Decision Point–Examining the Advantages of Insulated Metal Panels Against Tilt-Up
Engineering safety factors are determined by building codes, industry practices, general engineering principles, or ICC-ES Acceptance Criteria. For IMPs, overall panel strength is determined by the following laboratory tests:
- ASTM E72 -10 – Standard Test Methods of Conducting Strength Tests of Panels for Building Construction, and/or
- ASTM E330 – E330M-14 –Standard Test Method for Structural Performance of Exterior Windows, Doors, Skylights and Curtain Walls by Uniform Static Air Pressure Difference.
When an IMP panel meets required certifications and codes, that means the entire assembly has been put to the test. Everything from the metal facings and metal gauge’s thickness and tensile and yield properties; to foam core properties, including cohesion (how well foam sticks to itself when pulled apart), compression (how well foam holds up under pressure), and adhesion (how well foam sticks to metal skins); to panel design (joint engagement –male/female interlock depth, joint strength –geometry of male/female interlock, width of panels –distance between side joints, thickness –distance between skins); and finally, to attachment methods (clip strength, clip fit and placement within joint, load bearing area of clip, pullout strength of fasteners, pullout resistance of structural supports) is analyzed.
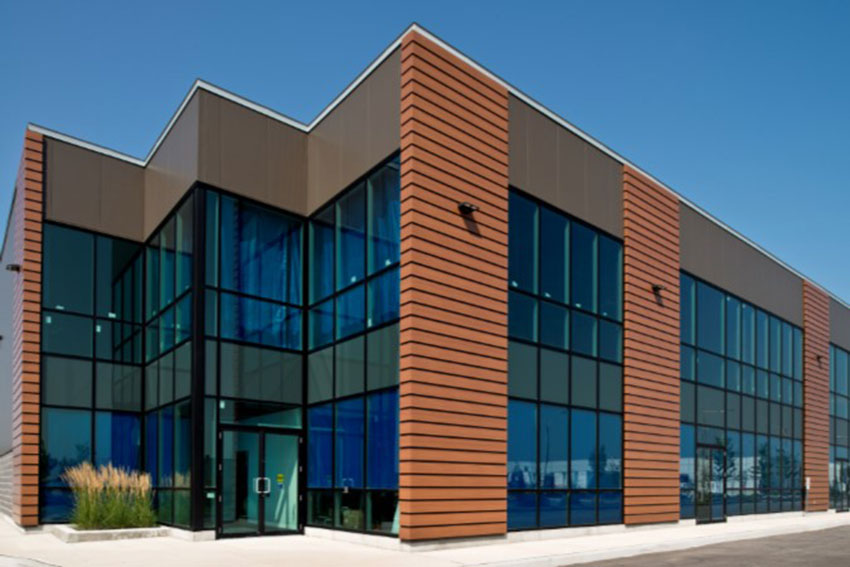
Photo courtesy of Kingspan Insulated Panels
This multi-tenant, mixed-use building on a prominent corner in Vaughan, Ontario, features insulated metal panels in dark bronze which complement the wooden panels.
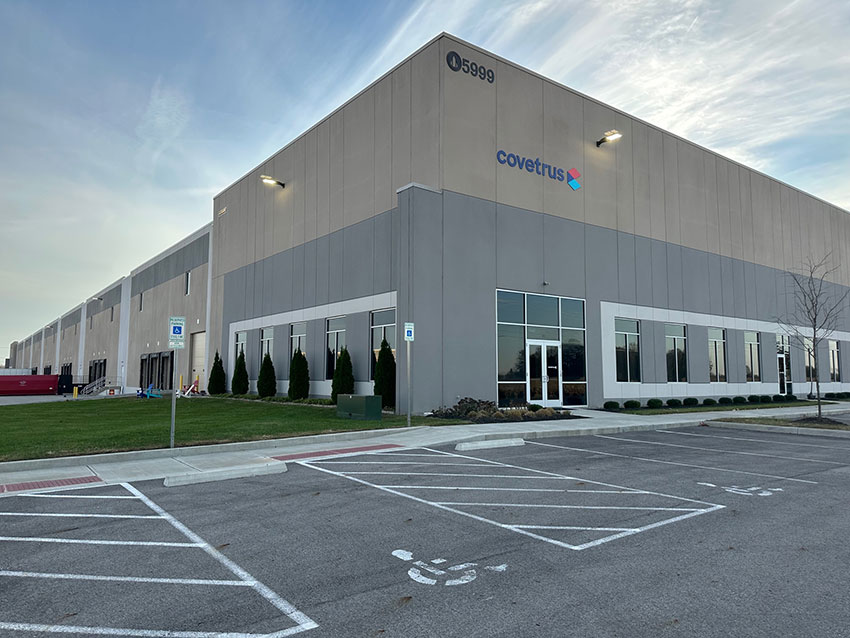
Photo courtesy of Metal Construction Association’s IMP Alliance
This building was built with precast, or tilt-up, construction, which requires a two-step installation process: large concrete panels are cast on site, which are placed in position by a crane.
The Competition: Tilt-Up Concrete
Tilt-up is a method of enclosure construction that uses large concrete panels, cast on site, that are raised into position with a crane. Concrete tilt-up products are a popular solution because of their general availability, durability, and fire resistance.
Constructing a tilt-up enclosure is a two-step process. First, the slabs of concrete that will form load-bearing sections of a building envelope or elevation, are cast horizontally on a concrete slab-on-ground. These slabs, referred to as panels, are tilted up with a crane after the concrete has reached necessary strength. The crane then sets the panels on prepared foundations. The designed wall line is formed from a series of these panels.
The American Concrete Institute (ACI) publishes concrete codes as well as guide and report documents. Under ACI 318 and the IBC, tilt-up is regarded as a form of precast construction. ACI 551.1R offers further guidance and description for tilt-up techniques.
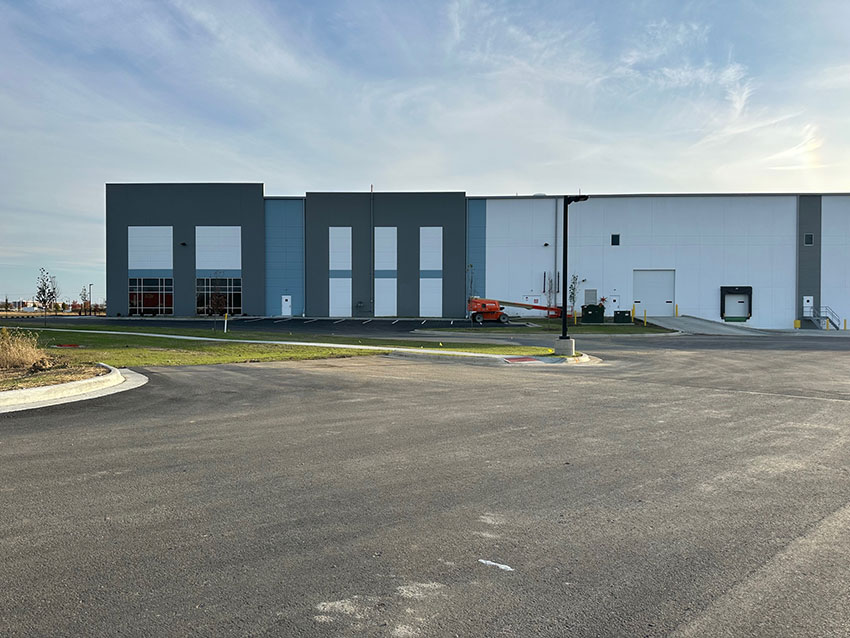
Photo courtesy of Metal Construction Association’s IMP Alliance
This concrete tilt-up building was limited to solid colors. The paint has no long-term warranties.
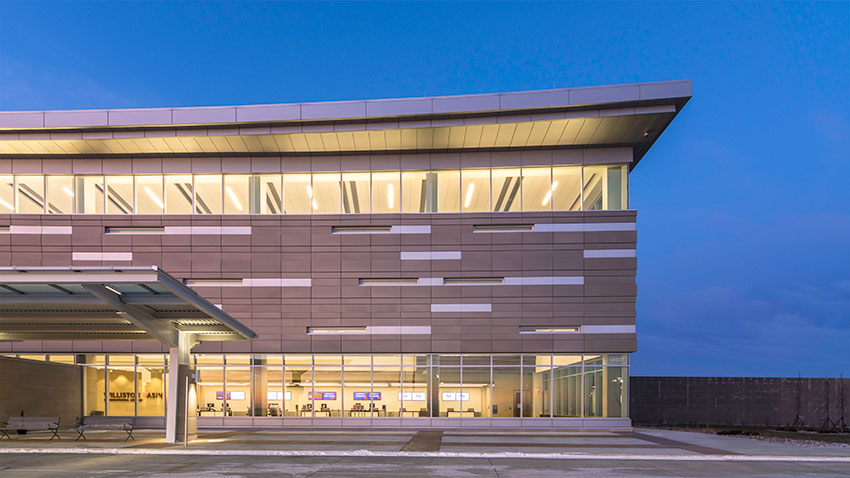
Photo courtesy of Kingspan Insulated Panels and Nucor Insulated Panel Group; Brennan Photo + Video
The Williston Basin International Airport in North Dakota is clad with insulated metal panels in an award-winning design.
Decision Point: IMPs and Tilt-Up
AestheticsFor concrete tilt-up applications, options are limited to solid colors, which are field applied. The paint has low to medium durability, with no long-term warranties. As the colors and finishes are generated in the field, controls are not exact.
IMPs offer long-lasting, durable finishes generated in a controlled environment. The panels have finish warranties of up to 35 years or more, and can use PVDF (Kynar), FEVE (Fluoropolymer based), SMP (silicone modified polyester), Polyester, and Plastisol finishes. Standard 1.0 mil and high build systems offer different finishes, including mica, metallic, weathered metal, wood grain, and prismatic. Long-lasting, low-maintenance paint finishes in a multitude of colors provide design flexibility.
Tilt-up concrete can offer a range of textured finishes. Aesthetic options vary from smooth to exposed aggregate to plank finishes. IMPs offer both smooth and stucco finishes. However, tilt-up wall profiles are more difficult to create in the field. Precast offers greater flexibility, but IMPs are a natural fit where a specific profile is desired. The roll forming manufacturing process allows for greater creative expression, making IMPs the most practical solution to profile.
Both IMPs and tilt-ups are capable of ornamentation and additional product integration. They can also both accommodate curved wall construction.
IMPS IN THE FIELD
Insulated metal panels (IMPs) are one of only a few types of building product that can provide an entire building enclosure in one prefabricated product. An insulated metal panel system can be used on its own to provide a complete enclosure, can be added over a lightweight structure and interior finish in new construction, or can be added over an existing enclosure to provide a new level of enclosure performance.
Initial Advantages: Cost and Installation
Insulated metal roof and wall panels can save costs in materials and labor, due to their single-unit composition and quick installation. “They effectively replace complicated, multi-component assemblies,” says Lisa Fischer, marketing manager at Kingspan. Preformed metal panels are typically lower in installed cost than those of tilt-up, precast, or brick. That's because metal panels can often be installed faster than other building materials, resulting in construction cost savings. Because of their reduced comparative weight, IMPs systems can also save money by lessening structural steel requirements, since less support structure is needed. IMPs arrive on site with built-in thermal breaks, continuous insulation creating high R-values, and connecting panel interlocks, all in a single-element format allowing for faster installation.
Insulated metal panels can be installed more quickly because their installation is also not dictated by weather conditions. This all-weather capability minimizes construction delays, permits fast-track scheduling, gets the building dried-in more quickly, and allows the other trades to proceed with their interior work. Ease of handling and transportation, enhanced job site coordination, and single crew and trade coordination all speed the experience.
Average labor and material unit costs for tilt-up are between $80 and $100 per square foot for a core and shell project. IMPs total from $35 to $55 per square foot for a complete system.
IMP Installation Notes
Panel fabrication and installation are critical components for a successful project. It is imperative that IMPs have good alignment and follow tolerances, especially for those panels with minimal profiles. “Spend time reviewing the structure before erection of the panels,” recommends Arnold Corban, Kingspan. Manufacturer provided installation drawings should always take precedence over generic installation guides. Drawings give guidance for the unique conditions on the project.
The best fabrication will not satisfy the customer if the installation does not match that same level of quality. Guidelines to govern installation tolerances, which establish acceptable visual quality for preformed metal installations, look like the following:
- Panels and trim shall be installed true to line and level (if horizontal) or plumb (if vertical). Exposed fasteners shall be installed in straight lines and at the locations shown on the approved drawings.
- Field measurements to check tolerances shall be by means of commercially available squares, tape measures, or levels that are in good working condition. Measurements shall be made with panels positioned without restraint (if checking fabrication tolerances) and with sufficient support to prevent significant distortion or deflection.
- Panels should be progressively installed so that overall misalignment or tolerance issues are not focused on a single panel on the wall.
IMPs provide exceptionally strong building enclosures. It is not uncommon for these panels to successfully achieve spans of 10 feet or more between supports. For structural support, the width and thickness of the panels or the support spacing can be adjusted. The gauge of the metal facings can affect spanning capability, resistance to thermal stress, and flexural buckling. The composite bond of IMPs produces a building unit that is much stronger than the individual components, even with very light gauge facings. IMPs are not classified as “load-bearing” panels in the sense of axial loading. They can be used on a load-bearing wall, but only if the axial load is carried by other construction─not by the panels. Many insulated panels have a progressive tongue-and-groove interlock joint, being hard-fastened to the structure only along their leading edge. These side joint fastened panels can exhibit low resistance to racking type loads.