Mitigating Risk with High-Performance Structural Wood Panels
The Risks In Light Wood Frame Construction
As in all types of construction, there are inherent risks in building light frame wood structures. Three consistent risks being addressed in building science communities are moisture management, improper installation and, potentially, structural failure. These risks can have disastrous effects on the building and on occupant comfort and safety, not to mention expensive rework and potential litigation against developers, builders, and design professionals. How best to minimize these risks is the focus of this article, beginning with a review of the risks themselves.
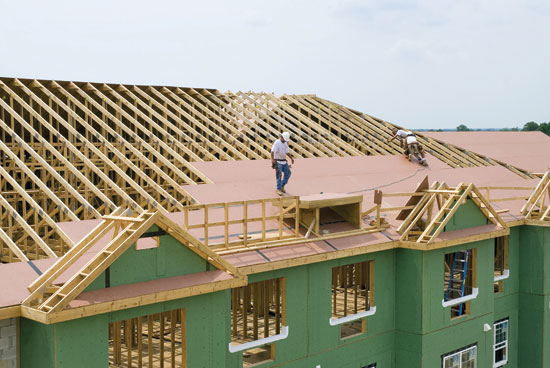
Photo © 2010 Huber Engineered Woods LLC. Photo used with permission of Huber Engineered Woods LLC.
Specifying high-performance roof, wall, and subfloor panels provides added assurance in strength and moisture management and can help mitigate risk in these performance areas during and after construction.
Moisture and Air Management
For centuries, builders have worked to manage moisture issues during construction and prevent the intrusion of unwanted moisture and air into their structures through the building envelope. High-performance panels provide solutions to these problems based on their ability to resist moisture absorption and intrusion and on their ability to promote drying. High-performance subfloor panels are highly resistant to moisture absorption, which translates to superior performance by minimizing any damage to finished flooring due to moisture-related swelling and movement beneath them. High-performance wall and roof panels manage moisture by creating a barrier that repels bulk water intrusion, yet allows moisture in the form of water vapor to diffuse through the panel once the structure is occupied. Exfiltration (air/vapor leakage out of a structure) can also create risks, resulting in the condensation of moisture within wall cavities or other parts of the structure. Inadequate air barriers may allow heated or air-conditioned air to leak to the outside, carrying the cost of heating or cooling that air with it. This air leakage vulnerability can put building owners at a competitive disadvantage against other properties that have built in energy efficiency controls to provide homeowners lower heating and cooling benefits.
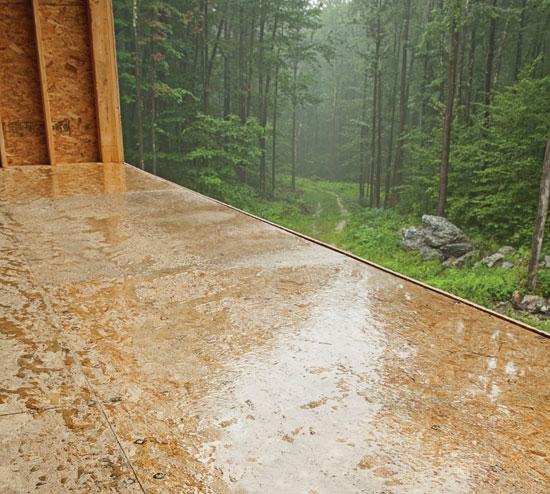
Photo © 2012 Huber Engineered Woods LLC. Photo used with permission of Huber Engineered Woods LLC.
High-performance panels can give the building community a better chance of creating structures that are more weather resistant, durable, and reduce rework construction time.
Improper Installation
Improper installation of roof coverings, improperly fastened structural wood sheathing, faulty flashing, open seams between sheathing or subfloor panels, poorly flashed windows or tape that fails to make a weather-tight bond are all significant threats in today's building environment and can contribute to improper function of a structure. Misuse of materials and lack of attention to the details in the installation process significantly increase the likelihood of problems in the future, and can lead to more complex and expensive problems like floor bounce or squeaks, water condensing within wall cavities, air leakage, mold and mildew, increased energy bills, and other conditions that are unacceptable to both the developer and dwelling occupant. Building envelope and subfloor problems that lead to structural damage or impact the finished materials that rest upon the structural elements could result in millions of dollars of rework to rectify the problems. The repair process costs the developer time and money, takes profit dollars out of the contractor's wallet, and can cause disruption in the life of the property owner. These situations can sometimes end up in a courtroom to determine where the opportunity was missed to mitigate risk upfront.
Failure Modes
According to the American Society of Heating, Refrigerating and Air-Conditioning Engineers (ASHRAE), the overwhelming majority—90 percent—of all building and building material failures involve moisture damage, with industry watchers claiming that some 80 percent of construction litigation concerns failures related to moisture.2 Structural failure can take the shape of an unhealthy home environment if mold is an issue or disrupt occupant comfort due to inconsistent surfaces affected, like an uneven floor with nail pops, squeaks, and bounce. While not all incidences of moisture intrusion or improper installation lead to severe damage, structural failure is possible. Prolonged exposure to moisture results in the weakening and decay of structural members.