Chemistry: A Major Driver of Building Performance
2. Roofs
Keeping precipitation out the building is the priority for any roof. Built-up roofs (BURs) — in various configurations and with numerous material combinations — have been on that job many decades. Other systems common for low-slope applications, including metal roofs, membrane roofing materials and spray-applied polyurethane foam (SPF) may be considered comparatively new. And vegetative roofs are enjoying resurgence as concerns for the environment grow. Let’s look at these last two broad roof categories, which have some important similarities, and better understand what chemistry has added to the mix of high-performance, more sustainable roofs.
Whether a roof has a natural, vegetative top layer or a synthetic, man-made look, an important element in each case is “what’s underneath?” Drainage and insulation can be handled in a number of ways, of course, but in many cases these two considerations get resolved or refined between the structure supporting of the roof and its waterproofing layer. Drainage is key to managing the precipitation that lands on the roof, and insulation helps manage the impact of the outside air and elements on the comfort of the inhabitants inside. In many cases, the insulation material used and the benefits it provides are essential to the roof system and overall building envelope performance.
Most low-slope roofing systems employ board stock insulation materials made from either expandable polystyrene (EPS) or extruded polystyrene (XPS). With an SPF roofing system, the system is comprised of a material known best for its insulation properties that also offers other qualities needed for a high-performance roof.
SPF Roofing Systems
As previously described, SPF is an insulation material commonly found in vertical wall applications that is also used in low-slope roof applications. It is unique from all other roofing systems. SPF is a generic chemical-based product that has been adopted and adapted by countless building product manufacturers, all over the U.S. and the world. SPF is certainly not a new product, but its benefits are many and have stood the test of time.
As most architects and builders know, SPF insulation is rigid, lightweight, wind resistant and effective in extreme temperatures and weather conditions. SPF insulation has the highest R-value per square inch of any commercially available insulation material. It is a very cost effective and sustainable means to rescue a failing roof because it can be installed directly to the existing substrate without tear-off in about 95 percent of retrofit situations (according to Spray Polyurethane Foam Alliance Life Cycle Cost Study, Michelsen Technologies, LLC, 2004), provided that the materials from the original roof are structurally sound and have not taken on too much water. This practice can divert thousands of tons of waste from the landfill, while also affording a fast installation with limited disruption to occupants.
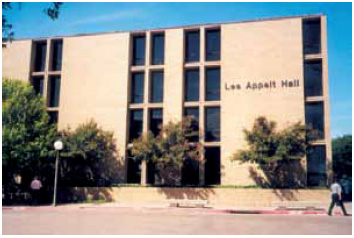
Texas A&M University monitored energy savings on 27 different buildings on the campus that had received a spray-applied polyurethane foam (SPF ) roof from 1980 to 1984. The results showed the university was able to cover the complete cost of the roof application through energy savings in an average of 4.5 years. Today, the main campus boasts more than 7 million square feet of SPF roofing.
After removing the gravel and cleaning up the old roofing surface, SPF can be sprayed on as a seamless, monolithic layer that is self-detailing or self-flashing and offers tenacious adhesion. The mixed liquid expands many times its original volume in a matter of seconds upon application, forming a rigid foam plastic that chemically bonds to the surface to which it is sprayed. Spraying the foam in .5-inch to 1.5-inch lifts allows the applicator to reach the desired thickness to fill in low areas, build up slope, and provide insulation in a single operation.
SPF is ideal for (very) low-slope roofs because its application and finished thickness can be very well controlled to provide slope-to-drain and avoid low spots (ponding). At the other extreme, SPF is ideal for domes, odd shaped roofs, or roofs with many openings for skylights, etc., because it can be applied to virtually any configuration with the same high-performance results. In fact, SPF insulated roofs paid for themselves through energy savings in 4.5 years on average, based on a Texas A&M study entitled “Energy Data Measuring Cost Saving on Campus SPF Roofs Compared to BUR Roofs,” Gerald Scott, PE, 1985.
SPF roofing systems also offer industry leading wind uplift resistance because there are no edges or seams for the wind to grab and pull away from the structure. Its composition allows it to withstand hailstorms and windborne debris while offering a 20-year life expectancy with limited maintenance requirements.
To protect the foam from the elements, and particularly from degradation due to exposure to UV rays, SPF roofing requires a top coating. Budget, climate, aesthetics and the choice of installer often determine which choice is best. Aggregate granules can be incorporated into the coating layer to provide a non-slip surface for those conducting roof inspections or servicing rooftop mechanical equipment. Three elastomeric coatings most frequently used as coatings for SPF roofs are:
- Urethane, typically the longest lasting of the choices;
- Silicone, which holds up well to high impacts/hail; or
- Acrylic, which resists dirt and tends to stay whiter longer are usually used.
All three of these high albedo-coatings (very reflective) do the following:
- Reduce the absorption of solar energy;
- Reduce surface temperatures;
- Reduce heat transfer into the building; and
- Help to reduce urban heat island effect and smog.
- And to maximize cooling energy savings, these coatings typically have:
- High solar reflectivity;
- High infrared emissivity; and
- Retain these properties for many years.
Elastomeric coatings tend to last between 10 and 15 years, depending on weather conditions and the amount of foot traffic they are exposed to during that time span. At the end of the coating’s service life, the SPF roof can be renewed by simply removing the coating and a minimal (1.4 inches to .5 inch) layer of the SPF (known as scarfing). A new layer of SPF (.5 inch to 1 inch) is applied, followed by a fresh coating. This practice can be repeated almost indefinitely, giving SPF roofing one of the longest life expectancies available for low-slope roofing.
Vegetative Roofs
A vegetative roof is first and foremost a roof, and therefore, has to get the waterproofing right. It is vital that the membrane underneath the plantings is durable and withstands the test of time. Again chemistry has made a significant contribution to the waterproofing component of a vegetative assembly. Done properly, a vegetative roof can double or even triple the useful life of the waterproofing system (roof) underneath it.
The chemical ingredients found in acceptable membrane roofing types for vegetative roofing according to the Federal Green Construction Guide for Specifiers, Section 07 55 63 (Section 07530) – Vegetated Protected Membrane Roofing, published by the Whole Building Design Guide, include:
- Thermoplastic polyolefin (TPO)
- Polyisobutylene (PIB)
- Polyethylene terephthalate (PET)
- High-density polyethylene (DHPE)
- Low-density polyethylene (LDPE)
- Polyvinyl chloride (PVC)
These chemical compounds are key ingredients in membrane materials, but they are not the membranes themselves. Performance of the final membrane product depends on each manufacturer’s unique recipe — even for comparable products based on the same chemical ingredients. For example, TPO is chlorine-free and offers high breaking and tearing strength and puncture resistance; PIB is gas-impermeable, requires no vulcanization, is elastic and most importantly, retains flexibility at low temperatures; and PVC provides excellent weathering characteristics, high tensile strength and long-term flexibility with excellent resistance to harsh chemicals and industrial pollutants.
Choice in membrane materials is usually based on the manufacturer, third-party validated performance testing results (such as ASTM or UL standards), availability, price and installer preference.
Each of these membrane roof materials ensure the numerous benefits of vegetative roofs are realized:
- Reduced heat island effect
- Replacement of the green footprint lost when the building was constructed
- Control and retention of stormwater runoff
- Clean outside air with less CO2 and other harmful contaminates
All of these high-performance waterproofing membranes provide a robust, long-lasting solution and are recommended according to the Whole Building Design Guide.
3. Wall Systems
Metal stud walls in commercial buildings and stick-built homes have been around a long time, but they are losing favor to more advanced wall systems that take advantage of leading edge chemistry and innovation by building product manufacturers to offer impressive environmental benefits among many others.
The following three wall systems can provide a more sustainable, high-performance building envelope than conventional construction techniques, especially when employed in concert with the other building envelope elements discussed here.
- Structural Insulated Panels (SIPs)
- Exterior Insulated Finishing Systems (EIFS)
- Insulated Concrete Forms (ICFs)
The common denominator for each of these wall systems is the insulation component expandable polystyrene (EPS). Polyurethane (PU) is an alternative to EPS, but is used much less frequently because it is typically more expensive for the same dimensions due to its higher R-value of 6.5/inch versus the EPS R-Value of 4/inch.
SIPs are essentially a “wall sandwich” with structural skin on either side of an EPS or PU insulating core. Suitable for residential and light commercial construction, SIPs are used for wall and roof applications.
SIPs begin life in a factory. CAD drawings of the structure to be built are converted to shop drawings, which are then plugged directly into computer numerical control (CNC) fabrication machines or are used to measure and cut the panels by hand. Special channels (chases) are cut into the foam to allow for the electrical wiring, and the insulation core is recessed around the edges to accept the connection splines or dimensional lumber used during construction.
Most SIPs feature OSB as the skins or facers that encompass the inner foam insulation core of the panel. But other skins are available, including:
- Metal
- Fiber cement
- Fiber reinforced concrete
- Plywood
- Gypsum board
Regardless of the structural skins, those skins are rarely the final façade for the building. Standard panels are available in 4-by-8-foot or 8-by-24-foot configurations. Thicknesses typically range from 4.5 inches to 12.25 inches but custom sizes and thicknesses are also available. Insulating air sealants — single- and plural-component polyurethane foams — are commonly used with SIPs to help join panels together quickly, ensure air barrier continuity, increase energy efficiency and increase structural strength.
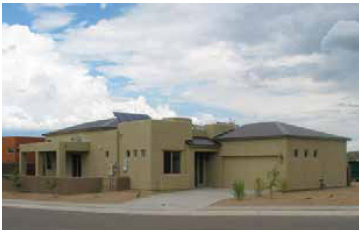
The Pepper Viner High-Performance Home in Tucson, Ariz., is 80 percent more energy efficient than an average Am erican home, reduces environmental impact and is built to last for decades. The project was part of an initiative to help systemize the production builder’s sustainable building procedures through a process called integrated design.
A recent Time & Motion study conducted by Reed Construction Data RSMeans Business Solutions showed that utilizing SIPs reduced installation time by 130 labor hours. When compared to RSMeans labor hours for a conventionally framed home, this is equivalent to time savings of approximately 55 percent. (For more information, see BASF Corporation Time & Motion Study, November 2006, submitted to BuildingInsight, LLC, conducted by Reed Construction Data/RSMeans.)
EIFS have survived some well-publicized problems from its past, such as leaks due to poor installation, which were often due to poor installation training. Well-tested master specifications for architects and aggressive contractor/installer training have made EIFS an extremely popular wall panel system today. Many manufacturers also offer moisture-drainage EIFS systems that include a drainage channel built into the insulation or adhesive elements of the system. Their popularity also stems from the incredible design flexibility they offer the architect. They are attached to the exterior façade and can be very impact and damage resistant based on the grade of mesh used.
EIFS are comprised of polystyrene insulation and reinforced synthetic stucco. Most systems also incorporate a liquid applied air/water-resistive barrier over the sheathing to further enhance thermal comfort and energy efficiency while reducing intrusive moisture concerns.
In 2007, the U.S. Department of Energy (DOE), through the Office of Energy Efficiency and Renewable Energy’s (EERE) Building Technologies Program, and the EIFS Industry Members Association (EIMA), sponsored a study, which was conducted by researchers at the Oak Ridge National Laboratory (ORNL). A building was constructed near Charleston in Hollywood, S.C., featuring panels with various wall claddings and assemblies. Each of the wall panels in which the claddings had been incorporated contained sensors that provided a full profile of temperature, heat flux, relative humidity and moisture content. These sensors collected information 24 hours a day, 7 days a week, and transmitted the data to the ORNL research facility in Oak Ridge, Tenn., for analysis.
The real-world data gathered during the study demonstrated that EIFS clad wall assemblies with drainage outperform other typical exterior claddings (brick, stucco and cementacious fiberboard siding) during most of the year, making EIFS an excellent exterior cladding choice for achieving key building performance goals in a hot and humid climate. (See Exterior Wall Cladding Performance Study, Oak Ridge National Laboratory/EIFS Industry Members Association, 2008.)
ICFs are interlocking, modular units of insulation that are connected and dry stacked (without mortar), often with a skeleton of reinforcing bars in the air space/cavity that separates the inside and outside insulated panels. These insulated forms are then filled with concrete. ICFs provide extreme structural strength (because they are filled with concrete) and are often used for basement walls (and even floors) with lighter weight wall solutions such as SIPs used on above-grade floors.
The insulated panels can be made up of EPS, graphite-enhanced EPS or PU. EPS is the most common and usually less expensive than other insulation forms. Graphite-enhanced EPS provides 20 percent better insulating performance, and is therefore more expensive, all other things being equal. Rigid polyurethane is also a choice for the insulated form material, which provides twice the R-value per inch of EPS and more compressive strength as an ICF form because it is denser.
Each of these high-performance wall systems provide the following important environmental benefits:
- Reduced air leakage, thermal bridging, and convection looping.
- Extremely high R-values — up to R-50 or more.
- Reduced HVAC loads and resulting reduced BTU requirements from early in the design process.
- FEMA-approved for flood zones.
- Wall stability — flat, won’t warp, expand or contract.
- Superior structural stability, stiffness, strength and predictable performance.
- Low environmental impact materials.
- Reduced transportation fuel costs due to lightweight materials used in each wall system.
- Low jobsite waste produced.
- Low or no VOCs.
Additionally the wall systems have individual, specific benefits to note as well:
- SIPs structural characteristics are similar to an I-beam.
- ICF passes seismic lab and field-testing.
- EIFS are resistant to wind-borne missiles in high wind events.
- EIFS can restore failing facades, retaining the embodied carbon footprint of existing structures.
- These notable benefits can be enhanced and leveraged when used in concert with other high-performance building envelope elements discussed here.