Cost Efficiency and Budgeting with Extruded Aluminum Trim
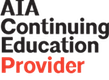
Learning Objectives:
- Describe the process of life cycle cost analysis and how it can be used to guide design choices for long-term value.
- Explain why investing in higher-quality and durable extruded aluminum will reap financial benefits for building owners and occupants over the duration of the building.
- Discuss the various types of coatings and finishes available on extruded aluminum trim and how each type can impact cost, durability, and overall project goals.
- Describe the inherent characteristics of aluminum that can help promote sustainable design and successful integration with green building programs.
This course is part of the Multifamily Housing Academy
Material performance and sustainability are two top requirements in modern architectural design. Whether we’re talking about the overall design or individual interior and exterior material selections, choosing durable, long-lasting products and systems that support human and environmental health will pay dividends across the lifetime of the project.
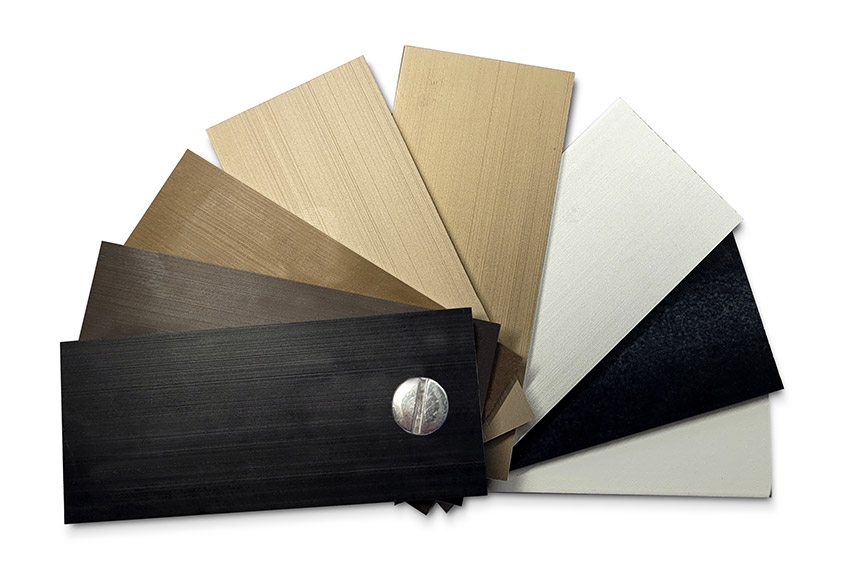
Photo courtesy of Tamlyn
Examples of different metallic color options in an anodized finish.
Trim is a key design choice that contributes significantly to the aesthetics of multifamily buildings. Although there are many options available, extruded aluminum rises to the top. Not only does aluminum have the design flexibility to enhance just about any project, but it is also a sustainable and durable material. Its performance characteristics make it a practical and affordable choice for both exteriors and interiors, especially when you compare the full lifetime cost of extruded aluminum to other materials. In this course, we will compare the performance and sustainability of extruded aluminum trim to other options, focusing on the long-term value that this material choice brings to multifamily projects. We will also explore how to use Life Cycle Cost Analysis to compare various trim options, and we will explore the pros and cons of various coatings and finishing options.
TODAY’S MULTIFAMILY BUILDINGS: A GENERATION APART
The multifamily building market includes an aging stock of poorly designed (and even more poorly finished) multifamily units, most built in the 1970s and 1980s. This unfortunate legacy is the consequence of a mindset focused on short-term gain: how many units can be crammed on a given site for as little as possible?
Today’s multifamily building sector is no longer a race to the bottom, and both owner and occupant expectations are higher. Retirees, millennials, and Gen-Zers don’t mind a smaller square footage of living space, but they are also looking for more amenities and shared community spaces, and they are drawn to mixed-use projects, with shopping or workspace located conveniently on site. They are also concerned with sustainability and are much more aware of the health impacts of their surrounding environment than generations before. And of course, aesthetics matter, too, with clean, modern lines and high-quality materials appealing to these tech-savvy residents.
In this course, we will discover why extruded aluminum trim, whether used in the interior or exterior, contributes to the long-term value of multifamily projects. First, let’s take a closer look at the total costs of ownership, and the critical role of the life cycle cost of key material choices.
Pay Now or Pay Later
It’s important to understand that the construction costs of a multifamily building represent a fraction of the total cost of owning it over the long term. Over time, operation, repairs, staff salaries, replacement or upgrades to materials and systems, utilities, and the cost of disposal and recycling eclipse the initial cost of construction. And that’s not including costs that are typically out of the owner’s control, such as property taxes and interest payments.
The same is true of specific building systems or finish materials: their initial, or first cost, is just the beginning. There are several categories of costs to consider over the lifetime of ownership of these materials, including the initial cost to acquire and install them, operation costs, maintenance and repair, replacement, and disposal or recycling.
It likely makes intuitive sense that some design choices will have a greater impact on certain costs of ownership. The selection of HVAC systems and windows, for example, will significantly affect how much energy the building uses. It is also not surprising that some choices with a lower initial price tag cost more in the long run. Take flooring—an important consideration for multifamily projects. Cheap carpeting may not cost much up-front, but it will likely need replacing every three to five years, and it requires frequent maintenance such as steam cleaning. In contrast, a durable, stain-resistant flooring product may outlast the carpet several times over, and require less maintenance, to boot.
There is a strong relationship between sustainability and long-term value. A building system that requires less maintenance and that lasts longer doesn’t just save money, but valuable resources, too.
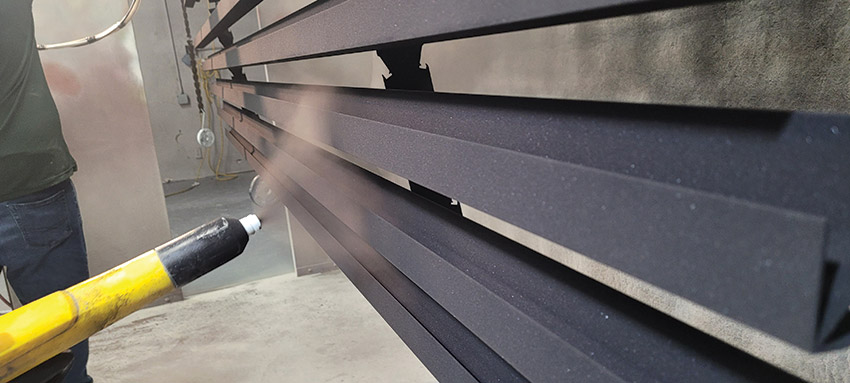
Photo courtesy of Tamlyn
The first layer of powder coat is applied to the extruded aluminum trim profile in a black-gloss finish.
What Is Life Cycle Cost Analysis?
Life Cycle Cost Analysis, or LCCA, is a tool that allows you to calculate the full cost of ownership and to compare one building material or system to another.
Here is a simple formula for calculating life cycle costs:
LCC = C + O + M + D
Where C = Construction, or the initial cost of acquiring the product or system
O = operational costs
M = Maintenance costs, including regular and periodic maintenance, repairs, and replacement
D = the costs associated with disposal or recycling
Before conducting an LCCA, you will have to work with the project owner to determine the appropriate life span of ownership—20 or 30 years, for example.
Some building components, such as lighting and heating systems, for example, come with obvious operational costs, since they require energy to operate. Others, such as trim and cladding, do not. However, the maintenance costs for these materials can be quite high, especially if the material requires full replacement during the ownership life cycle. Notably, maintenance refers to routine tasks, such as cleaning, to periodic maintenance, such as a deep cleaning, touch-up painting, or minor repairs.
Disposal and recycling costs will vary depending on the type of material and available recycling facilities.
Don’t worry if you can’t pinpoint every cost down to the dime; the goal is to calculate a reasonable estimate of the life cycle costs of products and materials so you can adequately compare them. Spreadsheet software can help, as can online tools such as One Click LCA.
It is strongly recommended that project teams address life cycle costs early in the design process, before major decisions have been made. Conducting a Life Cycle Cost Analysis early on, whether for an entire building or a specific system, such as a trim package, can yield several benefits:
- It can guide the design to ensure long-term value.
- It can provide the project owner with better estimates of the total costs of ownership.
- It can reveal hidden costs, such as costly maintenance.
- It can ensure sustainable choices by encouraging the owner to think about the long-term impacts of design options.
Now, let’s take a closer look at extruded aluminum trim and how it contributes to long-term value of multifamily projects.