BIM Comes to Masonry
The Landscape Today
Analytical models do exist, however, to assist in the design and installation of architectural masonry products. A few proprietary services offer a host of advantages in reducing time, cost, and potential problems in building complicated masonry jobs. The landscape is also changing as masonry industry stakeholders join forces to collaborate on creating and implementing new generation BIM-M, or BIM for Masonry.
Current Software Modeling Tools
Post-bid commercial software modeling programs do exist to assist in the ordering and installation of architectural masonry products. The models help the project team understand the products, order them accurately, resolve design issues related to CMU, layout bond patterns, stage complex orders, and increase productivity in the field. Further, the software enables practitioners to troubleshoot unusual design conditions such as an atypical bond pattern, bullnoses, score patterns, multiple textures, cove bases, arches, radius walls, or all of the above. The most successful technologies build models one unit at a time, as is done in the field—an approach that allows effective handling of the complexity of glazed CMU, ground face CMU, stone veneer, or other types of prefinished masonry units. Multiple colors, multiple textures, and intricate bond patterns can be modeled as well. Coded models facilitate an understanding of how precisely to build difficult conditions, with 3D layout drawings showing all conditions in the model to increase productivity in the field. “The take off detail is invaluable of course,” says Rick Riley of Hoffman Cortes Masonry, about this type of model. “The shop drawings save time and material in the field. They are like having a set of instructions on the wall. The foreman can give a copy to the b'layers on the wall and not worry about what is being set.”
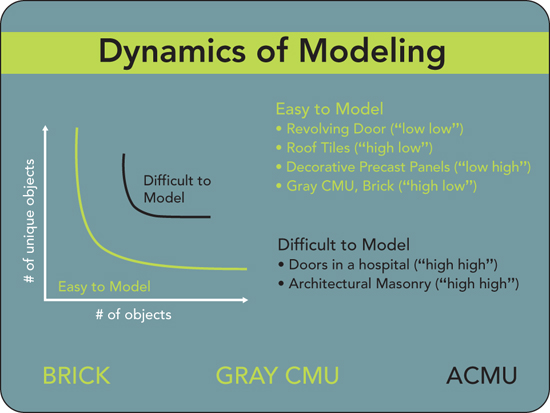
Image courtesy of Oldcastle® Architectural
It is important to point out, however, that the complexity of this type of quality modeling is primarily a post-bid activity. Design time masonry modeling is still in development but is an achievable ambition which the industry is actively pursuing.
BIM-M
BIM-M, or BIM for Masonry, is in the works, with several funding organizations blazing the trail. The Mason Contractors Association of America (MCAA), the National Concrete Manufacturer's Association (NCMA), the International Union of Bricklayers and Allied Craftworkers (BAC), Western States Clay Products Association, the International Masonry Institute (IMI), and The Masonry Society (TMS) are recommending that software developers include masonry in BIM software. Working with the Georgia Institute of Technology, the group has completed a roadmap to achieve that goal and is now working on realizing their vision, all with the help of industry individuals including masonry contractors, material suppliers, structural engineers, architects, and general contractors. Their rationale: If masonry is not included in BIM software as steel and precast concrete are, masonry may appear to be difficult to work with, and find itself in a bad position competitively.
Phase 2, which involves creating a digital library of masonry units and accessories in a common format, is currently ongoing. In subsequent phases, the group will prepare proposals for software vendors to include more masonry capabilities into their products and, ultimately, implement new software for the masonry industry. These efforts are slated to begin in 2015 and 2016, respectively. A first-generation BIM(-M) software for masonry is anticipated sometime in 2017 or 2018, with industry watchers maintaining it will have a significant impact on the way masonry buildings are designed, constructed, and maintained.
The Power of BIM
BIM has been dubbed a “game changer,” and as such opens the door to many advantages over conventional “longhand” techniques that have been part of the construction process for centuries. While many architects will probably never work on a project with the staggering convolution of a Disney Concert Hall, most will work on projects that require sophisticated detailing. In these instances, which include most projects in today's development portfolios, BIM can simplify an architect's job in many ways.
Reduce or Eliminate Errors
Computerized models have great potential to reduce human error and if an effective planning effort has been made by each discipline and is carefully reviewed and shared, BIM has the potential to avoid or at least reduce mistakes. Orders can be extracted directly from a quality BIM model, providing an exact representation of unit types, colors, textures, and quantities. With confirmation of the accuracy of the model, the exact product order can be delivered, eliminating the usual waste factor in sizeable orders. Further, because the software can break down and provide a better understanding of the construction project, there is a smoother implementation by contractors and subcontractors.
Clash detection. Integral to BIM modeling, clash detection is possible because each discipline—structural, MEP engineering, environmental engineering, etc.—has created an independent model which is then integrated in a single multilevel model. Clash detection identifies where the separate models have incompatible parameters, or an out-of-order time sequence that might cause design changes, higher materials costs, and the accompanying cascade of schedule and budget overruns. In the past, clash detection was performed on site as opposed to in the design phase when constructability issues can be resolved before construction begins, saving vast sums of money and time and producing a better building.
Quantity takeoff. A key part of any project, take off and estimating has been a tedious, time-consuming task. In the masonry field, the traditional method has been to cost out a project longhand, and then add a margin to the bid based upon the complexity of the job to cover all the intricacies that hand calculations cannot account for. For complicated architectural jobs this margin can be as high as 25 to 30 percent to cover unforeseen conditions. Yet BIM modeling can substantially decrease the time and effort involved, and derive a more accurate result. Field experience is full of case studies that have followed the cost of contractors' mistakes in estimating and ordering. In 2011, for example, designers of a Chicago Public School specified 67,000 ground face units, and subsequently followed two paths: the contractor's cost numbers and ordering methods and a modeling program to determine the same issues. While the modeling effort provided what in hindsight was an accurate cost figure and ordering scheme, the designers went with the contractor's decisions, and ended up requiring 12 add orders, additional mold set up fees and freight costs, and experiencing significant delays and color variation problems.
Benefits Realized
While prefabrication reduces field labor cost and time and increases accuracy in good quality construction, it requires highly reliable models to be successful. BIM models can achieve this level of accuracy via specifications, finishes, sequences, and a three-dimensional visual for each building component. Provided that BIM relates to fabricators' software, building elements can be manufactured according to precise specifications and delivered to the jobsite on time, in many cases curtailing costly and time-consuming field cutting. Since architectural masonry typically involves a manufacturer-applied design treatment to various faces and edges, like ground face or bullnose, it is essentially a very large prefabrication problem that is ideally suited to a BIM solution.
Optimizing Products
Synthesizing information from a number of disciplines, BIM has the capability to identify unique products, optimized for individual customers or projects, and for a faster, more efficient construction process in order to create better buildings with less effort. Masonry manufacturers typically have tremendous flexibility to produce exactly the right specialized unit to resolve just about any design condition but if these unique products are not located and accounted for during the QTO process, those units will never appear on the jobsite. This is another area where a BIM solution controls both the cost of masonry projects as well as the final aesthetic of the installation.
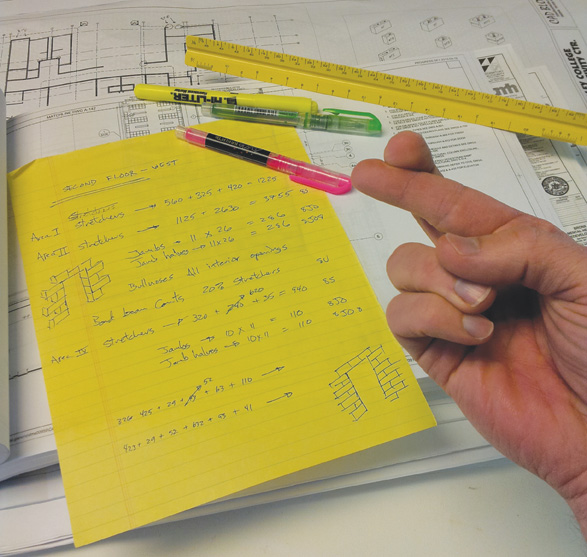
Photo courtesy of Oldcastle® Architectural
Traditional QTO technology is to cost out the job longhand, and add 25 percent.
Powerful Information Record
Information about a building project that is collected and created during its lifecycle provides an unprecedented data resource that can help owners and managers improve operational effectiveness throughout the service life of the building, and beyond. As this flow of information is cyclical—data collected by continuous measurement of various parameters—it becomes a database for future renovation and a QTO for repairs and building maintenance. Further, performance data of this depth can help determine the efficacy of designs and predictive models. In some cases, the information is critical in addressing unforeseen situations. One example is the experience of the Triumph Foods Packing Plant in St. Joseph, Missouri. Architects had called for 60,000 pieces of glazed block which was being installed as the plant suffered an explosion in 2005. Portions of the block turned to rubble. Instead of spending weeks or months in the reordering process determining what product was in the walls that were lost, the owners consulted the model that had been formulated for accurate QTO during the ordering process, which enabled them to retrieve the precise information on the size, color, character, and cost of the block that had been initially specified. The reordering process was completed in less than an hour, a dramatic reduction in time and effort versus conventional methods.
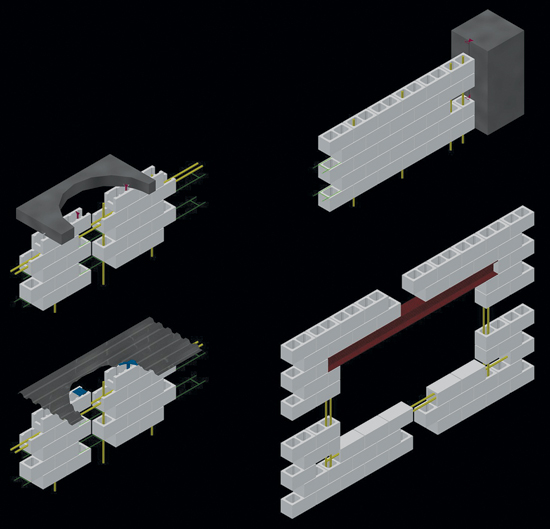
Image courtesy of CAD BLOX LLC
In addition to the units themselves, masonry walls encompass a host of supporting hardware.
Current Design Options
Typically, BIM modeling for masonry occurs on a post-bid basis rather than in the design phase, yet the latter is where it could be most valuable. The design advantages are multifold: The 3D model provides the benefit of visualization of the project that will facilitate a more accurate design with fewer errors and omissions, the ability to visualize bond patterns, exchange products and see the cost impact, and properly locate and size openings in the bond pattern to eliminate field cutting. With 4D modeling during the design phase, construction sequences can be visualized to develop a phasing sequence to be incorporated into the construction documents.