Shifts in Healthcare Design Create Demand for New Products
Some facilities contract with a mop rental or laundry company, which typically uses tunnel washers (a large scale computerized washing system consisting of a large long metal tube called a tunnel with a metal spiral agitator). This adds extra steps for shipping mops back and forth and runs the risk of loss and deterioration through the use of bleach and excess heat. Using in-house tunnel or standard laundry machines will run the same risks.
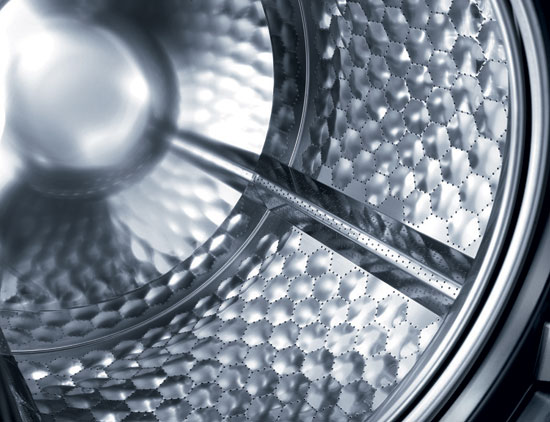
Photo courtesy of Miele Professional
Patented honeycomb drum in washers and dryers preserves the life of fibers.
One laundry system that has been successfully used in Europe for many years is specifically engineered to wash microfiber mops and cloths using features that are not offered by standard machines. The manufacturer has developed a patented convex-pattern honeycomb drum used on all washer and most dryer models that enhances cleaning and reduces microfiber and fabric wear. The size of the drum's water exit holes is smaller and a network of water channels create a skim water layer that cushions fabrics or laundry while the drum rotates. The honeycomb design allows virtually no penetration of fabric through the drum. (In traditional washing drums, the fabric penetrates the water exit holes, which shortens lifespan.)
Laundry Systems: H2O Dryer
More than two-thirds of energy used in the laundry process is consumed in the drying. One of the most energy-efficient commercial laundry technologies available is H2O drying. Introduced to the U.S. in 2013 and used in Europe for several years, the H2O dryer uses heat energy from hot water to dry laundry. It can be installed anywhere there is a source of hot water from solar thermal energy and geothermal energy to co-generation plants.
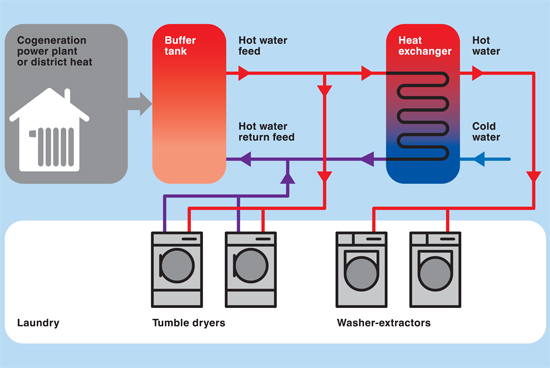
Diagram courtesy of Miele Professional
In H2O drying hot water supplied by a co-generation plant is used as a source of energy for drying.
The hot water is used to heat process air in a heat exchanger. The dryer's programs are specially designed to take care of laundry at lower process air temperatures. This new type of heating is available on tumble dryers with various load capacities. The new H2O dryer reduces laundry heating costs to virtually zero if the source of heat is a co-generation plant. In this case, the hot water is a by-product of cooling the generation plant and does not need to be heated separately. This approach also offers the additional benefit of cooling the water in the H2O dryer for reuse again as cooling water in co-generation.
The new H2O commercial drying technology can cut energy costs of a commercial tumble dryer by up to 96 percent depending on the heat source. “If you review the whole process of linen cleaning, the tumble dryers are by far the most energy-consuming step,” says Miele Professional laundry specialist Celeste Kopyscianski.
The H2O dryer has the same patented honeycomb drum cleaning benefits as the microfiber mop laundry system.