This CE Center article is no longer eligible for receiving credits.
Long Lasting
Terrazzo can last for more than 100 years. Does that sound like marketing fodder? It is not. As proof, there are four courthouses in the Pacific Northwest that have recently celebrated their centennial, and each of them features terrazzo flooring. Two of the four historic buildings are in Washington. Spokane’s Federal Building and U.S. Post Office turned 100 in 2009. The Tacoma Union Station got its 100th candle in 2011. In Oregon, Portland’s Pioneer Courthouse was completed in 1875 and is now the second-oldest courthouse west of the Mississippi. The terrazzo floors were installed in 1905 and remain in use today. The only signs of age in the aged floors are spots that are slightly worn down in front of the post office window and a couple of settlement cracks that occurred as the building settled into its bones over the past century. Yakima’s William O. Douglas Courthouse, and its terrazzo flooring, turned 100 in 2012.

The original terrazzo floors at the Tacoma Union Station in Washington turned 100 in 2011 and are still in use today.
“Terrazzo is a very durable, beautiful substance for buildings with high traffic,” explains Rebecca Nielsen, Historic Preservation Program specialist and LEED Accredited Professional with the U.S. General Services Administration (GSA) in Auburn, Washington. She oversees twenty historic register federal buildings in the Pacific Northwest. “Terrazzo was obviously a good choice because 100 years later, we are still using it,” she adds.
Over the years, the floors have required repairs to fix chips or minor cracks and an occasional resealing, along with routine maintenance to keep them functional. “The terrazzo is in great shape,” Nielsen continues. “We fix up the cracks and we maintain it. There is certainly no reason to replace it. It is working just fine.”
How Terrazzo Survived Hurricane Katrina
When Hurricane Katrina tore through New Orleans on August 29, 2005, it became the costliest natural disaster in U.S. history. Property damage was estimated at $81.2 billion. Eighty percent of the city and vast sections of neighboring areas were flooded when the levees and flood walls failed. Saltwater surged in, picking up mud, waste, sewage, petroleum, chemicals, and acids, and then sat in stagnated pools for weeks.
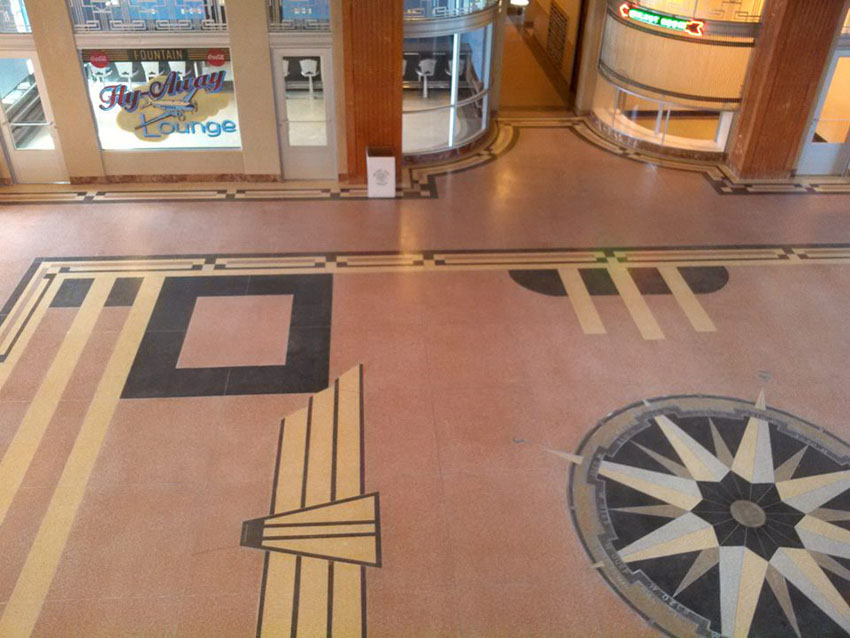
After Hurricane Katrina, the original terrazzo floors in the New Orleans Lakefront Airport generally remained intact and were restored with a light sanding and polish.
The New Orleans Lakefront Airport, located on Lake Pontchartrain, was one of the buildings that sustained incredible damage during the storm. Originally built in 1934 in the Art Deco style, this airport was deemed “the air hub of the Americas” and was considered a wonder of architecture and decor. When Katrina pushed the lake water inland, it submerged the airport in 4 feet of water. Furniture and equipment floated around the ground level.
After the water subsided, the $17-million post-Katrina restoration began. “There were massive property losses at the Lakefront Airport,” reports architect Alton Davis of Richard Lambert Consultants, the leader of the architectural team tasked with the renovation. “None of the drywall that had been installed since the 1960s survived. Even the grid behind the plaster had rusted. Most of the ground-level flooring that had been trapped underwater was destroyed as well—wood, carpet, ceramic tile, and vinyl composite tile (VCT). The terrazzo floors, however, generally remained intact. There were a few places where heavy equipment had gouged or cracked the floor, and that needed to be repaired, but most of the flooring needed no more than a light sanding and polish to be restored.”
The terrazzo at the airport was not the only terrazzo flooring found intact after Katrina. In fact, terrazzo floors around the city had survived their extended submersion and were able to be restored. This was the case for the terrazzo floors at the city’s convention center, train station, and a number of old churches and schools. Clyde Martin of American Tile & Terrazzo Co. of Metaire, Louisiana, was the contractor at the Lakefront Airport restoration and was heavily involved with many of the other terrazzo restorations throughout the city. “In one church, the roof and stained-glass windows were destroyed. The statues reduced to rubble. All that could be saved were the structural steel, a few brick walls, and the terrazzo floors,” he reports.
The destruction of Katrina highlighted the toughness of terrazzo flooring. “There is not another flooring choice that held up to the flood,” Martin says. “Water destroys carpet and vinyl tiles. Ceramic tile is easily broken by falling furniture and equipment, and it is hard to patch because of UV discoloration. If the tile grout is stained, it is more cost-effective to start over.”
In the flurry of rebuilding activity, a resilience-focused, flood-proofing trend emerged. Designers leaned on the materials that had proven their ability to survive the extremes and regularly chose metal roofs, concrete block, structural steel, and terrazzo floors for the new construction projects around the city.
“Moisture does not hurt cement. Some bathtubs are made from cement,” explains Gary French, technical director at the National Terrazzo & Mosaic Association. “If the water stays on top of the slab, the terrazzo flooring surface can be restored, oftentimes with just a little light sanding and polish. Even if the structure collapsed and the terrazzo floors were chipped or gouged when large equipment fell on them, the floors can be ground down and repaired.”
While many designers are aware of this material’s durability, seeing how it performed during Katrina and the post-Katrina reconstruction was a powerful reminder for many on just how tough terrazzo is. This sentiment was shared by Alton Davis as he discussed his experience during the restoration of the Lakefront Airport. “Katrina just reemphasized what I already knew about terrazzo. When they tear down the building, it will still be there. If the building lasts hundreds of years, the terrazzo will last hundreds of years.”
The Inherent Sustainability of Terrazzo
Beyond its natural resiliency, terrazzo also has many qualities that allow it to support several important tenets of sustainable design. While first focused on improving the energy efficiency of the built environment, green design considerations have evolved, now placing an increasingly stringent expectation around the material efficiency of the products incorporated into the built environment.
“Terrazzo, as a material, satisfies many green building concerns in terms of its makeup, longevity, and ability to protect the integrity of the indoor environmental quality of a space,” explains Edward Balkin, architect and director of design at Coover-Clark and Associates. “Specifying terrazzo flooring on a project can help to achieve recycled content thresholds, improve construction waste management efforts, and create healthy indoor environments, as its adhesives and sealants are all considered low-emitting materials.”
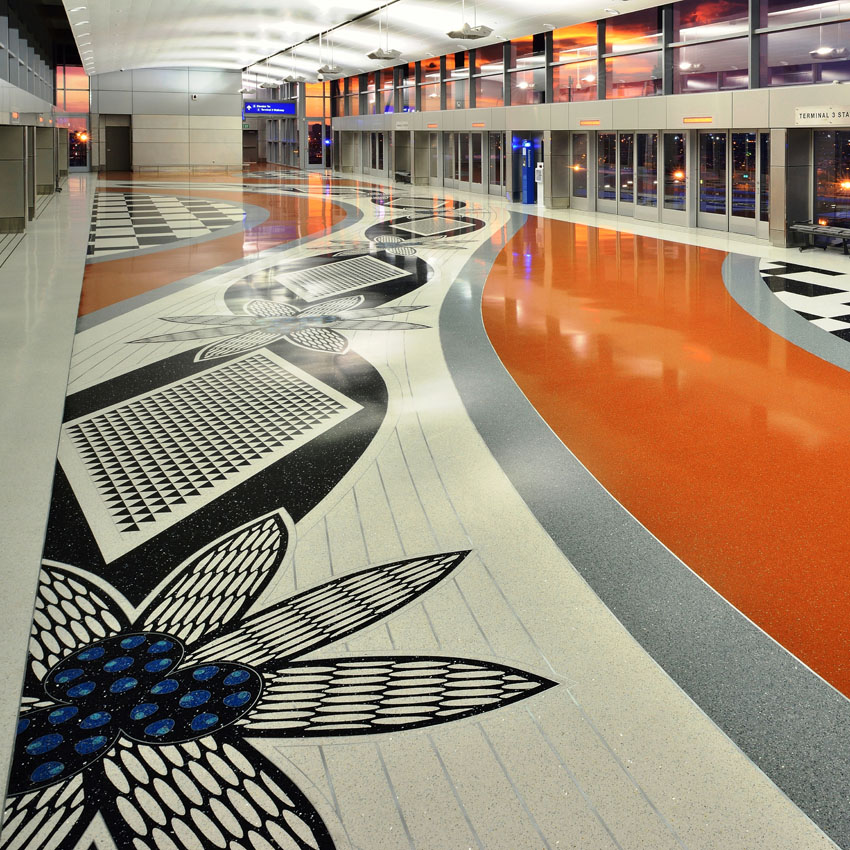
Terrazzo has a number of qualities that make it well-suited for projects with sustainable design goals. It can contribute toward recycled content thresholds, improve construction management efforts, and help create healthy indoor environments.
Recycled Content
There is an old saying in sustainable design that the most sustainable building is the one that is already built. It underlines the importance of the material cost that is incurred in the creation of something brand new. There is an environmental value to fixing something that exists, instead of scrapping it entirely and replacing it with something else. This, in a way, helps to explain the appeal of choosing products that contain recycled content. These products divert something from the landfill. They effectively repurpose some used materials into a new useful life and reduce the use of precious virgin materials and resources.
Terrazzo was originally created in Italy more than 500 years ago by Venetian workers searching for ways to use discarded marble remnants from slab marble processing. Used marble chips were tossed into cement, and the resulting speckled or spotted pattern that emerged on the cured and hardened surface was referred to as terrazzo. Today, terrazzo continues to incorporate recycled content in the form of the aggregates used in the matrix. Several glass aggregate suppliers are currently providing post-consumer recycled glass to the marketplace. A floor incorporating 100 percent recycled glass aggregate could contain as much as 75 percent recycled raw material by volume.
Several slab marble and granite quarries offer supplies of post-industrial stone left from slab granite and marble processing. Terrazzo can also incorporate stone or marble that has been salvaged from other buildings and re-crushed and sieved for use in the flooring. Pieces of pre-consumer porcelain and recycled concrete can also be used in a terrazzo floor. If plastic chips are selected as part of the matrix, they may contain as much as 20 percent recycled plastic. Aluminum divider strips may also contain recycled metal.
Regional Ingredients
Another material consideration gaining traction in the industry is the promotion of regional sourcing. The goal is to reduce the environmental impact that is made by transporting the building materials and products to the job site. The idea is that designers should attempt to use products manufactured or extracted within the region, as they require less energy to physically transport them to the site. Regional sourcing also supports the use of indigenous resources.
Terrazzo can be specified and supplied in a way that supports this region-centric approach. The variety of aggregates, as well as the cement and epoxy binders, are available throughout many areas of the United States. Not only can the material used within the terrazzo be sourced locally, but the distinct and regionally sensitive aggregates can create a flooring surface that has a greater connection with the space. For example, in regions where there is a lot of granite, granite can be incorporated into the terrazzo flooring to showcase a local resource. There are many manufacturers, suppliers, and distributors of terrazzo strategically located throughout the country.
Resiliency is a hot topic in design and construction today, motivated, in part, by the seemingly constant barrage of extreme weather events occurring across the country and around the world. And, sadly, these events seem as if they are happening more regularly—because they are. The Fourth National Climate Assessment (NCA4), released in November 2018, is a report mandated by Congress that “analyzes the effects of global change on the natural environment, agriculture, energy production and use, land and water resources, transportation, human health and welfare, human social systems, and biological diversity.” One of the key findings of NCA4 was that “the number of heat waves, heavy downpours, and major hurricanes has increased in the United States, and the strength of these events has increased too.” In addition, the report found the number of billion-dollar disasters, the term used for weather and climate-related disasters where overall damages or costs have reached or exceeded $1 billion, is on the rise as well.
From a design perspective, knowing that the occurrence of extreme weather events is on the rise gives designers good reason to look for ways to enhance the ability of a building, or a wider community, to prevent damage or recover from it more easily. This is the very idea of resilience.
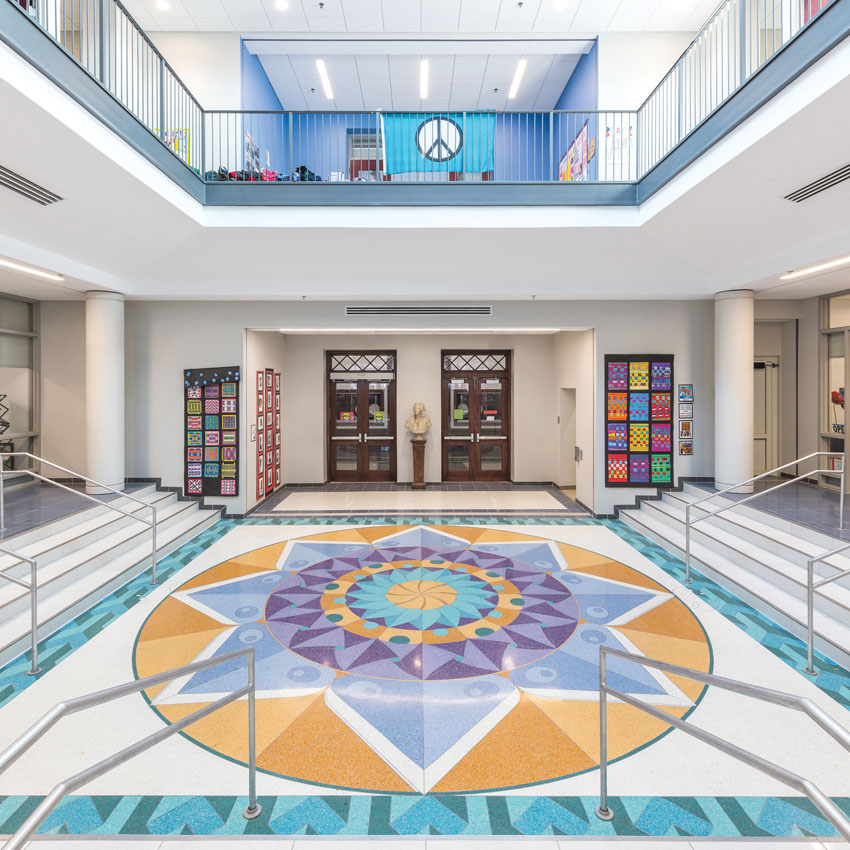
All images courtesy of The National Terrazzo & Mosaic Association
Terrazzo is a poured-in-place flooring material that offers a unique blend of resilient and sustainable qualities.
As a strategy, resilience requires looking at almost every design decision through an extra lens. Resilience can be affected by building siting and layout. It requires extra levels of redundancy to reduce the potential single points of failure, and it increases the scrutiny under which various building systems and materials are selected. It may also create a greater demand for using materials that are inherently resilient and able to withstand exposure to the elements and be restored to like-new conditions. One example of a truly resilient material is terrazzo.
Introducing Terrazzo
Terrazzo is a poured-in-place or precast composite material that can be used as flooring or for wall treatments. While each installation is custom and distinct, terrazzo contains a blend of marble chips, quartz, granite, glass, and other types of aggregate, which is poured with a binder that is cementitious, epoxy, or a combination of both. In general, a terrazzo blend is roughly 75 percent aggregate (marble, granite, glass, pebble, porcelain, mother of pearl, sand, etc.) and 25 percent binder.
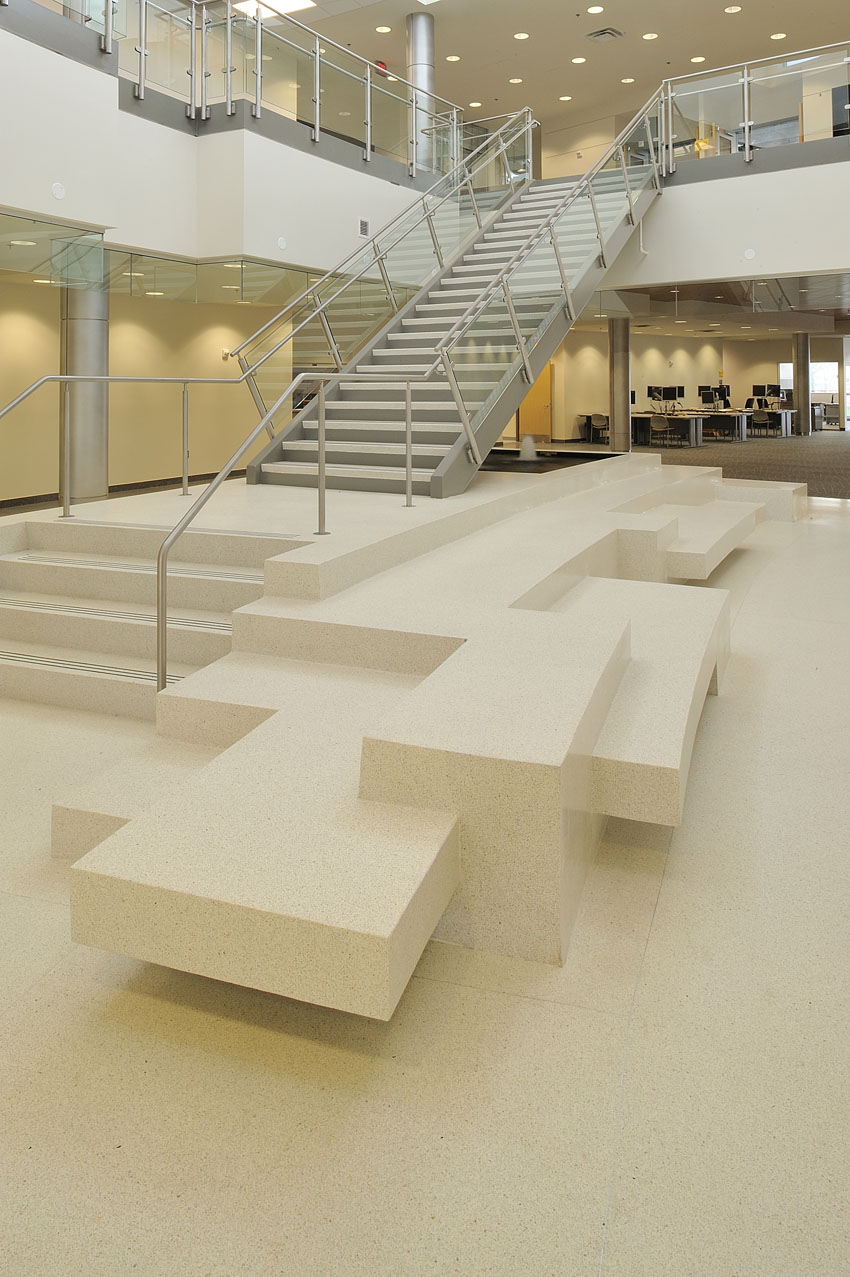
Terrazzo is difficult to damage, easy to repair, and available in an almost limitless number of colors and forms.
Divider strips are also part of every terrazzo surface. They are commonly used to separate different colors in the pattern and need to be placed at termination points (threshold of a door or where the flooring material changes) and at joints with excessive movement. The specific requirements for where the divider strips must be placed depend upon the type of terrazzo system being installed. The standard practice for cement-based terrazzo is to coordinate the placement of the divider strips with the joints found every 4 feet by 4 feet. This helps to counter the shrinkage and movement that can lead to cracking. Epoxy requires fewer strips and only true joints in the concrete must be honored. Divider strips can be selected in a variety of different material, including brass, plastic, zinc, and aluminum. The use of divider strips enables a terrazzo surface to contain ornate and intricate patterns, drawings, and designs.
If the binder is cementitious, the matrix is referred to as a cement matrix. If the binder is epoxy, the matrix is called an epoxy matrix. After the terrazzo is poured into place, it is cured. Then it is ground and polished smooth or otherwise finished to produce a uniformly textured surface.
The Inherent Resilience of Terrazzo
Terrazzo has many qualities that make in an inherently resilient material. It is extremely difficult to damage, and it can be easily repaired. It also is designed to last. Terrazzo installations can be found where the terrazzo flooring is still in use and more than 100 years old.
Durable
Terrazzo is designed to be more than decorative; it is designed to be used. It has an incredible compressive strength. Compressive strength of a material indicates its ability to resist compression. Materials often receive a compressive strength rating, which quantifies a compressive strength limit. If a material is compressed underneath a load that exceeds its strength, some materials can fracture, while others deform irreversibly.
As it relates to terrazzo, the compressive strength of a terrazzo floor with a concrete binder is 3,000 pounds per square inch (psi), which is identical to the compressive strength of the concrete slab on which the terrazzo is installed. This means that the concrete terrazzo flooring will not be compromised before the concrete slab it rests on is. Terrazzo flooring with an epoxy binder has a much higher compressive strength and is able to withstand loads of up to 10,000 psi.
In terms of impact resistance, terrazzo, again, is a hearty solution, especially when compared with other popular materials like large-format porcelain. A porcelain tile is not fully bonded to the underlying slab when it is installed, which results in a hollow spot underneath the face of the tile. This weaker area can be more easily cracked and broken when struck. Terrazzo is not installed as a tile but is poured upon the concrete slab as a liquid, forming a complete bond with the concrete slab underneath, devoid of hollow spots that would compromise the strength of the surface.
Easy to Maintain and Repair
In addition to being difficult to damage, terrazzo is easy to maintain, repair, and restore. Imagine a terrazzo floor that has been installed in a school for 50 years. If it gets chipped or starts to look dirty, maintenance teams can simply remove the old sealers and grind and repolish the floor. In no time at all, the terrazzo floor will be gleaming as if it were brand new. The thickness of the material makes it possible to grind it down and restore the appearance of the surface. If the terrazzo floor happens to crack, it can be patched and made functional again.
In terms of maintenance, terrazzo only requires regular damp mopping with clean water and occasional resealing. Wax and polishes are unnecessary, and even harmful to the surface by creating a buildup that dulls the finish. There are special sealers available for terrazzo that can be used to enhance the appearance of the product or provide additional protection, if desired.
Long Lasting
Terrazzo can last for more than 100 years. Does that sound like marketing fodder? It is not. As proof, there are four courthouses in the Pacific Northwest that have recently celebrated their centennial, and each of them features terrazzo flooring. Two of the four historic buildings are in Washington. Spokane’s Federal Building and U.S. Post Office turned 100 in 2009. The Tacoma Union Station got its 100th candle in 2011. In Oregon, Portland’s Pioneer Courthouse was completed in 1875 and is now the second-oldest courthouse west of the Mississippi. The terrazzo floors were installed in 1905 and remain in use today. The only signs of age in the aged floors are spots that are slightly worn down in front of the post office window and a couple of settlement cracks that occurred as the building settled into its bones over the past century. Yakima’s William O. Douglas Courthouse, and its terrazzo flooring, turned 100 in 2012.

The original terrazzo floors at the Tacoma Union Station in Washington turned 100 in 2011 and are still in use today.
“Terrazzo is a very durable, beautiful substance for buildings with high traffic,” explains Rebecca Nielsen, Historic Preservation Program specialist and LEED Accredited Professional with the U.S. General Services Administration (GSA) in Auburn, Washington. She oversees twenty historic register federal buildings in the Pacific Northwest. “Terrazzo was obviously a good choice because 100 years later, we are still using it,” she adds.
Over the years, the floors have required repairs to fix chips or minor cracks and an occasional resealing, along with routine maintenance to keep them functional. “The terrazzo is in great shape,” Nielsen continues. “We fix up the cracks and we maintain it. There is certainly no reason to replace it. It is working just fine.”
How Terrazzo Survived Hurricane Katrina
When Hurricane Katrina tore through New Orleans on August 29, 2005, it became the costliest natural disaster in U.S. history. Property damage was estimated at $81.2 billion. Eighty percent of the city and vast sections of neighboring areas were flooded when the levees and flood walls failed. Saltwater surged in, picking up mud, waste, sewage, petroleum, chemicals, and acids, and then sat in stagnated pools for weeks.
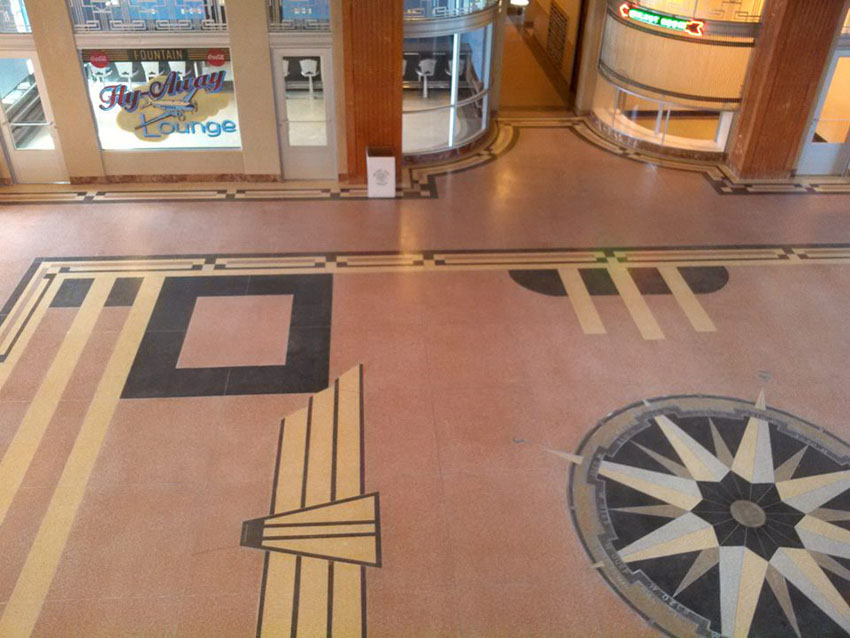
After Hurricane Katrina, the original terrazzo floors in the New Orleans Lakefront Airport generally remained intact and were restored with a light sanding and polish.
The New Orleans Lakefront Airport, located on Lake Pontchartrain, was one of the buildings that sustained incredible damage during the storm. Originally built in 1934 in the Art Deco style, this airport was deemed “the air hub of the Americas” and was considered a wonder of architecture and decor. When Katrina pushed the lake water inland, it submerged the airport in 4 feet of water. Furniture and equipment floated around the ground level.
After the water subsided, the $17-million post-Katrina restoration began. “There were massive property losses at the Lakefront Airport,” reports architect Alton Davis of Richard Lambert Consultants, the leader of the architectural team tasked with the renovation. “None of the drywall that had been installed since the 1960s survived. Even the grid behind the plaster had rusted. Most of the ground-level flooring that had been trapped underwater was destroyed as well—wood, carpet, ceramic tile, and vinyl composite tile (VCT). The terrazzo floors, however, generally remained intact. There were a few places where heavy equipment had gouged or cracked the floor, and that needed to be repaired, but most of the flooring needed no more than a light sanding and polish to be restored.”
The terrazzo at the airport was not the only terrazzo flooring found intact after Katrina. In fact, terrazzo floors around the city had survived their extended submersion and were able to be restored. This was the case for the terrazzo floors at the city’s convention center, train station, and a number of old churches and schools. Clyde Martin of American Tile & Terrazzo Co. of Metaire, Louisiana, was the contractor at the Lakefront Airport restoration and was heavily involved with many of the other terrazzo restorations throughout the city. “In one church, the roof and stained-glass windows were destroyed. The statues reduced to rubble. All that could be saved were the structural steel, a few brick walls, and the terrazzo floors,” he reports.
The destruction of Katrina highlighted the toughness of terrazzo flooring. “There is not another flooring choice that held up to the flood,” Martin says. “Water destroys carpet and vinyl tiles. Ceramic tile is easily broken by falling furniture and equipment, and it is hard to patch because of UV discoloration. If the tile grout is stained, it is more cost-effective to start over.”
In the flurry of rebuilding activity, a resilience-focused, flood-proofing trend emerged. Designers leaned on the materials that had proven their ability to survive the extremes and regularly chose metal roofs, concrete block, structural steel, and terrazzo floors for the new construction projects around the city.
“Moisture does not hurt cement. Some bathtubs are made from cement,” explains Gary French, technical director at the National Terrazzo & Mosaic Association. “If the water stays on top of the slab, the terrazzo flooring surface can be restored, oftentimes with just a little light sanding and polish. Even if the structure collapsed and the terrazzo floors were chipped or gouged when large equipment fell on them, the floors can be ground down and repaired.”
While many designers are aware of this material’s durability, seeing how it performed during Katrina and the post-Katrina reconstruction was a powerful reminder for many on just how tough terrazzo is. This sentiment was shared by Alton Davis as he discussed his experience during the restoration of the Lakefront Airport. “Katrina just reemphasized what I already knew about terrazzo. When they tear down the building, it will still be there. If the building lasts hundreds of years, the terrazzo will last hundreds of years.”
The Inherent Sustainability of Terrazzo
Beyond its natural resiliency, terrazzo also has many qualities that allow it to support several important tenets of sustainable design. While first focused on improving the energy efficiency of the built environment, green design considerations have evolved, now placing an increasingly stringent expectation around the material efficiency of the products incorporated into the built environment.
“Terrazzo, as a material, satisfies many green building concerns in terms of its makeup, longevity, and ability to protect the integrity of the indoor environmental quality of a space,” explains Edward Balkin, architect and director of design at Coover-Clark and Associates. “Specifying terrazzo flooring on a project can help to achieve recycled content thresholds, improve construction waste management efforts, and create healthy indoor environments, as its adhesives and sealants are all considered low-emitting materials.”
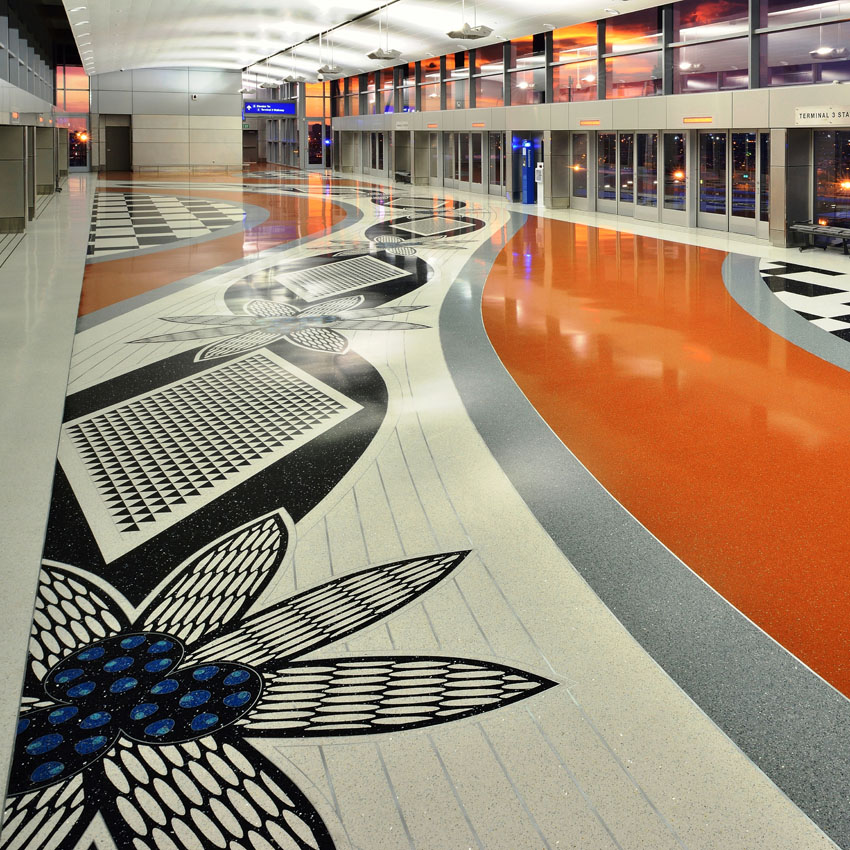
Terrazzo has a number of qualities that make it well-suited for projects with sustainable design goals. It can contribute toward recycled content thresholds, improve construction management efforts, and help create healthy indoor environments.
Recycled Content
There is an old saying in sustainable design that the most sustainable building is the one that is already built. It underlines the importance of the material cost that is incurred in the creation of something brand new. There is an environmental value to fixing something that exists, instead of scrapping it entirely and replacing it with something else. This, in a way, helps to explain the appeal of choosing products that contain recycled content. These products divert something from the landfill. They effectively repurpose some used materials into a new useful life and reduce the use of precious virgin materials and resources.
Terrazzo was originally created in Italy more than 500 years ago by Venetian workers searching for ways to use discarded marble remnants from slab marble processing. Used marble chips were tossed into cement, and the resulting speckled or spotted pattern that emerged on the cured and hardened surface was referred to as terrazzo. Today, terrazzo continues to incorporate recycled content in the form of the aggregates used in the matrix. Several glass aggregate suppliers are currently providing post-consumer recycled glass to the marketplace. A floor incorporating 100 percent recycled glass aggregate could contain as much as 75 percent recycled raw material by volume.
Several slab marble and granite quarries offer supplies of post-industrial stone left from slab granite and marble processing. Terrazzo can also incorporate stone or marble that has been salvaged from other buildings and re-crushed and sieved for use in the flooring. Pieces of pre-consumer porcelain and recycled concrete can also be used in a terrazzo floor. If plastic chips are selected as part of the matrix, they may contain as much as 20 percent recycled plastic. Aluminum divider strips may also contain recycled metal.
Regional Ingredients
Another material consideration gaining traction in the industry is the promotion of regional sourcing. The goal is to reduce the environmental impact that is made by transporting the building materials and products to the job site. The idea is that designers should attempt to use products manufactured or extracted within the region, as they require less energy to physically transport them to the site. Regional sourcing also supports the use of indigenous resources.
Terrazzo can be specified and supplied in a way that supports this region-centric approach. The variety of aggregates, as well as the cement and epoxy binders, are available throughout many areas of the United States. Not only can the material used within the terrazzo be sourced locally, but the distinct and regionally sensitive aggregates can create a flooring surface that has a greater connection with the space. For example, in regions where there is a lot of granite, granite can be incorporated into the terrazzo flooring to showcase a local resource. There are many manufacturers, suppliers, and distributors of terrazzo strategically located throughout the country.
Minimal Waste on the Construction Site
Another sustainable design goal is to reduce the amount of waste that is generated from construction or demolition activities. Nonhazardous construction and demolition debris can be recycled or salvaged. This leads to less waste being disposed of in landfills or incinerated.
Where a project requires the demolition of an existing structure with terrazzo flooring, terrazzo components may be salvaged for reuse or recycled. A qualified terrazzo contractor can assist with component recovery.
It should be noted that the process through which terrazzo is installed on a project also minimizes post-commercial waste and transportation costs. The flooring is manufactured on-site, which means that it is not shipped to the job site in multiple pallets or wrapped in lots of packaging. New techniques for grinding the terrazzo also produce less waste and require less water.
Long Life Cycle
The life of a product is an important consideration in sustainable design because the longer a product’s useful life, the longer it can be used and remain out of the landfill. Terrazzo floors have an outstanding record of durability and performance. This has been showcased in some of the projects discussed in this article that boast terrazzo floors that have been in use for more than a century. The floors typically last as long as the structure.
Low-Emitting Material
One of the biggest themes of green or sustainable design is that the design of a structure can be accomplished in a way that is good for the environment, good for the people occupying the building, and good for the business conducted inside the building. That is why creating a healthy interior is a key goal of this movement.
Chemical contaminants can damage the air quality and negatively affect human health, so many sustainable design building programs have established thresholds for volatile organic compound (VOC) emissions in the indoor air and the VOC content of materials. Selecting materials that satisfy these low emitting standards is one important aspect of achieving sustainable design.
Terrazzo is composed of naturally occurring aggregates, recycled glass or plastic, and processed cement or epoxy binders. Cement-based terrazzo systems use inorganic binders that contain no VOCs. The manufacturers of thin-set epoxy terrazzo systems have moved to formulas that have extremely low VOCs. The terrazzo systems can be installed with sealers that do not contain VOCs in excess of certain limits. Terrazzo exhibits little or no off-gassing over the life of the cured floor.

Designers for The University of Minnesota Amplatz Children’s Hospital selected terrazzo flooring to create the “Passport to Discovery” theme that is featured prominently throughout the facility.
For an example of terrazzo being used in a project designed with sustainability in mind, look no further than The University of Minnesota Amplatz Children’s Hospital. Designed to be Minnesota’s first green children’s hospital, the six-story, 231,500-square-foot building features a prominent and welcoming “Passport to Discovery” theme that guides children and adults through the building and encourages exploration. Each floor of the hospital is designed to reflect a specific ecosystem, enabling patients to travel through oceans, grasslands, lakes, rainforests, and deserts.
Terrazzo flooring was an important element that allowed this theme to be as engaging and pervasive as it is. “We were able to create a crisp, complex design,” explains interior designer Jennifer Mango, IIDA, ASID, of Tsoi/Kobus & Associates in Cambridge, Massachusetts. “The ability to customize with terrazzo is unparalleled.”
In addition to the design flexibility, the terrazzo material has many qualities that make it well-suited for a sustainably designed project. Terrazzo does not support microbial growth, absorb moisture, or grow mold. This is an especially important consideration in a children’s hospital, where patients may be more sensitive to these elements in the environment.
It also does not emit chemical contaminants into the air and is low maintenance. “Terrazzo requires far less maintenance than VCT and is maintained in a much healthier way, without chemicals and off gassing,” Mango continues. “This product was the best choice for return on investment. When you compare its life cycle with VCT, terrazzo will still be in use when the other surface is headed to the landfill.”
Common Misconceptions
Despite terrazzo’s long and distinguished history in architecture, and its increasing inclusion on projects today, many members of the design community still have several misconceptions about this material. Let’s take a look at some of the largest misunderstandings and set the record straight.
Installation Time
One of the biggest misconceptions in the market is that terrazzo flooring requires an incredible amount of time for proper installation. While the exact amount of time that an installation will take is specific to the project and impacted by factors like the climate in which the flooring is being installed, there are general timeframes that may be helpful. Cement terrazzo takes longer than epoxy terrazzo to install and can require three to seven days to cure after it has been installed. Epoxy terrazzo will typically cure overnight. In some parts of the country, such as Miami, contractors may be able to install it in the morning and be grinding it by the afternoon.
Thickness and Weight
Cement terrazzo was the original type of terrazzo. Five-hundred years ago, when the Venetians tossed the remnants of statues into the cement mix, they were making cement terrazzo. Epoxy terrazzo was introduced about 50 years ago and now makes up about 85–90 percent of the market in the United States. Many of the misconceptions about terrazzo today are centered around features of the older cement terrazzo material. For example, sand cushion terrazzo is a specific type of cement terrazzo system that many consider to be the top-of-the-line cement terrazzo solution. The sand cushion system features a layer of terrazzo that is 3 inches thick. This has left many architects with the impression that a high-quality terrazzo flooring must be 3 inches thick, requiring a 3-inch deck in the building plans to accommodate. In truth, there are high-quality terrazzo solutions available that are much thinner.
Epoxy terrazzo systems can be poured as thin as three-eighths of an inch. These thinner installations offer the same durability and strength found in the older, thicker systems. These thinner systems are also much lighter. Where sand cushion flooring weighs approximately 25 pounds per square foot, epoxy terrazzo only weighs 4 pounds per square foot.
New Construction versus Retrofit
Another common misconception is that terrazzo flooring can only be installed in a new construction project, but terrazzo is well-suited for both new construction and retrofit applications. Terrazzo can be poured over concrete slabs and other surfaces, old or new, and can certainly be installed in a new or existing space.
Design Flexibility
With terrazzo, the color selection is limitless, both for the color of the matrix and the colors of the various aggregates included in the matrix. There is also an incredible amount of flexibility in the possible forms that terrazzo flooring can take. A terrazzo surface is not restricted to modular sizes like tile or other flooring finishes, giving it the ability to accommodate designs that range from simple to extraordinarily complex.
“I think many designers do not realize how much you can do with terrazzo,” says architect Edward Balkin, director of design at Coover-Clark and Associates. “Colorwise, you can do almost anything with it, and you can produce elaborate designs or patterns in the flooring that give a space a different perspective and create a distinct, fresh look.”
Edward Balkin knows a thing or two about terrazzo, because he has specified this material many times, including on a recently completed airport terminal at the Minot International Airport (MOT) in Minot, North Dakota.
In Closing
In 2015, almost 300 million square feet of terrazzo were installed in the United States. A recent study conducted by a national research firm predicts that terrazzo will be one of the fastest-growing construction systems over the next 10 years, with annual installations expected to top 400 million square feet by 2024.
The recent (and growing) emphasis on resilient design may explain some of the anticipated increase in use. Terrazzo has demonstrated its inherently resilient nature, which can be attractive to architects and owners looking to create spaces equipped to handle extreme weather and disastrous conditions. Terrazzo has proven over time that it is difficult to damage and easy to repair. It ages well and can weather storms, making it one of few materials offering this blend of qualities.
Perhaps part of the reason for its increasing popularity is the market’s shift in thinking about sustainability and the increasing importance of the materials included in the built environment. Terrazzo is a textbook sustainability-friendly product. It has limited construction waste, can be regionally sourced, and will survive for the life of the building with minimal maintenance. This material is also good for the people around it. It is not cleaned with anything noxious. It will not harbor mold, mildew, or bacteria. As an added benefit, its design potential in terms of form and color is basically unlimited.
In short, terrazzo is good for the environment, good for the people who use it, good for the businesses built upon it, and good for the designers who want to create functional, beautiful, and unique spaces. It is the basic promise of the sustainability movement poured-in-place on the floor.
RESOURCES
Many of the projects profiled throughout this article were first published as case studies in Stories in Stone, a publication of the National Terrazzo & Mosaic Association. For more information, visit www.ntma.com/stories-in-stone.
Jeanette Fitzgerald Pitts has written nearly 100 continuing education courses exploring the benefits of incorporating new building products, systems, and processes into project design and development.