Building the Ideal Rainscreen: Advantages of Extruded Concrete Panels
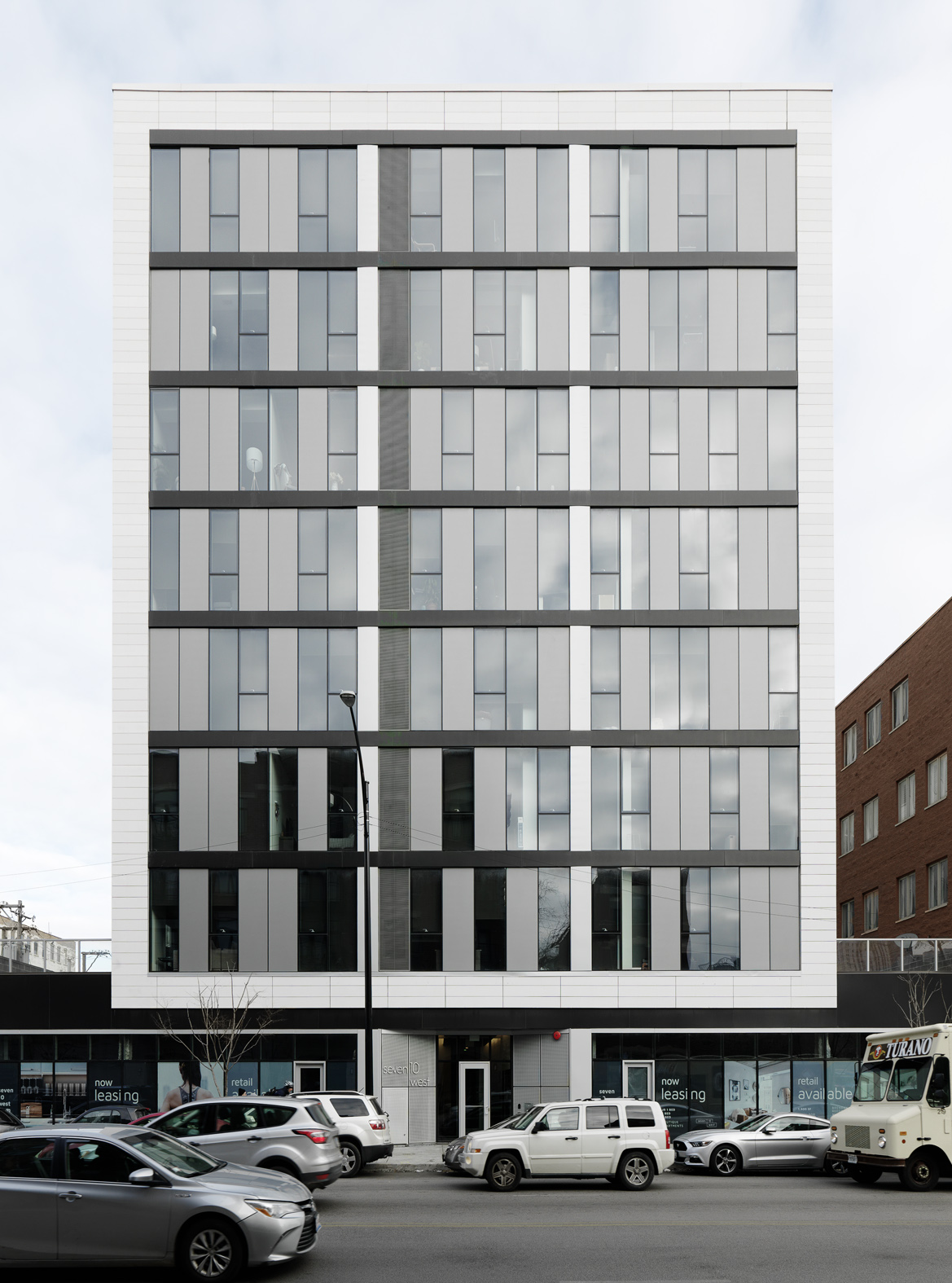
Photo: Rieder Group/Ditz Fejer
Project: 710 Grand
Architect: Brininstool + Lynch
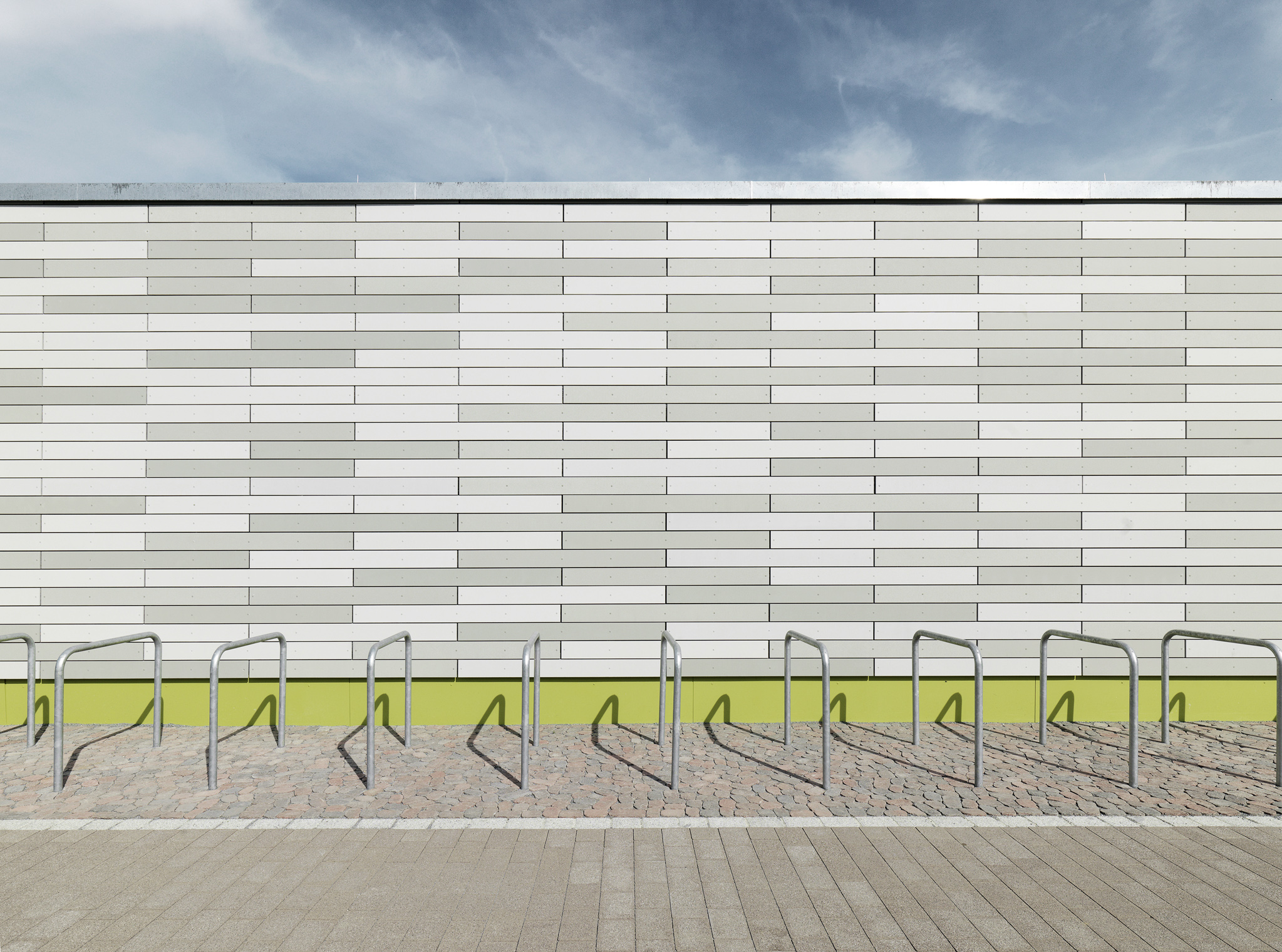
Photo: Rieder Group/Ditz Fejer
Project: School Alburg
Architect: Pielmeier
Understanding the Benefits of Extruded Concrete Panels for Rainscreens
Extruded concrete is an ideal material for rainscreens for many reasons. The manufacturing process creates a material that is thinner, stronger, and more manageable for designing and installing rainscreens. Also, extruded concrete is noncombustible and is available in a wide range of colors and finishes.
Andrew Rogers, president of Rieder North America, an extruded concrete manufacturing firm, has seen its products used in many applications.
“The 1⁄2-inch thick extruded concrete for flat rainscreen walls panels has been proven with over 10 years use in all parts of USA and Canada. The potential uses for this product are vast, including three-dimensional and curved parts for exterior and interior elements, flooring, and furniture,” he explains. “The future development of the product is also extensive, including thermally active facades, larger format panel sizes, and new and exciting textures, colors, and surfaces.”
Out of the concrete-based rainscreen materials, extruded concrete is quickly becoming a popular choice, and for good reason. Rainscreen panels made from extruded concrete layered with glass fiber can be rapidly produced, and the finished product combines many of the desired attributes necessary for quality rainscreens. The most notable qualities are that the finished product is a thin (1⁄2-inch), relatively lightweight, strong, and durable panel that is noncombustible and available in a range of colors and surfaces. By choosing to use rainscreens made from extruded concrete, designers can meet their aesthetic needs, all while using a superior product that is easy to install and will protect the building for a long time.
There are many advantages to extruded concrete rainscreens, most beneficial of which is the thickness tolerance. Cast-in-place concrete loses thickness tolerance, especially with a large sheet. Also, the extrusion is very fast, and it has the possibility of high output or production capacity. Some manufacturers can produce up to 30,000 square feet per day.
A 1⁄2-inch panel made of alternating layers of 3 millimeters of concrete and another layer of mesh made of glass fiber, followed by another 3-millimeter layer of concrete with chopped glass—repeated until 1⁄2-inch—makes for a high tensile strength and a durable panel.
The disadvantages don’t necessarily outweigh the advantages, but they need to be taken into account. For example, one of the limitations of extruded concrete is that it is limited to the width of the machine. So, if the machine width is 48 inches, that is the maximum-width panel that is available.
A beneficial feature of extruded concrete panels is that the products are naturally cured, typically for 28 days at room temperature. This curing process means that this aspect of their production requires very low energy use. If we compare this process to alternatives, such as aluminum, high-pressure laminates (HPL) coated with resin and paper, or cement board, extruded concrete comes out on top for manufacturing energy efficiency. The products are also all natural and thus are not prone to off-gas vapors in the way that other products might.
Extruded concrete panels have a wide range of color and texture options, which in turn makes them versatile for project design. Iron oxide is usually used to attain the product colors. The natural pigments blend in well with the natural environment to help designers achieve a seamless look between the project and the local landscape. In addition to colors, the panel surfaces can be sandblasted and honed to create vivid textures.
Finally, use of the product is highly versatile, especially when it comes to including original designs on a building’s exterior. Designers have the option of different panel sizes and shapes; for example, slat wall panels that can be easily installed by contractors or do-it-yourselfers. These panels require very little, if any, maintenance. In comparison to wood slat cladding, which needs to be treated or painted to maintain its appearance and durability, extruded concrete panels will retain their look through the lifetime of the product.
Another innovative element of the extruded concrete process is that it can be folded when wet and thus made into different shapes. Most commonly, panels are molded into “U” or “L” shapes that can be used to animate a building’s exterior, but the material can also be put in molds to create curved components. Architects may use U-shaped extruded concrete panels as exterior fins attached to the curtain wall to improve the solar shade capabilities on tall buildings. This 3-D design option has put concrete panels in direct competition with the traditional aluminum fins.
Conclusion
Rainscreen systems are quickly becoming an accepted part of building design, and for good reason. A clearly thought-out water-mitigation plan is an essential part of a project, and that plan can easily include durable, strong, stylish panels that make a bold statement. Extruded concrete panels bring a lightweight, naturally colored, and environmentally friendly option to the rainscreen system. Moreover, this versatile process of extruded concrete is quickly becoming a new way for designers to create 3-D forms that go beyond the basic flat panel.