Facades - The Ultimate Skin Care
Creating a green facade means coordinating the component elements such as metal accents and connections to facade structures. Some use lattice-type structures applied over the exterior of the building and are planted in the ground below. Thus, they require little to no soil since the plants creep up the wall or building along the lattice. Other systems rely on the use of modular tiles and trays that provide a structure for plants and soil. Such structures require a means of irrigation and ample space for the plant roots in which to live.
Any of these strategies for a green facade can all be designed effectively as part of a BIM process. Flexible BIM software with integrated, freeform 3D modeling tools allows designers to create and visualize such systems, similar to other facade systems. Hybrid BIM symbols contain both 3D objects and 2D graphics, which make it easy to visualize and create the required green wall structure and corresponding documentation. A BIM symbol may contain any 3D shape, specific plant objects, image props, and even foliage to help visualize the proposed system. In some programs, a tool specifically for foliage allows the creation of 3D foliage by drawing polylines or closed 3D shapes and has different options for the density of leaves and leaf type. The power of BIM in this case also allows for data to be attached to these symbols to help calculate the environmental impact (i.e., benefits) of the system.
FACADE EXPANSION JOINT SYSTEMS
As discussed already, large buildings will need expansion joints and those joints will need to be covered to keep the facade protected against weather and the elements. Therefore, once the engineer has determined the locations it is then typically up to the architect to select the expansion joint material and the means to cover or seal that joint. What is the best solution? The answer depends on the building and the conditions that it is subjected to. Caulking or sealant may be all that’s necessary for 1 inch or narrower joints with only a little lateral movement, but wider joints need a fully coordinated system. Compressible fillers are common and made from different types of foams that are secured into the joint. Others use bellows, blankets, or tough pleated rubber systems to fill the gap that can bend and move with the adjacent building structure. Metal architectural joint cover systems are usually the preferred choice to cover over expansion joints since they can be selected to meet a variety of criteria. They can move with the joint to absorb different types and amounts of building movement, be attached readily into the structure, and address fire code concerns. Architecturally, they can be finished on the outside with materials that match or are compatible with the finish and color of adjacent facade surfaces.
Matthew Fisher is the Senior Product Manager, JointMaster Division, of Inpro. He sees the issues associated with expansion joints on a daily basis and notes, “No one likes to deal with expansion joints, however, one of my favorite sayings is: If you don’t address expansion joints properly, Mother Nature will install one free of charge─and it will likely be less attractive and leakier than any of the intentionally designed options.
In light of all of the above, we take a closer look at some different types of expansion joint systems in the following sections.
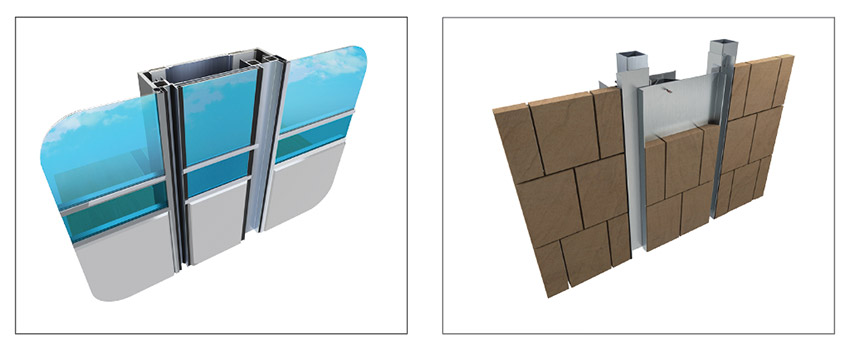
Images courtesy of Inpro
Metal expansion joint cover systems are available to allow for a full range of material types to be inserted so as to blend with the surrounding facade.
Metal Cover Plate Systems
While compressible foam or rubber cover systems will work just fine in some cases, there are cases where a metal system is called for in order to achieve the strength and durability needed. This is especially true on facades that are exposed to all types of weather conditions. In addition, metal cover plate systems should always be used for joints 6” or wider since other types will not likely perform as well over time. In addition to the durability of the cover system, a wide range of accessories can be added in any combination behind the cover to address thermal control, noise dampening, and water resistance as well.
Some things to consider when specifying metal expansion joint systems include the following:
- Quality Control reporting should be provided based on ASTM E1399 “Standard Test Method for Cyclic Movement and Measuring the Minimum and Maximum Joint Widths of Architectural Joint Systems.”
- If metal-based systems are used to cover the joint, they need to demonstrate durability and impact resistance. Composite panels (aka sandwich panels) offer a lightweight material that’s easy to fabricate using ordinary wood and metalworking tools.
- The joint system should accommodate common architectural fastening systems and be suitable for the facade type whether a curtain wall facade, rainscreen system, or other architectural cladding solutions.
- The amount of movement the cover plate should allow for needs to coordinate with the Structural Engineer's requirements- including seismic and lateral shear capable conditions. Note that it is highly suggested to steer engineers away from a full 100 percent (+/-) joint movement. Doing so means they are intentionally designing the structures to close completely together- down to 0", which would effectively crush any fire, water, or other components within the throat of the joint. Instead, challenge the engineers to leave at least 2-3 inches [50-75mm] at maximum closure to maintain the integrity of the systems, even though this means the joint will be slightly wider. A slightly wider joint solution is actually more cost-effective than the alternative systems that need to be deployed when 100 percent (+/-) is requested.
- The expansion joint system should readily conform to complex geometries including parapets, soffits, and other changes in direction on a facade through the use of clearly depicted transitions via isometric details. These can be sourced free of charge by reputable manufacturers for inclusion in contract documents.
- In terms of the finish of the cover plate system, it is common to specify architectural grade weather and fade-resistant resin (Fluoropolymer) color coatings over metal meeting AAMA 2605 requirements. A range of standard and custom colors are available from most manufacturers.
- For other types of finishes, a system that is adaptable to a range of infill options such as stone, tile, or stucco can be specified.
- Exposed fasteners should be avoided in most cases for appearance as well as for safety.
There are other details that can be considered in selecting expansion joint systems too, including the way the cover is engaged. Some systems have tight movement tolerances while others allow for generous day-to-day or seasonal changes without any true activation or resealing required. When a seismic event or dynamic movement is encountered, expansion joint covers are designed to survive the movement pattern. However much like every other system within the building, inspection and reset may be required.
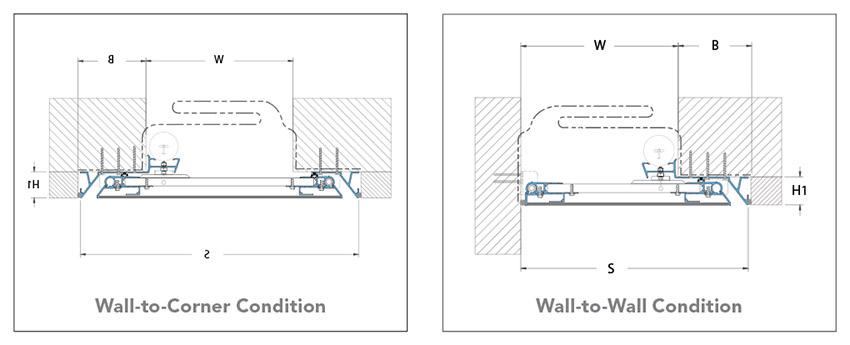
Images courtesy of Inpro
Metal expansion joint cover systems should be specified to meet the needs of a specific building facade and the conditions it is exposed to.
Notice
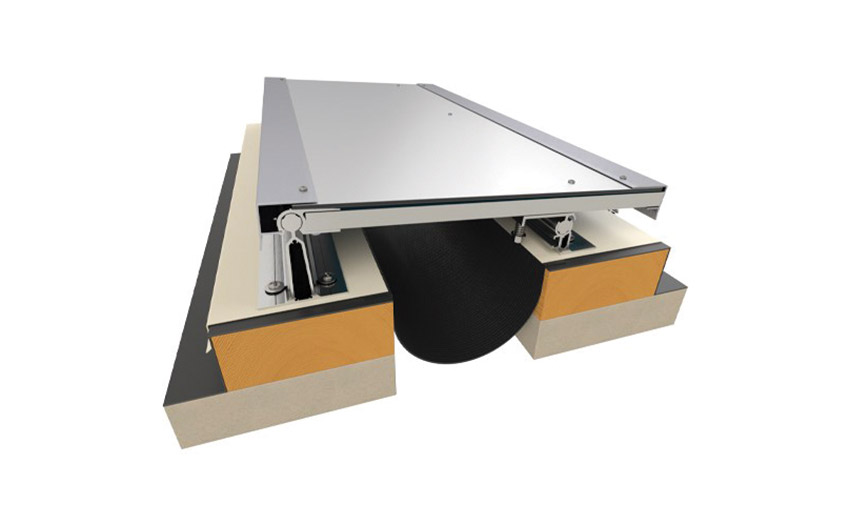
www.inprocorp.com/
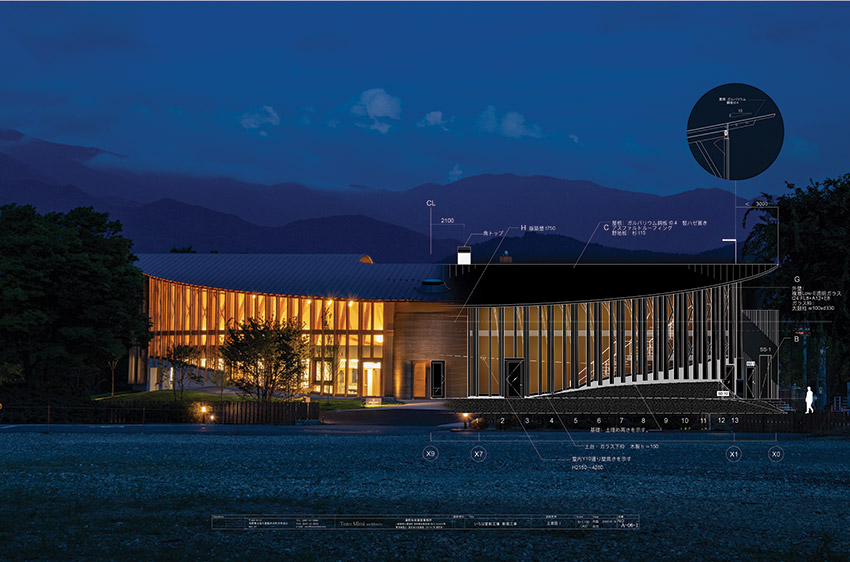
www.vectorworks.net