The Evolution of Water-Resistive and Air Barriers in Commercial Building Envelope Construction
System Solutions: Sheathing with Integrated WRB and AB
The ability of fiberglass mat sheathing to provide a fire- and weather-resistant substrate for multiple types of exterior cladding has made it a popular and cost-effective choice for many commercial buildings. Up until the year 2006, it was also considered to be an acceptable WRB if the joints and seams were caulked, but some seam failures of some products led to more current code requirements for WRBs and ABs. Manufacturers have responded with not just one but two different types of innovative sheathing products with code-approved WRB and AB systems integrated during their manufacture as follows:
- Method A – coated panels: This approach is based on an added manufacturing step of coating one face of fiberglass-mat-faced gypsum panels with a commercially available fluid-applied membrane under controlled conditions in the factory.
- Method B – fully integrated panels: This process fuses or marries the gypsum core to the fiberglass mat surface in a way that creates a single, monolithic WRB and AB product. More specifically, it integrates the gypsum core and fiberglass mat to form a hydrophobic, monolithic surface that blocks bulk water but allows vapor to pass through.
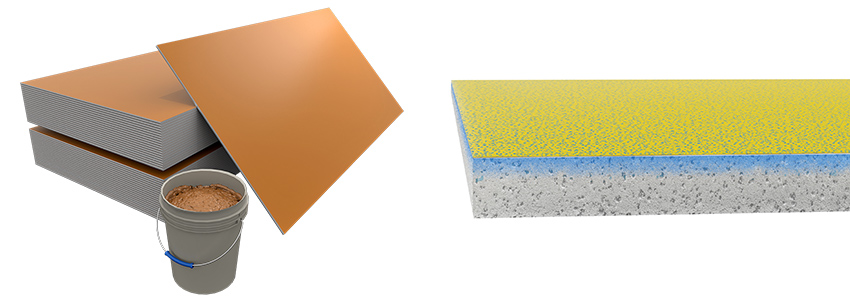
Two types of integrated sheathing are available including coated fiberglass matt gypsum panels shown on the left and core-integrated WRB and AB panels shown on the right.
These two manufacturing methods use different technologies, but both meet the code and performance requirements for use as a WB and AB provided the joints, sheathing fasteners, penetrations, opening, and material transitions are sealed in accordance with manufacturer’s instructions. They can also serve as a continuous drainage plane behind cladding. Proper detailing for drainage is subject to the professional judgement of the design professional. These claims are backed up by a variety of independent testing covering the following:
- Mechanical and physical properties: Both methods of producing integrated sheathing meet the same mechanical and physical properties of traditional gypsum sheathing. These include meeting or exceeding the requirements of ASTM C1177: Standard Specification for Glass Mat Gypsum Substrate for Use as Sheathing for characteristics such as flexural strength, nail pull resistance, water-resistance/absorption, effective stiffness, compressive strength, impact resistance, negative wind load resistance, and dimensional stability. The products also share the same properties as other gypsum board products for racking strength, thermal properties, weight, and overall performance.
- Fire resistance: Both types of integrated sheathing provide the same fire-resistant properties as other gypsum board products. These include successful testing under ASTM E119: Standard Test Method for Fire Tests of Building Construction and Materials, ASTM E136: Standard Test Method for Behavior of Materials in a Vertical Tube Furnace at 750 C, and ASTM E84: Standard Test Method for Surface Burning Characteristics of Building Materials. When 5/8-inch Type X gypsum sheathing is specified, it also meets the criteria for UL and ITS Fire-Rated Assemblies. Further, these types of exterior sheathing are noncombustible, and the manufacturers may be able to demonstrate compliance with NFPA 285 for fire-rated assemblies where a project design incorporates a tested condition.
- Water-resistive barrier testing: Among the various WRB tests that these integrated sheathing systems have passed, several are worth noting.
- ICC ES AC212: Acceptance Criteria for Water-Resistive Coatings Used as Water-Resistive Barriers over Exterior Sheathing is the standard for applied coatings by brush, roller, or spray but is also used to establish performance for integrated sheathing.
- ASTM C297: Standard Test Method for Flatwise Tensile Strength of Sandwich Constructions is a tensile bond or tensile strength test to measure the bond of a water-resistive barrier to the substrate.
- ASTM D2247: Standard Practice for Testing Water Resistance of Coatings in 100% Relative Humidity is an extreme condition test for water penetration at a treated joint.
- ASTM E331: Standard Test Method for Water Penetration of Exterior Windows, Skylights, Doors, and Curtain Walls by Uniform Static Air Pressure Difference is a four-stage, multiple-step, water-penetration chamber test using air pressure to force sprayed water through any openings and through the material itself.
- Air-barrier testing: The same integrated sheathing products are also tested for their performance as an air barrier. These have included successfully passing:
- ASTM E2178: Standard Test Method for Air Permeance of Building Materials, which is an air barrier test on products or materials to determine that the code requirements for air permeance has been met (0.004 cfm/ft2 @ 75 Pascals).
- ASTM E2357: Standard Test Method for Determining Air Leakage of Air Barrier Assemblies is testing designed to demonstrate that the product, as used in an assembly, meets code requirements for the air permeability of the assembly (0.04 cfm/ft2 @ 75 Pascals).
In short, both types of integrated sheathing have passed a full barrage of rigorous lab tests and in all cases have met or exceeded the requirements for a WRB, AB, and fire-resistant exterior sheathing.
Comparing Coated vs. Core-Integrated WRB AB Sheathing Systems
As we have seen above, both methods of producing integrated sheathing (i.e., Method A coated vs. Method B fully integrated) are excellent choices for an effective and proven exterior sheathing with an integrated WRB and AB system. However, there are several performance differences between these two types that design professionals need to be aware of.
Fully integrated systems often provide superior performance over coated systems in a number of ways. First, fully integrated systems have lower water absorption rates than coated systems when compared by weight (5 percent vs. 10 percent respectively). Fully integrated systems have zero flame spread as compared to 20 for coated systems and 0 smoke developed compared to 15 for coated systems. Both meet Class A fire ratings. The permeability ratings have been shown to be very consistent on fully integrated systems since no coating is applied—the integrated sheathing itself provides the resistance. Coated systems tend to have lower perm rates than core systems, which allow more trapped vapor to escape when a hydrophobic, monolithic surface is used that blocks bulk water but allows vapor to pass through. Note that variations exist between manufacturers on the sheathing panels and the rest of the flashing system too, so details should be verified based on manufacturers information. Finally, when using fully integrated sheathing systems, there is typically no need for additional expansion joint sealant, added membranes for rough openings, or reinforcing mesh for transitions as may be required in coated systems.
Overall, the fully integrated system carries a few more advantages than the coated systems and should be considered when specifying integrated WRB-AB Systems.