Gypsum’s Role in Earning Points in LEED v4 EQ, and Other Credits
Changes to EQ Category in LEED v4
The latest version of LEED intends to make interiors healthier, to provide a superior indoor environment in the interest of human health and comfort.
Key changes in the EQ category from the LEED 2009 version to LEED v4 include:
• Several credits from LEED 2009 versions have been combined into one, with the total available credits changing from four to three.
• The number of products specifically mentioned has increased.
• Paints and adhesives are required to meet actual low-emitting criteria.
• All products must now state their TVOC (total volatile organic content) into one of three very broad categories.
• Transparency of the total VOCs emitted will be heightened, making it simpler for specifiers to select the lowest-emitting products. This could cause manufacturers to further sharpen their sustainable goals.
The Connection Between Gypsum and Interior Environmental Quality
Gypsum can be an important material in contributing toward satisfaction of certain credits in LEED v4. Here are the applicable credits to consider when using gypsum:
- LEED for Building Design and Construction
- EQ Credit 1: Enhanced Indoor Air Quality Strategies – Option 2 Additional Enhanced IAQ Strategies - D
- EQ Credit 2: Low-emitting Materials
- EQ Credit 4: Indoor Air Quality Assessment - Option 2 Air Testing
- LEED BD+C: Homes
- EQ Credit 2: Contaminant Control – Option 4 Air Testing
- LEED for Interior Design and Construction
- EQ Credit 1 - Enhanced Indoor Air Quality Strategies-Option 2D
- EQ Credit 2: Low-Emitting Materials
- EQ Credit 4: Indoor Air Quality Assessment - Option 2 Air Testing
- LEED for Operations and Maintenance
- o MR Credit 2: Purchasing – Facility Maintenance and Renovation – Option 1iv
For this article, we’ll focus on gypsum’s role in contributing towards satisfaction of sustainability credits for LEED v4 for BD&C in the Indoor Environmental Quality category.
History of Gypsum
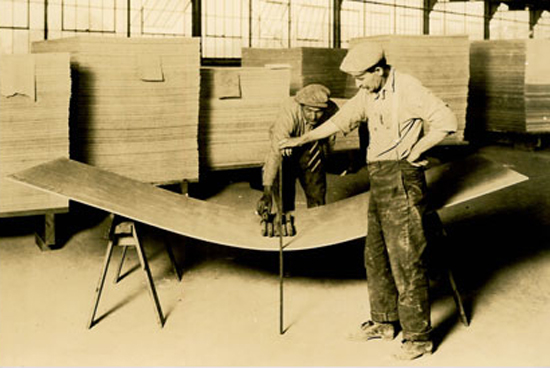
Photo courtesy of National Gypsum
Gypsum has been used for building for thousands of years. Demand for drywall accelerated during World War I, boosted by an urgent need for temporary military housing.
Drywall and plasterboard are non-technical synonyms for gypsum board. The main difference between gypsum and plywood, hardboard, and fiberboard is gypsum’s non-combustible core, and the monolithic surface for decoration that results when fastener heads and joints are covered.
Gypsum has been used for thousands of years. Around 3700 B.C., gypsum was used in the building of the Great Pyramid of Cheops. Around 1200 B.C., gypsum was used in the palace of King Minos of Crete. In the late 1700s, gypsum was chemically treated with heat and then rehydrated to make plaster of Paris, which is still used today. Also in the late 1700s, Benjamin Franklin promoted gypsum in agriculture as a soil additive. The first drywall was created in 1888 when Augustine Sackett sandwiched plaster of Paris between layers of paper.
Five years later, in 1893, the Alabaster Company used a mixture of gypsum plaster and fiber to build the Columbian Exposition at the Chicago World’s Fair. Demand for drywall accelerated during World War I, boosted by an urgent need for temporary military housing.
In 1925, founders of a major national gypsum company developed a process to make drywall lighter and more flexible. Their innovation was what we now know as modern drywall. Early in the 20th century, most American homes were built with interior plaster walls. By 1955, half of the homes were built with gypsum drywall. In the 1960s and 1970s, the use of gypsum drywall expanded rapidly into commercial construction. In Chicago, the 100-story John Hancock Center (started 1965) and the 108-story Sears Tower (started in 1970 and now called the Willis Tower) both were built with gypsum drywall.
Today, gypsum covers the interior of more than 97 percent of the new homes constructed in the U.S. and Canada, and is used to finish the interior and sheath the exterior of non-residential structures throughout the world.
Twenty years ago, the North American gypsum board manufacturing industry was comprised of 16 companies. Many were small, regional, one- and two-plant enterprises, and most produced only gypsum board and gypsum plaster.
Currently, the eight members of the Gypsum Association ship more than 99 percent of all the gypsum board, gypsum panels and gypsum plaster products sold in the United States and Canada. The U.S. members of the Gypsum Association directly employ over 10,000 individuals and have annual full-capacity sales of more than $10 billion.
The modern gypsum board manufacturing industry is fully immersed in the sustainability movement. Over one-third of the material used to manufacture gypsum board is recycled from other industrial processes and the facing material on paper-faced gypsum products is 100 percent recycled paper. Many production facilities use only recycled material to manufacture gypsum products.
How Gypsum is Mined and Manufactured
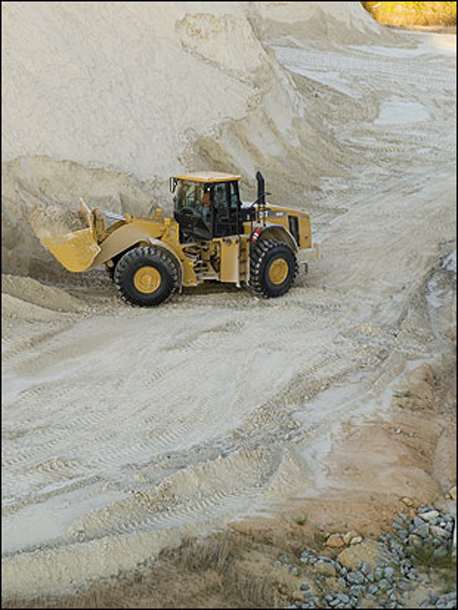
Photo courtesy of National Gypsum
Byproduct gypsum is the ultimate in recycled content. It comes from a process used to remove sulfur dioxide from emissions at coal-fired power plants. After the power plant removes fly ash and other impurities from the coal combustion process, the remaining stack emissions are fed through a limestone slurry which removes sulfur dioxide.
Natural gypsum is a mineral that is extracted from veins of ore near the surface of the earth. Byproduct gypsum is created by desulfurizing flue gases in fossil-fueled power plants. Both natural and byproduct gypsum have the same general chemical composition (CaSO4 • 2H2O) and both are calcium sulfate. The wholesale use of byproduct/gypsum began in the 1980s, though the technology was developed in the 1930s.
For the manufacturing process, natural gypsum rock or byproduct gypsum is crushed to a powder that is heated to about 350 degrees F. The result is “calcined” gypsum, which is used as the base for gypsum board, gypsum plaster and other gypsum products.
According to the Gypsum Association, the calcined gypsum is then mixed with water and additives to form slurry that is fed between continuous layers of paper on a board machine. The paper edges of the board are machine-wrapped as the face and back paper become chemically and mechanically bonded to the gypsum core.
As the board moves down a conveyer line, the calcium sulfate recrystallizes or rehydrates, reverting to its original rock state. The board is then cut to length and conveyed through dryers to remove any free moisture.
Subsequent to drying, board is inspected and trimmed to its final length. Individual boards are placed face-to-face in pairs to form a two-sheet “book.” The cut ends of the book are bound together with end bundling tape and the board is then prepared for storage or shipping.