Individual Parts Bring a Greater Whole
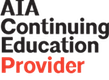
Learning Objectives:
- Explain what a metal composite material (MCM) is and how it is produced.
- Review the available options for MCM skins, including finishes, materials, and specifications, and how these aesthetic options can elevate occupant experience.
- Discuss how MCM skins promote sustainability and practicability of the structure through its life cycle, shielding it from everyday wear and leading to enhanced building durability and health.
- Describe the attributes of MCM core material and how these benefit occupants and create a safer structure during fires.
- Debate the benefits MCM provides, including those related to environmental concerns, efficiency, and economy. Demonstrate how MCM, as a designed material bolsters structural lifespan, green goals, and the well-being of users.
This course is part of the Metal Architecture Academy
Putting It All Together: The Combined Benefits of MCM
The union of metal skin and core material in MCM yields multiple benefits to architect, building owner, and occupants. Not only do MCMs offer exceptional design and aesthetic flexibility, but they also create a reliable building envelope, are environmentally friendly, and keep installation and maintenance costs low.
MCM Systems Protect the Building Envelope
Properly designed and installed, MCM systems provide a very reliable building envelope that resists the elements and protect against air and water infiltration. Installation systems are available that virtually eliminate concerns over mold and mildew.
MCM is also an environmentally responsible and sustainable choice for buildings. Approximately 70 percent of an MCM aluminum by weight is recycled content.
MCM Systems Create Lower First Costs
Aesthetics is one reason MCM systems are increasing in popularity. Affordability is another. Early in their history, the use of MCM systems was limited to high-end projects. However, as a result of improvements in product technology and manufacturing efficiencies, as well as fabrication and installation techniques, MCM systems are more cost-competitive today than ever before.
Initial construction costs are often lower with MCM systems because the panels can typically be installed faster than alternative exteriors, such as precast, granite, or brick. Because of their light weight, MCM systems can also save money by reducing structural steel requirements since less support structure is needed.
As a result, MCM systems are now installed on a wide variety of building types and applications, ranging from major project wall panel systems to cornices and canopies, and frequently used to join areas between other major building materials, such as glass and precast panels.
MCM Systems Lower Building Life-Cycle Costs
Today’s MCMs retain their color and finish for decades, ensuring that the building maintains its aesthetic appeal and property value for the long term. This longevity makes a difference when it comes time to sell the building. Facilities clad with MCM systems retain their curb appeal and never look dated, thereby reducing the need for pre-sale refurbishing costs.
Fire Protection
One of the phrases often heard in the field is “engineered to perform.” Performance encompasses the ability of a product to endure, withstand daily wear and tear, and provide protection during hazardous events like fires and floods.
The only element generally considered combustible in an MCM is the core itself. While many of the fire-resistant cores have been tested and meet the requirements of a Class A material, the metal skins add an additional protection for that core material. Fire will typically reflect off the metal skin for quite some time before the metal becomes compromised and the core is directly exposed.
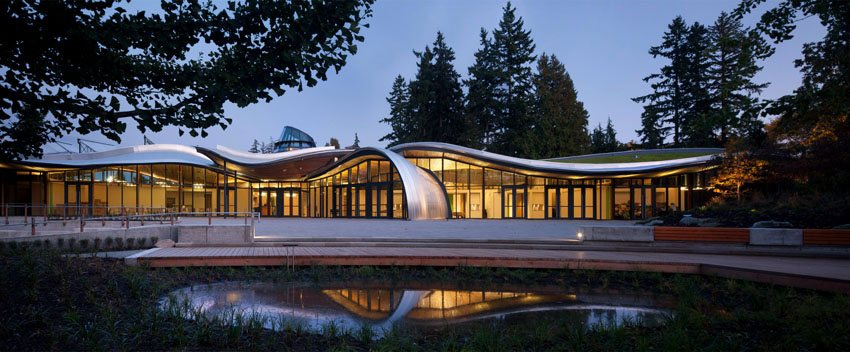
Photo courtesy of 3A Composites USA
VANDUSEN BOTANICAL GARDENS VISITOR CENTRE, VANCOUVER, BRITISH COLUMBIA
Aluminum composite panels were blended with traditional wood supports to both evoke and promote sustainability and beauty.
Vision Achieved, Codes Met
What was once a small, focused industry that offered a lightweight alternative to solid plate installations has expanded into an industry today offering varied materials and manufacture meeting key performance requirements. With MCM systems, the choice of material is in the hands of the designer, and the choices of the owner and end users determines the type of performance required for a building to be considered safe and acceptable.
Step back to that plan table at Perkins+Will Canada. Now, travel to the job site and see the plans realized. Of all the qualities that garnered the VanDusen Botanical Gardens Visitor Centre in Vancouver, British Columbia, a 2013 Chairman’s Award from the Metal Construction Association for metal roofing, perhaps foremost was how it blends striking aluminum composite panels with traditional wood supports to both evoke and promote sustainability and beauty. What sets the VanDusen building apart visually is its bold use of approximately 12,000 square feet of MCM panels on an undulating roof designed to look like five orchid leaves. The panels used in the building feature two coils of 0.020-inch aluminum thermobonded to a polyethylene core, all of which can be recycled. The panels cover a living, vegetation-filled roof constructed mainly of Douglas fir beams and plywood.
“The roof is really exuberant,” says Jim Huffman, design principle for project architects Perkins+Will Canada, Vancouver. “And they wanted a building that really drew people in. One of the first meetings we had with the client—and I have never had a client say this before—they wanted the building to be outrageous.”
The panels proved easy and quick to install, a plus in Vancouver’s rainy climate. Because the 19,000-square-foot building has an organic design, the roof elements include a flowing stream of positive and negative curves, all achieved with an interlocking system of prefabricated panels. The installation firm designed a joint system that incorporated a two-piece nose cone that allowed them to extend one piece into the next panel, creating a seamless series of panels throughout each of the roof’s elements.
Containing the heavy load of the roof’s soil and plant life was one thing, but the panels also carried stress in a way that gave Perkins+Will and KPS a material that could bend and roll reliably and consistently into the organic shapes they created in their 3-D design software.
“This is art; this is expression,” Dalzell says. “This is not a solid product; it is a shape and form. And what you do is, you let the shape and form take over a little bit. If you try to do what we pulled off here on a flat sheet of metal, be it aluminum or stainless or whatever, it would probably kink on you. You would be pushing it too hard, and it would let go.”
The building was designed to exceed LEED New Construction Platinum standards. Even more ambitiously, it has been submitted for the International Future Living Institute’s Living Building Challenge, a stringent standard that Huffman is confident the building will meet.
In addition to demonstrating sustainability with the living roof, the Visitor Centre practices it every day in ways that make the building a net-zero consumer of energy and water. It achieves that status, in part, by using solar hot water tubes on the roof to transfer heat to underground tanks for later use and an innovative, on-site bioreactor to clean wastewater and return it to a leaching field nearby.
“Our firm is a strong believer in sustainability, and that was one of the things that we thought a botanical garden should show to the public,” Huffman says of the building, which cost almost $22 million (Canadian) to build. “That whole project is about sustainability, about showing people how they can live in the future. I think it is one of the greenest buildings in North America, if not in the world, right now.”
Amanda Voss, MPP, is an author, editor, and policy analyst. Writing for multiple publications, she also serves as the current managing editor for Energy Design Update.
![]() |
The Metal Construction Association brings together a diverse industry for the purpose of expanding the use of metal in construction through marketing, research, technology, and education. MCA member companies gain tremendous benefit from association activities that focus on research, codes and standards, market development, and technical programs. www.metalconstruction.org |