Air, Water, and Moisture Management in Light Commercial Building Envelopes
Vapor Management
As mentioned previously, water can take many forms and water in its liquid state is not the only concern in managing moisture in a building. Water as vapor can also cause problems, especially when it becomes trapped in an assembly and turns to liquid, that is condensation, and wets structural assemblies. Water vapor moves by only two mechanisms—air transport and vapor diffusion. Of these two, air movement accounts for more than 98 percent of all water vapor movement in building cavities, according to the U.S. Department of Energy. Consequently, in most homes, managing air infiltration and exfiltration will be more important.
The air contains a certain amount of moisture, or water vapor, which depends on its temperature and relative humidity. Hot air could hold more moisture than cold air, hence air currents could carry significant amount of moisture into the building enclosure. Air-transported moisture must not be confused with vapor diffusion, though. Diffusion is the slow molecular movement of water vapor through porous materials and assemblies. In order for diffusion to occur there must be a driving force and a pathway. The driving force is the difference in water vapor concentration or difference in vapor pressure across an assembly; diffusion occurs through vapor permeable materials from an area of higher concentration (higher vapor pressure) to an area of lower concentration (lower vapor pressure).
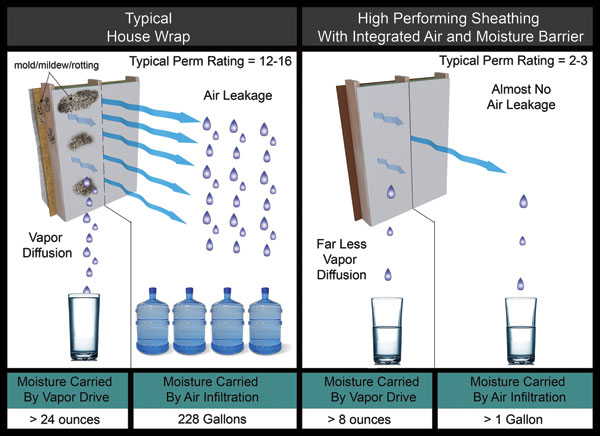
Image courtesy of Huber Engineered Woods
High performing sheathing with an integrated air and moisture barrier has far less vapor diffusion than a typical house wrap.
The accompanying illustration demonstrates magnitude of vapor carried by air versus vapor diffusion—a key reason to create an effective air barrier, not just for infiltration purposes but for vapor management as well.
In new construction, vapor retarders, or vapor barriers, can be installed to reduce vapor diffusion into the building assemblies. This is where “perm” ratings become applicable—the key physical property which distinguishes vapor diffusion retarders from other materials is permeability to water vapor. Materials which retard water vapor flow are said to be impermeable. Materials which allow water vapor to pass through them are said to be permeable. A question becomes, which perm rating is right for a water-resistive barrier? There should be a balance: A water-resistive barrier should have enough permeability to allow the wall system to adequately dry out but not so much permeability that excess water vapor is allowed into the system from the outside. A water-resistive barrier should have enough permeability to allow the wall system to adequately dry out, but not so much permeability that excess water vapor is allowed into the system from the outside. Many building codes define a vapor diffusion retarder as a material that has a permeability of one perm or less as tested under a dry cup test method. The sweet spot is considered 10 ≤ Perm Rating ≤ 20.
Solar Vapor Drive
Inward vapor movement due to solar radiation is known as solar vapor drive. Essentially what this means is that a wet surface that is heated by the sun will develop a high vapor pressure, and this can force moisture to be driven into absorbent materials.
While traditionally the prime concern was wind driven vapor drive, in today's buildings, most of which have air conditioning, vapor diffusion from outdoors can constitute an even greater problem. In addition, inward driven solar vapor drive, from the outside in, is potentially more problematic in producing mold and rot than winter vapor drive. While vapor drive will occur with higher humidity on one side of a wall, the sun is a very powerful engine that will drive moisture through most wall components. If the wall components were poorly chosen, inward vapor solar drive, can pose a substantial threat. Exterior walls must be completely sealed to prevent vapor or air from entering, which is not an easy task. Architects should never use a material on the interior that will trap moisture in the wall, like poly or vinyl wallpaper. Further, water-resistive barriers with high perm ratings can allow too much vapor to pass into the building envelope. It is better to use a forgiving water-resistive barrier that will still allow moisture to escape, but not allow too much moisture to be driven inside—this would decrease comfort levels and energy savings as the HVAC has to work harder to dehumidify moisture laden air.
The accompanying clearly illustrates the dynamics of solar vapor drive.
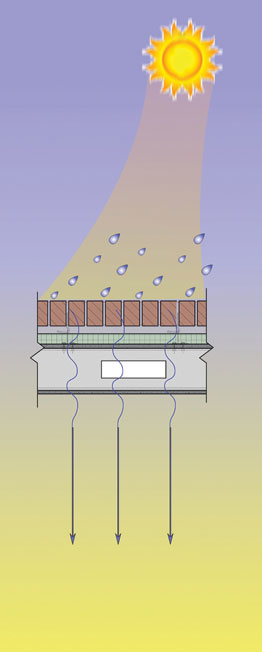
Image courtesy of Huber Engineered Woods
A wet surface that is heated by the sun will develop a high vapor pressure, and this can force moisture to be driven into absorbent materials.
Pitfalls of Today’s Control Methods
Careful attention must be paid to the installation of traditional control methods. Problems are a certainty with improper installation.
Water-Resistive Barrier
A water-resistive barrier is a thin membrane intended to resist liquid water that has penetrated behind the exterior cladding. A few rules of thumb must be followed. Proper installation is critical. Water must remain outside of the protective wrap. If installed properly, a water-resistive barrier may improve a structure's overall moisture efficiency and performance by acting as a secondary moisture drainage plane. Water-resistive barriers withstand bulk water penetration and wind-driven rain that penetrates the exterior cladding from intruding into the wall assembly. Water will be channeled down the outside surface of the water-resistive barrier, thus reducing the potential for condensation build-up in the wall assembly which reduces the likelihood of moisture problems, rot, and degradation. Water-resistive barriers come in a variety of widths and lengths as well as a variety of materials. These materials consist of polymeric-based sheets (plastic) and can include spun-bonded (fibers), cross-woven (tapes), film (sheets) or a combination thereof.
Roll or Spray-On Products
With these products, it can be difficult to achieve the proper mil consistency. There is inefficiency due to the fact that multiple layers of coating are required. The required cure time makes for a slower installation process.
Grade D Building Paper
This product does not function well as air barrier/retarder. In addition, this product is prone to tear easily, particularly if left exposed, and can be difficult to install in windy conditions.
Building Wrap
In order to function as an effective air barrier, all seams, holes, and penetrations in the building wrap must be properly sealed (including the bottom), a time consuming and laborious process. Building wrap also suffers from drawbacks of Grade D building paper, notably, it is prone to tear if left exposed, and is difficult to install in windy conditions. There is poor adhesion of flashing material and tape as well as complex and ever-changing flashing, repair, and installation details to accommodate in order to effectively deploy building wrap.
Generally speaking, these control layers must be installed properly or they can be more detrimental than beneficial. Problems range from product function and quality to complex and conflicting installation details. Some wraps and papers are of poor-quality regardless of how they are installed. Many perforated wraps, for example, result in the passage of water and air or have low abrasion and tear resistance. In macro porous perforated housewraps, the dilemma is that the macro holes in the film provide vapor permeance, but sacrifice air and water resistance. With micro-porous perforations, the conundrum becomes whether the material is sufficiently abrasion and tear resistant. Asphalt papers and felts, on the other hand, may be more moisture absorbent but less pliable.
As a result of the difficulty of installing building wrap or conventional systems, several problems can occur, including reverse flashing; building wrapped tucked into the building; improperly flashed penetrations; and flashing tape that doesn't stick. With cladding such as stone and stucco, numerous steps are required. Note that code requires two layers of Grade D paper for direct applied stone or three-coat stucco over wood based sheathing. The necessary layers include wood sheathing; a first layer of grade D paper or wrap (drain plane); a second layer of paper or wrap (bond break); wire mesh; brown coat, a scratch coat, and a finish coat.
Dried In Roof
Drying in is making a building impervious to the rain by protecting it with roofing underlayment, at least a layer of felt or a building wrap product. This is a critical step in construction as once the roof is dried in, electrical, plumbing and HVAC may begin rough installation. If the roofing felt blows off, the building is not dried in, and this causes delays in other trades. In a National Association of Home Builders survey, nearly one quarter (23 percent) of respondents cited absence of or damaged felt as a problem. Even if a small area of roof were exposed, problems could occur in between decking and felt installation. Because two trades are involved, there is a break between processes and if it rains, snows, etc. during this time, the roof goes unprotected. Felt is also difficult to install, especially on higher structures as installers have to climb up and down the building to transport rolls of felt, which constitutes a potential safety issue.