The ABCs of LCAs and EPDs
The Rundown on Roofing Systems
Within the study’s extensive LCA breakdown of roofing systems, the following systems were analyzed and compared: PVC membranes, TPO membranes, architectural low-slope metal roof panels, asphalt shingles, and architectural steep-slope metal roof panels.
Starting with a PVC membrane, the initial raw material production of the panels was found to be the main environmental contributor, and the assembly’s disposal ranks high in eutrophication potential due to disposal of the plastic to landfill and its connection to phosphorous emissions to water from leachate treatment.
With a TPO membrane, because the assembly design and material inputs are very similar a PVC assembly with the exception of the membrane polymer, the potential impacts were similar.
In analyzing the architectural low-slope metal roof panel, the 60-year service life for both the metal deck and metal roof panels mitigate the assembly’s environmental impact, which stands out in comparison to a 30-year service life for PVC and TPO membranes. And unlike the environmental burden created by the plastic contained in PVC and TPO assemblies, the ability to recycle the majority of the steel produces an end-of-life credit. In addition, the regrinding the asphalt underlayment to aggregate filler is considered valuable as well.
With asphalt shingles, the LCA impacts primarily stem from raw material production and maintenance as the shingles and asphalt felt sheet need to be replaced halfway through the 60-year building life.
Because the shingles are generally not sourced locally, the nitrogen oxide and sulfur dioxide tailpipe emissions from transport vehicles factor in more significantly. Additional emissions are calculated for wood disposal to the landfill.
Like low-slope metal, architectural steep-slope metal roof panel can last 60 years. In most categories, steep-slope metal’s environmental impacts are lower than those of asphalt shingles.
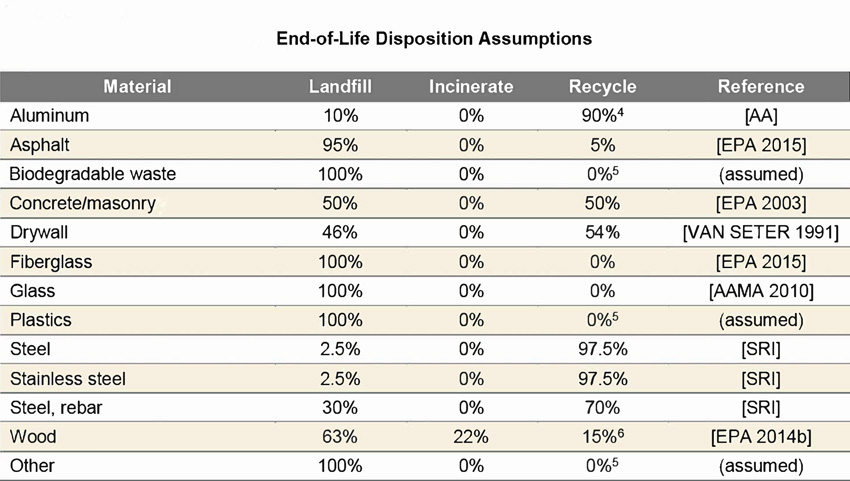
Image courtesy of Metal Construction Association
As compiled in the Metal Construction Association’s “Life-Cycle Assessment of Roof and Wall Envelope Assemblies,” metal roofing and cladding systems offer the highest recyclability percentages as compared to other materials.
Overall, Trisha Montalbo, senior consultant, thinkstep, Boston, reports, “The metal roofing system was shown to use less nonrenewable energy resources, like crude oil, across its life cycle than all the other systems. Compared to asphalt shingles, the metal roofing system also has lower energy consumption and less potentially harmful emissions across its life cycle.”
Generally speaking, KieranTimberlake’s Bates points out that longevity of service life and visual appearance over time are arguments in favor of metal roofs over PVC and TPO. He adds that compared to asphalt shingles, metal roofing absorbs less thermal energy from sunlight, thereby reducing cooling loads.
Wall Assembly Comparisons
In the wall assembly portion of the study, the following systems were analyzed: brick veneer, exterior insulation finishing systems, architectural precast concrete, tilt-up concrete panels, industrial insulated metal panels, architectural insulated metal panels, metal composite material panels, and metal wall panels.
Honing in on the metal wall systems, once again a 60-year service life serves an environmental advantage for these assemblies. With industrial insulated metal panels, 60 percent of the assembly is made from steel and the rest is a gypsum wallboard backing, which has a low impact-to-mass ratio for most categories. Recycling the steel makes a significant contribution to reducing the assembly’s environmental impact and is particularly significant when compared to precast concrete.
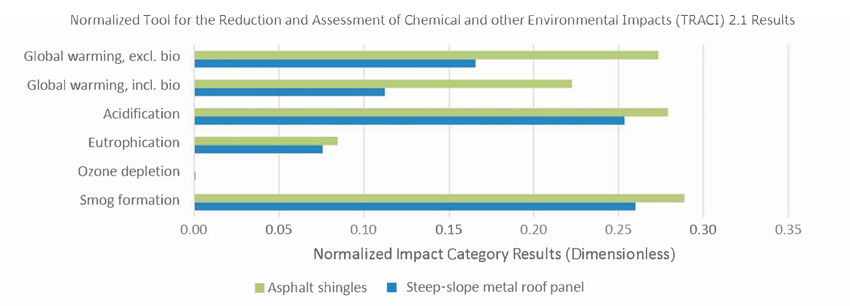
Image courtesy of Metal Construction Association
Within MCA’s extensive roofing and cladding LCA study, steep-slope roof assemblies leave a smaller environmental footprint in all categories when compared to asphalt roofing systems.
Made from a similar material composition, architectural insulated metal panels therefore produce a similar environmental evaluation. Overall, the impacts associated with an architectural insulated metal panel assembly are generally lower than those associated with the tilt-up concrete assembly. In the realm of global warming potential, excluding biogenic carbon, the metal panels fare better than precast concrete assemblies. For eutrophication potential, the panels are the second lowest, in comparison to all the wall systems which were studied.
For metal composite material panels, end-of-life credit is given for the aluminum cladding and gypsum wallboard, and with metal wall panels, for the steel cladding and gypsum wallboard. Overall, the metal wall panels offer a lower environmental burden than the tilt-up concrete assemblies. When factoring in end-of-life credits, this slightly increases the preference for the metal wall panel over the EIFS assembly.
“The excellent recyclability of steel is one of its strongest environmental attributes,” confirms Montalbo. “Additionally, with respect to carbon footprint and demand for nonrenewable energy resources, most of the metal wall assemblies were preferable to the concrete-based assemblies.”
Although both the metal composite material (MCM) and metal wall panels have higher ozone-depleting emission potential than other cladding materials, this concern is normalized when compared to the average statistical environmental burdens in the United States.
Applying LCA Data
Offering some overall perspective on the significance of this study, Philip S. Moser, P.E., senior project manager, Simpson Gumpertz & Heger, Waltham, Massachusetts, is pleased the industry invested in harvesting this valuable LCA information.
“In-depth and non-biased LCA studies like this are important because they advance the state of knowledge in the industry,” he states. “I am glad that the team responsible for study had a high level of commitment to making the study as accurate, credible, and transparent as possible.”
Unfortunately, this isn’t always the case, as Moser references Ehrlich’s Environmental Building News article on cladding, which laments the inconsistency of past cladding industry LCA studies. Here, Ehrlich cites one vinyl siding study that ranked vinyl is the most environmentally responsible siding choice, outperforming brick, fiber cement, stucco, cedar, and EIFS on most metrics. Meanwhile, a cedar lumber industry study shows cedar outperforming vinyl, brick, and fiber cement, and another brick industry study presented brick as outperforming block masonry, fiber cement, vinyl, and EIFS.
The article then quotes LCA expert Rob Sianchuk, director of business development, Coldstream Consulting, as saying, “For LCA practitioners, one of the most frustrating things is stereotyping materials” by over-generalizing based on LCAs.
“With that controversy as a backdrop, it was particularly important that the MCA study is non-biased and credible,” Moser states.
Stressing the importance of accurate LCAs, thinkstep’s Jewell points out that they are very useful to paint the whole picture as opposed to guessing what factors are most important to support a more ecofriendly environment. Furthermore, by bringing the full picture to light, this prevents the shifting of environmental burdens from one part of the life cycle to another. For this particular study, a framework is provided to enable comparability of complex scenarios.
“Many designers don’t have the time or resources for a comprehensive options comparison of the scale presented in the study,” notes Bates. “By providing this analysis as a resource, the MCA is enabling the proliferation of important environmental performance data to an audience that, while interested, wouldn’t otherwise have the LCA data upon which to act.”
That said, to optimally utilize this data, Moser recommends carefully reviewing the details of the assemblies that were studied. “Because preferences for assembly makeup vary by region, building use, budget, and designer preferences, it is important to verify that the assemblies that were studied are representative of those that are being considered on a project before attempting to make design decisions based on the data provided in the study.”
Meanwhile, Bates believes that the information in the study can best be leveraged early in the design phase when deciding upon the core building components. This approach can help point the designers toward a particular construction typology that is most likely to satisfy their sustainability objectives while meeting the other project requirements.
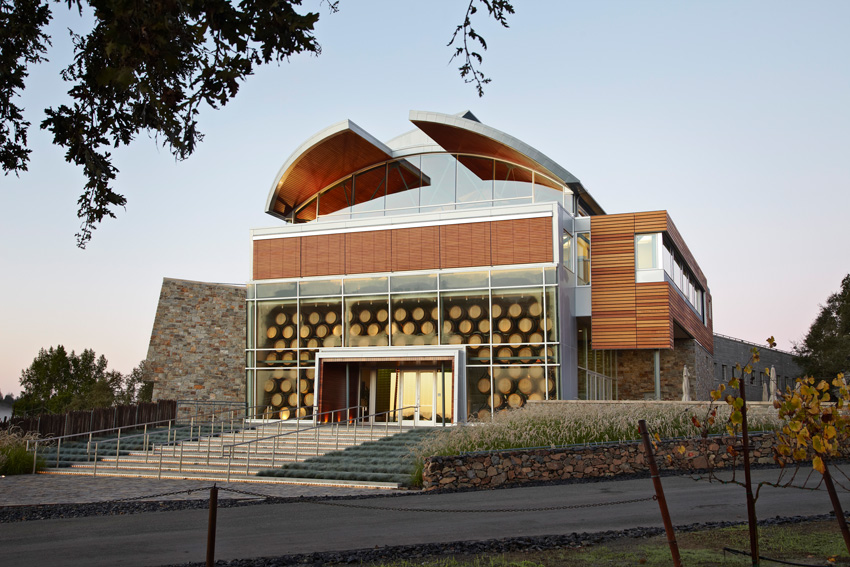
Photo courtesy of RHEINZINK
Emulating a wine barrel, the administrative building for the Williams Selyem Winery in Sonoma County, California, incorporates a curved, barrel-vaulted roof topped with stepped zinc panels.
But before this can happen, building teams must incorporate sustainability performance into their design and purchasing decisions. “Technical requirements, aesthetics, and price will always be important decision criteria, but this study now enables carbon footprint, energy use, water demand, and other environmental metrics to also be included,” Montalbo says.
In addition to benefitting building owners, designers, and contractors, Jakubcin points out that studies like these are also quite useful for product manufacturers, as they provide an opportunity to identify the environmental burdens associated with the entire life-cycle stage of producing their product. “Once these environmental items are identified, the organization can develop programs to reduce the environmental burdens that they feel are important to their company goals,” he says.
Along these lines, the study itself points out that materials account for the majority of the environmental burden associated with each assembly, so addressing the types of materials and amounts used can potentially make the largest impact on reducing the product’s environmental profile.
The report also cites indirect energy consumption as a major factor driving products’ environmental burden. “Therefore, a better way to reduce cradle-to-grave impact may be to add insulating material to limit use-stage energy consumption,” the study recommends.