The Evolution of Water-Resistive and Air Barriers in Commercial Building Envelope Construction
Labor, Material, and Installation Savings
When using individual materials or systems to achieve the different barrier layers, more labor and time is usually needed for the installation, meaning more construction cost. When using integrated sheathing products, there is typically less time required since multiple barriers are installed at the same time (i.e., eliminating other products and installation steps), while the products may cost more or less than the aggregate of the other products. Integrated sheathing systems typically require less labor with fewer crew members because of the simplicity of installing and finishing them. Further, at least one manufacturer points out that less-specialized labor is required since any sheathing installer should be able to readily install integrated sheathing as well.
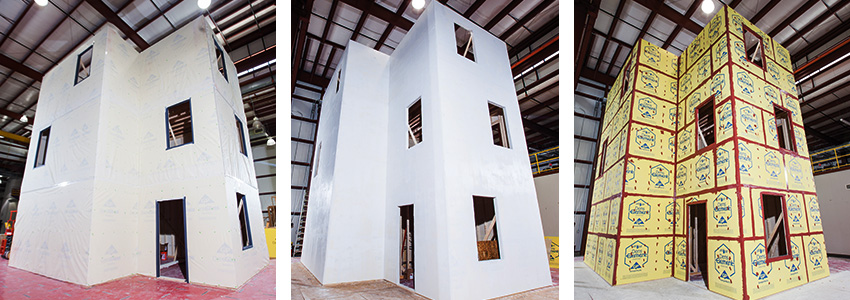
Independent testing of three different WRB and AB installations found that integrated sheathing installed in less time and with cost-saving potential.
In order to investigate these concepts, a time-motion study was undertaken by Home Innovation Research Labs. It compared installation time and material usage for three different types of systems, namely 1) sheathing plus joint treatment plus building wrap; 2) sheathing plus joint treatment plus fluid-applied membrane; and 3) integrated sheathing with WRB-AB system plus joint treatment. The study determined that the integrated WRB-AB gypsum sheathing system was completed faster than the other two methods, with one installation step eliminated altogether. It noted that the integrated sheathing was installed 25 percent faster than the building wrap in the study and 40 percent faster than the fluid-applied membrane in the study. Material savings were also found to be possible.
Using these findings, we can create a hypothetical project example based on a building with 20,000 gross square feet of wall area that used integrated sheathing instead of individual WRB and AB systems. Under that scenario, it can be projected that approximately 22,500 square foot of building wrap (plus tapes and staples) would not be used. Similarly, compared to fluid-applied membrane systems, approximately 125 gallons for thin-mil fluid applications (160 square foot per gallon) or up to 267 gallons (75 square foot per gallon) for thick-mil applications would not be used. Other potential savings include equipment use and reduced safety risks. Overall, labor, material, and time savings have been projected as quite possible using integrated WRB-AB gypsum sheathing systems instead of traditional WRBs and ABs, all without jeopardizing performance. In fact, the manufactured nature of the barriers provides better quality control and reduces the risk of on-site mistakes and any compromise in performance.