contains reference design values for dowel-type connections such as nails, bolts, lag screws, wood screws, split rings, shear plates, drift bolts, drift pins and timber rivets. Design values for proprietary connectors are provided in code evaluation reports.