Pre-Finished Modular Plaster Panels
Green Building Contributions
The U.S. Green Building Council (USGBC) has developed the LEED® rating system for green buildings which has been recognized as the leading green building standard in this country. The LEED 2009 system is in place through the year 2015 which overlaps with LEED version 4 introduced late in 2013. Since buildings are currently being designed under both systems, credits and points may vary depending on the LEED version selected. Nonetheless, there are some inherently good characteristics in modular plaster panels that can contribute to green building design. Environmental Product Disclosures (EPDs) are available from some manufacturers or are in the making and can be requested.
We have noted already that the primary raw ingredient of polished plaster finishes is natural lime. This is mixed together with recycled marble powder which is crushed and graded as a by-product of marble slab and tile manufacturing. This mixture can account for up to 60 percent of the plaster make-up allowing it to contribute to recycled content credits. The result is a positive environmental impact by intervention, ensuring that hundreds of tons of pre-consumer crushed marble each year is re-used rather than sent to a land fill.
In terms of indoor environmental quality, most plaster products have low or zero volatile organic compounds (VOCs) meaning they do not introduce any into the indoor air. Similarly, the plaster finishes are applied to formaldehyde-free substrates such as MDF avoiding the use of that most common VOC. When water-based color coatings are used in the plaster finishing process, they commonly have anti-bacterial and hygiene properties to prevent the build-up of mold, mildew or bacteria. In all, the use of the plaster panels carries little if any impact on the quality of the indoor air.
Specifying Modular Plaster Panel Systems
When specifying modular plaster wall panels, the various choices and specification details need to be properly identified. Coordination with manufacturers during the design phases of a project will help gain insight into details, cost drivers, installation requirements and fabrication lead times. Some of the relevant items to address in a standard 3-part specification format are highlighted as follows, some of which can be verified or coordinated with information available from manufacturers.
Part 1 - General
Quality assurance is often addressed by citing specific national testing and standards for products. In the case of modular plaster wall panels, there are several that are particularly relevant:
• Mold/Mildew Resistance ASTM D 3273/3274
• Pencil Hardness Samples ASTM D 3363 - Shore D Hardness
• Scrub Resistance ASTM D 2486 – 79
• Impact Resistance ASTM D 2794
• VOC levels ASTM D3960
• Fire Test ASTM E84 – 98 - Interior panels should be tested for surface burning characteristics and rated accordingly.
Other key General specification information includes the appropriate request for submittals and shop drawings that confirm that the correct wall panels are being ordered and fabricated. Further a full warranty should be called for and submitted that demonstrates coverage for a reasonable period of time.
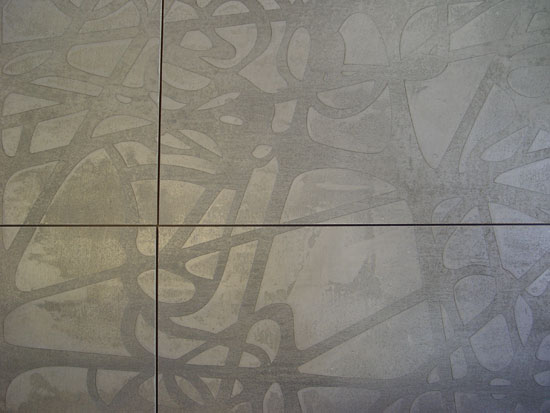
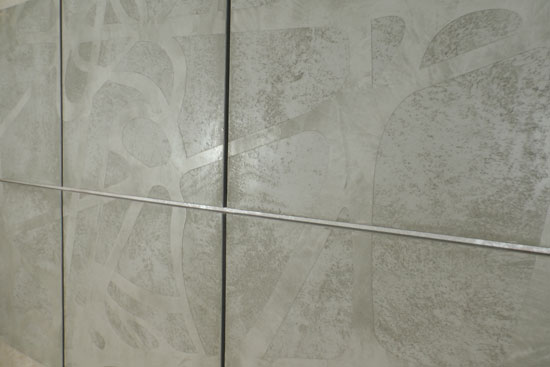
Photos courtesy of ArmourFX, a division of Armourcoat Surface Finishes, Inc.
Specifying modular plaster panels should include color, texture, and installation systems to assure a complete interior design and construction solution.
Part 2 - Products
Identifying the specific modular wall panel products that are desired requires covering several items. If multiple product types are selected for a building, then obviously they each need to be specified and their locations identified on the drawings.
• Panel shape and size: Size and shapes of the panels are generally shown on the drawings, but parameters for minimum and maximum sizes can be addressed in the specifications.
• Panel type and finish: Fundamental to the panel appearance is the choice of texture and finish being used. The choice should be influenced based on interior design requirements or the overall design properties being sought. The specific color and finish of the panel should be identified based on either standard manufacturer choices of custom specifications.
• Substrate: The type of substrate used to receive the plaster should be identified (MDF, plywood, etc.) including the thickness and other characteristics as appropriate to define its strength and rigidity.
• Adhesives: If an adhered installation is anticipated the specific type of adhesive should be called out that is compatible with both the substrate and wall materials. All adhesives must also meet code and testing requirements.
• Attachments: Concealed fastening with Z-clips is often part of a manufacturers system. As such, it should be specified to be provided by the same company that provides the panels as a complete, integrated system.
• Accessories: Fasteners and joint sealers may be recommended by the manufacturer but need to be addressed to be sure they are appropriately suited to the particular building application.
Since some aspects of products vary between manufacturers, using the specification items above will aid in product to product comparisons during design and assure appropriate installations during construction.
Part 3 - Execution
Installing pre-fabricated modular wall panels is fairly straight forward but requires appropriate attention to detail to assure the desired outcome is achieved. It is important to note that hand crafted processes produce a beauty and appeal that comes in part from variations in the surface and appearance. Everyone involved should expect this variation within the normal range of tolerances for any given finish.
• Examination and Preparation: The interior wall system that is receiving the panels needs to be in place and accessible. It should all be inspected for completeness and conformance with the building design and adequacy for correct attachments before the wall panels are installed.
• Installation and Field Quality Control: Since it is the installation of the fastening system that can determine if the panels end up appropriately aligned, level, and plumb, special attention should be paid to aligning clips or channels properly. Installers should definitely follow manufacturers’ instructions and approved shop drawings and comply with allowable tolerances.
• Repairs: In the event of any minor damage or blemishes, consult the manufacturer of the panel. It is likely that simple field repair may be possible instead of returning and re-fabricating a particular panel.
• Cleaning and Protection: The nature of most panel finishes is to be fairly smooth and easy to clean. Consult manufacturer’s instructions to avoid the use of anything that would harm or deteriorate the finish.