Polished Concrete Overlayments
Priming
The use of a primer is often advised to assure that there is full adhesion to the substrate. An example would be a project where a self-levelling underlayment product is used to prepare the concrete slab. In that case, the primer needs to be applied over the prepared concrete slab and allowed to cure before the underlayment is applied. Similarly, before the overlayment layer is placed, a primer will be needed regardless of whether the substrate is a prepared concrete slab or a new layer of underlayment. The overlayment primer will serve the dual purpose of increasing adhesion while covering and reducing pinholes in the substrate that may otherwise cause issues.
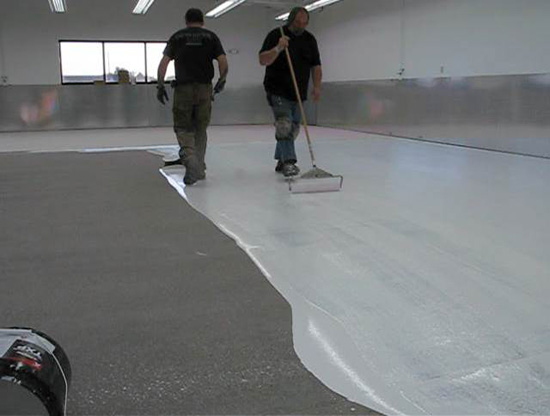
Photo courtesy of CTS Cement Manufacturing Corporation
Spreading an epoxy primer over the substrate is the preferred choice before a final overlayment is poured.
There are essentially two common primer choices used—either acrylic based or epoxy based. The choice of which type of primer to use will depend on meeting specific project conditions. Acrylic primers can allow any substrate patches or repairs to telegraph through to the finished flooring. It will usually require multiple thin coats and has no crack bridging capabilities. Nonetheless, acrylic primers are considered faster to install and less expensive than epoxy. On the other hand, epoxy primers may reduce telegraphing, can be applied in a single coat, and has crack bridging capabilities for non-moving cracks in the substrate. It may, however, be slower to install and more expensive than acrylic. When comparing the two, keep in mind that for polished concrete overlayments, epoxy primers are preferred for their superior characteristics.
Mixing and Placing the Overlayment
After the substrate is prepared and primed, then a self-leveling overlayment with C4A3S cement is now ready to be mixed. On-site batch mixing is preferred for polished overlays because the mixing time and water dosages can be more accurately controlled by the installers. Continuous mixers are not recommended since they don’t provide adequate time for the material to be fully mixed properly. Since this is a finish concrete product, it is temperature sensitive. This means it is best to maintain the material temperature between 60 and 80 degrees Fahrenheit. In hotter or colder situations, cold or warm mix water may be used to help regulate the material temperature.
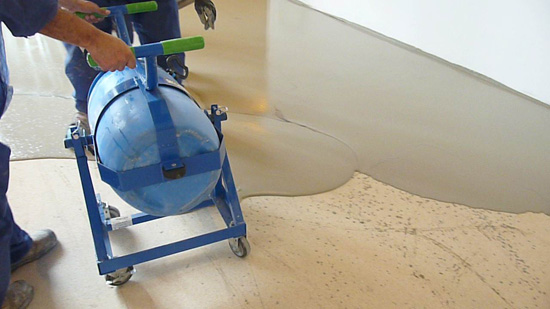
Photo courtesy of CTS Cement Manufacturing Corporation
Mixing the overlayment in a batch mixer and placing it evenly over the prepared substrate is done quickly and efficiently at proper temperatures.
Mixing is the point where the final characteristics of the overlayment are defined. If specified aggregates are desired, they should be present and added to the mix. Similarly, if coloring is called for, the appropriate colorants should be measured and added to the mix. The mixing time may vary depending on the additives and aggregates used, so manufacturer’s data should be reviewed in that regard. The size of any given batch should be equal to the area that needs to be covered in a given section of the floor. Sections may be defined by room sizes or by divider strips, commonly used for terrazzo type of applications, or by pre-determined joint locations.
Once mixed, concrete overlayments should be placed right away over the floor slab. Control joints should be pre-established if required to control cracking. Also, expansion and isolation joints that separate the floor slab from other parts of the existing structure should be honored and incorporated in the overlayment. If the application includes divider or terrazzo strips, those should be in place and levelled to the proper height prior to overlayment placement. When terrazzo strips are not being used, saw cut joints within 24 hours of placement and fill with the appropriate joint fill material.
When placing the mixed material, manufacturers recommend that the edge of the placed material is kept wet to assist in the proper meeting of separate placements. It is also important to use proper tools for placement and finishing such as a gauge rake to place the material to the desired thickness, followed by a spike roller used as the finishing tool. The spike roller removes the tool marks from the gauge rake and assists in leveling the finish surface. It also helps in removing any trapped air sometimes caused in the mixing process. Once all of the material is placed, the overlayment needs to cure in a protected state. It is important to minimize air movement over the surface until the product has reached sufficient strength.
Grinding and Polishing
This is the final step that creates the final finished appearance of the floor. It should not start until the overlayment has been allowed to fully cure per manufacturer’s recommendations and instructions. From there, the degree of polish and shine can be determined along with the amount of aggregate to expose. The first grinding step will be a coarse grit level to create a uniform appearance and expose the aggregate. Additional grinding steps will then be carried out at increasingly finer levels to refine the floor to the desired clarity and gloss. The nature of the material allows for a very high gloss to be achieved if desired while still maintaining appropriate slip resistance for safety. The final step is to apply a clear surface stain protector if desired or required.
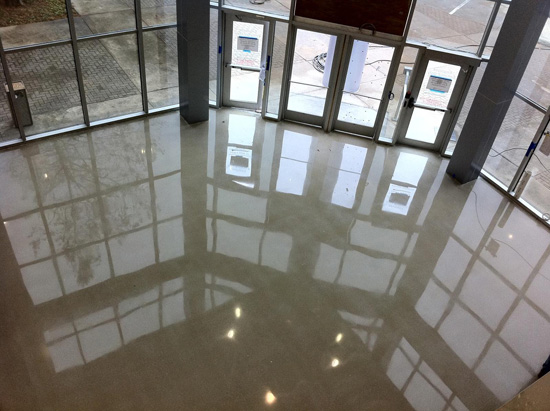
Photo courtesy of CTS Cement Manufacturing Corporation
Grinding and polishing the overlayment topping provides the final finished appearance in a sheen and gloss that can be specified to suit a particular project.
The end result of the entire process is a finished floor that is uniform, level, smooth, and easy to maintain. It is a combination of both design and installation efforts that allows this final outcome to be achieved.
Green Building Contributions of Polished Concrete Floors
The U.S. Green Building Council has produced the best known green building rating system with the Leadership in Energy and Environmental Design (LEED) program. Under that program and others that use similar criteria for rating sustainability in buildings, there are categories where the use of polished concrete floors can contribute to the overall design of a sustainable building.
• Optimize Energy Performance: As the largest single category of the LEED rating system, energy usage appropriately receives a lot of attention in design. Finding ways to replace fossil fuel energy with renewable sources of energy is the focus of many energy design strategies. Passive solar heating has been and continues to be a viable approach but without the proper amount of thermal mass in a structure, solar gains will simply heat up the air in an interior space quickly, sometimes uncomfortably so, and then cool it back down quickly as well. The use of polished concrete floors in residential or commercial buildings where the design allows the sunlight to strike the floor means that the floor is warmed, not just the air in the space. The significance is that the mass of the concrete can store more heat than air so the interior temperature rises slowly and comfortably if designed properly. After the sun has set, the warmed concrete continues to be warm and radiates its heat back into the living space. This approach will often allow conventional heating systems to be turned off later in the fall and earlier in the spring effectively shortening the heating season. In the coldest months of winter, it can be a very effective supplement to a conventional heating system, meaning that less purchased fuel or energy is used to warm the building.
• Materials and Resources: The latest version of LEED takes a rather holistic approach to the use of materials and products in buildings. Essentially, it relies on an overall life-cycle assessment of products that may result in a manufacturer or a trade association issuing an Environmental Product Declaration (EPD) to identify the energy and environmental impacts associated with a particular material from its initiation (mining, extraction, etc.), through manufacturing, delivery, use in a building, and its end of service life options. Concrete that uses portland cement has been viewed as an energy-intensive product that contributes to greenhouse gas emissions. Happily, C4A3S cement has been found to be 60 percent more environmentally friendly than portland cement, producing 32 percent less carbon dioxide per pound during manufacture and 66 percent less over the life of the concrete. This is enhanced by the use of recycled content in the concrete such as aggregates, fly ash, etc. which may range from 10 to 30 percent by weight of the concrete, with 15 percent being typical. In the case of site mixed overlayments in particular, it is easy to see that the amount mixed is totally in the control of the installers, meaning that waste is minimized or eliminated since only the amount needed is mixed and used.
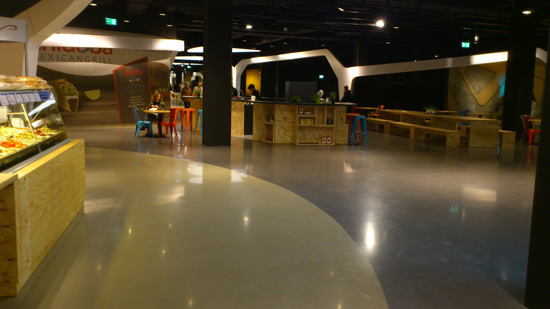
Photo courtesy of CTS Cement Manufacturing Corporation
Polished concrete floors can be used in a variety of building types to help contribute to green, sustainable, and healthier buildings.
• Indoor Environmental Quality: This green building category addresses several areas. First, it looks at the human health impact of building products, particularly from volatile organic compounds (VOCs) found in many different types of products and materials. The nature of polished overlayments is that a hard, permanent surface is created that does not require any additional paint, coatings, or adhesives that commonly are a cause of VOC release in buildings. Therefore the overlayment process can reduce or eliminate this concern altogether in regards to the floor. Second, this category looks at the quality of the space in terms of daylighting and the quality of light in the space in general. Using lighter-colored materials, including on the floors, helps with light reflectivity and the distribution of light, particularly in a commercial building space.
In the end, of course, it is the building that is certified or designated as green or not, and it is all of the individual decisions along the way related to the items above and others, that collectively produces a sustainable design.