Innovations in Aluminum Cladding Systems
In addition to wall cladding, most buildings require some related materials to cover surfaces adjacent to the walls such as soffits and fascia. The word soffit originated with the Latin suffigere, meaning “to fix underneath.” Technically speaking a soffit is the underside of any element of a building. So there are soffits on ceilings, stairs, arches, and even cornices. The most commonly referred to type is found in the area under the eaves on the exterior of a building. This type of soffit extends horizontally from the side of an exterior wall to the edge of the eave and closes the space beneath the eave. Although relatively well protected due its limited exposure, soffits can be vulnerable to weather damage and impacts from other nearby construction failures. Roofing failures of torn or missing roofing, damaged flashing, ice dams, or unintended water infiltration can all add stress to the soffit support or the soffit material itself. Deteriorated or misaligned soffits can create openings that lead to further weather infiltration or small animals entering and causing damage. Since this type of incursion is one of the biggest threats to a building's stability and the health and well-being of its occupants, an integrated cladding and soffit system with a rainscreen design to manage moisture is well worth considering.
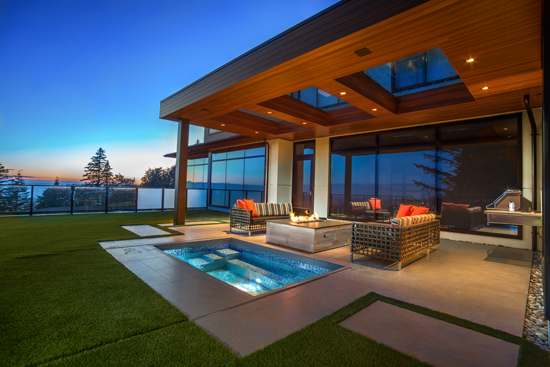
Photo by Dale Klippenstein
Any “underneath” area can constitute a building soffit including this extended area forming an outdoor seating area.
Fabricating Aluminum Materials with a Wood Appearance
One of the advancements of aluminum cladding, siding, and soffit materials is the development of finishing processes that create a very realistic finished wood appearance. Wood-grained aluminum cladding, siding, and soffit materials, used in conjunction with a back-framing system, can provide architects with an aesthetic, energy-saving option for exterior facades in both commercial and residential construction. One misconception about wood grained aluminum materials is that this kind of product is merely a vinyl laminate put on to an aluminum sheet, which is not at all the case. To fully understand these innovative aluminum products, an examination of the multi-step production and fabrication process is in order. Along the way, we will note the ways that aluminum processing has become more environmentally responsible of late as well.
Aluminum Extrusions
Generally speaking, aluminum cladding, siding, and soffits are extruded, meaning the aluminum alloy is changed into objects with a cross-sectional profile. As previously mentioned, extrusion allows aluminum's key physical characteristics to be optimized. In the extrusion process, aluminum is either forced through or drawn through a die that conforms to a particular profile. Extrusion offers several advantages, notably the capability of producing intricate cross sections with superior surface characteristics.
Aluminum Pretreatment
Once the aluminum is extruded and ready for finishing, a pre-treatment process is necessary. The quality of finished metal begins with a proven method to clean it. Traditionally, chrome and phosphate were used to accomplish this task. However, due to potential health hazards, the United States Environmental Protection Agency (EPA), the Occupational Safety and Health Administration (OSHA), and local jurisdictions have severely restricted the use of chrome-based pretreatment processes. In recognition that the future will bring ever more stringent controls, costs, and potentially hazardous effects, some aluminum material manufacturers have opted for pretreatment processes that do not utilize chromium, cyanide, phosphate or other chemicals that have been identified by the EPA or OSHA as potentially harmful. Further, green goals have been achieved by totally eliminating sludge from the pre-treatment process, obviating both the need for hauling, containment and disposal of hazardous materials and the associated costs. Other features that can add to the sustainability of a product are pretreatment processes that involve special formulations to control corrosion.
Powder Coating
A dry finishing process with a four-decade history in North America, powder coating is used on many products for an environmentally sound, durable, and high-end finish that is available in a wide array of colors and textures. Sophisticated technological processes have enabled superior performance.
The powder coating process eliminates or minimizes several issues innate to liquid paints, with the presence of solvents being the key factor. Solvents are inherent to liquid finishes, and they contain volatile organic compounds (VOC), which are emitted as gases from certain solids or liquids, and include chemicals that may potentially result in short- and long-term adverse health effects. VOCs are not present in powder coatings, so they do not release VOCs into the environment, eliminating the need for expensive pollution control equipment and enabling straightforward compliance with EPA regulations. Generally speaking, powder waste is negligible since overspray or unused powder can be easily and economically returned to a feed hopper for future use. Also, less exhaust is incurred in the process—the coating booth emits exhaust air that can be recirculated into the plant, with less hot oven air reaching the outside area. Heating and cooling costs are eliminated for make-up air and the cost for maintaining oven temperatures is minimized.
When specifying powder coatings, the American Architectural Manufacturers Association (AAMA) can be cited for established performance standards. Specifying the performance of powder coatings is typically tied to AAMA 2603, 2604, or 2605, which express increasingly more stringent requirements as evidenced by South Florida simulated outdoor exposure and laboratory accelerated testing procedures. AAMA 2603 is a lower performing specification used for interior applications. AAMA 2604 certified powder coatings demonstrates a 500 percent improvement over AAMA 2603 in the critical areas of color and gloss retention. Finishes so certified will provide hardness and resistance to abrasion, making them suitable for high-traffic areas such as storefronts and doors. The exterior specification for high performance, AAMA 2605 certifies finishes with superior resistance to weathering, humidity, and salt spray testing. Further, some proprietary finishes can give aluminum superior UV resistance, high gloss, and color retention when compared to vinyl, wood, fiber cement, and other powder coated materials.
Sublimation
The process of embedding ink into the base powder coat is known as sublimation and is used to create a realistic wood grain appearance. To achieve the effect, the pre-treated, base-coated aluminum extrusion is bagged in a film that has the desired wood grain pattern inked onto it. The film is then vacuum sealed to the extrusion, covering all of its critical surface areas. Next, the prepared extrusions are placed into an oven where the ink turns to a gas and penetrates through the full thickness of the base powder. It essentially “tattoos the ink” onto the powder coated aluminum. The result is a permanent wood grain pattern with the full benefit of the UV resistance and durability of the base powder coat. It is also possible to add an anti-graffiti coating which allows acetone cleaners to be used without compromising color and gloss retention.
Design Considerations
When choosing to use wood grain appearing aluminum materials, there are several design considerations to take into account in order to achieve the desired aesthetic effect within the context of an energy efficient building.
Aesthetics
For centuries, the look of wood has been valued in the built environment. The natural characteristics of the various wood species add interest and variety to a space and serve as accents or feature elements that effectively contrast or complement other components of a façade or interior. By its very nature, wood has irregular features that are pleasing to the eye. The way in which real wood grows, and the way in which the board is sawed both influence its grain appearance. Wood grain does not always appear uniform, and in many instances the unusual patterns of sawn wood are considered highly desirable from an aesthetic standpoint. In optimizing the selection process, it is important to specify a product in which the faux wood grain has the color, tonal variations and characteristics of the actual wood itself.
Some simulated species naturally lend themselves to specific applications. Popular choices in wood grain aluminum siding include light and dark cherry, which are quite similar to cedar and have good variation in tone and depth. Fir and Ash have a uniform wood grain appearance suitable for contemporary applications. The range of walnut wood grains also work well as accent pieces in modern designs. Dark knotty pine is a popular choice for rustic and large-scale soffit applications.
Profiles
Profile dimensions of the finished extruded products are important to consider as well. Some companies offer several variations, with industry examples ranging from 4-inch to 6-inch channel and V-groove options. The gauge of aluminum used for siding and soffit panels can vary but are available up to 1/16 of an inch. Standard panel lengths are 12 or 24 feet, which enables significant clear spans that can lead to dramatic design possibilities. Long spans also mean fewer seams and faster installations. Products that offer vertical and horizontal profiles, that is, that can be installed vertically or horizontally using the same profile, offer the greatest design flexibility. Some manufacturers offer a range of component profiles to assure a clean, consistent application. These include starter, finishing and expansion strips; J tracks for door and window surrounds; inside and outside corner pieces; and venting profiles. Also available are profiles that act with installation systems, such as back framing, without exposed fasteners to touch up or hide resulting in a clean, sleek look.
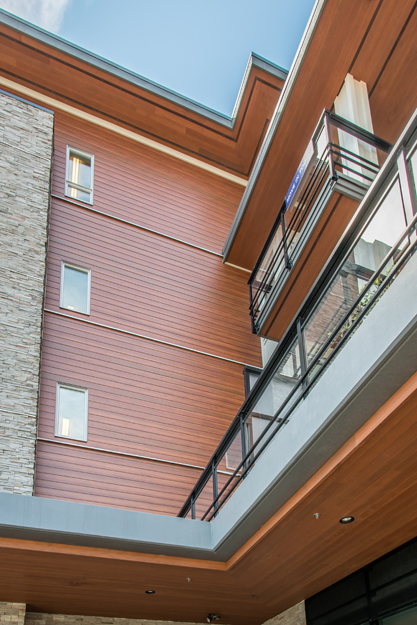
Photo by Dale Klippenstein
The manufacturing process for wood-grained aluminum siding allows for a range of color schemes that can complement other materials. Project: Sotaire (multifamily residential)