Fenestration as Barriers for Better Performance
Fenestration Energy Standards
While the NAFS standard addresses the strength and integrity of fenestration products, the National Fenestration Rating Council (NFRC) is the most widely used standard for energy performance. A commonly cited rating is NFRC 100, which is a set of procedures and guidelines for determining the U-factors of all types of windows and doors. This is the fundamental rating that many people look for in regard to demonstrating thermal energy performance both for influencing the building design and for demonstrating compliance with the IECC. Note that this standard looks at all of the components of a glazing product or system (i.e., window, curtain wall, entrance, storefront, etc.) and shows an overall U-Factor for the product, not just a U-Factor for the glass. This allows design professionals to make comparisons and decisions based on the total product, not just the glass used.
A similar rating is NFRC 200 which is used to determine the Solar Heat Gain Coefficient (SHGC) and Visible Transmittance (VT) of glazing in windows and doors. The SHGC is useful for determining how much heat is contributed by the sun through the glass. It is regulated by the IECC and has particular significance in warm climates. The VT is helpful in determining the effectiveness of daylighting and views in a building space. Both of these NFRC ratings are essentially technical documents intended for use by testing labs and other window and door professionals. Hence, when window and door companies indicate that their products are tested or certified to NFRC 100 and 200, it simply means that they have had simulations and/or physical testing performed on their products in accordance with the guidelines published in NFRC 100 and 200.
The things that manufacturers control which directly influence the results of the NFRC ratings are many and varied. The glass can be standard double-glazed or higher-performing triple-glazed. The spaces between the glass panes can be separated by standard aluminum spacers or high-performance “warm edge” spacers. The air in those spaces can be replaced with an inert gas such as argon. The glass itself can be treated with coatings to improve thermal emissivity (i.e., Low-E) or to change the SHGC─either of which may directly affect the VT of the glass and its coloration. The frames of the glazing systems used in commercial buildings are typically made out of aluminum, which is great at conducting heat and not good at restricting it. Hence, manufacturers incorporate one or more thermal breaks in the aluminum framing such that inner and outer aluminum members are held together with materials that conduct less heat but maintain appropriate strength.
All of these performance details can be specified in a project, along with the preferred appearance characteristics to achieve the desired outcomes. However, working with an experienced glazing systems manufacturer can help ensure that particular combinations of characteristics are indeed possible and available. It can also help determine the relative cost impact of different selections. If code compliance is a concern, they may also be able to help in that regard by offering systems that have been accepted in similar climate zones for similar projects.
ENERGY PERFORMANCE CODES
While industry standards set the bar for quality and the basis for testing, codes dictate the level of performance needed to show compliance for the health, safety, and welfare of the public. The codes reference the standards and use them to document the required performance. Some of the applicable codes are reviewed in the following sections.
International Energy Conservation Code (IECC)
Energy performance in buildings is a good case in point of the design and construction industry moving out in front and the codes needing to be updated to keep pace. Since the 1980s, there has been a concerted movement that has taken hold in design, construction, product manufacturing, and building operations to reduce the amount of energy used in buildings. Energy codes emerged during this time – not to regulate energy consumption (i.e., there are no violation orders issued if a monthly utility bill is too high), but to regulate design and construction so that energy usage in buildings is better controlled. That control falls into two categories; 1) energy conservation, which is the act of reducing the amount of energy needed in the first place, playing out most notably in a better-performing building envelope (insulation, air sealing, glazing traits, etc.); 2) energy efficiency, which means reducing the amount of energy required to power equipment, lighting, etc. and still achieve the desired outcomes (heating, cooling, light levels, etc.). Taken together, we refer to the energy performance of a building as a combination of conservation and efficiency measures that achieve a measurable outcome. The International Energy Conservation Code (IECC) addresses all of these aspects of energy performance. It also recognizes that different climate zones exist around the country that directly impact the energy performance of buildings.
Pushed by this movement, the IECC has undergone a number of revisions and updates, this time focused on establishing the “code minimum” level of energy performance while still allowing these other voluntary programs to go beyond that level. Note that the health, safety, and welfare significance of the IECC is more than just a concern for the environment in general related to air quality and climate change. It is also based on addressing the adequacy of the supply of energy to buildings. The energy crisis of the 1970s demonstrated that real or imposed shortages of energy supply posed a significant threat to the public (think about how long is too long when experiencing a power outage). Virtually all buildings now rely on energy to operate the heating, cooling, lighting, appliances, electronics, and equipment. If that supply is compromised or interrupted, so is the safety and quality of life of the people who are in those buildings.
ASHRAE 90.1
The American Society of Heating, Refrigeration, and Air Conditioning Engineers (ASHRAE) has long been involved in optimizing the engineering of energy-using equipment in buildings. They have also recognized the significance that the building envelope has on the amount of energy needed to operate that equipment, both in terms of capacity and in the amount of time it needs to run. As such, ASHRAE has committees and work groups made up of members and associates to generate some recognized standards for building design. ASHRAE 90.1 “Energy Standard for Buildings Except Low-Rise Residential Buildings” is meant to apply to most commercial, industrial, and institutional buildings. The International Code Council has recognized this standard as “equivalent” to, albeit not identical to, the requirements of the IECC. Hence, it is a recognized alternative to use when showing code compliance for non-residential buildings. While there are indeed differences between ASHRAE 90.1 and the IECC, a building designed to meet the minimum standard of either one should yield approximately the same overall energy performance. Note that in some jurisdictions, such as New York City and elsewhere, commercial buildings must use ASHRAE 90.1, not the IECC to show compliance with the Energy Code.
California Title 24
The state of California codes are referred to as the California Building Standards Code, which is embodied in the California Code of Regulations, Title 24. It is commonly referred to simply as “Title 24” and includes 1) some adopted I-Codes as written; 2) some I-Codes with adaptations to suit California; and 3) some California-generated standards to suit particular state concerns. As such, the Title 24 codes are generally more stringent, particularly in regard to energy performance and seismic issues, than the model I-Codes alone. That means that the “code minimum” threshold for energy performance can be expected to be higher in California than elsewhere in comparable climate zones. It has also been observed that other states, particularly those in the Pacific Northwest, have begun to follow California’s lead and are starting to incorporate their own state adaptations to the model codes.
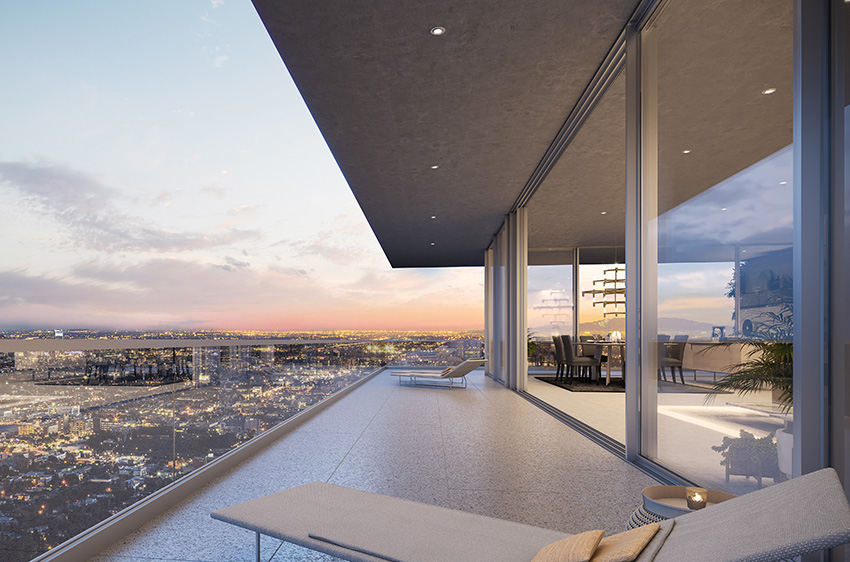
Photo courtesy of CRL
Sliding glass door and wall systems provide a sophisticated and elegant look but can also meet needed performance and operational requirements.
International Green Construction Code (IgCC)
The International Code Council has collaborated with a number of non-profit organizations to create a model green building code. Referred to as the International Green Construction Code (IgCC), it addresses more than just energy but also other common aspects of a green building such as site design, water usage, material selections, and indoor environmental quality. This code has primarily been adopted by localities, as opposed to statewide adoptions, and provides multiple options for achieving minimum performance levels. It works in a very similar manner to the voluntary programs (such as LEED) but codifies it so that code enforcement officials have a tool to work with similar to other codes.
Outside of the IECC and the IgCC, there are numerous organizations that have been addressing the issues related to energy performance in buildings. Accordingly, many well-known voluntary programs such as the Architecture 2030 Challenge, The AIA 2030 Commitment, LEED, ENERGY STAR for Buildings, Passive House, The Living Building Challenge, and others have emerged and evolved in the past 20 years and become very much a part of the mainstream of building design. Based on all of these developments, it is clear that the current direction of building design is to continue to seek better energy performance in buildings and reduce the emissions caused by the use of fossil fuels in the heating, cooling, and operation of buildings or the generation of electricity.
With all of the above in mind, we look next at three common types of operable fenestration systems used in commercial buildings. Fixed glazing systems (i.e., fixed windows, curtain walls, storefront systems, etc.) are fairly predictable since they do not open or close. Hence the thermal and strength performance of these products relates directly to the nature of the frame or support design, the characteristics of the specified glass, and the ability to seal the glass permanently in the frame. Operable doors and windows need to do all of these same things but have the added requirement of being able to open to allow for passage or ventilation, or both, but then be able to close and seal tightly again,─not just once, but repeatedly over time. The three systems addressed here are sliding glass door and wall systems, bi-folding glass door and wall systems, and glazed entrance systems.
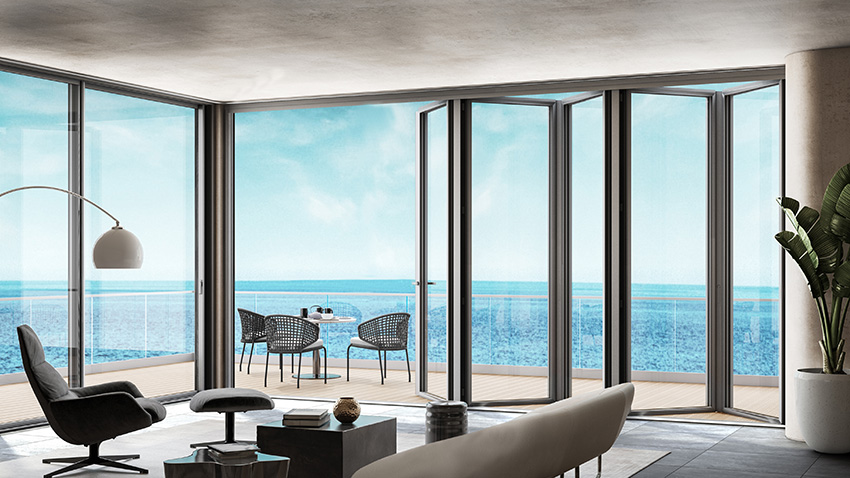
Photo courtesy of CRL
Bi-folding glass door and wall systems provide a different design and operational option for large format openings compared to sliding glass doors and wall systems.
Notice
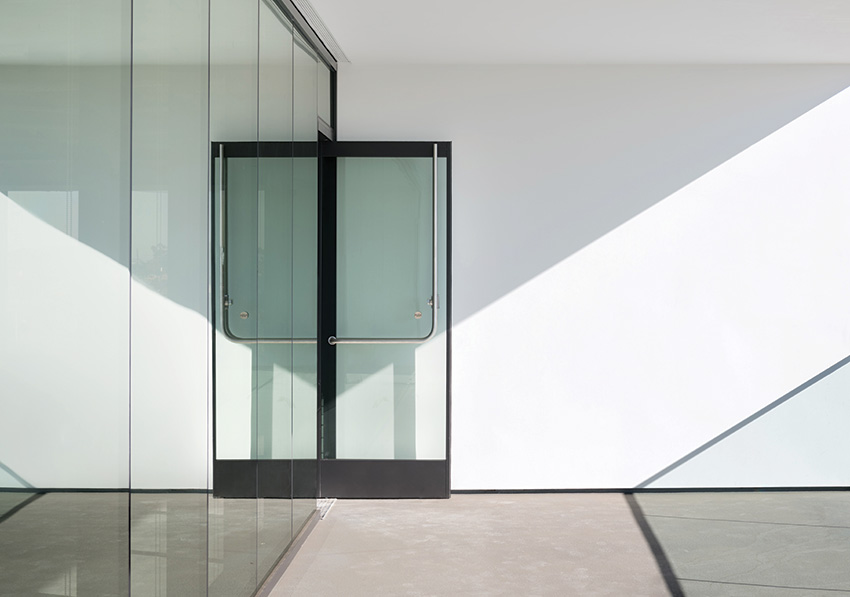