This CE Center article is no longer eligible for receiving credits.
Commercial building envelopes have evolved in recent decades, driven in large part toward better performance for durability, resilience, and energy efficiency. Some of the motivation for these results has been driven by code requirements, others by green building standards, and some simply by owner demands for better performance, faster installation, and labor efficiencies. In response, a number of building products have used innovation backed up by performance testing to address the particular need to create the four barriers needed as part of any building enclosure, namely water-resistive barriers (WRBs), air barriers (ABs), thermal barriers, and vapor retarders. In particular, there has been a rapid acceleration of innovation in air barriers and water-resistive barriers recently.
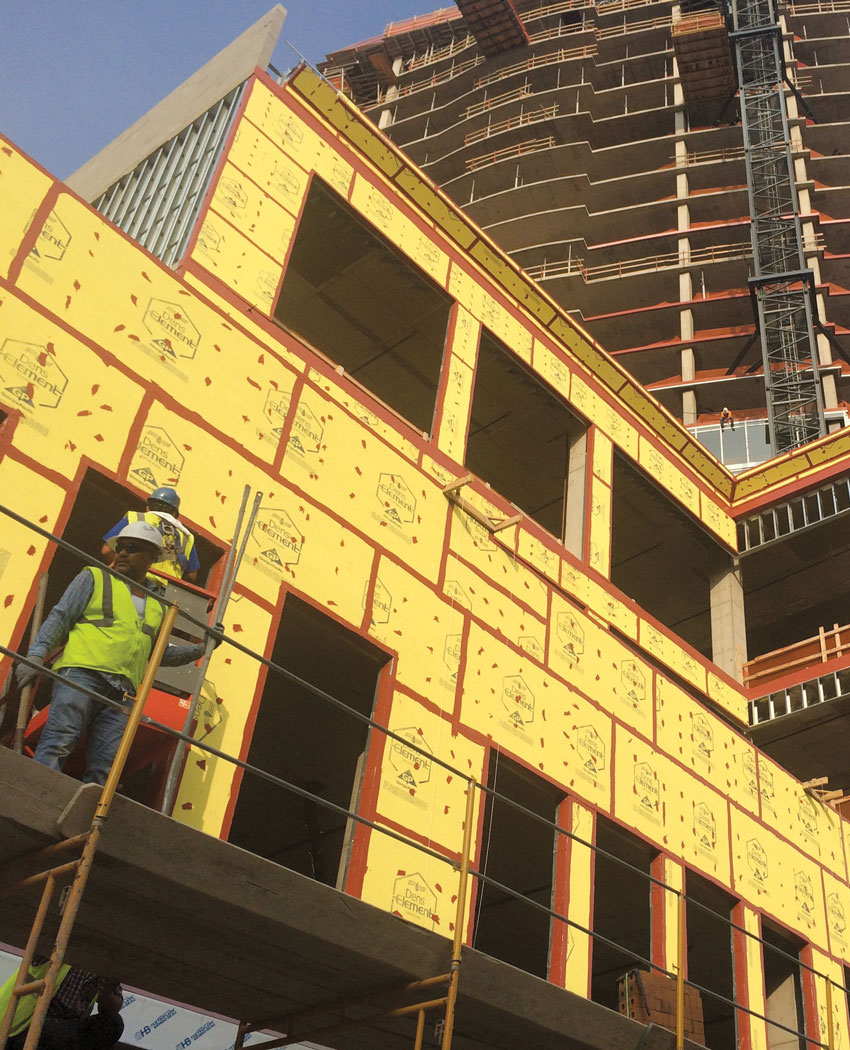
All images courtesy of Georgia-Pacific Gypsum
Commercial buildings require continuous air and water-resistant barriers in order to meet codes. The means to provide those barriers has evolved since the 1960s with integrated solutions that save time and costs while delivering high performance.
Therefore, in this course, we will focus on helping architects get up to speed and stay abreast of some of the latest advances in these barriers. Of particular note, all-in-one, integrated gypsum sheathing systems will be looked at that include WRB and AB systems during manufacturing as alternatives to field-applied water- and air-barrier systems. These integrated systems can speed up installation and save time and money during construction. And, since they have been shown to reduce improper field installations, they provide greater reliability and less professional risk compared to separate field-applied solutions.
Code-Required Barriers to Protect the Building Envelope
Typically, each of the four common barriers in a building envelope have been treated independently by designers, contractors, and product manufacturers. Indeed, even the building codes address them individually, as we will here as follows.
Water-Resistive Barriers (WRBs)
This barrier is intended to do exactly what its name implies: resist bulk water from penetrating into a wall assembly from the exterior side. WRBs are specifically required by the International Building Code (IBC) and the International Residential Code (IRC) for the purpose of protecting the materials and components of a wall assembly from water that may penetrate past the exterior cladding. Without such protection, unwanted water penetration over time can intrude into the assembly, thus producing deterioration, degradation, and even failure, any of which can render a building unsafe or unhealthy for occupancy. To avoid those conditions, a properly tested WRB is typically called for behind the exterior cladding of a wall assembly on the face of the sheathing or similar surface. The wall assembly then needs to be designed to allow the WRB to function as a water-control layer by channeling water down its exterior face to drain harmlessly away to the exterior. In so doing, it reduces or eliminates potential water and moisture problems inside a wall assembly, particularly in cavity wall framed construction.
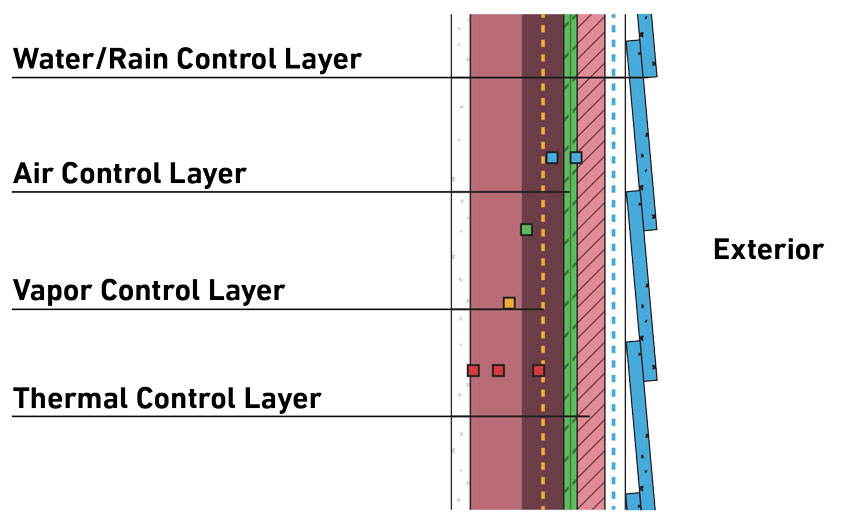
The four barriers, or control layers, of an exterior wall envelope all need to be understood independently of each other
Continuous Air Barriers (ABs)
This barrier has received a lot of attention in recent years since unwanted air infiltration has been seen as both a significant drain on energy performance and a means to transfer unwanted air-borne moisture into buildings. In particular, the International Energy Conservation Code (IECC) now has very specific, mandatory requirements for providing continuous air barriers in building envelopes aimed at restricting or preventing the passage of air in order to assure minimum levels of code required energy performance. The code leaves it to the architect to determine the best location of the AB, whether on an interior or exterior side of a construction assembly, but does indicate that it needs to follow the same line as the building thermal barrier. Its purpose is to essentially “wrap” the building shell to prevent air passing from the outside to the inside due to wind, building “stack effects,” or mechanical ventilation pressure differences. To achieve this in exterior walls, the AB is most typically located behind wall cladding on the face of sheathing or similar surface, just like a WRB.
It is worth noting that the IECC identifies 16 common building materials that qualify as an acceptable air barrier, including such things as plywood, OSB, roof membranes, concrete, masonry, metals, and gypsum board, among others. This makes sense since it is hard to imagine air blowing directly through any of these materials. It clarifies the requirement and also allows for other materials to be used as an approved air barrier if it can show by testing per ASTM E2178 that it achieves an air-penetration rate of no more than 0.004 cfm/ft2 (four thousandths of a cubic feet per minute per square foot of material) when tested at a pressure difference of 75 Pascals. This is fairly good news for most materials, but there is an additional requirement that cannot be overlooked, namely the seams, joints, openings, or penetrations of those materials. Under the IECC, in order to qualify as an acceptable continuous air barrier, the entire assembly of materials and products must restrict air penetration. In this case, the complete assembly must be tested, not just the sheathing or similar product, and demonstrate an air-penetration rate of no more than 0.04 cfm/ft2 (four hundredths of a cubic foot per minute per square foot of material), also when tested at a pressure difference of 75 Pascals. While the requirement for the assembly is less stringent that for the materials, it is nonetheless a dramatic, measurable improvement over previous versions of the IECC, which did not fully address an AB. As a result, it means that much more attention needs to be paid to the continuity of the AB and that all seams, joints, penetrations, and openings must be carefully detailed and properly sealed.
Vapor Retarders
While WRBs address bulk water and ABs address airborne moisture from one side of an assembly, there is also a concern for vapor penetration from the other side of the assembly. Therefore, the IBC and IRC require the use of vapor retarders to protect the building construction on both sides of an assembly. Most commonly, a vapor retarder is required in colder climates and should be installed on the interior face of an exterior wall, roof, or floor assembly. The intent is to prevent warm, moist air from penetrating into the assembly and condensing to form water that can become trapped and cause damage.
The determination of whether or not a vapor retarder is required is based on the location of the building within any of the eight climate zones identified and cross referenced in the energy code (IECC). Then, depending on the location, one of three types of vapor retarders may be dictated. A Type I retarder provides virtually no permeability of vapor while a Type II allows some permeability. A Type III vapor, retarder slows the passage of vapor, or diffusion, but allows more permeability than either Type I or Type II. In this case, it is presumed that any vapor that enters will also exit.
Thermal Barriers
Restricting the transfer of heat through a building envelope (i.e., from inside to outside during heating season or from outside to inside during cooling season) is critical to good energy performance in a building. Therefore, the IECC has always required a continuous thermal barrier to control heat energy flow and reduce energy usage in buildings. The level of performance of this barrier is expressed in tested R-values for insulation products or based on U-factor analysis of an entire assembly. In practice, that means that insulation is used to form the thermal barrier and can be placed between studs and framing or installed continuously either on the inside or outside face of an assembly. The specific assembly and the materials used can be quite varied and are the purview of the architect to determine based on the needs of a particular building. Whatever the design, however, thermal performance must be detailed and demonstrated to show code compliance.
As noted earlier, products are typically available to provide one of these four barriers. However, some products have been formulated and tested to provide more than one type of barrier and are promoted to be used that way. That can cause confusion over how certain products should be used and whether or not other products are needed to assure all of the barriers are provided. In order to be sure that any particular assembly meets all of the needed performance characteristics, therefore, it is important that design professionals understand the four separate barrier functions and incorporate them appropriately in construction assemblies.
Commercial building envelopes have evolved in recent decades, driven in large part toward better performance for durability, resilience, and energy efficiency. Some of the motivation for these results has been driven by code requirements, others by green building standards, and some simply by owner demands for better performance, faster installation, and labor efficiencies. In response, a number of building products have used innovation backed up by performance testing to address the particular need to create the four barriers needed as part of any building enclosure, namely water-resistive barriers (WRBs), air barriers (ABs), thermal barriers, and vapor retarders. In particular, there has been a rapid acceleration of innovation in air barriers and water-resistive barriers recently.
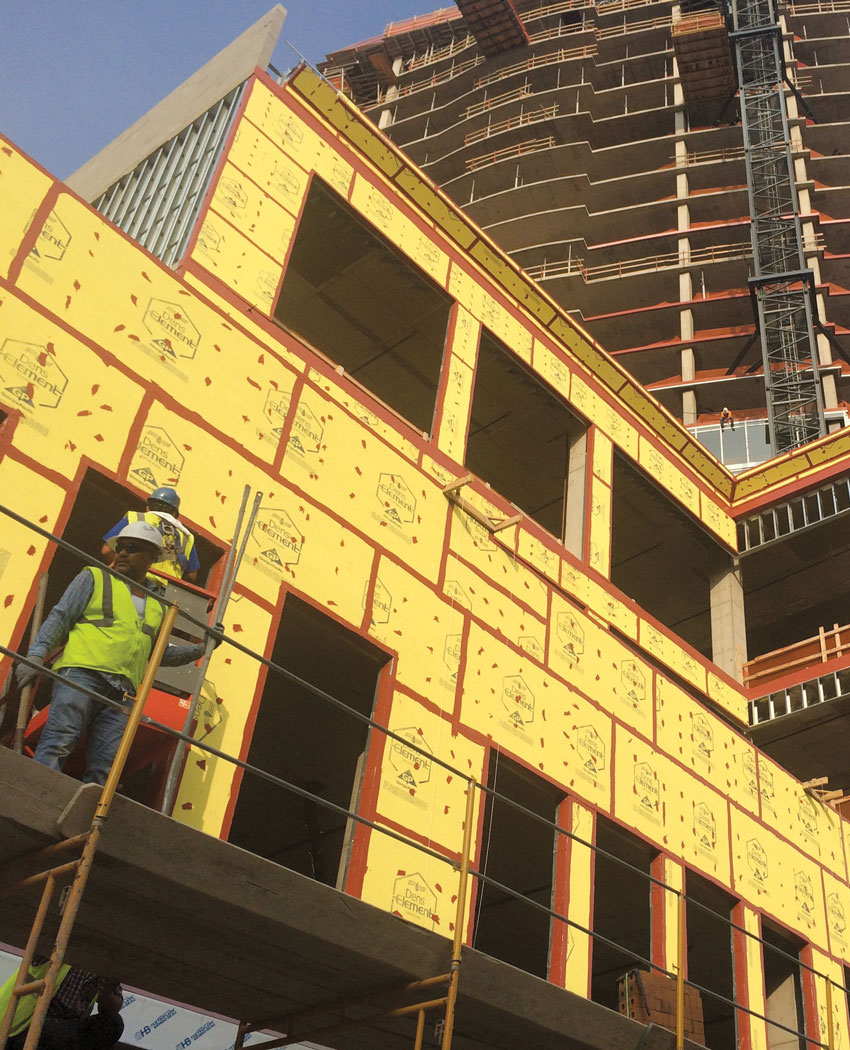
All images courtesy of Georgia-Pacific Gypsum
Commercial buildings require continuous air and water-resistant barriers in order to meet codes. The means to provide those barriers has evolved since the 1960s with integrated solutions that save time and costs while delivering high performance.
Therefore, in this course, we will focus on helping architects get up to speed and stay abreast of some of the latest advances in these barriers. Of particular note, all-in-one, integrated gypsum sheathing systems will be looked at that include WRB and AB systems during manufacturing as alternatives to field-applied water- and air-barrier systems. These integrated systems can speed up installation and save time and money during construction. And, since they have been shown to reduce improper field installations, they provide greater reliability and less professional risk compared to separate field-applied solutions.
Code-Required Barriers to Protect the Building Envelope
Typically, each of the four common barriers in a building envelope have been treated independently by designers, contractors, and product manufacturers. Indeed, even the building codes address them individually, as we will here as follows.
Water-Resistive Barriers (WRBs)
This barrier is intended to do exactly what its name implies: resist bulk water from penetrating into a wall assembly from the exterior side. WRBs are specifically required by the International Building Code (IBC) and the International Residential Code (IRC) for the purpose of protecting the materials and components of a wall assembly from water that may penetrate past the exterior cladding. Without such protection, unwanted water penetration over time can intrude into the assembly, thus producing deterioration, degradation, and even failure, any of which can render a building unsafe or unhealthy for occupancy. To avoid those conditions, a properly tested WRB is typically called for behind the exterior cladding of a wall assembly on the face of the sheathing or similar surface. The wall assembly then needs to be designed to allow the WRB to function as a water-control layer by channeling water down its exterior face to drain harmlessly away to the exterior. In so doing, it reduces or eliminates potential water and moisture problems inside a wall assembly, particularly in cavity wall framed construction.
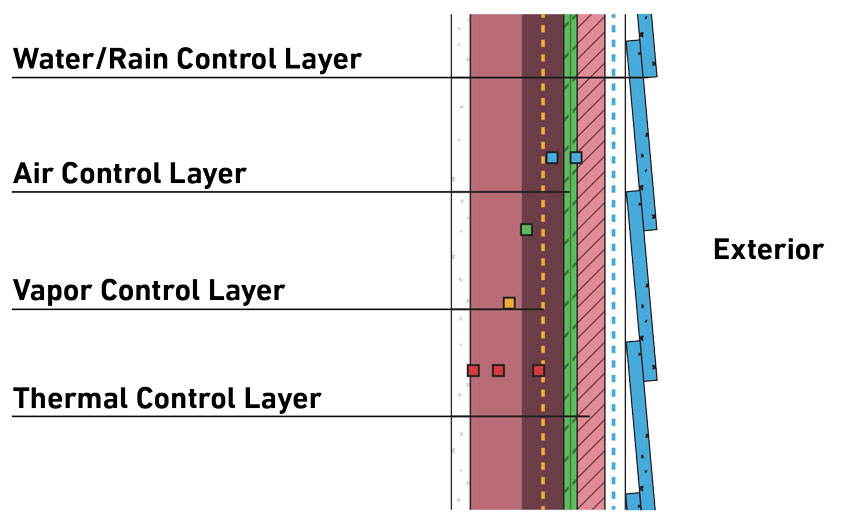
The four barriers, or control layers, of an exterior wall envelope all need to be understood independently of each other
Continuous Air Barriers (ABs)
This barrier has received a lot of attention in recent years since unwanted air infiltration has been seen as both a significant drain on energy performance and a means to transfer unwanted air-borne moisture into buildings. In particular, the International Energy Conservation Code (IECC) now has very specific, mandatory requirements for providing continuous air barriers in building envelopes aimed at restricting or preventing the passage of air in order to assure minimum levels of code required energy performance. The code leaves it to the architect to determine the best location of the AB, whether on an interior or exterior side of a construction assembly, but does indicate that it needs to follow the same line as the building thermal barrier. Its purpose is to essentially “wrap” the building shell to prevent air passing from the outside to the inside due to wind, building “stack effects,” or mechanical ventilation pressure differences. To achieve this in exterior walls, the AB is most typically located behind wall cladding on the face of sheathing or similar surface, just like a WRB.
It is worth noting that the IECC identifies 16 common building materials that qualify as an acceptable air barrier, including such things as plywood, OSB, roof membranes, concrete, masonry, metals, and gypsum board, among others. This makes sense since it is hard to imagine air blowing directly through any of these materials. It clarifies the requirement and also allows for other materials to be used as an approved air barrier if it can show by testing per ASTM E2178 that it achieves an air-penetration rate of no more than 0.004 cfm/ft2 (four thousandths of a cubic feet per minute per square foot of material) when tested at a pressure difference of 75 Pascals. This is fairly good news for most materials, but there is an additional requirement that cannot be overlooked, namely the seams, joints, openings, or penetrations of those materials. Under the IECC, in order to qualify as an acceptable continuous air barrier, the entire assembly of materials and products must restrict air penetration. In this case, the complete assembly must be tested, not just the sheathing or similar product, and demonstrate an air-penetration rate of no more than 0.04 cfm/ft2 (four hundredths of a cubic foot per minute per square foot of material), also when tested at a pressure difference of 75 Pascals. While the requirement for the assembly is less stringent that for the materials, it is nonetheless a dramatic, measurable improvement over previous versions of the IECC, which did not fully address an AB. As a result, it means that much more attention needs to be paid to the continuity of the AB and that all seams, joints, penetrations, and openings must be carefully detailed and properly sealed.
Vapor Retarders
While WRBs address bulk water and ABs address airborne moisture from one side of an assembly, there is also a concern for vapor penetration from the other side of the assembly. Therefore, the IBC and IRC require the use of vapor retarders to protect the building construction on both sides of an assembly. Most commonly, a vapor retarder is required in colder climates and should be installed on the interior face of an exterior wall, roof, or floor assembly. The intent is to prevent warm, moist air from penetrating into the assembly and condensing to form water that can become trapped and cause damage.
The determination of whether or not a vapor retarder is required is based on the location of the building within any of the eight climate zones identified and cross referenced in the energy code (IECC). Then, depending on the location, one of three types of vapor retarders may be dictated. A Type I retarder provides virtually no permeability of vapor while a Type II allows some permeability. A Type III vapor, retarder slows the passage of vapor, or diffusion, but allows more permeability than either Type I or Type II. In this case, it is presumed that any vapor that enters will also exit.
Thermal Barriers
Restricting the transfer of heat through a building envelope (i.e., from inside to outside during heating season or from outside to inside during cooling season) is critical to good energy performance in a building. Therefore, the IECC has always required a continuous thermal barrier to control heat energy flow and reduce energy usage in buildings. The level of performance of this barrier is expressed in tested R-values for insulation products or based on U-factor analysis of an entire assembly. In practice, that means that insulation is used to form the thermal barrier and can be placed between studs and framing or installed continuously either on the inside or outside face of an assembly. The specific assembly and the materials used can be quite varied and are the purview of the architect to determine based on the needs of a particular building. Whatever the design, however, thermal performance must be detailed and demonstrated to show code compliance.
As noted earlier, products are typically available to provide one of these four barriers. However, some products have been formulated and tested to provide more than one type of barrier and are promoted to be used that way. That can cause confusion over how certain products should be used and whether or not other products are needed to assure all of the barriers are provided. In order to be sure that any particular assembly meets all of the needed performance characteristics, therefore, it is important that design professionals understand the four separate barrier functions and incorporate them appropriately in construction assemblies.
Evolution of Common WRB and AB Materials
One of the most common building envelope construction types for commercial and residential buildings is based on using wood or metal framing to create exterior walls. That framing is then covered on the outside face with a sheathing panel secured to the framing studs with openings cut as needed for windows, doors, and other openings. This sheathing has formed the basis for most of the water resistance and air resistance in wall assemblies since the 1960s. In commercial construction, the most common sheathing that has been used are gypsum-based products, which are recognized by codes to serve as air-barrier materials. In order to make that air barrier continuous as well as create a full water-resistant barrier, there have been a continuous series of innovations over the past six decades that can be summarized as follows.

The evolution of water-resistant and air barriers relied on innovations in different types of sheathing technology in the 1960s, 70s, and 80s.
1960s: Paper-faced gypsum sheathing was the norm without the use of any particular WRB. This provided fire resistance in exterior wall assemblies and a basic air barrier, but problems related to water and moisture emerged, including delamination of the paper.
1970s: Asphalt-saturated felt paper was identified in building codes to be installed as a WRB. Today, it is still the only code-listed product for a WRB while allowing others that meet tested performance criteria. While adding felt paper over gypsum board is effective at shedding water and protecting the paper surface, it is not effective as an air barrier, meaning that the joints and seams of the gypsum panels all needed to be sealed.
1980s: As concerns about energy conservation and product durability emerged in the 1980s, several innovative products came onto the market. The first was gypsum board sheathing that replaced the paper facing with a fiberglass mat facing. This meant that the amount of time that gypsum sheathing could be exposed to normal weather was dramatically increased compared to paper-faced sheathing. The fiberglass mat surface also provided a basic but effective WRB surface. The second innovation came in the form of fibrous building wraps used on both residential and commercial construction to create primarily an air barrier, although some provided a WRB as well.

Innovation of water-resistant and air barriers continued with the development of specialty products during the 1980s through to today.
1990s: A number of other rigid board stock products emerged on the market to act as a sheathing or substrate behind cladding on an exterior wall. In some cases these were fiber-based products, and in other cases they were variations on rigid insulation boards. Some purported to be able to provide multiple barriers, including WRB, AB and thermal barrier properties. Most needed to be covered promptly since they could deteriorate quickly in weather, sun, or wind.
2000s: While building wraps remained popular over most sheathings, they had some significant limitations with installation that raised concerns about their ability to be truly continuous. There were also some International Building Code changes in 2006 that required WRBs to be applied to the sheathing. In response, some other materials such as heavier-adhered membranes applied in the field over the sheathing were sometimes used. In other cases, fluid-applied membranes that were sprayed or brushed over fiberglass mat gypsum sheathing became preferred to assure performance. Most of the fluid-applied membranes required a thick, measured layer to be field applied but offered full continuity as both a WRB plus an AB since they could readily conform to any irregularities or variations in the underlying substrate. Adhered membranes were bulky and more labor intensive to install over any irregular areas.
2010s: As the technology for fluid-applied membrane barriers developed, they became more effective, thus allowing thinner applications to be tested, and were shown to be highly effective still as both a WRB and an AB. They were still applied in the field and dependent on the skills of the applicators.
Current: In light of the above evolution, some gypsum manufacturers have developed, and now offer, the latest innovation in this technology, namely, incorporating both a WRB and AB directly into fiberglass-mat-faced gypsum sheathing. In order to assure continuity in an assembly, they also offer a complete system of compatible liquid flashing materials to completely seal joints, seams, openings, penetrations, etc. This reduces the dependence on a field installation for effectiveness while taking advantage of the best properties of all products involved.
While the trend of improvement and innovation is clear in this area, not all design professionals have kept up with the progression. This puts them at a disadvantage and potential risk for not specifying the best available solution for a particular project. This condition is compounded by the fact that all of the types of products discussed above are still available and used to one degree or another today.
In order to help with an assessment of these different solutions, the following advantages and disadvantages should be considered for each.
- Building wraps and asphalt felt: As products, these have the advantages of working well as either a WRB or AB, and they are well-known, fairly cost-effective, and straightforward to install in almost any weather condition. They are also usually vapor permeable, meaning that any vapor trapped within the assembly can escape back out through them. Their disadvantages lie not in the product, then, but in their installation during construction. All require fasteners or staples to hold them in place, which causes holes that compromise their ability to act as a WRB. They are also difficult to seal in order to create a truly continuous AB. And as anyone who has visited a construction site where building wraps are left exposed can attest, they are prone to flutter in the wind, which can create larger holes, rips, tears, or complete separation.

Asphaltic felt paper is the only water barrier specifically mentioned in building codes although other products that can demonstrate equivalent, tested performance are acceptable as well.
- Fluid-applied membranes: The multiple capabilities of fluid-applied membranes gives them the advantage of potentially acting as both a WRB plus an AB when covering over sheathing. They are widely available, seal continuously around rough areas and openings, and have a fairly quick installation time through spraying or rolling. Their disadvantages are found in the field in the form of weather limitations for application, the possible need for sealing joints and fasteners first, plus the control of the application thickness for uniformity and effectiveness. They also require careful review of the manufacturer’s information to be sure that permeability and performance match expectations.
- Adhered membranes: Installing an adhered membrane over sheathing may provide both WRB plus AB protection in a consistent, manufactured thickness. Since adhesives are used, no fasteners are required and no joint sealing is needed ahead of time. They have the disadvantages of being more labor intensive to cut and install the membrane, usually require a primer first for good adhesion, and may be prone to wrinkling or poor adhesion if not installed well. Further, termination mastics and accessories are often needed along with some sequence planning to be sure they are solving moisture problems and not causing them. They also have weather limitations, often create a lot of scrap and waste on-site, and the permeability can be impacted by the primer application.
- Rigid board stock: This type of sheathing, particularly if it has some insulation capabilities, may provide a thermal barrier, WRB, and AB all in one product if the joints are properly sealed and it meets the requirements for continuous insulation defined by codes. It can also be lightweight and easy to install. Their downside comes from the comparatively fragile nature of the materials, which makes them easy to puncture, prone to movement, and with greater potential for compromising the WRB or AB properties. Since many are made of petro-chemical elements, they are prone to burn or melt. They also typically require special fasteners and/or washers for installation.
In short, while all of the above common choices may meet the material requirements for different barriers, a closer look at their installation and suitability for different projects can reveal some significant limitations. They will also have variations in the time they take to install and their corresponding costs. Having considered all of these other options, we will next take a more detailed look at the most current technology—integrated sheathing.
System Solutions: Sheathing with Integrated WRB and AB
The ability of fiberglass mat sheathing to provide a fire- and weather-resistant substrate for multiple types of exterior cladding has made it a popular and cost-effective choice for many commercial buildings. Up until the year 2006, it was also considered to be an acceptable WRB if the joints and seams were caulked, but some seam failures of some products led to more current code requirements for WRBs and ABs. Manufacturers have responded with not just one but two different types of innovative sheathing products with code-approved WRB and AB systems integrated during their manufacture as follows:
- Method A – coated panels: This approach is based on an added manufacturing step of coating one face of fiberglass-mat-faced gypsum panels with a commercially available fluid-applied membrane under controlled conditions in the factory.
- Method B – fully integrated panels: This process fuses or marries the gypsum core to the fiberglass mat surface in a way that creates a single, monolithic WRB and AB product. More specifically, it integrates the gypsum core and fiberglass mat to form a hydrophobic, monolithic surface that blocks bulk water but allows vapor to pass through.
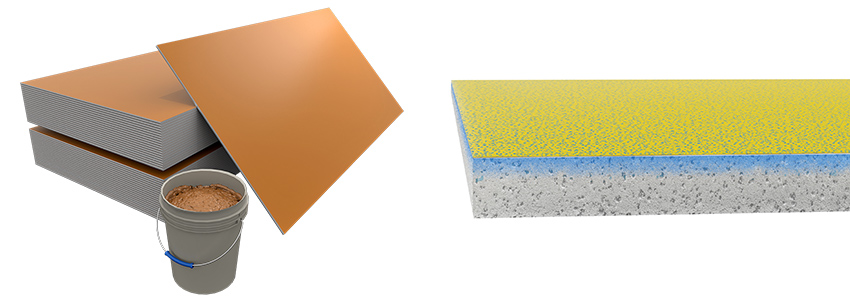
Two types of integrated sheathing are available including coated fiberglass matt gypsum panels shown on the left and core-integrated WRB and AB panels shown on the right.
These two manufacturing methods use different technologies, but both meet the code and performance requirements for use as a WB and AB provided the joints, sheathing fasteners, penetrations, opening, and material transitions are sealed in accordance with manufacturer’s instructions. They can also serve as a continuous drainage plane behind cladding. Proper detailing for drainage is subject to the professional judgement of the design professional. These claims are backed up by a variety of independent testing covering the following:
- Mechanical and physical properties: Both methods of producing integrated sheathing meet the same mechanical and physical properties of traditional gypsum sheathing. These include meeting or exceeding the requirements of ASTM C1177: Standard Specification for Glass Mat Gypsum Substrate for Use as Sheathing for characteristics such as flexural strength, nail pull resistance, water-resistance/absorption, effective stiffness, compressive strength, impact resistance, negative wind load resistance, and dimensional stability. The products also share the same properties as other gypsum board products for racking strength, thermal properties, weight, and overall performance.
- Fire resistance: Both types of integrated sheathing provide the same fire-resistant properties as other gypsum board products. These include successful testing under ASTM E119: Standard Test Method for Fire Tests of Building Construction and Materials, ASTM E136: Standard Test Method for Behavior of Materials in a Vertical Tube Furnace at 750 C, and ASTM E84: Standard Test Method for Surface Burning Characteristics of Building Materials. When 5/8-inch Type X gypsum sheathing is specified, it also meets the criteria for UL and ITS Fire-Rated Assemblies. Further, these types of exterior sheathing are noncombustible, and the manufacturers may be able to demonstrate compliance with NFPA 285 for fire-rated assemblies where a project design incorporates a tested condition.
- Water-resistive barrier testing: Among the various WRB tests that these integrated sheathing systems have passed, several are worth noting.
- ICC ES AC212: Acceptance Criteria for Water-Resistive Coatings Used as Water-Resistive Barriers over Exterior Sheathing is the standard for applied coatings by brush, roller, or spray but is also used to establish performance for integrated sheathing.
- ASTM C297: Standard Test Method for Flatwise Tensile Strength of Sandwich Constructions is a tensile bond or tensile strength test to measure the bond of a water-resistive barrier to the substrate.
- ASTM D2247: Standard Practice for Testing Water Resistance of Coatings in 100% Relative Humidity is an extreme condition test for water penetration at a treated joint.
- ASTM E331: Standard Test Method for Water Penetration of Exterior Windows, Skylights, Doors, and Curtain Walls by Uniform Static Air Pressure Difference is a four-stage, multiple-step, water-penetration chamber test using air pressure to force sprayed water through any openings and through the material itself.
- Air-barrier testing: The same integrated sheathing products are also tested for their performance as an air barrier. These have included successfully passing:
- ASTM E2178: Standard Test Method for Air Permeance of Building Materials, which is an air barrier test on products or materials to determine that the code requirements for air permeance has been met (0.004 cfm/ft2 @ 75 Pascals).
- ASTM E2357: Standard Test Method for Determining Air Leakage of Air Barrier Assemblies is testing designed to demonstrate that the product, as used in an assembly, meets code requirements for the air permeability of the assembly (0.04 cfm/ft2 @ 75 Pascals).
In short, both types of integrated sheathing have passed a full barrage of rigorous lab tests and in all cases have met or exceeded the requirements for a WRB, AB, and fire-resistant exterior sheathing.
Comparing Coated vs. Core-Integrated WRB AB Sheathing Systems
As we have seen above, both methods of producing integrated sheathing (i.e., Method A coated vs. Method B fully integrated) are excellent choices for an effective and proven exterior sheathing with an integrated WRB and AB system. However, there are several performance differences between these two types that design professionals need to be aware of.
Fully integrated systems often provide superior performance over coated systems in a number of ways. First, fully integrated systems have lower water absorption rates than coated systems when compared by weight (5 percent vs. 10 percent respectively). Fully integrated systems have zero flame spread as compared to 20 for coated systems and 0 smoke developed compared to 15 for coated systems. Both meet Class A fire ratings. The permeability ratings have been shown to be very consistent on fully integrated systems since no coating is applied—the integrated sheathing itself provides the resistance. Coated systems tend to have lower perm rates than core systems, which allow more trapped vapor to escape when a hydrophobic, monolithic surface is used that blocks bulk water but allows vapor to pass through. Note that variations exist between manufacturers on the sheathing panels and the rest of the flashing system too, so details should be verified based on manufacturers information. Finally, when using fully integrated sheathing systems, there is typically no need for additional expansion joint sealant, added membranes for rough openings, or reinforcing mesh for transitions as may be required in coated systems.
Overall, the fully integrated system carries a few more advantages than the coated systems and should be considered when specifying integrated WRB-AB Systems.
Labor, Material, and Installation Savings
When using individual materials or systems to achieve the different barrier layers, more labor and time is usually needed for the installation, meaning more construction cost. When using integrated sheathing products, there is typically less time required since multiple barriers are installed at the same time (i.e., eliminating other products and installation steps), while the products may cost more or less than the aggregate of the other products. Integrated sheathing systems typically require less labor with fewer crew members because of the simplicity of installing and finishing them. Further, at least one manufacturer points out that less-specialized labor is required since any sheathing installer should be able to readily install integrated sheathing as well.
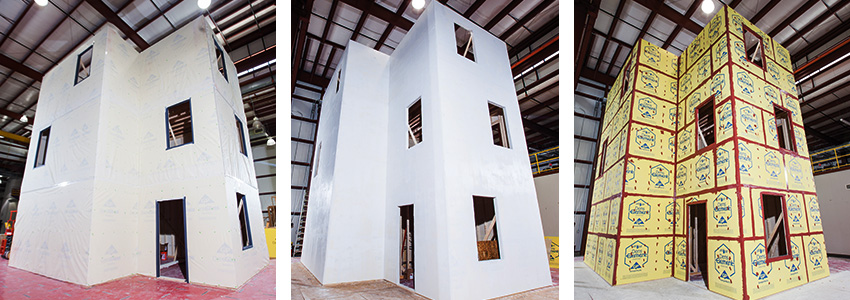
Independent testing of three different WRB and AB installations found that integrated sheathing installed in less time and with cost-saving potential.
In order to investigate these concepts, a time-motion study was undertaken by Home Innovation Research Labs. It compared installation time and material usage for three different types of systems, namely 1) sheathing plus joint treatment plus building wrap; 2) sheathing plus joint treatment plus fluid-applied membrane; and 3) integrated sheathing with WRB-AB system plus joint treatment. The study determined that the integrated WRB-AB gypsum sheathing system was completed faster than the other two methods, with one installation step eliminated altogether. It noted that the integrated sheathing was installed 25 percent faster than the building wrap in the study and 40 percent faster than the fluid-applied membrane in the study. Material savings were also found to be possible.
Using these findings, we can create a hypothetical project example based on a building with 20,000 gross square feet of wall area that used integrated sheathing instead of individual WRB and AB systems. Under that scenario, it can be projected that approximately 22,500 square foot of building wrap (plus tapes and staples) would not be used. Similarly, compared to fluid-applied membrane systems, approximately 125 gallons for thin-mil fluid applications (160 square foot per gallon) or up to 267 gallons (75 square foot per gallon) for thick-mil applications would not be used. Other potential savings include equipment use and reduced safety risks. Overall, labor, material, and time savings have been projected as quite possible using integrated WRB-AB gypsum sheathing systems instead of traditional WRBs and ABs, all without jeopardizing performance. In fact, the manufactured nature of the barriers provides better quality control and reduces the risk of on-site mistakes and any compromise in performance.
Conclusion
We have looked at a full range of options and the evolution of systems for providing code-required water-resistive barriers and air barriers in commercial exterior wall construction. Integrated sheathing is the latest manufacturing process and product improvement in a field that has had a history of impactful innovation for the past 70 years. By way of summary, the following charts compare all of the different systems we have discussed from several aspects. Design professionals are encouraged to assess these attributes and select the ones best suited for their particular projects.
Peter J. Arsenault, FAIA, NCARB, LEED AP, is a nationally known architect, consultant, continuing education presenter, and prolific author advancing building performance through better design. www.pjaarch.com, www.linkedin.com/in/pjaarch