Gaining Urban Space: Platforms Over Rail Yards
“You’re trying to figure out how to land the building, and the structural load, to the ground, to terra firma, and the transfer truss ends up being the most efficient way to do that,” he says.
Essentially, the structural engineers are dealing with a set of support points coming up from the foundation and the building coming down on top of that. “You’ve got to figure out how to marry the structure loads coming down and support them, and the transfer truss is what accomplishes this,” Robbins adds.
To do this in the most economical way, engineers try to minimize the span between those touchdown points. Alternatively, if the spans get too large, the design will not be economically feasible.
That said, for Hudson Yards, there are points below the 10-story retail complex where trusses had to span lengths are long as 155 feet and support uniform loads of nearly 4,500 pst. “The trusses required close architectural mechanical and structural coordination to maximize the structure, achieve a usable space, and fit the required systems into them,” Gottlieb explains.
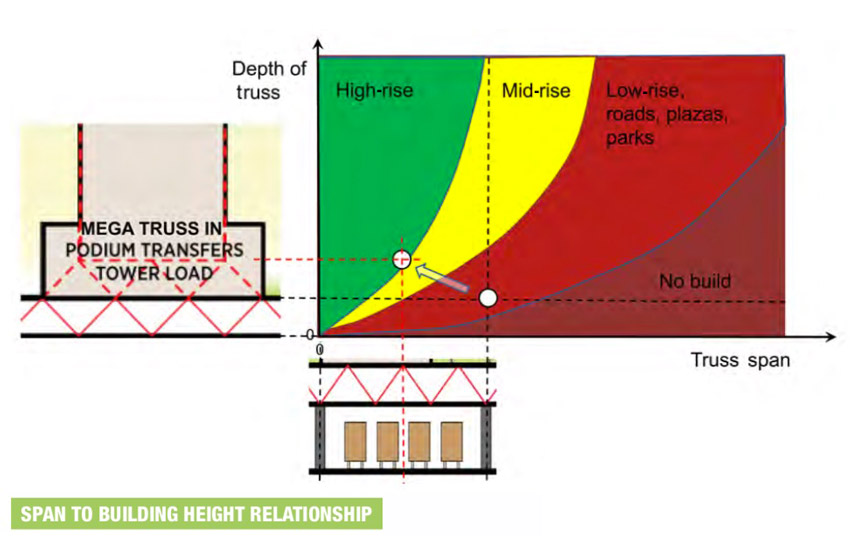
Image courtesy of Sunnyside Yard Feasibility Study
Truss depth increases in relation to the height of the buildings.
While these mega-trusses do solve the challenge of dealing with large spans, it should be noted that their diagonal structural members need to cut through the building core, which makes the space in the podium of the building a little less useable. For example, within Hudson Yard’s retail complex, the truss is installed between floors one and three, and it does take up a portion of the real estate.
Sharing some more details about the truss design, these elements were sized based on erection weight and crane capacity, and many were designed as two side-by-side trusses, which were tied together after erection. “Had a single truss been used, it would have been too heavy to lift over the railroad tracks,” Flynn says. “By splitting the trusses, we could erect one truss at a time and tie them together later. This minimized the impacts to the railroad below.”
The stable box truss assembly formed by these double trusses supported a fast, lightweight installation of precast planks to cover the tracks.
“The trusses were each installed during a 2-hour window once a week in the afternoon over the tracks, allowing all the trusses to be installed in a six-week period, covering half the yard and all the complex switching tracks,” Gottlieb says.
As noted, the structure had to be fully optimized so that all the structural elements could be fitted to the architectural design and the limited dimensional volumes but without using any additional material that would drive up pick weights for the cranes. “Minimizing weight was critical to allow the cranes to efficiently erect the project and minimize crane positions for the project,” Gottlieb adds.
Complex Coordination
While a sophisticated level of engineering and architectural design goes into these platform projects, one of the most challenging aspects is the extremely high level of coordination required. Projects of this nature are highly interdisciplinary; transit companies, engineers, architects, cost estimators, financial modelers, urban designers, and municipal officials must all work together.
“These projects cannot be built efficiently without full dedication and collaboration of the private and public entities involved,” Estevez says.
As opposed to a greenfield project, the notion of coordinating construction with ongoing train operations, yard underground activities, security, ventilation, etc. is a daunting task. “To tackle these challenges [for Hudson Yards], our structural engineering team worked closely with around 20 different consultants representing various engineering fields as well as contractors and clients,” says Silvian Marcus, F.ASCE, director of building structures, WSP, New York. “To add to this mix, every step of design had to pass a rigorous review by city authorities, railroad authorities, police and fire departments, etc.”
Just the issue of taking trains out of commission during construction alone is a difficult and costly endeavor. For example, at Hudson Yards, in areas where the train tracks were straight, the team could take four adjacent tracks out of service at a time, allowing drills and other equipment could be left in place. However, in some areas with switches where trains change tracks, the team was permitted to drill a caisson for only 2 hours each night.
Similarly, the erection and stabilization of steel members could often only proceed within in limited time frames. “These time windows ranged from 20 to 90 minutes, depending on the number and location of tracks affected,” reports Flynn.
Furthermore, the cranes had to be located in “off-track areas,” which increased the distance from the crane to the final location of the piece being erected and made the use of very large cranes necessary.
“We used the largest cranes that were available and then needed to configure the steel members so their weight was within the crane capacity,” he explains. “This led to the side-by-side steel truss concept and also the location of field splices in the laminated steel columns.”
Another challenging issue with these platform projects is the fact that developers are working with a transit company whose primary job is to make the trains run. “They’re not developers, they’re not urban planners,” Robbins explains. “There can be some individuals within the organization who have the vision to see that if you do an overbuild, it can help fund rail operations, but it’s not how these transit companies are used to thinking or doing business, so that’s a paradigm shift for them.”
Project Process
In terms of how to best execute these complex projects, Flynn explains that the first step is addressing the big picture, discussing project needs, and evaluating the ability of the railroad to tolerate some disruption and maintain the necessary level of service.
Before starting the design, the team must collect as much existing information about the existing underground facilities as possible.
If information is limited or unavailable, then an attempt is made to conduct a survey. This survey can be visual for above-ground utilities, or it may use ground-penetrating radar or X-ray techniques for underground utilities.
At Hudson Yards, a detailed 3-D BIM model was developed following a comprehensive study of all existing conditions. The model then served as part of the preliminary design, also helping the project team to determine what items needed to be field-verified.
“The schematics need to be presented early to the operations division of the public entities to assure that the work is feasible and the best solution for the project,” Estevez says. “Subsequent design development and construction documentation needs to be created with collaboration from all entities.”
The building team must also develop a detailed understanding of train operations, as working with preexisting conditions and active train lines is a delicate balancing act. For example, the team could be dealing with an underground foundation and column directly above it.
“Often, due to tight track layout and multiple underground conduits and utilities, individual footings literally have to be carved out to allow for passage of these conduits,” Gurevich explains. “Columns above sometimes must be shaped to accommodate curved train clearance outline and other limitations.”
In terms of ensuring access during these tight time windows, close coordination with the railroad staff is essential. To best enable this, Flynn recommends bringing more railroad personnel into the building team’s project meetings, as these sessions progress from ideas to details.
“It is important for all parties to understand each other’s goals and concerns,” Gottlieb adds. “By having regular interface with the rail design teams, Hudson Yards was tailored to address their concerns, including vertical and horizontal clearance to track outages to meet the rail infrastructure’s needs while allowing the project to be completed.”
Ultimately, the only way to make these complex projects work is with a high level of planning and frequent meetings. “The key is constant communication between the builder and the railroad,” agrees Flynn.
Emphasizing how complex these types of projects can become, Estevez shares a poignant example. At the base of the 30 Hudson Yards 102-story tower, the only place to locate the building core was on a small terra firma area within the northern portion of the site. “The entire building core—including structural lateral load system, elevators, and mechanical systems—had to shift over 80 feet midway up the building to provide full perimeter of window space at commercial floors,” he says.
At 100,000 tons of steel, these issues contributed to making 30 Hudson Yards the heaviest and most complex steel high-rise building ever built.